Robotic TIG Welding: Is Automating TIG The Best Solution?
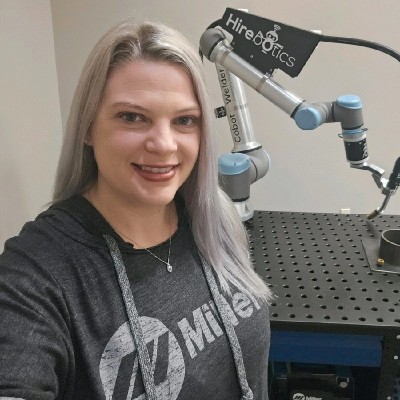
May 17, 2024
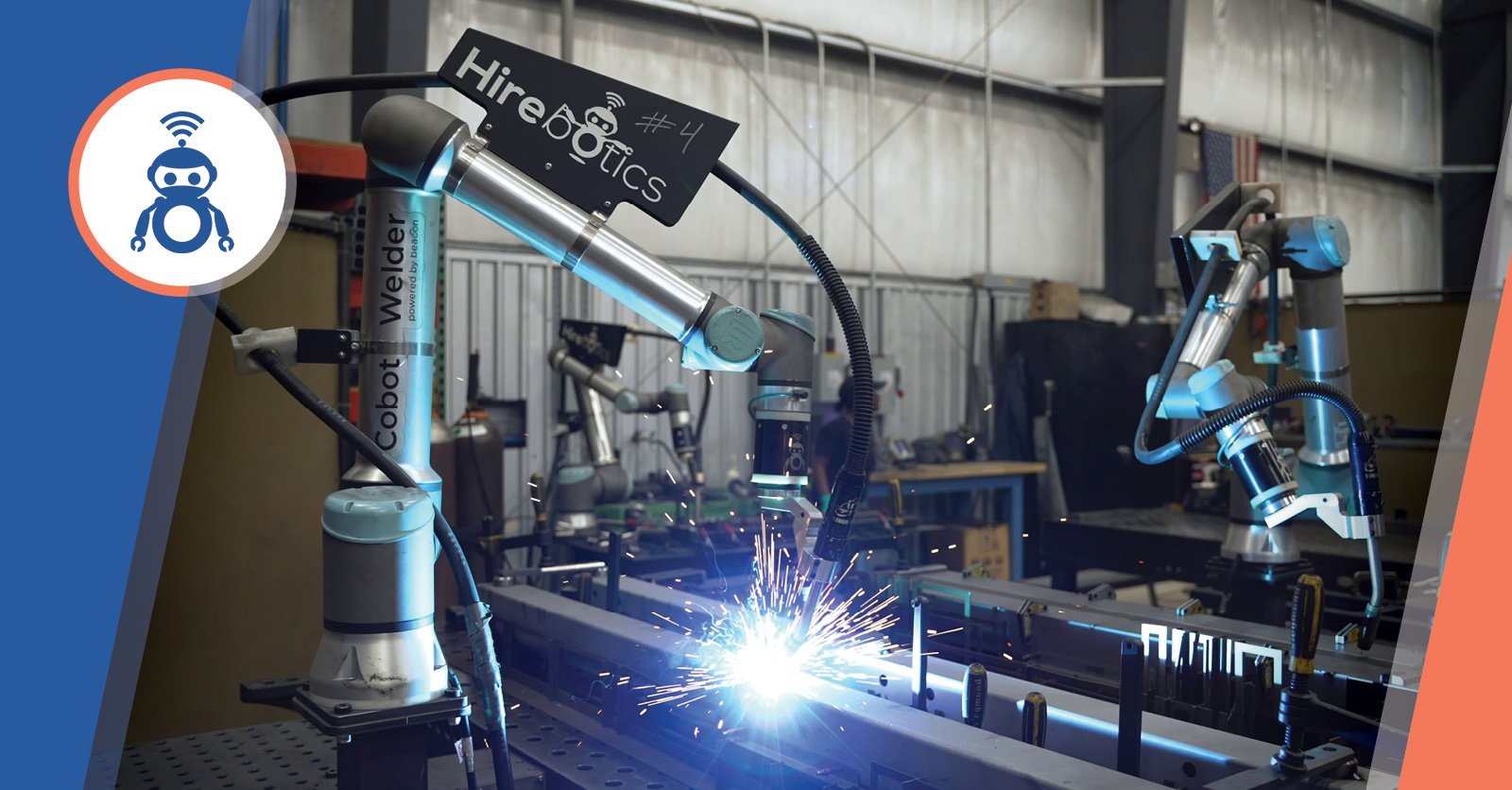
Since manual TIG (Gas Tungsten Arc Welding or GTAW) welding is painfully slow, the first thought for many shops is to automate it.
Skilled welder numbers are dwindling while the manufacturing demands are rising. Naturally, you want to figure out how to make the welding process faster.
