Welding Safety: How Welding Robots Can Mitigate the Risks
February 22, 2022
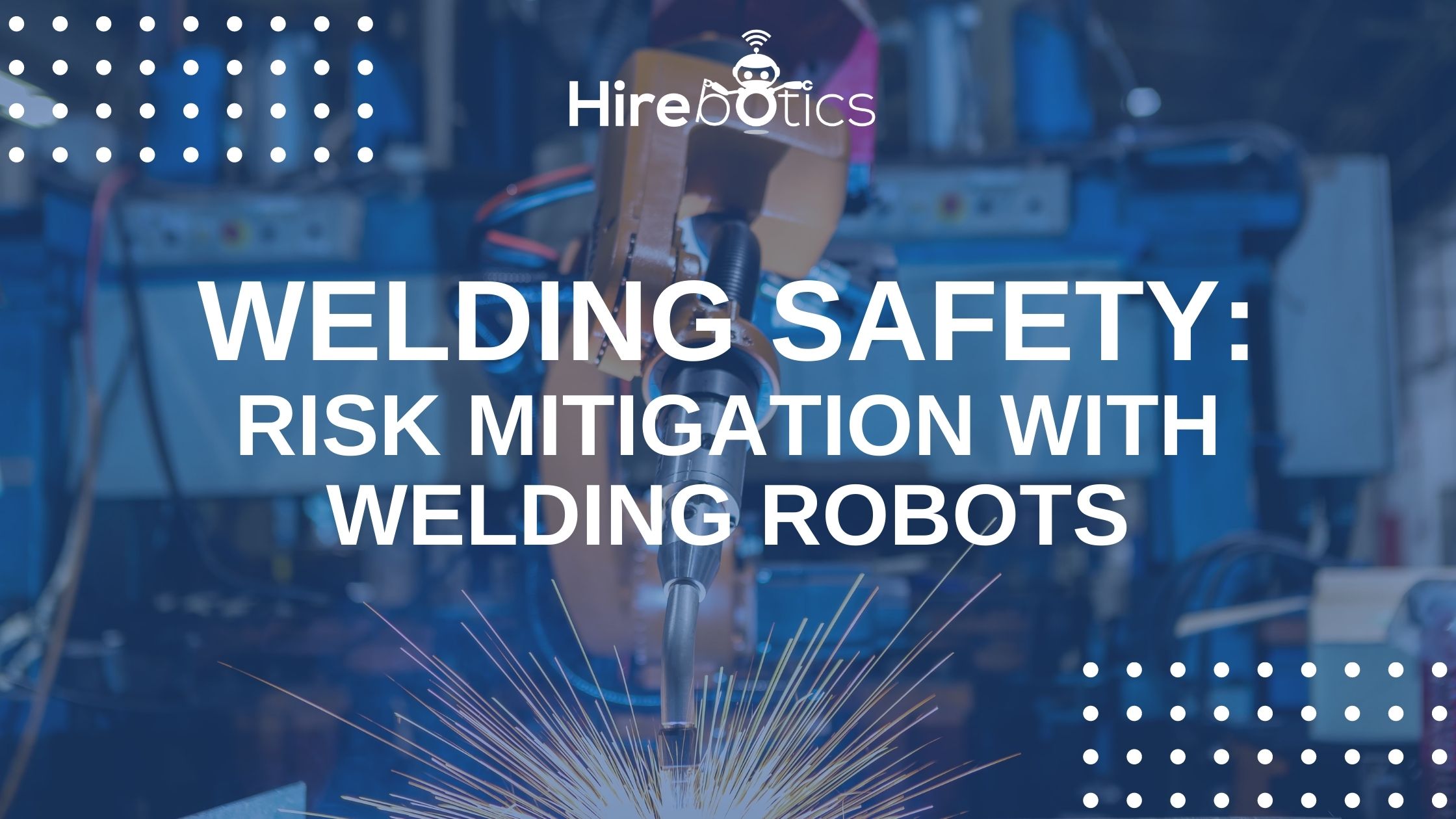
It is common knowledge that welders occupy a hazardous role in industrial settings. Therefore, it is an obvious target for risk mitigation as workplace safety continues to be a driving force for today’s management. Understanding the specific risks associated with welding and the tools at our disposal helps us make more informed decisions regarding worker safety. This article will highlight the basic tenets of welding safety and some powerful options to reduce the risk of injury.
Why is Welding Safety Important?
