3 Compelling Business Cases for Welding Cobots
April 20, 2023
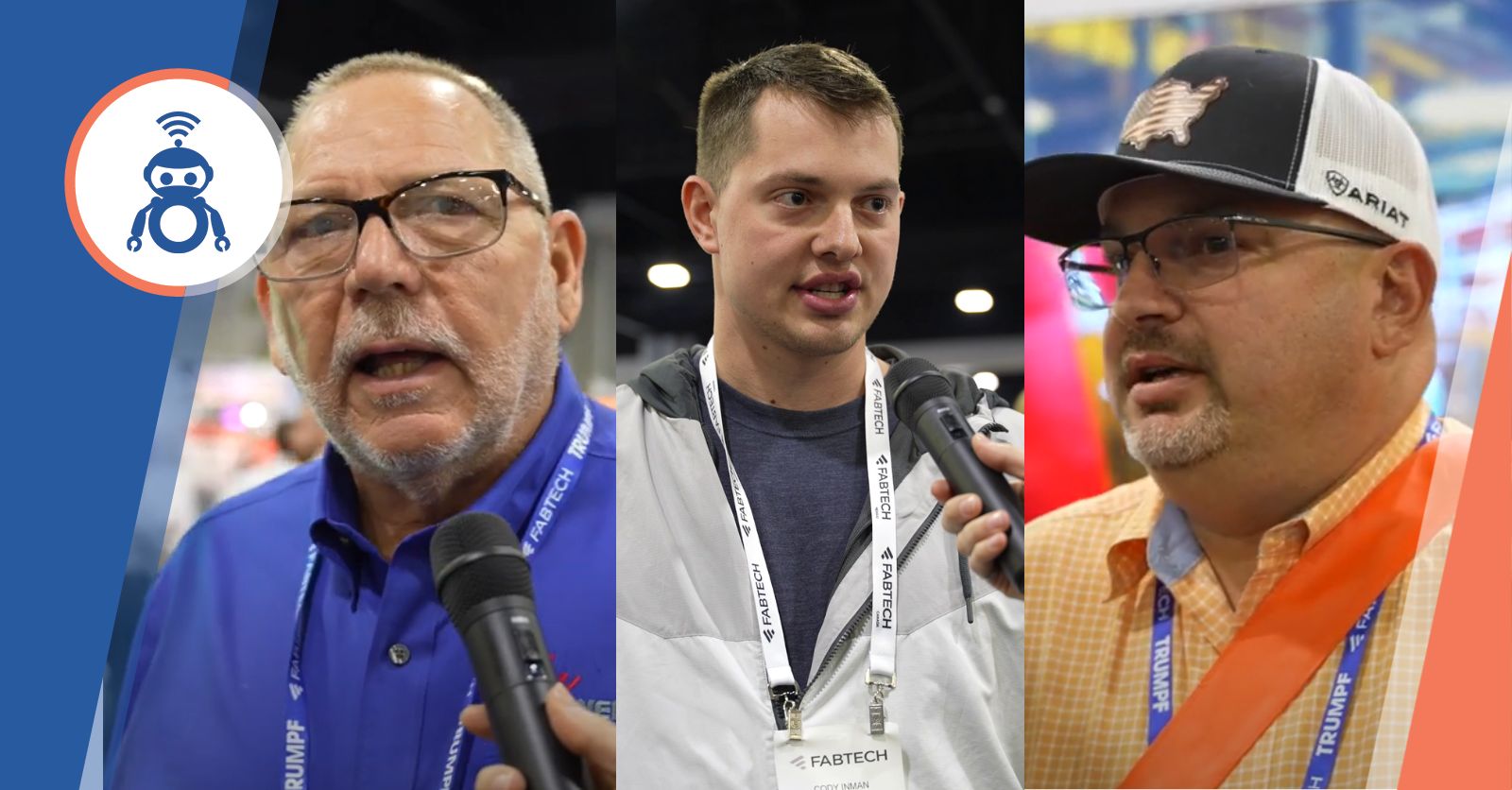
What is it truly like on shop floors when companies implement a welding cobot? What are the concrete results?
Welding cobots are increasingly important in manufacturing and fabrication shops' production processes.
Also known as cobot welders, cobots for welding resolve many of the challenges businesses face: minimizing the potential of human error, reducing labor shortage issues, improving overall production quality, efficiency, and capacity—and many other benefits.
We spoke to three different businesses that rely on welding and their recent experiences with cobot welding.
The results are indeed impressive!
