How to Choose a Welding Cobot in 2023
March 22, 2023
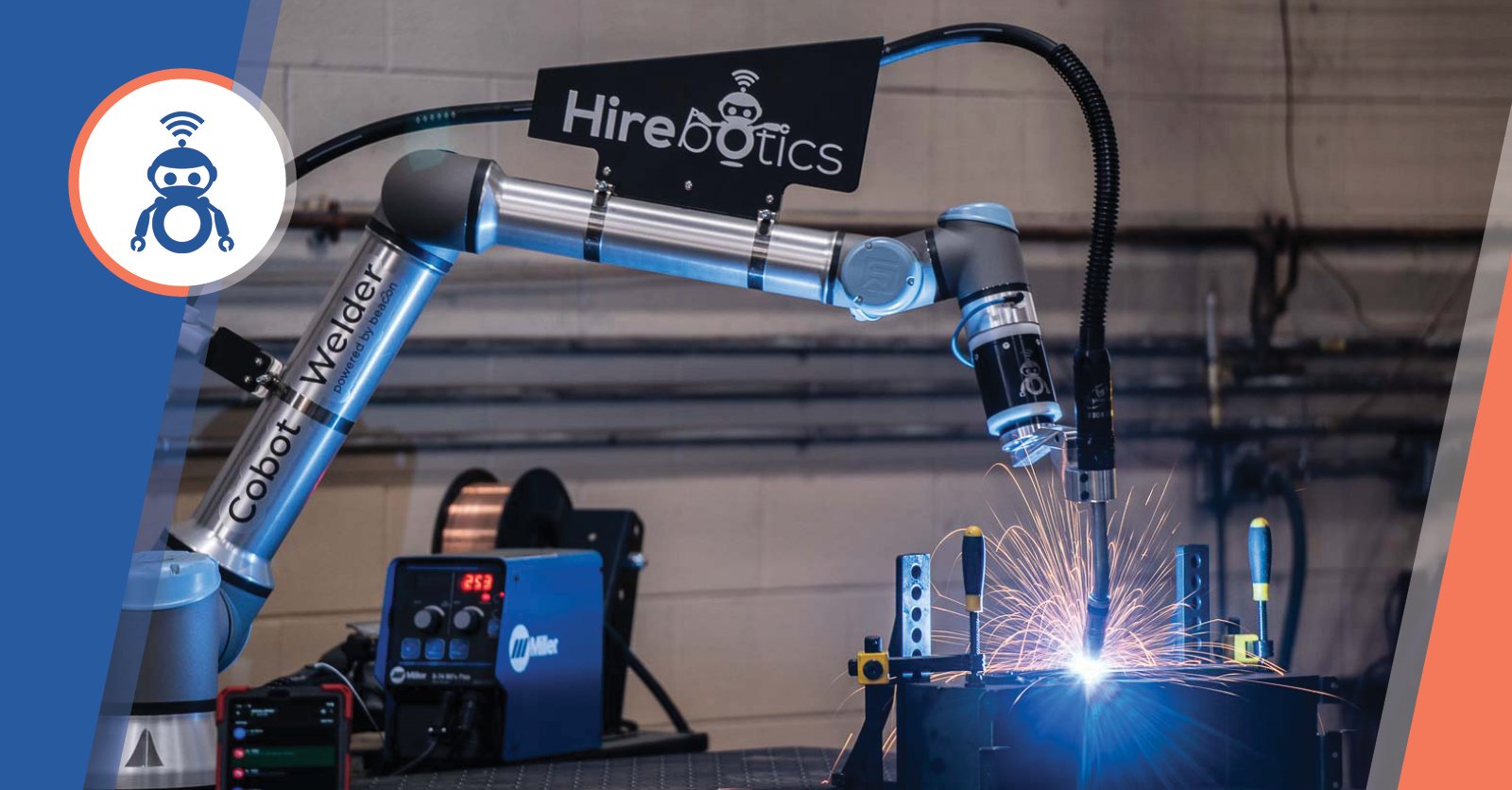
With all the available options on the market, it’s hard to decide on the best robotic welding system for your specific welding operations, right?
