MIG Welding Aluminum: How the Cobot Welder Makes it Happen
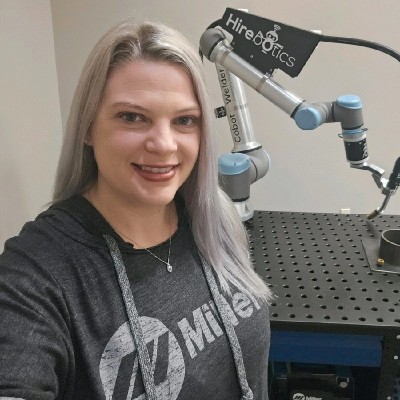
February 20, 2024
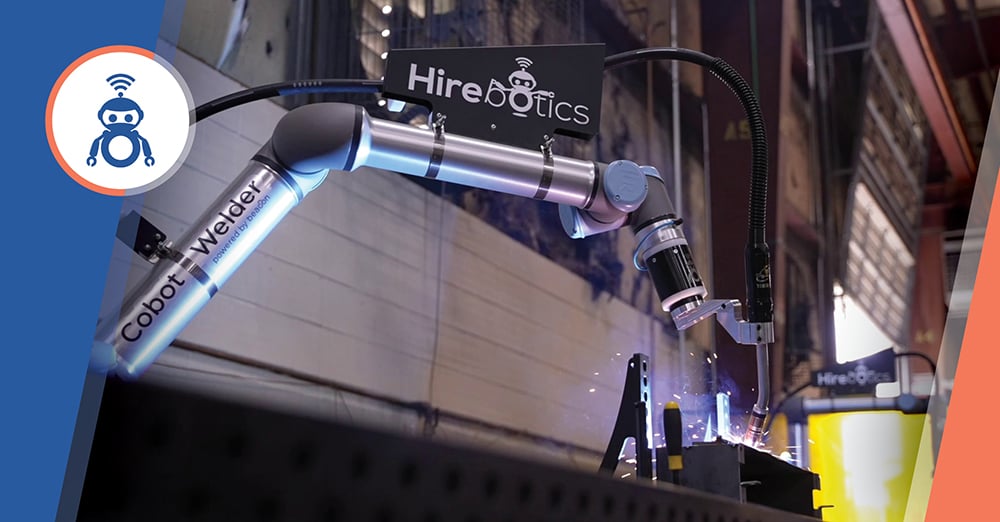
Aluminum welding brings its own set of challenges, particularly with Gas metal arc welding (GMAW) - commonly known as metal inert gas (MIG). MIG welding aluminum requires preparation, the right equipment, and precise techniques to achieve a quality weld - whether a cobot is involved or not. These techniques include push-only weld travel, push-only weld travel angle, a clean aluminum weld surface, and regularly evaluating the condition of process consumables like the liner and drive rolls.
Let's explore how this technique works, why it is challenging, and the possibility of MIG welding aluminum with a cobot.
Understanding Aluminum MIG Welding
MIG welding aluminum is a complex task that requires specialized knowledge and techniques, primarily due to the unique properties of aluminum.Unlike welding steel or other common metals, aluminum presents specific challenges that can affect the quality and strength of the weld. From the properties of the filler wire material to the equipment used, we can find many challenges when welding aluminum.
- Oxidation and corrosion concerns: The tendency of aluminum to oxidize more rapidly than other metals can interfere with welding. While protective against further corrosion, this oxide layer complicates the welding process, leading to potential weaknesses in the weld if not properly managed.
- Aluminum's softness and distortion risk: Due to its relative softness, aluminum is more prone to distortion and damage under the high heat of welding. This characteristic demands careful handling to maintain the integrity of the material.
- Challenges with thermal expansion: Aluminum expands significantly more than other metals when heated. This characteristic can introduce complications in the welding process, potentially leading to uneven welds if not properly accounted for.
- Electrical insulation issues: The electrical insulating properties of aluminum can make it challenging to maintain a consistent welding arc, a key factor in achieving strong and reliable welds.
- Selection of shielding gas and wire: The choice of shielding gas, like pure argon or a mixture of argon and helium, plays a crucial role in the quality of the weld. Similarly, selecting the appropriate aluminum welding filler wire is essential to avoid common defects like porosity.
