How Much Does a Robotic Welder Cost?
January 1, 2024
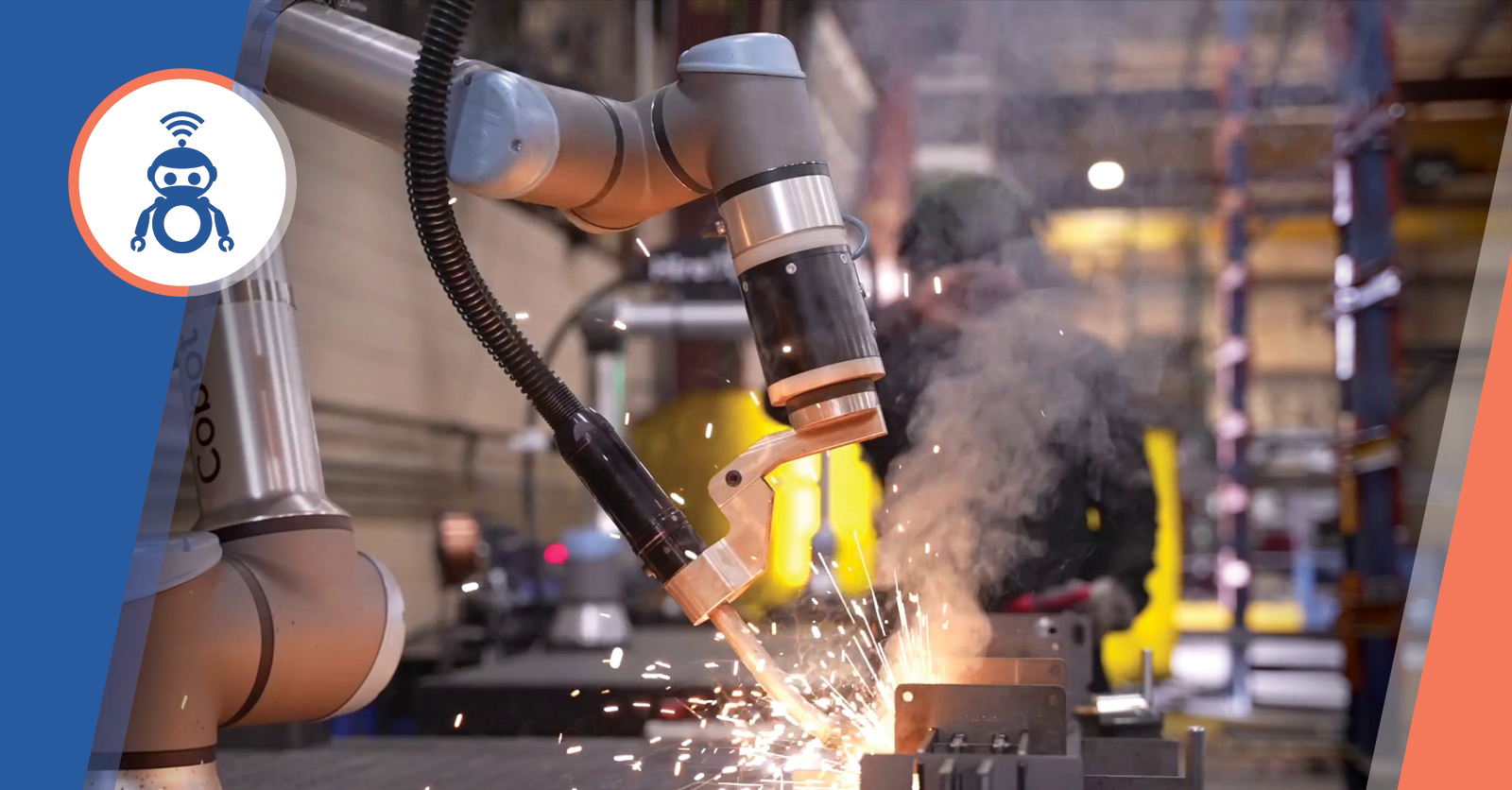
Welding robots have had a steady presence in manufacturing for decades.
Their popularity should be no surprise as robotic welding is a widely adopted automation solution that addresses the global shortage of skilled welders for manufacturers.
Even so, there are plenty of unknowns for manufacturers new to welding robots. One of the biggest concerns is cost.
The cost of a robotic welder can reasonably start around $50,000 USD. Costs quickly exceed $100,000 for moderate to large-scale robotic welding applications. There are many components included in a robotic welding system that can make the price vary.
In this article, we will dive deeper into the components that make up a robotic welding system and explain how much a welding robot costs.
Table of Content |
The Components of a Robotic Welding System
Manufacturers new to automated welding solutions might not be aware of all the components that make up a full robotic welding cell. It is more than just the robot and torch!
Here are some key components of a fully functional welding robot system:
- Robot Hardware
- Welding System
- Welding Gun
- Extra Tooling
- Safety
- Consumables
- Reprogramming
Robot Hardware
This is the most obvious component of your robotic welding system—the robot itself. It is also typically the most expensive component.