Welding companies face many challenges in today’s competitive landscape. In addition to the standard issues most small and medium-sized businesses (SMBs) encounter, companies with welding operations have many sector-specific headaches that limit growth.
A long-running shortage of qualified welders is now being compounded by significantly longer lead times in the supply chain and skyrocketing prices for raw materials.
Many welding companies have decided the best response to these issues is to invest in welding automation—specifically, welding cobot solutions.
Let us give you some pointers on how to best choose the right welding robot for your needs.
Table of Content |
What Is the Best Robot Type for Your Welding?
Two types of robots can be used for robotic welding: traditional robots and collaborative robots (cobots). Here are the main differences:
|
Traditional Robot Welder |
Cobot Welder |
Size and weight |
Large, heavy, and fixed in place |
Smaller and lighter than robots, can be moved around the shop floor |
Flexibility |
Are better for high-volume/low-mix jobs as the programming is complex and takes time |
Can be used for both high-volume/low-mix or low-volume/high-mix jobs |
Human safety |
Must be set up in a restricted area or robust enclosure to ensure worker safety |
Can be set up anywhere on the shop floor; cobots feature sensors to detect and respond to workers in the vicinity |
Programming |
Requires robotics experts to use the teach pendant |
Feature intuitive hand-guiding or app-based programming method so that any welder can use it |
Affordability |
Total cost of ownership is high; the systems often have a high price tag, and businesses should factor in the costs of robotics programming and maintenance expertise |
Cobots are typically more affordable and don’t require the extensive training, robotics expertise, and costly maintenance that conventional robots do |
The best robot type for your welding applications is determined by several factors, including:
- Shop floor configuration for worker safety and equipment footprint
- Access to in-house robotics expertise
- Production type: high-volume/low-mix or low-volume/high-mix
- Budget
Choosing Your Welding System
When choosing your robotic welding system, considering the welding equipment brand and distributor you are dealing with can be a good starting point. Many welding equipment providers have started to offer welding automation solutions that may be interesting for your needs.
In the robotic welding ecosystem, there are multiple types of companies offering robotic welding systems, like the welding suppliers themselves, but also robot companies and even third-party OEMs.
You can get more context and examples in this article about the US manufacturers of welding robots.
During your research, you can ask the following questions:
- Can the system produce the parts you want with the quality and productivity you need?
- How does the welding system integrate with the robots? Is everything integrated into an intuitive robot interface, or is it more custom than that?
- What resources (costs and time) are involved in training and onboarding workers on your robotic welding system?
- What maintenance considerations need to be considered from a budget, expertise, and lead time perspective?
Of course, other elements are important to consider, but this should be a good starting list.
One great way to ensure you can have all your questions answered and actually learn how the welding robot works is to get on a demo call with the company you are looking into.
What is a Welding Cobot
Collaborative welding robots, called cobots, are robotic arms paired with welding equipment designed to work closely alongside human workers. Where traditional robotics must be fenced off to protect workers from being injured in a robot collision, cobots are smaller and designed to work with humans so that they don’t pose any risks.
Like traditional robots, cobots can carry out monotonous and repetitive welding jobs. This means you can assign experienced welders for other critical and value-added tasks.
Welding cobots offer easy-to-learn programming interfaces, lowering the knowledge barrier needed to put those collaborative welding robots into production. This is a compelling advantage because most SMBs don’t have the robotics expertise internally, and hiring robot experts as contractors can be costly.
Select the Right Welding Cobot for Your Business
1. Welder Accessibility
Most welding companies are looking into automation to solve today’s crippling labor shortage. However, many of the traditional robotic welding solutions on the market still require someone experienced with robot programming.
Moreover, experienced robot programmers are just as challenging to find as welders due to the demand. Professional programmer requires about eight years of formal schooling, and their salaries tend to be higher than a certified welder.
