4 Reasons For Using Collaborative Robots in Your Welding Operations
June 30, 2021
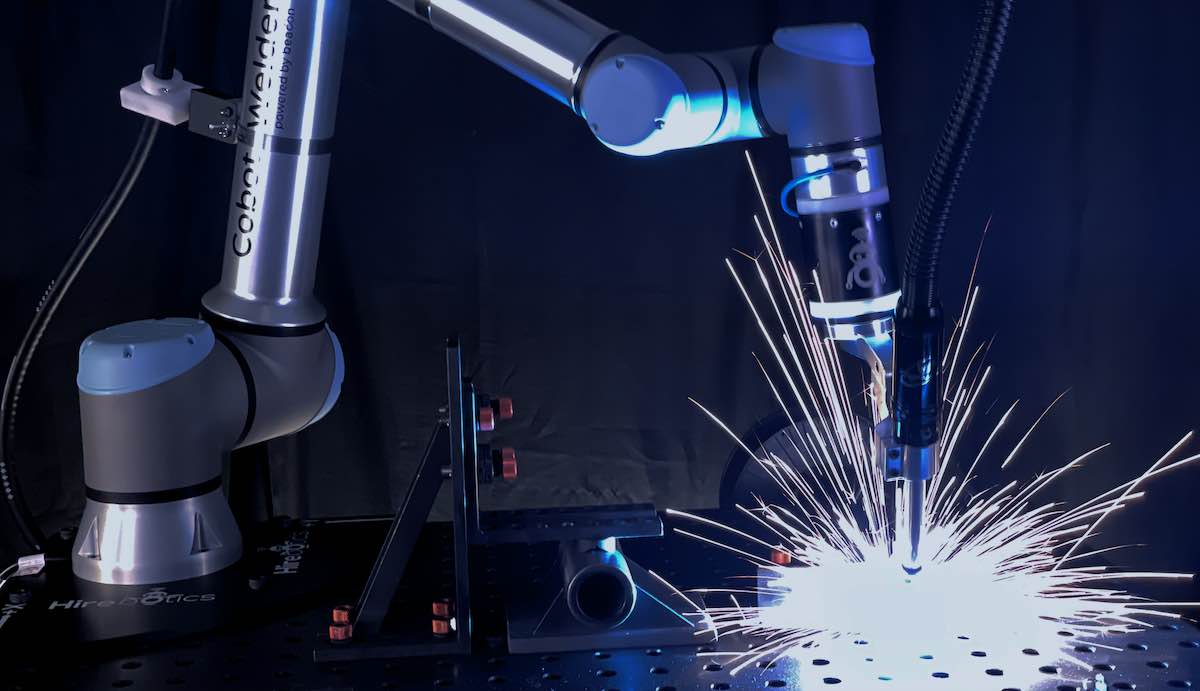
Even though welding is an essential part of the manufacturing industry, there is a shortage of qualified welders. In the United States, the median age of a welding technician is 55, with only 20 percent of the total welders under 35. According to the American Welding Association, these demographics can lead to a predicted shortage of 440,000 welders by 2024.
Medium-sized welding shops are acknowledging the need to automate parts of their manufacturing process. But, the traditional industrial robots aren't best suited for high-mix-low-volume production. Enter the interim solution for this problem: Collaborative Robots or Cobots.
Cobots are an excellent option for smaller welding companies looking to automate their production. They can help automate your welding operations with consistent quality and investment return within a few years. But is a collaborative robot suitable for YOUR welding company?
Watch our Client Case Studies Here!
What are Collaborative Robots?
Collaborative Robots are robotic arms coupled with end-of-arm toolings (EoAT) like grippers, sensors, or welding equipment. Once programmed, they can work safely with humans in a shared space, unlike traditional industrial robots that work with no human intervention.
Cobots are an ideal choice for smaller manufacturers who deal with low-volume, high-mix production for many reasons.
Once set up, they can work alongside human workers, unlike industrial robots built to do one task in a high-volume environment.
Industrial robots need complex codes and programming, but you can use cobots even if you have no programming experience.
They’re small and lightweight, and workers can move them around the factory floor to automate different tasks.
Welding Cobots and Their Benefits in The Welding Industry
If you want an excellent example of how a welding cobot integrated into a medium-sized company, you don’t need to look any further than Wisconsin.
Processed Metal Innovators LLC (PMI) is a Wisconsin-based metal fabricator that manufactures stamped and welded metal parts for appliances, automobiles, appliances, and more. Unfortunately, like most companies in the welding industry, PMI suffered from a shortage of certified welders and had to turn away large quantity orders. Besides, industrial robotic welders were not a fit for smaller production batches.
PMI turned to a welding cobot tool to increase its production capacity and profitability. The pairing between man and machine worked, and PMI could quote work that they weren’t able to do before. They also increased their production by having the cobot welder ready to weld the parts even before the client approves the Purchase Order.
There are many more advantages to adding a collaborative robot to automate your welding process. If you are still on the fence about whether to automate and invest in a welding cobot, let’s look at some benefits of using a collaborative robot in your manufacturing process.
1. Increased Capacity and Boosted Productivity
Suppose you have a small to medium welding company struggling to fulfill large order quantities. In that case, a cobot welder can help you solve these issues. It can weld small parts all day if needed without taking a break and take the pressure off your welders. They can then concentrate on other more significant, value-driven tasks.
Also, it’s lightweight, and without safety fences, so it can be moved from one location to another as needed.
You can also take on different new jobs with small or bigger batches while understanding the cost and time needed to produce. Using solutions like the Cobot Welder from Hirebotics, you can track the performance and productivity of each job. This allows you to offer better pricing and clear lead time at quoting time.
See How Advanta Industries saw a 400% productivity increase from using a welding cobot!
2. Cost Savings and Flexibility
In high-mix, low volume production, a collaborative robot is adaptable to perform different tasks in a day.
Once programmed, a welding cobot can pull up already programmed jobs anytime and adapt to new sizes and geometries. For example, a collaborative robot can do a small batch production in the morning and do another job in the afternoon. Think of it as having an all-around assistant ready to help with any task.
And because of its increased precision, a welding cobot tool can use materials more efficiently and welds faster. This translates to cost savings and higher yield.
3. Constant Quality
It’s no question that certified welders are great at their job. Still, the constant repetition of the task can often result in human error and sometimes poor quality results as the welders get tired.
A cobot welder can take over the repetitive, mundane tasks of welding small parts. Once programmed, it produces the same quality 24/7 as required. Again, this automation assists your welders and frees them up to do more critical tasks.
4. Easy to Install and Maintain
Industrial welding robots are bigger, need to work in enclosed robotic cells, and need advanced programming knowledge to set up. Welding cobots, on the opposite, are relatively easy to install and move around. They also don’t need robotics specialists to program. Instead, you can train your current welding team to start, program, and maintain the robot.
5. Made for Welders
Collaborative robots are making welding automation more accessible to SME’s than ever. But beware NOT to substitute your need for welders for a need for robot programmers. Your welding cobot system of choice should act as a tool that your actual welder can use to boost their productivity. Doing more with the welders you have has always been Hirebotics' approach to automation.
The Cobot Welder is increasing productivity and bringing cost savings through its ease of use and flexibility. Using an app-based teaching approach, Hirebotics is allowing any welders to take their own smartphone (something they know) and teach the cobot Welder to weld (something they master)!
No wonder we see more and more success stories in welding shops, thanks to the cobot welders!
Curious about how easy it can be for your welders to set up and program a welding cobot?