Welding is one of the most dangerous tasks for workers in industrial settings. Per the Bureau of Labor Statistics, of all recorded injuries to metal and plastic workers, 28% were represented by welders. That’s a stunning statistic. Your welders are likely the most at risk of severe injury in your facility. Injuries are very damaging to the injured party. They can also negatively impact morale across the workplace and build a negative reputation for an employer.
Workplace injuries also carry financial implications. There are immediate losses: penalties, fines, and loss of production. OSHA often gets involved for any workplace injuries. For those injuries related to safety code violations or negligence, OSHA will levy fines. As of January 15, 2022, OSHA fines are as follows:
- $14,502 for serious or other-than-serious violations
- $14,502 per day for failure to abate
- $145,027 per willful or repeated violation
Production losses can hurt, too, especially in today’s labor shortage. Welding-related injuries often lead to time away to recover. This puts a strain on the workforce and can hurt production numbers until you are back to full capacity.
There are downstream costs associated with welding injuries as well. They typically raise insurance premiums, a significant component of a workforce’s overall burden rate. Increases here have a meaningful impact on your bottom line. A welder’s long-term productivity can be affected if the injury is severe enough. It isn’t uncommon for workplace injuries to negatively affect a worker’s strength or range of motion. These realities hurt a worker’s potential productivity.
Safety Risks and Hazards for Welders
The potential risks to welders are serious. Consistent exposure to high voltage electricity and extreme heat makes this occupation dangerous. The most common risks welders are exposed to include:
- Fires
- Explosions
- Electrocution
- Radiation exposure
- Toxic fumes and gases
- General ergonomic risks
The severity of these risks makes it clear how this role is one of the most dangerous in manufacturing. Burns, welder’s eye, and even cancer are just some of the results welders face today. However, you can take steps to mitigate some of these safety risks.
Best Practices for Welding Risk Mitigation
Welding is dangerous, but standards bring this risk to an acceptable level. While this isn’t an exhaustive list or strict reference for workplace safety, it can point you in the right direction when it comes to welding safety.
Before anything else, welders should be certified through an accredited program. This baseline requirement ensures that a welder understands the basics of welding. Welding programs also cover welding safety considerations. This goes a long way in preventing injury. Welders are significantly less likely to experience an injury if they have a basic understanding of a welding training program.
The heat associated with welding poses many risks. Burns, fires, and explosions are primary concerns. Therefore, welding is considered a “hot work” task. This means it should be performed in a designated hot work zone. The actual ANSI definition gives more clarity to this declaration than the scope of this article will provide. The idea is that this zone will be free as possible of flammable material.
Simple PPE can go a long way to minimizing the safety risks associated with welding. The AWS (American Welding Society) recommends that welders wear proper fire retardant clothing. This includes clothing items such as leather gloves, heavy FR clothing, and steel-toe boots with non-slip soles. These items help avoid burns, falls, and electrocution.
In addition, a proper welding helmet and safety glasses are essential for preventing eye-related injuries. Welder’s eye or arc eye is an injury that welders can experience due to improper eye protection. Welding produces extreme levels of UV radiation. This is damaging to welders’ eyes, and this is why screens or shields are essential for others working in the welding environment. Passers-by unfamiliar with the area can accidentally look in the direction of an active welder. This can cause them to incur injury.
How does Automation Impact Welding Safety?
With all these inherent risks, it’s normal to consider alternatives to the standard welding process. The most immediate and surefire risk mitigation strategy is to remove humans from the hazard as much as possible. Robotic automation is a common way that manufacturers achieve this level of risk mitigation. Robotic welding is a standard industrial robot application. This means that welding is an application that robots are commonly deployed to take on. Many manufacturers and integrators can provide robotic welding systems.
By integrating a welding robot, you remove the person from the immediate hazard. The robot is handling the active welding task. This includes operating the torch and sometimes manipulating the workpiece are the most common points of injury for welders.
While not performing the welding task themselves, people will still be involved in this system. In most automated welding processes, people are still required to load and unload parts. Interacting with robots can be dangerous. Automating the welding process doesn’t altogether remove all risks. There are safety considerations to be had with robots as with welding. It is common to integrate significant safety measures with your robot system, including:
- Safety cage
- Safety scanners
- Sensors
- Door locks
- E-stops and rope pulls
Advantages of Welding Automation
Automating your welding process brings significant advantages outside of safety improvements. In addition, robotic automation has the potential to bring massive improvements to your welding process. Any of these factors could be reasons to automate on their own.
Increased Productivity
Robotic automation increases productivity levels for most manufacturers. This increase in productivity comes from welding robots’ impressive combination of speed, strength, and stamina. Robots can move heavy payloads at higher rates than most humans are capable of. Additionally, robots don’t get tired. They can perform all day long, day after day, with no need for breaks.
