What is a Cobot? | Benefits and Applications
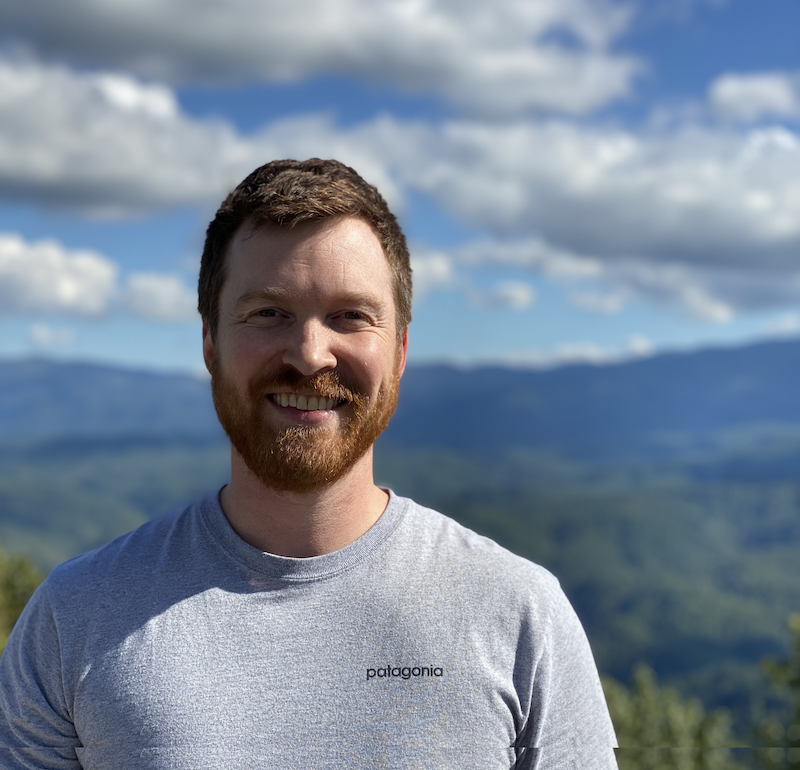
March 14, 2023
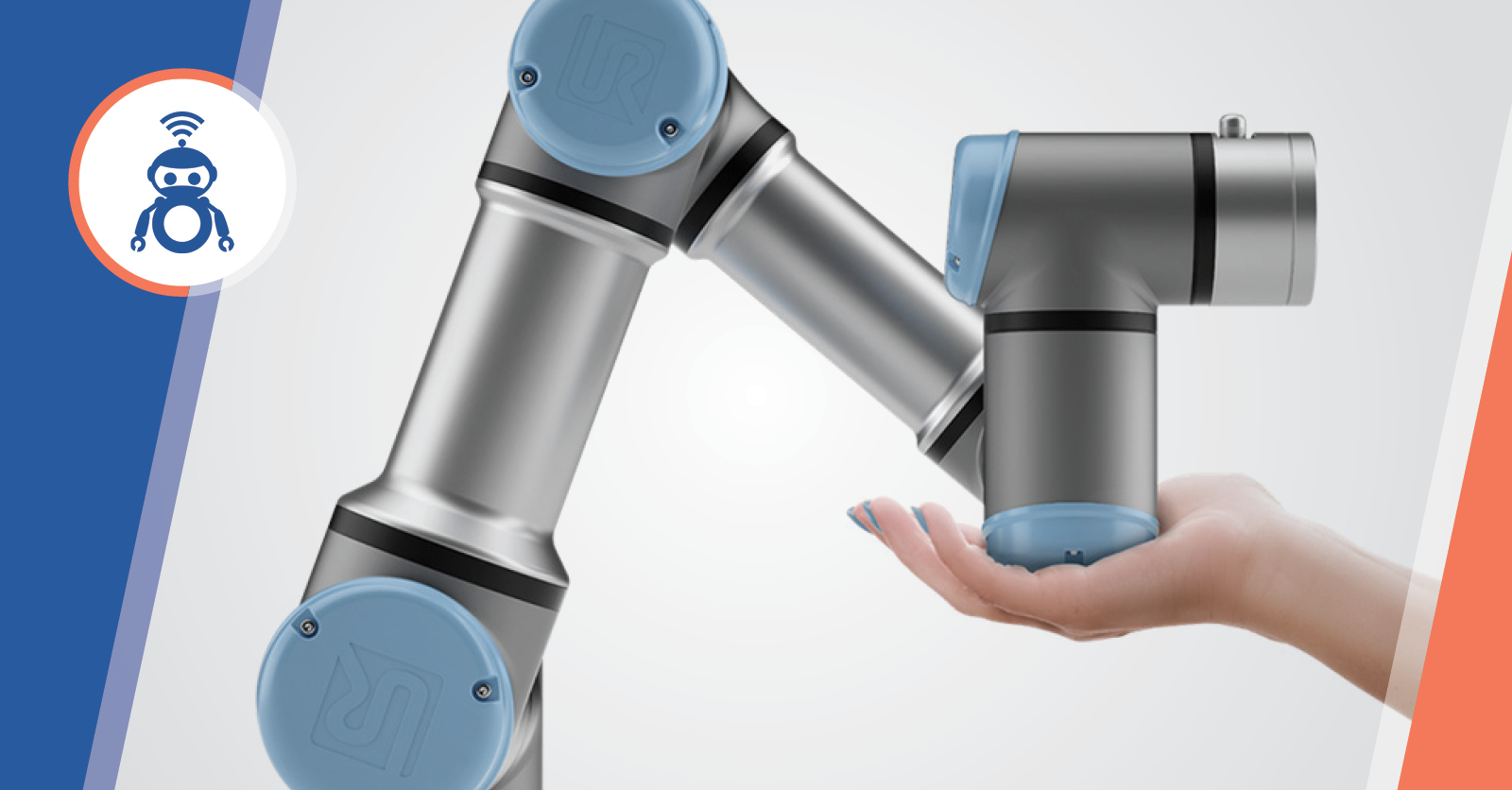
Collaborative robots, or "cobots" for short, have become an increasingly popular topic in the world of manufacturing.
Let’s answer these questions in this article:
- What is a Cobot? (of course)
- How different is their programming?
- Why use collaborative robots in your factory?
- How can they help your production tasks?
- How much do they cost?
- How can cobots streamline your operations and increase efficiency?
Definition of a Cobot
A collaborative robot, or cobot, is an industrial robot designed to work collaboratively with human operators in a shared workspace. Unlike traditional industrial robots that are often large and dangerous, cobots are generally smaller and designed to be safer to work around.
They are equipped with a safety mode that allows them to work alongside humans while significantly limiting the risk of injury or harm. According to the international standards ISO 10218 part 1 and part 2, there are four types of collaborative features for robots.
What makes a robot a cobot?
To be collaborative robots, the robots must feature one of the following:
- Safety Monitored Stop
- Hand-Guided Programming
- Speed and Separation Monitoring
- Power and Force Limiting
Cobots vs. Traditional Industrial Robots
What is the difference between a cobot and an industrial robot?
There are many differences but the main difference between collaborative robot arms and traditional industrial robots lies in their level of interaction with human workers. Unlike traditional robots, which are often placed in cages or other restricted areas to keep humans at a safe distance, cobots are designed to work alongside humans collaboratively.
The other differences are around the topics of safety, ease of programming, and affordability.
Safety
Cobots are typically equipped with advanced safety features that allow them to operate safely around humans without the need for barriers or other safety measures.
Ease of programming
