Welding Robots: Types, Advantages, and Limitations
September 29, 2021
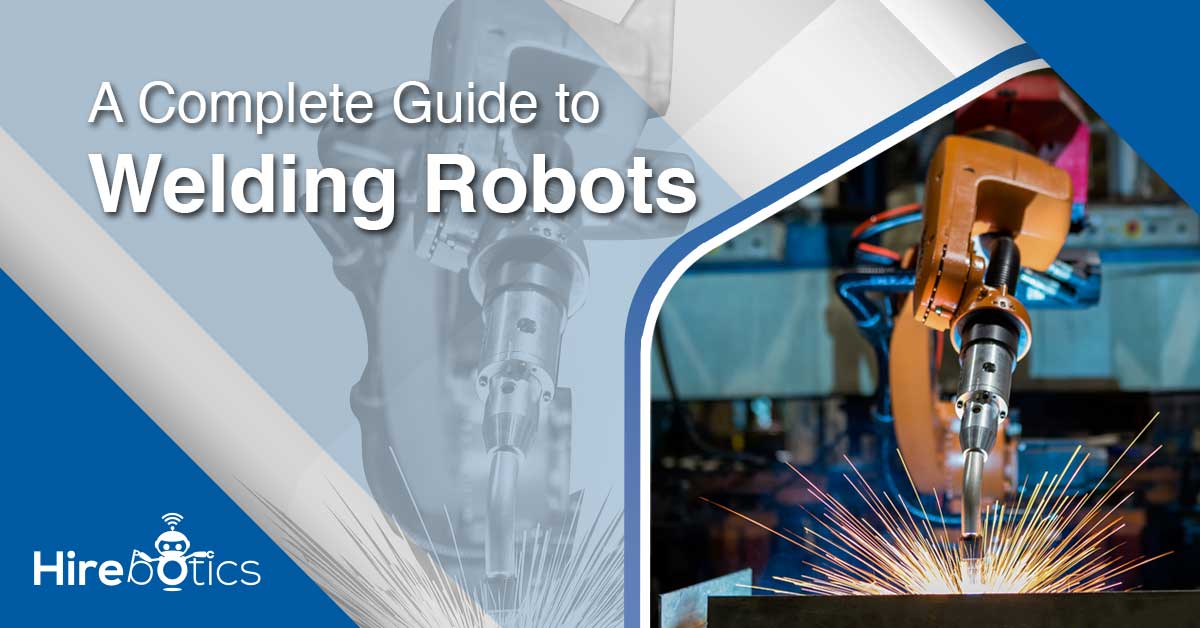
Technology has come to the welding industry in the form of welding robots. It's an exciting time for the industry. Robotic welders are constantly evolving to adapt to more and more welding processes. Are you curious about welding robots and want to know more about them? Do you want to know the different types of robot welders? Let's find out.
In this article, we will discuss:
- Manual versus Robotic Welding
- How Long Has Robotic Welding Been Around
- Advantages of Robot Welding
- Limitation of Robot Welding
- What are Welding Robots Used For
- Different Types of Robot Welders
- The Welding Industry is Evolving
Let's delve right in!
Manual Welding vs. Robotic Welding
As the name connotes, robotic welding is welding automation that uses a welding robot arm to weld. In this type of welding, the robot moves the torch along the joint to weld the pieces together. Welding robots can now do many types of welding processes using advanced welding tools.
There are two kinds of robotic welding: automatic and semi-automatic.
In an automatic robotic welding system, parts are fed in either a conveyor or a magazine. They are then clamped in position for the robot to weld. Once the robot welds the pieces, operators move them to another operation to be inspected, assembled, or packaged.
In a semi-automatic robotic welding system, an operator enters the robot cell, and removes the completed weld. The operator then positions the next pieces for the robot to weld.
Compared to manual welding, robotic welding is faster and has higher productivity. This is because the robot doesn't need to take breaks. The welding cost per piece also decreases since the welding robot can produce more welded parts than its human counterpart.
How Long Has Robotic Welding Been Around?
