How Cobot Welding is Solving the Welding Industry Challenges
July 15, 2021
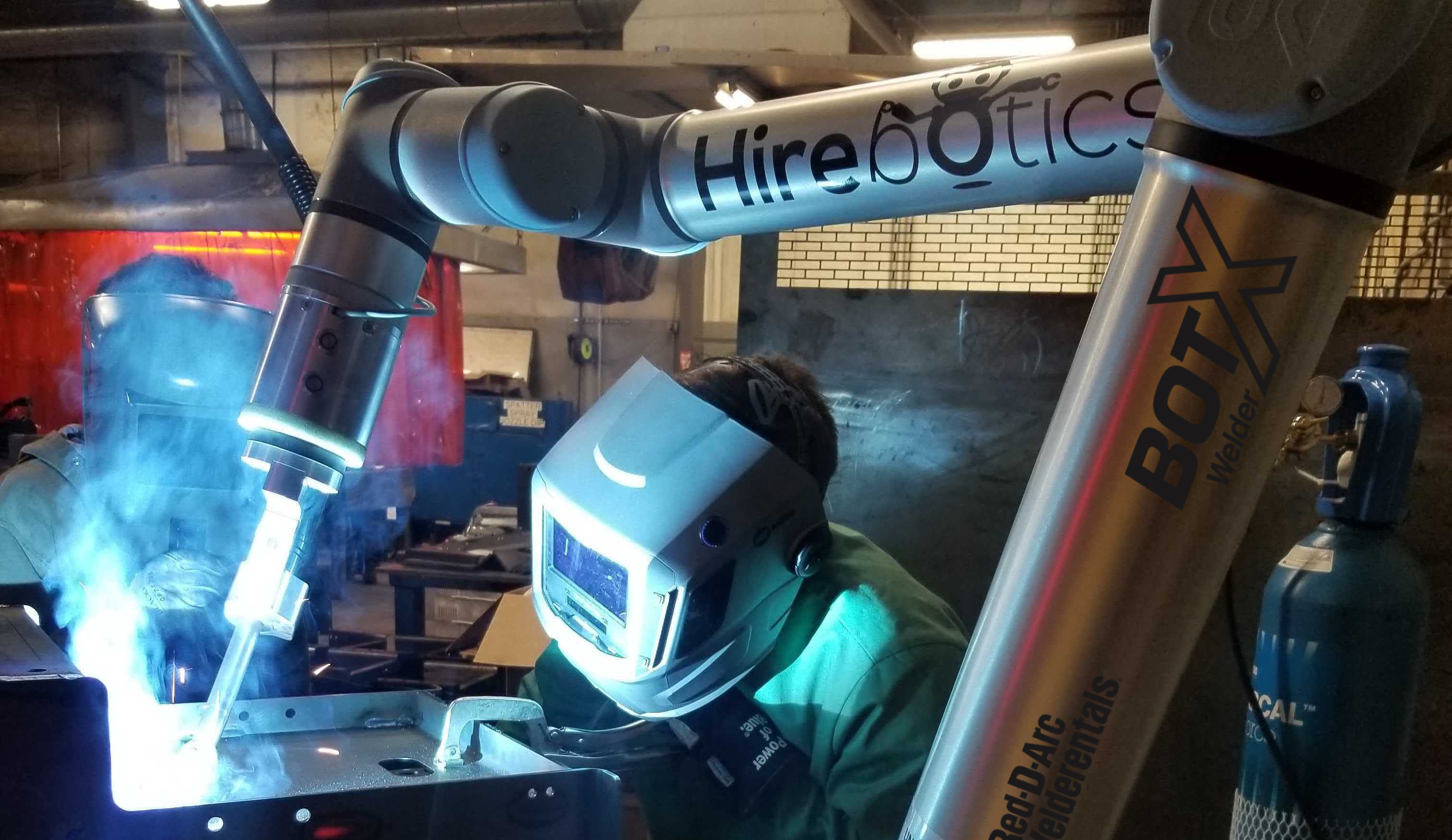
Does your business have a hard time finding skilled welders? Are you struggling with high welding costs that cut through your revenue? Do you find yourself rejecting orders because you can’t keep up with the demand?
Automating your welding operation holds the key to solving these problems. How exactly? Let’s find out, but first, we need to better understand the challenges you face with your welding operations.
Welder Help Wanted! - Facing the Welder Shortage
The current welder shortage the industry faces has been an issue for a long time. The American Welder Society projects a 400,000 welder shortage by 2024. If you want to see this trend for yourself, go to any internet job board. You'll see the copious number of companies wishing to hire welders without any takers.
The average age of welders in the USA is 55. And hiring welder help is difficult because of the aging workforce. Young people are difficult to encourage to take up welding as a career. Young people are reluctant because they see the job as monotonous, dirty, and not paying well.
