Universal Robots | The Benefits and Capabilities of Cobots
February 15, 2023
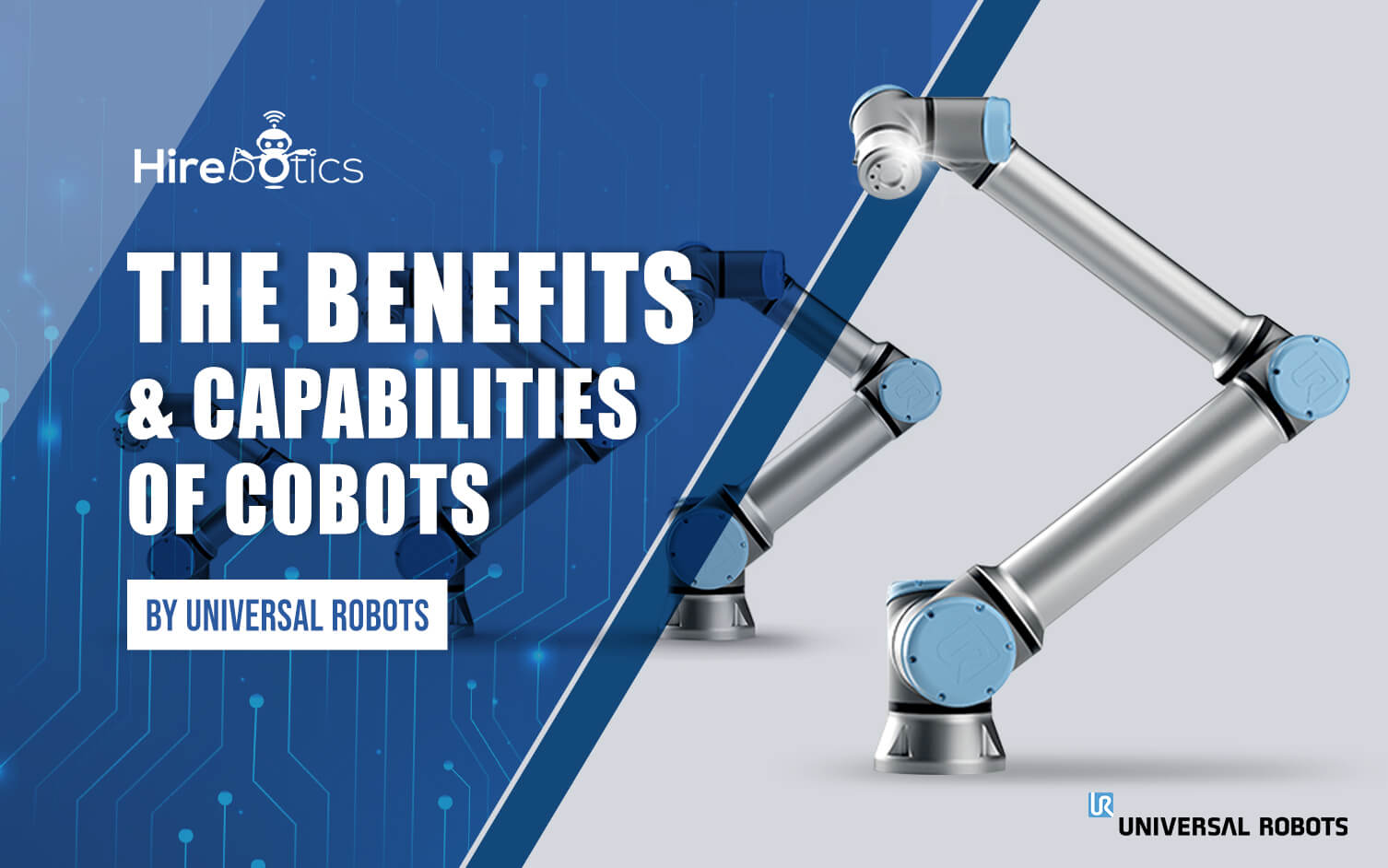
Universal Robots (the company) is renowned for developing ground-breaking collaborative robots (also known as cobots), which are used in a variety of different industries.
Let’s dive into the world of Universal Robots and find out why it has become a juggernaut in the cobot market.
What is Universal Robots?
Universal Robots was founded in 2005 by Esben Østergaard, Kasper Støy, and Kristian Kassow who were students at the University of Denmark. Their goal was to democratize robot technology and make it accessible to all types of companies, including small- and medium-sized businesses (SMEs).
Universal Robots sold its first collaborative robot in 2008. The UR5 cobot struck the perfect mix between sophisticated 3D programming and user-friendliness. The first generation of UR10 cobots soon followed in 2012, allowing manufacturers to carry out more large-scale tasks.
In 2015, Teradyne Inc. (Nasdaq: TER), a North American automatic test equipment designer and manufacturer, acquired Universal Robots.
How many Universal Robots are sold?
Universal Robots claims that they have sold over 50,000 units worldwide by the end of 2020.
Why did Teradyne Inc. buy Universal Robots?