- Spray transfer technique necessity: Achieving a spray transfer or pulse spray transfer (for thin-gauge or out-of-position welding) are essential for quality MIG welding of aluminum. This technique involves fine-tuning wire feed speed and voltage settings to ensure a stable and effective welding process.
- Importance of proper polarity and settings: Using the correct polarity, such as DCEP, and accurately setting wire diameter, feed rate, current, voltage, and gas flow rate are vital for producing a high-quality weld.
- Surface preparation: Properly cleaning the aluminum surface and removing any oxide layer before welding is crucial to prevent defects and ensure a strong, durable weld.
How to MIG Weld Aluminum
MIG welding aluminum, though challenging, can be achieved with the right setup and understanding of the material's unique properties. Here's how to effectively MIG weld aluminum:
Cleaning and Material Preparation
- Clean the aluminum: Before starting the welding process, clean the aluminum base metal to remove the oxide layer, which can lead to issues like porosity and lack of fusion in the weld. Use an appropriate acid to create a clean surface. Base material cleanliness is the most important part of welding aluminum.
- Proper storage of metals: Store filler and base metals in a dry location with minimal temperature fluctuation to reduce condensation. Bring them into the welding area 24 hours before welding to reach room temperature, which minimizes condensation issues.
Equipment Selection
- Welding power sources: Choose a welding power source designed for aluminum to deliver a tailored arc and reduce spatter. Miller Electric advises that a pulsed MIG welding system can be particularly beneficial, especially for thin-gauge aluminum, as they help reduce rework and scrap.
Filler Metal Selection
- Choosing the right wire: When selecting a filler metal, consider factors like base material composition, joint design, position, weld bead appearance, hot cracking sensitivity, weld strength, and corrosion resistance. AWS A5.10 4xxx, 5xxx, and 6xxx series are commonly used aluminum wire grades, but alternatives like 4943 offer higher tensile strength without distorting the base material.
Shielding Gas
- Confirming Proper Shielding Gas for Filler Metal: The choice of shielding gas depends on the thickness of the base metal and the issues experienced during welding. Argon is the most commonly used, though an argon/helium blend may be needed for deeper weld penetration and improved weld puddle fluidity. Nitrogen, another inert gas for welding purposes, has gained popularity as a helium substitute due to increasing helium costs.
Wire Feeding Systems
- Spool gun and push-pull system: A spool gun can eliminate birdnesting by holding a spool on the gun and feeding the wire only a few inches. While more expensive, push-pull systems offer ergonomic benefits and the financial advantage of using larger spools. Continuous-feed push systems are a newer addition, maintaining constant contact with the wire and eliminating birdnesting.
- Push-only system for specific cases: Feeding aluminum wire through a push-only system can be viable in certain situations. Heavier or larger-diameter wire, such as 1/16 inch, may feed consistently in a push-feed system. Smaller wire diameters are less dependable with this method. The push-only system is an option when push-pull systems are not feasible, offering flexibility in specific welding scenarios.
High-quality aluminum welding is possible when you understand the unique challenges of MIG welding and select the appropriate equipment and techniques.
How the Cobot Welder MIG Welds Aluminum
With the growing shortage of skilled welders, automated welding technologies have become vital for businesses trying to keep up with demand and save on costs.
Using cobots (collaborative robots) for MIG welding aluminum has become a go-to automation solution for manufacturers. Using a setup like the Cobot Welder powered by Beacon and using a Miller S74 feeder makes welding aluminum easier and more precise.
The Cobot Welder uses a push-only feeding system to MIG weld aluminum. This setup is performing well for our clients (stay tuned for our next case study!) For it to be efficient, we do not recommend going for a wire diameter below 3/64”, but you can use 4043, 4943, or 5356 material with this system.
Here’s how the Cobot Welder MIG welds aluminum:
Use the Right Equipment
To start things off, you'll need a few things:
- Polymer liner and brass jump liner: These are key for handling wire sizes from 3/64" to 1/16", and they help you avoid common hassles like bird nesting.