You are about to learn some critical info on robotic TIG welding to see if this is the right call for your business. We’ll also show you a possible alternative for higher productivity and ease of use.
Table of Content |
What To Consider Before Automating TIG Welding
Robotic TIG welding isn’t usually the most economically viable automated welding method. TIG is a challenging welding process with many settings and low resistance to errors or contamination.
You’ll be welding faster with a TIG robot than by welding manually. But, even with a robot, TIG remains the slowest welding process.
Automation improves productivity, but automating TIG requires more effort than other processes like MIG welding.
Besides low productivity, you’ll face challenges like these with robotic TIG welding:
- TIG welding process is more complex than MIG - Unless you really must use TIG, you’ll be dealing with excessive effort to set up every part on a cobot. MIG gun is generally simpler to set than the TIG torch, and so are the settings. For example, AC TIG welding aluminum can require setting the AC balance, AC frequency, AC amplitude, waveform, and pulse settings. With MIG, you’ll mostly deal with the wire feeding speed (WFS) and arc voltage. You’ll have to set up some additional settings to “stack dimes” with robotic MIG, but this may also be necessary with a TIG robot, depending on what you wish to achieve. So, while robotic TIG speeds up the process, it’ll give you less of what automation offers than MIG.
- A bulky TIG torch - If you use a wire feeder with a robotic TIG, the torch can get quite bulky. You might have issues accessing tight joints. In contrast, MIG torch is much more compact because the wire is fed directly through the arc, instead of independently.
- Low wire feeding speed - Even with a robot, wire can’t be fed as fast as with MIG.
- Lots of back and forth with the power source - Robotic TIG welding software typically won’t let you control the power source at the software interface. And since TIG has a lot of weld settings you can use, this means frequent adjustments at the power source.
- Tungsten electrode erosion - The tungsten electrode erodes with use, affecting arc characteristics. So, you’ll have to monitor it and design a process to replace it.
- Protecting the robot from TIG High-Frequency - HF start is the best TIG arc starting method to completely eliminate the chance of tungsten contamination. However, HF produces an energy jolt that can interfere with the robot’s programming or damage the unit. If you wish to use HF, you’ll need to invest in case-hardened robot arms with shielded cables. Or, you can use a lift TIG system. When properly executed, the chances of tungsten contamination are negligible. But, this can require more caution on the operator’s side.
Advantages of Robotic TIG Welding
- Faster than manual TIG welding
- Better heat input control over manual TIG
- Significantly improved welding repeatability
- Reduced rework
- Higher profits
Disadvantages of Robotic TIG Welding
- Programming a TIG robot/cobot requires being a TIG expert, as the process factors are complex
- Many welding variables that can affect the weld quality
- Low wire feeding speed
- While faster than manual, robotic TIG is still slower than other welding processes
- HF can interfere with or damage the robot
- Tungsten erosion can cause weld defects, or inconsistent welds
- Bulky robotic TIG torch can make it difficult to access tight joints
How Would You Automate TIG Welding With a Robot?
Before considering welding automation, you must be aware of the two types of welding robots.
Traditional robots move fast and are meant to work in a dedicated area with limited access. Due to their nature, they require more safety measures, such as area scanners and fences. These robots typically require knowledge of a programming language and can take hours or days to program a part. They are most often used for high-volume and serial production.
Collaborative robots (cobots) work alongside your operators. They are much easier to program and are perfect for high-mix, low-volume jobs. Cobots have intrinsic safety measures like speed and force limitation; hence, they can’t hurt workers. For many low-to-medium part batches, cobots make the most economic sense. With the right cobot, your own staff can use it, and they can program the robot quickly, giving you flexibility for variable part production without hiring a programmer.
To use robotic TIG welding, you’d need a complete robotic welding cell. Whether for a cobot or a traditional robot, a cell would typically contain:
- Welding robot arm.
- TIG welding power source.
- TIG torch with assembled consumables.
- Welding table suitable for fixturing.
- Jiggs and fixtures.
- Fume extraction system.
- Cold or hot wire feeding system.
- Supply for a shielding gas.
- Water cooling system for the torch (if welding at high amps).
- Welding curtains to protect the shop staff from arc exposure.
- Safety enclosure (not needed for cobots).
- A teach pendant or another method of interacting with the robot.
To automate TIG, or any other process, the goal is to teach the robot a weld path and have it manipulate the torch with set weld settings.
With cobots, this is much easier to achieve with features like graphical interfaces, freedrive of the arm by hand, dedicated application screens on the teach pendant, or even phone apps like Beacon from Hirebotics.
A welding cobot typically requires the operator to quite literally grab the robot’s arm and move it to the start of the weld. Then, in a teach pendant or other software interface, adjust the weld settings. Next, move the cobot’s arm to the end of the weld, and finish off in the software. And… the weld is programmed!
However, TIG is a tricky process. Even with a cobot, there are many programming challenges.