Another key difference is the ease of programming and operation. Traditional robots typically require robot programmers to set up and program. Cobots are usually designed to be intuitive and user-friendly. This makes them ideal for small and medium-sized businesses that may not have the resources or expertise to operate traditional industrial robots.
Affordability
Finally, cobots are typically more affordable and flexible than traditional robots, which makes them an attractive option for businesses looking to implement automation cost-effectively and quickly.
How to Program a Cobot
There are several methods of programming a robot, including traditional (offline) programming, teach pendant programming, and hand-guided programming.
Traditional programming involves writing code to control the cobot's movements and actions. This requires a high level of technical knowledge and expertise and can be time-consuming. This is a more advanced method that involves using specialized software on a computer and understanding the kinematics of the robot.
Teach pendant programming uses an interface connected directly to the robot, allowing you to move it physically while programming (recording positions). Traditional teach pendant will provide controls following the axis systems of the robot and still requires an understanding of the kinematics behind the robot's movements. You can also program external systems through advanced commands like I/Os and macros. They usually follow specific language or code of their company brand.
The good news is that cobots have started to change this old way of programming robots by redesigning the teach pendant interface to be more intuitive and graphical.
Moreover, with the event of cobots, a new programming method is now more accessible: Hand guiding. As of now, it might be the most intuitive method for programming a cobot. Hand guiding involves physically moving the robot arm from point to point to build a program.
This method allows even non-technical personnel to program the cobot quickly and easily, making it an ideal solution for small and medium-sized businesses that may not have the technical expertise or resources for traditional or offline programming.
Overall, the method of programming a cobot depends on the complexity of the task and the available resources.