- Contact tips: Depending on what you're welding, you'll need different sizes, like 3/64" and 1/16".
- U-groove drive rolls: These are super important for feeding aluminum wire smoothly.
Recommendations for Optimal Welding
For successful aluminum welding using 4043, 4943, or 5356 material:
- Wire diameter: It's advised not to use wire smaller than 3/64" diameter to avoid feeding problems considering the setup of the Cobot Welder.
- Torch length: A torch length not exceeding 10' is recommended to minimize resistance and bird nesting risks. For older systems with longer torches, a 10' torch specifically configured for aluminum welding can be acquired.
Setting Up Your Cobot
Setting up your cobot for aluminum welding isn't difficult:
- Swap out the drive rolls and liners: First, change these parts, load your aluminum wire onto the feeder, and you're halfway there.
- Ease up on the spool brake: Aluminum's lighter, so lighten up on the feeder's brake to avoid feeding issues.
- Pulse process settings: If you're going with a pulse process, make sure your welder is dialed in for your wire size, material type, and gas. The feeder's Profile Pulse setting can give your welds that neat, TIG-like look.
Following these steps, welding aluminum with a cobot is very effective and can provide you the “stack of dime” look usually obtained with TIG welding.
Benefits of MIG Aluminum Welding with a Cobot
MIG welding with a cobot offers several benefits, including:
- Increased precision and consistency: Cobots deliver highly precise and consistent welds, improving overall weld quality.
- Enhanced productivity: Automating the welding process with cobots can significantly increase productivity and throughput by reducing rework and scrap.
- Reduced labor costs: Cobots can operate continuously, taking on repetitive tasks and reducing the need for manual labor and associated costs.
- Improved worker safety: By handling hazardous tasks, cobots minimize the risk of injuries to human workers.
- Flexibility: Cobots are adaptable to various tasks and can be easily reprogrammed for different welding jobs.
- Ease of use: They are designed to be user-friendly, requiring minimal training for operation.
What if you could MIG weld aluminum with perfect repeatability, transforming this challenging weld into a seamless and efficient process?
MIG Welding Aluminum with the Beacon App
Our Cobot Welders make MIG welding aluminum a smooth and efficient process. Paired with our Beacon platform, you’ll be in running production within a few hours when you receive your system.
Imagine programming a cobot for welding tasks as easily as using a smartphone app. That's exactly what the Hirebotics Beacon app offers. Beacon is changing robotic programming by replacing the traditional, complex teach pendant with a simple, intuitive app accessible via phone or tablet. This innovation makes cobot programming more accessible and flexible, even for those without any prior programming knowledge.
Key Advantages of the Beacon App:
- User-friendly interface: Beacon moves away from complex programming languages, using pre-defined welding terms that are easy to understand. Any welder can start using it right away without programming expertise.
- Real-time monitoring and alerts: The app allows for the continuous monitoring of cobot operations, providing alerts for system errors or stops. This feature enhances efficiency and minimizes downtime.
- Flexibility and scalability: With support for multiple users and teams, Beacon makes it easy to scale up operations and provide the right editing access to the right people. You can add more cobots and users as your business grows without any hassle.
- Cost-effective: The app eliminates the need for specialized programmers or welders trained in robotics, leading to significant cost savings.
Our cobot welding system is cost-effective and easy to set up and operate, making it a perfect fit for shops engaged in diverse production. This approach is perfect for shop owners looking for efficient automation solutions without the hefty investment or complicated setup of traditional robotic welding systems.
Find out how one of our clients, DeAngelo Marine Exhaust, has already witnessed transformative results, including a tenfold increase in production, improved quality, and shorter lead times.
Your Aluminum Welding Cobot Solution
Facing the challenges of MIG welding aluminum, especially with a growing welder shortage?
Hirebotics' Cobot Welder, enhanced by our intuitive Beacon app, offers a solution that your current welders can learn and operate in a matter of hours. This technology also ensures consistent, high-quality welds, eliminates human fatigue and errors, and requires minimal training.
Explore how the Cobot Welder can enhance your operations. Schedule a demo to see for yourself and begin your journey toward advanced, efficient welding solutions.