It is recommended to select a welding cobot that should be easy and accessible enough that your current welders can use it without a background in robot programming. If your welders can quickly learn to use the robot, it means less downtime, faster setups, a higher production capacity, and a speedier return on investment for your business.
2. Quality, Ease of Use, and Flexibility
Performing and recognizing a good quality weld is vastly more important than programming because rework will eat up profit margins fast. Welding cobots elevate your welders’ expertise and productivity, which won’t happen if the process can’t deliver consistent quality welds.
This was the main driver behind the engineering of Hirebotics’ Cobot Welder, which is widely regarded as the most user-friendly cobot on the market. Welders can program the cobot from a smartphone or a tablet with a dedicated application that does all the complicated programming behind the scenes. Welders can also ‘teach’ the cobot what to weld using only two buttons on the robot arm.
.png?width=645&name=Cobot%20Welder%20-%20Teaching%20Part%20(2).png)
This simplified job setup means less time learning how to program it—and more time welding lucrative contracts. Many welding businesses take on high-volume/low-mix jobs because, with traditional robots, the programming complexity can be cumbersome and cause costly downtimes.
However, with an easy-to-program cobot, companies can expand their production capacity to take on high-mix/low-volume jobs without significant reprogramming, re-fixturing, or adjusting.
3. Reporting is a PLUS
There’s an adage in manufacturing: “If you can measure it, you can manage it.” Reporting capabilities should be an important criterion in your selection because it will help you:
- Validate the cobot’s ability to do the job while maintaining throughput targets.
- Verify reports from your employees.
- Improve future calibration and performance levels.
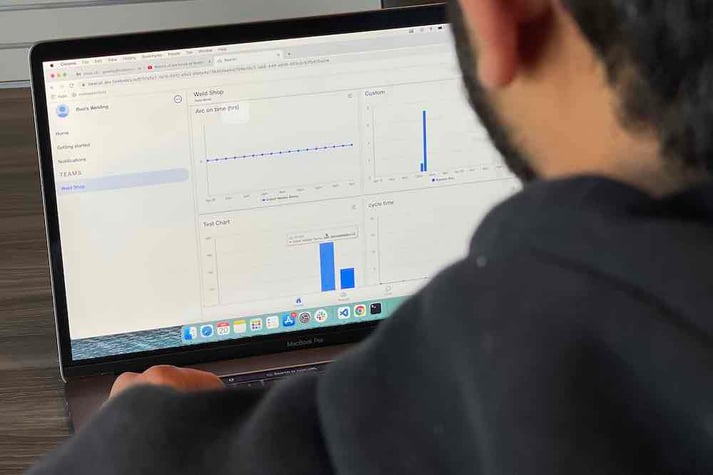
There is a lot of data and features that a welding cobot with reporting capabilities can provide, including:
- Precise cycle times and consumables usage: These numbers can help produce more accurate quotes and lead time estimates for your clients, improving competitiveness and profit margins.
- Real-time alerts: Knowing when a job is finished or when the machine needs attention dramatically reduces downtime between jobs or during lights-out operations, maximizing uptime.
- Saved Program Directory: A directory that can store all the programs and import them into new cobots.
- Industry 4.0: Updates and new welding paths can be easily downloaded, while business-critical reports can be viewed anytime and anywhere. It can also connect to ERPs, project management applications, or accounting software to reduce manual data processes and errors.
4. Company Support, Training, and Accessibility
After-sales support is another important consideration when you choose a welding cobot. The technology provider should be accessible to answer your questions in a timely manner.
With today’s connectivity, some cobot companies provide real-time support over video calls. Some, like Hirebotics, produce support articles and videos that you can watch and practice directly in the welding cobot app, Beacon, while producing parts.
Next Step
Choosing the best cobot welding solution that works for your company doesn’t have to be daunting. With the right cobot welder, you can solve production issues on the floor, boost productivity, and out-edge the competition.
Wondering if a Cobot Welder can be a good fit for your operation or what the size of the investment is? Get in touch with our team and schedule a demo time!