When asked, the President and CEO of Teradyne, Mark Jagiela, said that Universal Robots would complement the company’s System and Wireless Test business units and become a growth platform.
Since the acquisition, Universal Robots continued to pioneer the industry by launching several innovations, including the:
- UR+ ecosystem for custom automation solutions
- UR Academy to help teach people of all skill levels how to handle lightweight robot arms
- Award-winning UR e-Series collaborative robots
- Heavy-duty UR16e with a 16-kg payload capability
- ActiNav, the first autonomous bin picking kit for machine tending applications
- The new UR20 - Revealed at Automatica 2022 with a 20kg payload capacity and 1750mm of reach.
Today, Universal Robots has carved an enviable reputation for high-quality and accessible cobots—many of which have one innovation and design awards. It has offices and training facilities throughout the world. In 2021, the company reported revenue of over USD $311 million.
What Are Universal Robots Cobots?
Collaborative robots (cobots) have completely transformed the manufacturing industry and how processes have been automated. Cobots are basically robots that can safely work with humans.
They are equipped with sensors to detect issues and anomalies. If the cobot’s work is interrupted because of these problems, it automatically turns into a safety mode.
UR Products: Universal robots UR3, UR5, UR16, UR10, and missing NEW UR20!
Traditional robots, on the other hand, would continue operating, which could be dangerous for a user or nearby worker. In a nutshell, cobots foster safer and more seamless human-robot collaboration.
While conventional robots are often considered a means to replace human workers, UR cobots have actually been built to provide a smart and efficient helping hand to a manufacturer’s team. Also, cobots have been designed to be operated intuitively by employees of different skill levels.
Inevitably, collaborative robots improve human capabilities in performing tasks that require precision and endurance, which can reduce injuries and fatigue that plague staff members who carry out tedious and repetitive tasks.
The cobot market is projected to grow from USD $1.2 billion in 2021 to USD $10.5 billion in 2027, with a compound annual growth rate (CAGR) of 43.4%. Interact Analysis estimates that cobots will take up 30% of the total robot market by 2027 as well.
The Benefits of Universal Robot Cobots
The benefits of cobots are numerous and impact many aspects of a business. Once manufacturers turn to cobots, they never go back.
Universal Robots offers many compelling reasons why companies should use cobot automation:
- Consistent Quality
- Improved Efficiency
- Enhanced Safety
- Reduction of production costs
- Easier to program and use
- Unprecedented flexibility
- Happier employees
1. Consistent quality
Once programmed, cobots perform the same task over and over again. These repetitive functions are not influenced by human error, exhaustion, lack of personnel, etc. UR Cobots provide repeatability and consistent quality for manufacturers operating in highly regulated industries, such as the automotive and aerospace sectors.
2. Improved efficiency
Universal robots have proven to be instrumental in boosting productivity and accelerating throughput. In today’s tight labor market, cobots can be assigned monotonous tasks to either fulfill production runs when employees are not available and/or ensure that skilled workers can be reserved for more motivating projects and tasks. Collaborative robots can also operate 24/7, which allows companies to increase production capacity. Studies show that Cobots can reduce the idle time of the human workforce by as much as 85%.
3. Enhanced safety
UR Cobots features built-in safety measures, such as speed, force, and power limits, in order to safeguard workers. That is why humans and collaborative robot arms can work side by side. The American Society of Mechanical Engineers details how the design of Universal Robots includes comprehensive cobot safety features.
Risk assessments and safety precautions must be taken into account; however, cobots are considered safer than the bulkier industrial robots of the bygone days.
(Find full infographic at ASME.org)
4. Reduction of production costs
In order to compete both domestically and with lower-cost off-shore labor markets, manufacturers are increasingly looking into an automation journey. Universal Robot can help companies not only to reduce production costs thanks to their efficiency but also mitigate the impacts of fixed-price contracts, which can extend for several years, should labor costs rise.
5. Easier to program and use
Contrary to traditional industrial robots, Universal Robots cobots are much easier to program. UR Cobot programming revolutionized the robot programming industry by developing a graphical interface with intuitive commands - no more lines of code were needed. In fact, the newest generation of some cobot solutions needs no programming at all.
This is exceptionally important in industries that have a hard time recruiting skilled workers. Little-to-no programming also means almost anyone can use a cobot with minimal training.
6. Unprecedented flexibility
UR Cobots tend to have a smaller footprint than traditional robots. They do not require a heavy set-up process (mere hours) and are often mobile. Manufacturers can therefore move cobots around the shop floor and to different areas depending on the work to be completed This level of adaptability simply cannot be achieved with conventional robots.
7. Happier employees
Universal Robots are developed to work alongside people—not take over their jobs. While collaborative robots can tackle unsafe, dirty, or monotonous projects, employees work on more enjoyable tasks. Workers that use cobots tend to feel more supported and appreciated by their employers. They get to upgrade their skills and experience a higher level of job satisfaction.
The Many Applications of UR Cobots
Universal Robots have truly become game-changers for manufacturers and shops looking to increase product quality, accelerate production lines, and expand production capabilities.