The welder shortage is nothing new. Back in 1999, the American Welder Association identified it, and they suggested investment in vocational welder education as a solution to the problem. This solution is an excellent one. But, it takes time for it to grow.
Currently, there is a strong push for students to invest in a college education which trends to veers young people away from vocational studies like welding. Unfortunately, twenty years later, the problem of welder shortage still exists. And worse than before.
Pricing Competition is Fierce - Facing High Welding Costs
Is reducing your welding cost part of your managing priority? Whether to stand out among the competition or increase your bottom line, welding costs are not to be neglected. Here are the main welding cost drivers that you can start to address:
- Labor costs - Studies show that 85% of welding costs come from labor. So, labor is where you need to cut costs, but how? Think about how you can optimize your welders’ time and work so that they can produce more and faster.
- Reject, rework and scrap costs -Reduce those by detecting welding defects early on. When you don't notice a missed or faulty weld earlier, costs can escalate at every stage of the welding process. For example, you can quickly repair a defective weld with minimal expense if caught early on. But a faulty weld detected after painting can cost more. It costs more because you'll have to strip the paint out and return the wrong part to the weld cell for repairs.
Moreover, the worst-case scenario of a defective piece is bodily harm or property damage. These, in most cases, will result in expensive lawsuits against your company. - Post-weld operations costs - Examine your welding process. Post-weld grinding of spatter and excess weld metal can eat up your welders’ time and increase your lead time. With cleaner welds done the first time, you’ll save time and money.
- Non-value added tasks costs - Avoid paying overtime by streamlining your welding process. You want to reduce any unnecessary steps that cause delays and more welder time than needed.
Increasing Productivity
The welding industry is very competitive. New materials and processes are continually being introduced. To stay afloat, you need to improve productivity. High productivity translates to increased profitability.
You can improve productivity by improving the consistency in your weld operations. Because of human constraints, weld quality will vary. Even the most skilled human welder in your company is sure to have a bad day. And the continuous monotony of the job can lead to tiredness and fatigue. Fatigue can manifest itself in the roughness of the seam weld and post-weld operations increase.
Quick Tip - Another way to up productivity is to examine your weld process with an open mind. Understand where the bottlenecks lie and either eliminate or replace them. For example, replace processes that cause unnecessary downtime.
Minimizing quality issues can also boost productivity.
Unpredictable Welding Costs and Lead Time
In any welding shop, knowing how to calculate welding costs and time is essential. These two things are vital for client quotations and production lead time.
The challenge comes from calculating time as it relies on the human variable. We all know humans can be highly unpredictable. No matter how much allowance you give in your calculation, sometimes it's not enough. Delays can happen; your welders can get tired or have a bad day that can affect their work. This normal human behavior can wreak havoc on your lead time.
As you know, clients are not happy with delays and long lead times. Not having a surefire way to quote your jobs might lead to your company losing contracts or rejecting welding jobs.
OK, enough rambling about the challenges you face daily, let’s talk about overcoming these!
We've Identified the Challenges; What are the Solutions?
Automation is the way forward in solving these challenges in the welding industry. Now, if we talk about welding automation, you might think about robot welding. It sure looks like a very viable solution. But if you consider it a bit more, you'll see that robotic welders might not be the best solution for all manufacturers.
The first robotic welders were designed to work in the automotive and heavy equipment industry. They are used to automate repetitive and high-volume welding tasks. These robots can be more expensive with their rigid installation and jigs placed in a robotic welding cell. A justified practice because it's dangerous for humans to get near them. Plus, they need expert mechanical engineers to program.
These robots work well for high-volume productions. But not so much for the low volume, high mix environments of most small and flexible welding operations. But what should you do if welding automation is still needed? This is when we introduce collaborative robots.
Collaborative robots or cobots are robotic arms designed to work with humans. Unlike traditional robots, they are using technologies to work alongside your workers. They can easily be programmed and repurposed to do multiple tasks. They fit well with the volume, high mix productions.
Welding cobots can take over monotonous and repetitive weld jobs. This extra hand helps augment the welder shortage as your welders can now use them to do more consistently. Moreover, the high-tech environment encourages young people to get on board as welders.
They offer consistency and quality welding as they take over the monotonous jobs. This frees your experienced welders for other more critical and value-added tasks.
The efficiency of welding collaborative robots allows your company to be able to accept more jobs. It also lowers your lead time. The quality and the speed of weld jobs are an advertisement in themselves. This can help drive people to your business.
Unlike traditional robots, they are easy to program, and some even are accessible for welders without programming knowledge to operate them!. Take, for example, the Cobot Welder by Hirebotics, which only requires a phone app to operate. Your existing welders can then handle and maintain the cobot with little training.
The Takeaway
The Cobot Welder is not a cure-all miracle. And it will take time to be able to address all the challenges. But it's certainly a good place to start.