Welding Robot Programming: Demystifying "Ease-of-Use"
December 15, 2021
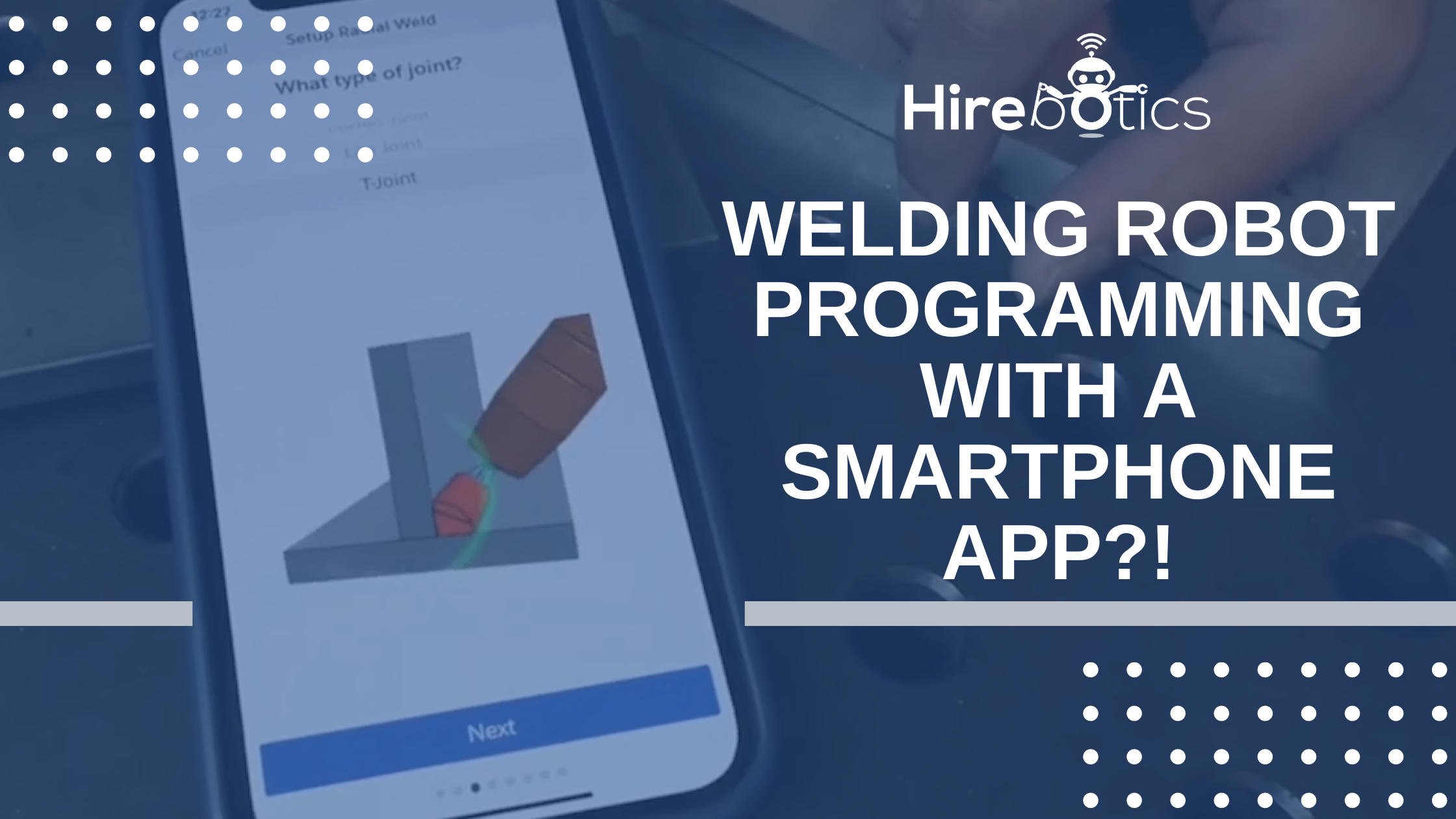
You’ve decided that automation with a welding robot will positively impact your production. However, one of the primary considerations you have to think about is how soon can the robot be in production. We are seeing more and more welding solutions lowering down the barrier of complexity and this seems to have a good impact on time to production.