Cobot Benefits
Collaborative automation offers many benefits to manufacturers across different industries. Here are a few of the most significant advantages:
- Improved safety
- Increased efficiency
- Flexibility
- Cost-effectiveness
- Improve quality control
Improved Safety
Cobots are designed for human safety, as they are equipped with sensors and software that enable them to detect and respond to human presence. This makes them much safer to work around than traditional industrial robots, which are typically kept in cages or behind safety barriers.
Increased Efficiency
Cobots can perform tasks faster and more accurately, improving overall productivity and reducing costs. Cobots can perform repetitive tasks without fatigue or error, allowing human workers to focus on more complex tasks that require creativity and problem-solving skills.
Flexibility
Cobots can be programmed to perform a wide range of tasks and can easily be reprogrammed for new applications. This makes them ideal for small and medium-sized businesses that may not have the resources or expertise to implement complex automation systems.
Additionally, smaller businesses might not have the production volume required to justify large, dedicated automation systems. Flexibility is crucial for protecting these manufacturers’ investment in robotics.
Cost-Effectiveness
Cobots are generally more affordable than traditional industrial robots due to how simplified their cell can be–making them accessible to a wider range of businesses. They also require less maintenance and training than traditional robots, reducing overall costs and improving ROI.
Improved Quality Control
Cobots can perform tasks with a high degree of accuracy and consistency, reducing errors and improving overall quality control. This is particularly important for manufacturers in specific industries, such as electronics, where even small errors can significantly impact product quality and customer satisfaction.
Overall, collaborative robots offer many benefits to businesses looking to improve their operations and increase efficiency. From improved safety to increased productivity and cost-effectiveness, cobots can help businesses stay competitive and adapt to the changing demands of the market.
Common Collaborative Robot Applications
Collaborative robots can be used in various industries and applications. Their versatility is one of their primary strengths for manufacturers.
Here are a few of the most common cobot applications.
Assembly
Cobots can assemble products, such as electronic devices or automotive components. They can perform tasks such as screwing, gluing, and inserting components with a high degree of accuracy and consistency.
Machine Tending
Machine tending is one of the more common collaborative robot applications. Cobots’ pick-and-place capabilities and ability to work alongside people make machine-tending applications a natural fit. Some manufacturers are achieving lights-out production with cobots in machine tending applications.
Packaging
Cobots are important to the packaging industry. They can package products, such as food, beverages, or consumer goods, into boxes or containers. They can also perform tasks such as labeling and palletizing, improving overall efficiency and reducing labor costs.
Material Handling
Perhaps the most basic task for cobots is material handling. Cobots can move materials and products from one location to another, reducing the need for human workers to perform mundane manual lifting and transport tasks. This can help reduce the risk of injury and improve overall productivity.
Quality Control
Cobots can perform quality control tasks, such as inspecting products for defects or inconsistencies. Quality control, while important for many industries, are critical for industries such as aerospace and defense systems. Cobots can perform tests or measurements on products, ensuring they meet the required specifications for that product or industry.
Welding
Cobots can even handle welding tasks, such as spot welding or arc welding. Cobots are built to tackle the high-mix, low-volume production environments common to small and medium-sized welding shops. They can perform these tasks with a high degree of precision and consistency, even better than human welders, improving overall quality control and reducing the risk of errors, defects, and safety incidents.
Collaborative Robot Brands
There are several players in the collaborative robot market creating high-quality products for industrial manufacturers. While the cobot family is still relatively new, here are a few manufacturers known for their strong cobot lineup.
![]() |
UR3e, UR5e, UR10e, UR16e, UR20* |
![]() |
TM5-700, TM5-900, TM14, TM12* |
![]() |
IIWA 7, IIWA 14, and the new LBR* |
![]() |
Yumi, GoFa, Swifti* |
![]() |
CR-4iA, CR-7iA, CR-14iA, CR-15iA, CR-35iA* |
*Lists potentially non-exhaustive
Universal Robots
Universal Robots is perhaps the most well-known cobot brand. UR commands the greatest cobot market share and offers a range of collaborative robots designed for small and medium-sized businesses. Their robots are known for their flexibility, ease of use, and affordability, making them a popular choice for businesses looking to implement automation systems.
Universal Robots offers five different models, each with different payloads and reach, to suit a wide range of applications: UR3e, UR5e, UR10e, UR16e, UR20.
Techman Omron
Techman Omron is a Taiwanese-based manufacturer of collaborative robots that offers a range of robots designed for various applications. Their cobots are known for their ease of use, thanks to their intuitive programming interface and built-in vision system that enables them to recognize and locate objects.
Techman Omron cobots are: TM5-700, TM5-900, TM14, TM12.
Kuka
Kuka is a German-based company that offers a range of industrial robots, including collaborative robots. Their cobots are known for their versatility and precision, making them suitable for various applications. Kuka cobots are designed to be highly adaptable and can be easily programmed to perform complex tasks. They also commonly have advanced safety features, such as collision detection sensors and safety-rated control systems.