You might think that welding robots are a new invention, but the truth is they've been around for more than 60 years. Let's take a quick look at how robot welding developed.
George Devol invented the first programmable robot in 1954. Later on, he created the world's first industrial robot. After that, he established the world's first robot company Unimation. Here in this company, Devol and his colleagues created the first industrial robot. They called it Unimate. General Motors (GM) Automobile factory used Unimate in their factory in New Jersey. The robot did spot welding and extracted die castings. After the initial trial, the positive review spread the popularity of the welding robot worldwide.
In 1978, with GM's money, Unimation made the Programmable Universal Machine for Assembly (PUMA). This machine is still in use today.
In the 1980s, the industrial robot industry grew. Companies came up with new robotic welding machines every month. It's also in this decade; robotic arms developed more mobility and control.
Robot designs have continued to improve ever since then. Robotic interfaces improved, and designs were streamlined and simplified. The operator interfaces were also enhanced to make maintenance and repair easier.
From industrial robots, smaller collaborative robots (Cobots) were invented to work alongside humans. Cobots are easier to program and are safer than their industrial counterparts.
Welding cobots are continuing to develop. Who knows what kind of developments will happen in the future.
Advantages of Welding Robots
There are many advantages to adding a robotic welder to your process. Let's discuss a few important ones here:
- Increased productivity
- Constant quality
- Reduce waste and consumables
Increased Productivity
Robotic welders get the job done faster, more efficiently. They also make fewer mistakes compared to their human counterparts. They can achieve up to 85% efficiency compared to 20% of their skilled human counterparts.
Robots never tire, need a break, or go on vacation. They can produce the same quality welds day after day. Human welders more or less have less than 50% arc-on time, and this number can drop as fatigue sets in. Robots can have up to as high as 95% arc-on time.
Constant Quality
Robots don't get distracted. They can maintain constant weld speed, current, and other variables. Because of this, they can deliver very high weld quality every time. Using welding robots for welding projects that need stringent quality requirements is ideal.
Reduced Waste and Consumables
Welding robots eliminate a lot of welding mistakes that come from human welding. This is because robots don't tire and cut the problems fatigue can bring. Welding robots deliver the same weld quality no matter the situation. Avoiding scraps makes it easier to stay on budget, especially on high-value jobs.
Robotic welders are efficient so that they can use consumables like fillers more effectively. This efficiency reduces the amount of waste produced. Nozzles are also another consumable that robotic welders use economically, increasing their lifespan. Consumables are purchased less frequently, saving costs.
Limitations of Welding Robots
Although welding robots have a lot of advantages, they have their limitations. Let's take a look at a couple of these.
Requires Programming and Training
Most industrial robots need complex programming skills. So you may need to hire a new set of programmers to deal with programming the robot. You also need specialized training and safety courses for your workers. These courses are to familiarize themselves with how to work with robots safely. Robotic integrators can help you to install industrial robots or you can do it in-house with your own knowledgeable employees.
Needs a Considerable Investment to Start
Welding robots need a sizable amount of investment - both in machinery, jigs, as well as training. However, if used correctly, robots can pay for themselves in the span of one to three years. If you want to know how long you can get your investment back, you can use an online robotic welder Return of Investment (ROI) Calculator. This will tell you if it's worth the investment or not.
What Are Welding Robots Used For?
Currently, welding robots account for 20 percent of the total amount of welding in the USA. However, this number is rising fast. Generally speaking, industries use robotic welding where high production rates are required. Spot welding, usually used in the automotive industry, is one of the most popular welding robots. Yet, arc welding is also becoming an increasingly popular choice for the use of welding robots.
What Are the Different Welding Robots In The Market?
There are many brands of robotic welders in the market. But for this article, let’s talk about the different types of robots based on the welding processes they use.