How does easy programming speed up the integration in your production? What are the other advantages of straightforward programming of your new robot? What are the robot programming types on the market? Let’s find out.
How Easy and Fast Programming Speed Up Your Automation Efforts
Let’s quantify what easy and fast programming means. This is because the words ‘easy and fast’ are subjective and have been largely overused in the robotics industry. What is easy and quick for Elon Musk or an expert robot programmer probably doesn’t hold for most people.
“Fast and easy” robot programming should mean that most of your employees can learn and operate the robot, even those who don’t have any robot programming experience. If it can be learned by people experienced in the task (and not robot programming), you have a powerful solution in your hands.
In welding operations, it means that your welders could easily learn how to set up and program this new welding robot. Being experts in welding, they would control the methods and quality while increasing their output. This will have a great return for your company.
Faster Deployment
“Easy and fast” programming should also mean easier deployment. When a robot is simple to program, it can be put in production faster - we have even seen a couple of hours from box to production. More rapid deployment means less downtime, and time is gold for medium-sized welding businesses like yours.
Technology Adoption
Robotics can be intimidating to your employees. Having a robot welder that’s accessible to your welders can ease the adoption. You don’t need a dedicated robot programmer to run it. Your welders get used to it by learning it and seeing how this new tool can help them. It’s then easier for them to accept it as part of their team and ultimately speed up the automation process for your welding production.
Lower Welding Costs
With faster deployment, you’ll also see faster impacts on your welding costs. You can lower the cost of your welds by addressing the cost drivers that affect the price: labor and rework or scrap costs. Managing these cost drivers translates to more significant revenue for your company and happier customers because of the faster turnaround time.
Other Advantages of Accessible Robot Programming
Choosing a robot that’s easily programmable means you don’t need to hire robot programmers. However, this is not the only advantage of easy programming. Let’s look at a couple of essential points.
Flexibility
Easy programming means more flexibility for you and your team members. You can redeploy the robot to do different tasks and productions. The simpler it is for your team less downtime your robot will have. This will maximize your investment.
Your Welders are the Programmers
Using a robot system that is accessible to your current employees means that there is no need to onboard a robot programmer. Ultimately programmers are as hard to find as welders. They can also be more expensive. Empowering the welders to program the robot by themselves is good for the acceptance of the technology and your bottom line.
No-Code Programming of the Cobot Welder
The Cobot Welder by Hirebotics stands apart in terms of programming because it is not using the standard UR robot teach pendant or a URCap. Hirebotics developed an app to be able to teach the robot without touching the teach pendant. This also means that your team doesn’t need to understand robot logic and programming.
The functions or nodes are designed for welding applications to the point that a welder will rapidly understand how to use the application. The robot has a smart puck to guide it to different positions. They are then recorded at a press of a button on the puck.
Let’s Program a Linear Weld
We’ve been talking about how different the Cobot welder’s app is, so let’s put it to the test by programming an easy linear weld.
We’ve outlined the crucial steps:
- Create a new program and name it.
- It will ask for the welding parameters like speed, feed, weaving...
- Then grab the puck and press the green button to move the robot in its freedrive mode. Position the robot to your desired starting position.
- The blue button is what you use to record the position.
- Do this for the final weld position and you have your linear weld saved.
- Now to be able to run this weld, the “program” needs to be initiated by the buttons on the operator’s panel (physical buttons on the cobot Welder’s table).
- For this Create a New Playlist and add the weld/part you just created.
- You are now ready to push the start button on the operator’s panel. Make sure that your arc on/off button is turned off if you are doing a dry run.
Congratulations, you’ve successfully programmed your first weld!
Programming for All
With technology, programming a robot became accessible to everyone, and not just people with programming skills. A robot welder that’s easy to program empowers the people who will use it - your welders.
Do you want to learn more about welding? Download our Getting started with welding cobots Ebook for free!