Their cobot models are: IIWA 7, IIWA 14, and the new LBR.
ABB Robotics
ABB is a Swiss-based company that offers a range of industrial automation products, including collaborative robots. ABB’s cobots are known for their high payload capacity and speed, making them suitable for heavy-duty applications such as material handling and welding. Like Kuka cobots, they are also often equipped with advanced safety features, such as force-sensing technology that enables them to detect and respond to human presence.
Their cobots are: Yumi, GoFa, Swifti.
FANUC
FANUC is a Japanese-based OEM that offers a range of industrial robots, including collaborative robots. FANUC cobots are known for their precision and reliability, making them ideal for applications such as assembly, material handling, and painting. They are equipped with advanced vision systems that enable them to recognize and locate objects for a variety of applications, allowing them to handle more complex and unpredictable tasks.
Their cobot models are: CR-4iA, CR-7iA, CR-14iA, CR-15iA, CR-35iA.
Cobots in Industry
Collaborative robots are highly flexible, allowing them to operate in many applications across most industries: metals, pharmaceuticals, automotive, electronics, packaging, plastics, food and beverages, etc.
Let’s look at how manufacturers use cobots today in those key industries.
Metals
Collaborative robots are commonly used in the metals industry for tasks such as machine tending, welding, and assembly. The cobot’s flexibility and ease of programming allow it to excel in these high-mix environments. Cobots can help improve safety by reducing the need for human workers to perform manual handling tasks, enhancing consistency and productivity for tasks like welding, and improving overall efficiency and productivity.
Pharmaceuticals
In the pharmaceutical industry, cobots can be used for tasks such as packaging, quality control, and laboratory automation. The high-volume production environment leads to plenty of repetitive and mundane tasks. Collaborative robots can help improve accuracy and consistency in these tasks, while also reducing the risk of contamination and improving safety.
Automotive
Once the birthplace of industrial robotics, cobots are now having an impact on automotive manufacturers. Collaborative robots are widely used in the automotive industry for tasks such as assembly, painting, and material handling. Cobots can help improve speed and efficiency in these tasks by enhancing workers’ output, while also reducing the risk of injuries to human workers.
Electronics
In the electronics industry, cobots can be used for tasks such as circuit board assembly, quality control, and material handling. Their low-payload capacity and soft touch are welcome for electronics manufacturers. Collaborative robots can help improve speed and accuracy in these tasks, while also reducing the risk of damage to delicate components.
Packaging
Collaborative robots are commonly used in the packaging industry for tasks such as palletizing, case packing, and labeling. Cobots can help improve efficiency and accuracy in these tasks, while also reducing the need for manual labor.
Plastics
The plastics industry has come under increasing demand in recent years, putting a strain on manufacturers to keep up with production. In the plastics industry, cobots can be used for tasks such as injection molding, assembly, and material handling. Collaborative robots can help improve speed, consistency, and efficiency in these tasks, which is critical for manufacturers hoping to meet high production demands from their growing list of customers.
Food and Beverage
Increasing food and worker safety regulations have led to more automation in the food and beverage industry. Collaborative robots are increasingly used in this industry for tasks such as picking, packing, and palletizing. Cobots can help improve hygiene and safety in these tasks, reducing the need for manual labor and improving overall efficiency.
What is the price of a Cobot?
On average, cobots can cost anywhere from $30,000 to $65,000 for just the robotic arm. However, the cost of a collaborative robot can vary depending on the brand, payload capacity, and reach, among other factors.
It is important to remember that the cost of implementing a full cobot solution can be much higher than just the cost of the arm itself. Additional costs may include end-effectors, safety systems, programming software, and installation costs. Furthermore, depending on the application and level of customization required, the total cost of a cobot solution can easily surpass $100,000.
Nonetheless, when compared to traditional industrial robots, which can be roughly twice the cost of a cobot solution, cobots offer a more affordable and flexible solution for small and medium-sized businesses looking to automate.
Cobots Help Manufacturers Get Started in Automation!
Cobots are an excellent way for manufacturers to dip their toes into the world of automation. Unlike traditional industrial robots, cobots are easy to program and operate, making them ideal for small and medium-sized businesses with limited automation experience.
By implementing cobots, manufacturers can quickly improve production capacity, reduce errors, and empower human workers to perform more productive and complex tasks.
At Hirebotics, we develop easy-to-use automation solutions (such as our Cobot Welder) that can help you get started with cobots quickly and easily. Our automation system uses an app from where your welders and operators can teach the cobot to weld in a matter of hours only.
Contact us today to learn how we can help you get started with welding automation!