Researching different brands and suppliers is important because the robot you choose will greatly affect your daily experience with the machine.
The Cobot Welder offered by Hirebotics features the UR brand of collaborative robot. UR is the most used robot brand in collaborative robotics today.
Welding System
The welding system consists of the power supply, control interface, and ancillary components.
This system supplies the power needed to create the heat required for welding. It also houses the interface that allows the robot control system to communicate with the welding system.
This communication leads to better coordination between the robot and the welding system, leading to higher quality output.
Additional components include things like cabling/hosing, wire feeder, and cooling systems. The cost will be dependent on the size and complexity of these systems.
Welding Gun
The welding gun is the end of arm tooling required for welding robots to perform their task. Choices here abound depending on the type of welding tool you require.
- Laser heads are available for laser welding applications.
- Electrodes can be mounted for resistance spot welding tasks.
- Robotic MIG welding would require a simple MIG welding gun with options for robot control.
Costs can vary here depending on the type of welding and sophistication of tooling required.
Extra Tooling
Many weld cells operate more efficiently when extra tooling is provided. Examples of such components include things like mounting fixtures/jigs, sensors, and TCP (tool center point equipment).
Simple sensors like proximity or optical sensors typically won’t have a large impact on the cost of your system. More sophisticated sensing equipment like ultrasonic sensors or vision systems can cost several thousand dollars USD.
Mounting fixtures or jigs are used to hold the workpiece in a stable and repeatable position. The cost of these components becomes more expensive as their size and complexity increase.
Safety
Safety equipment should always be considered for any robotic welding system. These components include things like safety floor mats, interlocks, and light curtains.
The greater the safety risk your welding system poses to operators, the more safety equipment you will require.
Collaborative robotic welders typically require less risk mitigation. This is because their collaborative nature is designed for hybrid work near human workers.
Risk mitigation is often the responsibility of the end-user. You should ensure you have the budget for the required safety equipment based on the specifics of your use case.
Consumables
You should have a good understanding of your consumables costs if you are considering automating an existing welding process. These costs will vary depending on the type of welding being performed.
It should be noted that consumables are often used more efficiently by welding robots vs. human welders. This is because robots are programmed to do the same thing every time.
Human welders are more prone to mistakes due to inexperience or fatigue. These mistakes can lead to wasted consumables or even unusable parts.
Robotic Welding Programming
There are costs associated with programming robots. This happens both upon commissioning and when reprogramming.
This is often the case when a new part needs to be welded that isn’t part of the welding robot’s existing programming.
Some manufacturers have robot technicians on staff. However, many don’t because these professionals are in short supply and are expensive to employ. Additionally, those new to automated welding tools rarely have this staff already in place.
This reprogramming can be outsourced to third-party suppliers. Rates vary based on region and are typically on a per-hour basis with service minimums.
Welding robots come with a teach pendant, which is recommended by Original Equipment Manufacturers (OEMs) for writing basic programs. The teach pendant is a handheld device that allows operators to control and program the robot.
The teach pendant typically has a keypad with functions like speed adjustment, torch control, and jog commands.
It also includes components like the live/dead man switch and e-stop for safety purposes.
Operators should practice using these components to understand how they work and ensure safe operation of the robot.
Although the software (called URCap for UR robots) may be customized, a basic understanding of the interface and robot terms is still needed to be able to program those welding robots.
Simplify Programming with Beacon
Some robot types are easier to reprogram than others. The Cobot Welder from Hirebotics has a low-barrier of entry to program compared to other welding tools.
Beacon is changing robotic programming with an app accessible via cell-phone or tablet, removing the need for a complicated teach pendant.
This user-friendly app simplifies cobot programming for non-programmers by using easy to understand welding terms.
Maintenance
When considering the cost of a robotic welder, it is important to factor in maintenance expenses. Just like any other machine, welding robots require regular maintenance to ensure they operate efficiently.
Some robotics companies include annual maintenance in the initial purchase price of the robot. However, it is crucial to verify with the company whether this annual maintenance includes all necessary services or if there are additional fees for certain tasks.
On the other hand, some robotics companies may charge an extra fee for annual maintenance. This means that on top of the initial purchase price, you will need to budget for regular maintenance costs throughout the year.
It is important to understand how often maintenance is required and what specific services are included in the maintenance package.
Total Cost of a Robot Welder
Now that you understand the necessary components that make up the cost of a welding robot system, what kinds of costs can you expect?
It’s a difficult question to answer because so much depends on the scale and complexity of your application. Additional factors, such as the type of welding and the supplier chosen, can also impact your final price tag.
Simple, small-scale robotic welding systems can reasonably start at around $90,000 USD. Costs quickly exceed $150,000 for moderate to large-scale robotic welding applications.
The specifics of your application will largely determine your costs. Whether that cost is reasonable based on the value you will receive from automating your process is dependent upon the details of your business.
Wondering what the cost of the Cobot Welder is? Discover it here!