The different welding robot types are:
- Resistance Spot Welding Robots
- Collaborative Welding Robots
- Shielded Metal Arc Welding Robots (SMAW)
- Robotic Gas Metal Arc Welding (GMAW/MIG)
- Robotic Gas Tungsten Arc Welding (GTAW/TIG)
- Robot Laser Welding
- Plasma Welding Robot
Resistance Spot Welding Robot
The automotive manufacturing industry commonly uses resistance spot welding. It’s a resistance welding process that uses larger electrical currents to join two or more sheets in a single location.
Spot welding robots are articulating robots. They are robots that have rotary joints that have a range of anywhere from two to 10 axes. Spot welding robots have a servo motor equipped with a high-resolution encoder that accurately controls the motion of the spot welding gun. The welding gun has a pair of electrodes that can open and close. It also comes with software that controls the acceleration, position, and force of the robotic arm.
Collaborative Robot Welding
Collaborative robot welding, or cobot welding for short, is also a robotic arm, usually 6-axis, with a welding torch as its end effector. Unlike industrial robots, cobots can work alongside humans. Because of this, there is no need to house them in a welding robot cell. You can only take care of the welding safety (flash, splatter). They are also easy to deploy and redeploy to different tasks.
With the advent of collaborative robots (or cobots), medium-sized welding businesses can also benefit from welding automation. They are also easier to program. The Cobot Welder from Hirebotics is hands down the easiest cobot in the market to program. How easy is it? Your welder can easily teach the robot with their phone using the app.
Shielded Metal Arc Welding Robots (SMAW)
Shielded Metal Arc Welding (SMAW) is also called stick welding. In this type of welding, an arc is created between a consumable flux electrode and the welded material.
A SMAW robot needs to consider a variation of the tool center point (TCP). A TCP is a variable used in robots for the computer to keep track of the tip of the tool, here the consumable electrode. The consumption rate of the electrode determines the direction of the robotic arm.
Robotic Gas Metal Arc Welding (GMAW/MIG)
Usually, robots are used for GMAW welding when high deposition rates are needed to get a high production rate. In GMAW welding or MIG welding, a consumable electrode is melted and acts as a filler material. Robotic GMAW welding or robotic MIG welding is used for welding stainless steel, copper, nickel, carbon steel, and aluminum. It’s usually used for metals that have high melting points of conductivity.
Robotic Gas Tungsten Arc Welding (GTAW/TIG)
Gas tungsten arc welding (GTAW) robots are used when welding thin parts or wanting aesthetic and precise welds.
In Robotic GTAW/TIG, variables such as torch movement, shielding-gas pre flow, pulse frequency, etc., are automatically controlled. Arc length can also be automatically maintained with automatic voltage control. Intelligent GTAW robotic welding systems have cameras that help with joint location tracking and error detection. In this type of system, the operator calibrates the camera and teaches the robot the weld path. The robot then takes a picture before the arc is established and compares this image to the reference image. This type of system is ideal for welding thin materials where the placement of the arc plays an important factor.
Robot Laser Welding
A laser welding robot is a type of welding that uses a focused laser beam as the energy source. Laser welding can either be through heat conduction or deep laser.
The robot laser welding machine is composed of a fiber laser head, a tracking system, a fiber laser, and an industrial robot. It’s usually used to weld materials of different thicknesses from different angles and different directions. Medical devices and the aerospace industry typically make use of robot laser welding.
Plasma Welding Robot
This type of robot welder uses a plasma arc as the heat source to melt the junction of the two metals that needs welding. Plasma welding robots are equipped with a plasma torch. A tungsten electrode is suspended inside the torch. The electrode compresses the arc, so the plasma flows from the torch at high speed. Plasma welding robots usually make use of six-axis articulated robots.
Plasma robots are used for welding a variety of metals regardless of their thickness. Robotic plasma welding is well known for precise welds and short cycle times. These robots can also weld both narrow and welds without part distortion.
The Welding Industry is Evolving
The welding industry is constantly evolving. With robot welding and cobot welding in the industry, both small and medium welding businesses can harness the advantage of robot automation. It's undoubtedly an exciting time for the welding industry. At the rate technology is evolving, who knows what tomorrow's welding technology will bring? Stay tuned!