Welding Cobot Programming: From a Teach Pendant to Your Phone
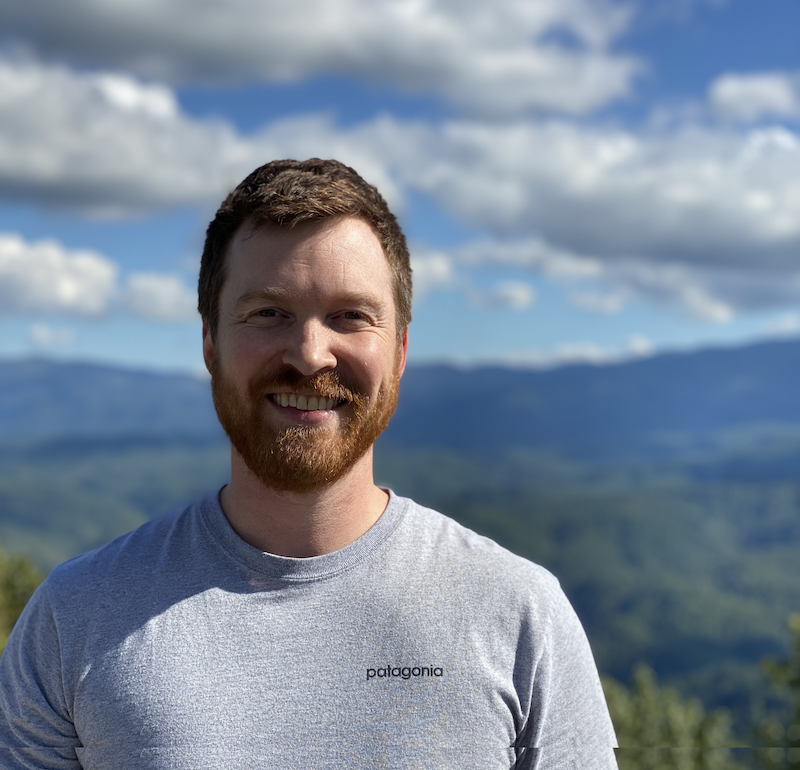
February 1, 2023
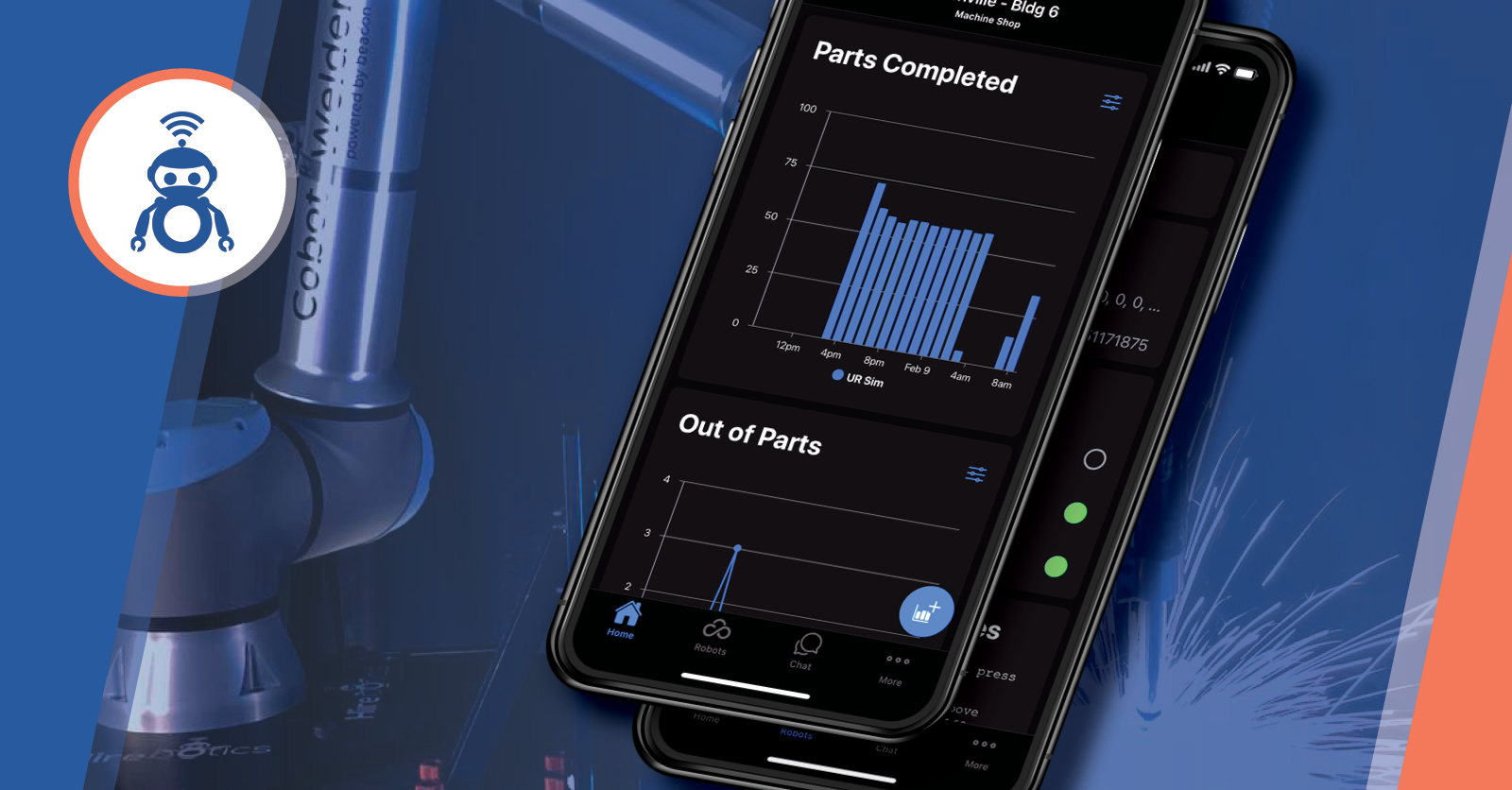
As manufacturers transition their labor-intensive workflows to industrial automation, many may still not be aware of the challenges of robot programming.
There are many challenges to robotic programming. Oftentimes, it requires in-depth expertise to understand the robot or cobot’s logic. If your company doesn't already have in-house expertise, it will need to hire third-party expertise, which can be costly over time.
The reason? You need to consider the setup of the automation cell and the production changes, product updates, and constant optimization of the cell.
Also, due to the tight labor market, robotics experts may change companies, taking a business’ robotics organizational memory with them. It’s back to square one.
Currently vetting potential welding robot and cobot vendors? This article will give tips on evaluating robotic solutions' programming capabilities to help you overcome their associated challenges.
Types of Cobot Programming Methods
First, let’s look into the different programming methods that are available for robots and cobots. The two most common programming methods are teach pendants and offline programming software; however, there are other means, including global/joint/tool/workpiece coordinates and lead-through.
Teach Pendant Programming
Teach pendant programming entails using an electronic device to interact with and control the motions of industrial robots. With a teach pendant, robotics programmers can “teach” specific points and path sequences (trajectories) to a particular brand of robots using a proprietary programming language, usually code-based.
Some cobots have entered the market and innovated teach pendant programming. As an example, Universal Robots designed their collabot programming language to be graphical or block-based therefore simplifying the traditional code programming.
Offline Programming Software
To reduce production downtimes caused by shop floor programming, offline programming softwares allow specialists to program an industrial robot or cobot on a computer based on the equipment’s hardware and brand.
Unfortunately, these two robot programming approaches cause a set of challenges that can prevent many businesses from either adopting automation from the get-go or fully seizing the tremendous efficiency, quality, and capacity advantages robotization can afford.
The new solution...