These productivity gains are often found for manufacturers with high-volume production processes. These are processes that are creating hundreds of repetitive welded parts per day. Unfortunately, low-volume or custom production tasks aren’t usually good fits for automation as they don’t allow the robot to outperform its human counterparts.
Improved Consistency
A considerable advantage welding robots have over humans is their sheer consistency. Some models can get down to micron-level of consistency. This means that they can stop on the same spot in space with micron-level accuracy when they are following a program. This leads to more consistent parts, better quality, and less waste. On the other hand, human welders can sometimes make mistakes. Whether due to fatigue or inexperience, these mistakes ultimately result in wasted parts and consumables. This waste negatively impacts your bottom line.
Autonomy
Robots have the potential to work autonomously from the rest of your workforce. The level of autonomy is relative to your willingness to invest in upstream and downstream equipment. For example, some facilities can achieve “lights-out” production. This means they can produce with little to no human supervision for extended periods. This typically requires part feeding and unloading equipment. However, this type of automation can have a massive impact on your bottom line.
Welding Robot vs. Welding Cobots
Many types of robots are used for welding. The most common options are six-axis industrial robots and collaborative robots. At a glance, these robots might look very similar, but they serve different purposes.
Industrial Robots
The industrial robot is the most common robot found in manufacturing today. Moreover, they are found in many applications other than welding. This is due to their solid combination of speed, strength, reach, and dexterity. In fact, it’s this exact combination that makes them so great at welding. Welding is incredibly demanding when it comes to dexterity. This task often requires the welder to operate at precise angles. The industrial robot does this with ease while it is a challenge for other robot types.
Industrial robots are great for automating tasks, but they are challenging to have around people in a working environment. Industrial robots are unaware of their surroundings for the most part. Because of this, unsuspecting people wandering into the working envelope can be seriously injured by industrial robots. This is why such an emphasis is placed on ensuring proper risk mitigation is integrated with any robot project. Safety equipment allows a robot to react appropriately when a human is within range. For example, a welding robot without safety equipment can be just as dangerous to people as the welding task itself.
Collaborative Robots
Collaborative robots, or cobots, are a friendlier version of the industrial robot. Their stated purpose is to work with and around humans. Cobots can do this because they have built-in safety features. These features are designed to reduce—not eliminate—the risk of injuries to humans. These features include speed and force limits. Limits keep them from moving in a way that could be harmful to humans. It is important to note that there are still apparent risks for a welding cobot. While it is less likely to harm a human due to a collision, this robot is still operating a welding torch. Proper procedures and safety risk mitigation strategies should be implemented to ensure safe operation. For example, while you might not need a full-fledged safety system with a cobot, it is still wise to ensure technicians wear the appropriate PPE when working with and around your welding cobot.
Cobots also have the advantage of being the most user-friendly robot platform on the market. Cobots are designed with ease-of-use in mind. Therefore, they are often marketed to users that are new to robotics. Where an industrial robot might require serious programming skills to perform even a simple move, a cobot can be taught with a pendant or even by hand. Hand-teaching allows users to move a robot in the desired path and build a complex program through simple point-to-point motion. This allows for easy programming and simple redeployment. These critical cobot features make it so desirable for those new to automation.
The Hirebotics Cobot Welder is an accessible robot welding package. Experienced welders with no robot programming experience have learned how to use this product in as little as an hour. This is a huge benefit to using a cobot welder for your welding automation project. Without experienced robot programmers on staff, the investment in a standard industrial welding robot starts to add up quickly. In addition, 3rd party integrators or manufacturer’s technicians must be called out for every program change and update. Meanwhile, Hirebotics Cobot Welder users simply go out and do it on their own.
The Hirebotics Cobot welder offers the safety of cobots into your welding environment. The Universal UR10e is UR’s most popular robot platform. The UR10e comes with safety features to make a hybrid work environment viable. Force limiting sets a maximum value for the force that the arm can exert at any one time. This limitation reduces the chance that a collision with the robot will result in serious bodily injury. This feature allows it to stop moving in the instance where it collides with something or someone. Speed limitation keeps the robot from moving too fast. This also reduces the chance of severe bodily harm upon impact.
The Hirebotics Cobot Welder is an excellent choice for manufacturers looking to automate their welding process. It is an impactful automation tool that provides users with powerful data to transform their manufacturing process.
Curious? Schedule a Cobot Welder demo to see it for yourself.