There are many different applications of cobots, including:
- Assembly and quality assurance
- Material handling
- Machine tending
- Dispensing
- Finishing and polishing
- Removing materials
- Palletizing
- Grinding
- Packaging
- Injection molding
- Welding
- And so much more!
Moreover, through their UR+ platform, we are seeing more and more application kits coming to market. Here is an example of a Universal Robot welding—programmed in 90 seconds!
The International Federation of Robotics (IFR) recently reported that the following industries were the largest adopters of cobots: automotive, electrical/electronic products, metal and machinery, chemical and plastic products, and food and beverage.
Some manufacturers design accessories for cobots for a particular industry in order to help businesses to overcome unique challenges. For example, Hirebotics leverages the advantages of the Universal Robots for their cobot welding package. These specialized cobot systems provide many advantages to companies. The following demonstrates the tremendous potential of cobots dedicated to a specific sector.
Universal Robot Cobots in Welding
Universal Robot collaborative robots are highly relevant in the welding industry, positively impacting welding businesses and teams. They are the perfect fit to carry out welding tasks and offer advantages over manual welding and traditional robots.
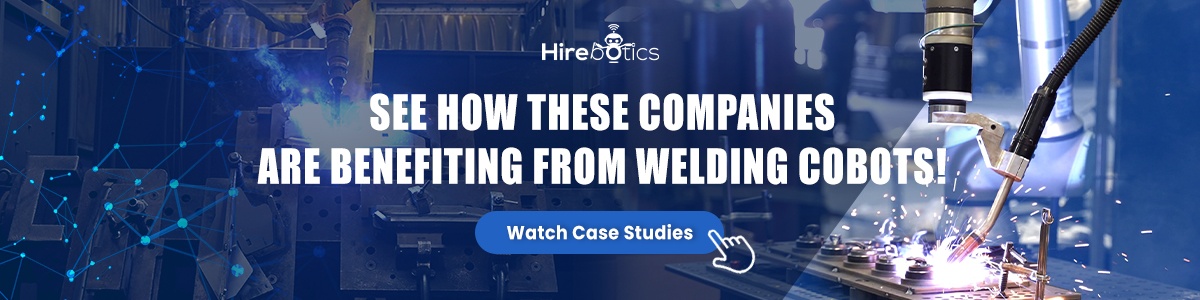
Here are how UR welding cobots help manufacturers improve their production.
1. Alleviate the pressure of a lack of welders
Welding cobots have become the saving grace for companies that are struggling with a shortage of welders. Cobot Welder, for example, is a simple-to-use welding cobot system that eliminates the need for complex programming and knowledge in robotics.
This welding cobot, integrated with Universal Robots, empowered welders to become operators and use their skills in welding in a more productive manner.
2. Offer more precision and quality to welding jobs
By systemizing welding workflows using cobots, manufacturers can improve the consistency and overall quality of the parts they produce.
Welding cobots are also less prone to human error, operate at the same capacity 24/7, and do not become fatigued as is the case with manual welders.
3. Increase productivity
Welding cobots can significantly accelerate production runs and increase throughput—all without compromising quality. Also, less time is spent on cleaning each weld due to reduced spatter, which ultimately means teams can deliver welding projects faster and increase customer satisfaction.
Finally, welding teams can also take on more and different types of projects (high-mix, low-volume, longer continuous seams for large parts, etc.) thanks to the level of automation and speed cobots offer.
4. Bring more control over your workflow
Welding cobots give welding teams more control and flexibility over their production processes. Whether it is better managing project quality or timelines or deploying cobots to different jobs depending on the complexity, welding teams can optimize their workflows and more easily attain their overall business goals.
How Much Does a Universal Cobot Cost?
Universal Robot price varies between $30k to $65k, but that is only the UR cobot arm price. However, these prices will rarely be the end cost of your application because you'll need tools and systems to actually execute the task you want to automate.
There are many cobot makes and models on the market. Depending on the vendor, different packages are offered to include the robotic arm, mounting stand, power supply, learning interface, cables, sensors, and effectors as well as delivery, support, and maintenance.
Other cobots can be more or less expensive based on features, performance levels, and craftsmanship. As an example, here is what to consider when calculating the cost of a robotic welder. <-
When choosing a cobot, it is important to consider the application as well as the return on investment versus the status quo or opting for other legacy technologies. For example, many welding businesses have found that the payback period on welding cobots is shorter than originally anticipated. It really is all about doing the math!
The Future of Cobots with Universal Robot
The future of cobots, like those developed by Universal Robots, looks very promising. In the wake of the global pandemic, supply chain issues, a massive labor shortage, and prioritized cost efficiencies, more and more manufacturers—from large corporations to SMEs—are turning to cobots to facilitate operations.
According to ABI, the cobot market had a global valuation of $600 million in 2021. It is projected to spike to $8 billion in 2030, with a forecasted growth rate of 32.5%. As cobot innovations progress, the manufacturing industry will continue to transform for the better as cobots assist an upskilled workforce in boosting efficiency and quality.
Wondering if a Universal Robot Welding Cobot could fit into your business? Book a Demo Here!