App-Based Cobot Programming
Luckily, robotic technologies and software development advances have paved the way for a new generation of app-based cobot programming solutions for cobots.
Let’s look into the advantages of app-based programming and how it differs from one of the most widely used programming methods for robots: teach pendants.
Cobot’s Teach Pendants or App-Based Programming?
There are several hurdles with using teach pendants for controlling robots and cobots, compared with app-based programming. Here are the top differences and what they can mean to a manufacturer’s throughput and performance.
1. Ease of use
The first issue with teach pendants is usability. The vast majority of teach pendants required skilled programmers to set up, configure and operate.
Technicians with little-to-no programming experience often feel intimidated as they try to figure out the myriad of buttons to push and screens to program a robot or cobot for each distinct application and each robot brand the company may have.
In this day and age, robot programming experts are hard to recruit and retain. Onboarding and training non-programmers can be lengthy and costly at best, impacting production cycles and lead times.
On the flip side, programming a robot or cobot with an app designed for a specific application and with non-robotics specialists in mind can facilitate use.
For example, Hirebotics’s Beacon is a free software solution that can be accessed from a smartphone or tablet. Most people are familiar with apps and smartphones or tablets in their day-to-day lives.
What could take weeks to ease the learning curve with a teach pendant can take just a few hours with an intuitive app that doesn’t inundate users with tons of robot jargon, like “TCPs, payloads, COG, coordinate systems, etc.,” that are more geared towards robot programmers.
2. Generic vs. Application-Specific Cobot Programming
Many robots and their teach pendants are built generically; that is, they can be used for almost every imaginable purpose. Now, while that provides great versatility to program even the most complex workflows, the technician must know how to develop logical programs.
Again, these generic tools can slow down manufacturing processes as the robot, or cobot has to be completely programmed for each application. The programming times and complexities are worsened for companies with high-mix/low-volume production environments.
App-based programming solutions can be purpose-built for an application, such as welding. Operators don’t have to understand robot programming—but they do need to understand the application involved.
A case in point? A welding cobot with an app allows welders to program the equipment using an interface that features the lingo they are accustomed to for their jobs. Programming with an app designed for a precise application makes working with a cobot and robot a breeze.
3. Flexibility and “forgiveness”
With a teach pendant, users are tied to the robot. For them to be off the pendant, a company must invest in offline programming, which is inherently complex, or establish a connection from a PC or laptop to access it from elsewhere.
Contrarily, programming apps can be designed to consider tool features out of the box, especially if they have been developed for a specific application. If an app for robotic programming in welding applications, like Hirebotics, considers that a robot will have a welding torch, it can already be set up with all the required TCP and tool details for specific tasks related to the welding torch.
4. Cloud Advantages & Capabilities
Apps can easily be cloud-based, which offers users the flexibility to quickly and easily work away from the robot without even needing to be by a computer for remote work. Ideally, you can just tap the programming app from a mobile phone or tablet, set up the programming sequence, and you’re done!
Moreover, if there is a problem with the robot or cobot, the off-site operator can easily understand what’s happening and quickly remedy the situation.
The cloud-based feature can also allow automatic version saving. If a user changes something to the cobot program that doesn’t work, they can swiftly restore the prior version, empowering them to work on the system without fearing “messing up.” This is a huge time-saver for projects with extremely tight deadlines as it eliminates many of the back and forth of conventional teach pendant workflows.
Beacon - App-Based Programming of Welding Cobots
While more OEM companies are developing app-based robot and easy cobot programming solutions, some, such as Hirebotics and their Beacon app, offer game-changing features for companies that use their welding cobot, Cobot Welder:
![]() |
|
![]() |
|
![]() |
|
![]() |
|
![]() |
|
![]() |
|
As you can see, it is the dawn of a new era in robot and cobot programming with next-generation apps that leverage the best practices and evolution of many popular consumer-based apps.
The democratization of welding robots is well underway. Are you ready to embark on the journey?