Programming Challenges of a TIG Welding Cobot
TIG is more complex than comparable welding processes. It has too many settings and torch variables. You often have to address multiple factors, especially for aluminum and stainless steel.
You must use an appropriate TIG cup for the joint, adequate tungsten stickout and shape, the proper shielding gas flow for the cup size and joint type, and keep in mind the filler wire addition and how it’ll flow with the joint since it’s added separately.
And now, you need to consider how to adequately set up the software in accordance with the hardware. For example, if you want to weld thin sheet stainless steel, you’d typically use pulsed TIG. Using a 15-degree sharpened tungsten would help with a low fusion profile to prevent excessive heat input. But, if your pulsed peak current is too high, the sharpened tungsten tip can erode and contaminate the weld.
Naturally, if you use a robot, you don’t want to babysit it the whole time. So, if the tungsten erodes, the robot will continue welding with an unfavorable arc.
That’s just one example of how software and hardware with TIG must work together. There’s lots of back and forth between the torch, filler wire setup, robot torch positioning, and power source to get it all right.
Robotic TIG Welding Applications
Robotic TIG welding can be used for almost all manual TIG welding applications and more. Some of the most prominent robotic TIG welding industries are:
- Aerospace
- Defense
- Marine, especially luxury boats and yachts
- Sheet metal fabrication
- Semiconductor
- Food and beverage
- Transportation
These industries require exceptional weld quality. So, TIG welding has been a traditional choice.
TIG provides high accuracy, excellent weld fusion, and weld purity. These characteristics are critical for high-value industries or those with stringent welding standards.
However, with the right MIG welding cobot, you can produce TIG-like welds that are completely reliable and meet the same customer/industry standards as TIG.
While TIG is still widely used, MIG welding has taken over many TIG applications thanks to automation. MIG is far more productive and easier to use. So, you’ll often see many fabrication facilities using robotic MIG.
Learn more in our guide to welding robots, where we discuss all robotic welding types.
Robotic TIG Welding Aluminum
TIG welding is among the best processes for welding aluminum. Robot/cobot TIG welding aluminum can yield excellent results, but there are a few things to consider:
- It’s not recommended to use hot-wire TIG for aluminum due to the low electrical resistance of these wires. So, you can’t use hot-wire TIG to boost welding speed and deposition.
- You must use an HF start for aluminum, so you’ll need a robot with HF shielding.
- Robotic AC TIG for aluminum requires more operator skills.
- If the robot’s TIG torch is too bulky to approach the joint, you can get weld defects from reduced shielding gas coverage. Aluminum is very sensitive to contamination.
- Robotic DC TIG aluminum welding produces dull and less appealing welds than AC TIG and requires significant weld precleaning.
What if you could automate aluminum welding with perfect repeatability without dealing with these process-related issues?
You won’t face these problems with cobot MIG welding aluminum. Our MIG Cobot Welder is far more productive than TIG and much easier to use. And the best part is… It matches the TIG’s weld fusion and appearance!
Robotic TIG Welding Stainless Steel
TIG welding stainless steel is more challenging than aluminum because this metal doesn’t tolerate high heat. What’s worse, stainless steel retains heat. It won’t let it dissipate into the air, making it easier to overheat the part.
Robotic TIG welding can help with heat management as a robot can be very precise with heat input. In particular, pulsed TIG welding can be very beneficial for stainless steel. Pulsed TIG ensures minimal heat input and prevents excessive weld oxidation, part deformation, and loss of corrosion resistance in austenitic stainless steels.
Pulsed TIG requires more skills from the operator than pulsed MIG, but the results are the same. Our Cobot Welder’s Miller Auto DeltaWeld™ 350 allows it to use advanced pulsed MIG for maximum heat control. And you can manage it all in one interface, our smartphone app Beacon. So, no back and forth with the power source to set up the pulse.
Robotic TIG vs. MIG - A Higher Productivity Alternative
Whenever possible, we recommend transitioning from TIG to MIG welding. MIG is faster and easier to use, and with the right MIG equipment, you can produce similar or identical results as TIG.
Many manufacturers who replaced TIG with robotic MIG welding experienced astronomical productivity gains. While the first instinct might be to automate TIG, switching to robotic MIG can yield drastically higher output.
For example, DeAngelo Marine Exhaust Inc., a Florida-based, leading industry expert in the field of marine exhaust systems, achieved a monumental production boost by using our Beacon-powered MIG Cobot Welder. They 10X their welding output and paid off our Cobot Welder with a single large order!
As you can imagine, marine exhaust systems are a TIG welding job. Most fabricators wouldn’t consider MIG as an option. However, DeAngelo Marine decided to give our MIG cobot a shot, and the rest is history. Their welders aren’t overworked anymore, but they still produce high-quality parts, only far faster.
We highly encourage you to listen to the DeAngelo Marine Exhaust case study podcast embedded below. You’ll get insights from their CEO and our cofounder in a podcast hosted by the Manufacturing Happy Hour. Or, you can read the full case study here.