Table of Content |
Wenger Manufacturing: Productivity Boost at 120 Welding Inches a Minute
Wenger Manufacturing, located in Sabetha, Kansas, produces welds for extrusion and drying equipment mainly used in pet food companies. Their clients demand high-quality welds to ensure minimum weld failure and costly downtimes.
The business initially used what Andy Harris, a welding tech, described as an “old-school robot.” The goal was to leverage the robot to address the current lack of qualified welders. However, problems soon occurred because the robot had difficulties getting welds right each time, every time. Precision and consistency were lacking.
The Wenger Manufacturing team decided to test-drive Hirebotics’ Cobot Welder. Both Andy and Roger Edeleman, Supervisor of Fabrication and Welding, were amazed at the minimal programming and the fact that the welding cobot wrote its own program without having too much input.
They decided to assign a staff member who has never welded to learn how to use Cobot Welder. Within an hour, they were able to produce perfect welds.
“It was a total game changer,” said Andy.
Even more astounding: Wenger Manufacturing was able to boost welding inches per minute far beyond industry standards. “The average welder in North America can carry out about 12 to 10 inches per minute. But thanks to Cobot Welder, we are running 120 inches and achieving perfect welds every time.”
Columbia Energy: Upskilling Employees and Boosting Efficiency
The team at Columbia Energy and Environmental Services in Richland, Washington, had no prior robotics experience. The company, which manufactures decontamination equipment for local businesses and labs across the United States, opted for a cobot welder to expand the capabilities of its employees on the shop floor.
Several experienced welders volunteered to try the welding cobot, despite having never used one before. Wesley Blackard, Shop Supervisor, said that they picked it up really easily, without the need to learn any complex welding cobot programming.
Jordan Warner, Fabrication Specialist, easily incorporated the company’s current welding procedures into new workflows using the cobot welder. “We really appreciate the repeatability. Every part is uniform from start to finish.”
Greg Kraft, Fabrication Manager, was pleased by the cobot's efficiency gains. “We were able to produce 180 different parts in 2 days,” he said. No small feat for welding that is considered a manual-intensive job!
As with many other fab shops and manufacturers, adding welding cobots is not a means to eliminate jobs. In fact, many businesses, faced with dwindling new welding applicants and an aging workforce, view cobots as a means to upskill current welding employees to increase retention and job satisfaction. Mundane tasks can be relegated to welding cobots, while complex and more stimulating projects can be assigned to human welders.
Advanta Industries: Investing in 8 Welding Cobots and More
Advanta Industries, based out of Petersburg, Michigan, has a similar story to Columbia Energy and Environmental Services. The company manufactures welds for the automotive industry, producing very large parts—think 12’ x 10’ or 8’ x 6’ components. These types of welds are not typically made with robots.
However, after seeing welding cobots in action at a Fabtech event a few years ago, the team decided to invest in this technology, and they now have 8 cobot welders for the two plants. “Sure, it was scary at first,” explained Cody Inman, Operating Manager. “We had zero experience in robotics before. But we envisioned that this new technology could help our business prosper.”
And prosper it did. While in-house welders were very hesitant at first, they soon realized the benefits. “The cobot welders came almost fully assembled. Programming was as easy as it gets,” said Dylan Taylor, Plant Manager.
Some of the cobot welders have been paired up to handle large parts. Others are dedicated to dull and repetitive tasks, freeing up welders’ time for more complicated work. The integration of cobots was so successful that Advanta Industries aims to double the number of cobot welders on both shop floors very soon.
Beyond the Hype: The Multifaceted Benefits of Welding Cobots
Cobot welders are incredibly versatile machines that can be used for a variety of welding tasks, including arc welding, resistance welding, spot welding, and more.
The use of welding cobots offers many benefits, including increased precision, higher quality welds, improved product consistency, reduced cycle times, less waste, and faster speeds.
Furthermore, cobots are easy to program and can be quickly reprogrammed to adapt to changing production requirements, allowing businesses to remain agile in their operations.
While seasoned welders may initially be skeptical, integrating them into the decision-making process of equipment procurement can help alleviate fears and transform employees into technology ambassadors.
By investing in welding cobots, businesses can yield greater value in terms of efficiency and cost savings. With the ever-evolving advancements of welding technologies, cobot welders are now more capable than ever before, offering an ideal solution for many businesses looking to streamline their production processes with the same number of employees. The key is to assess your business’ needs and understand the ins and outs of choosing the best cobot welder for your application.
Wondering if a Cobot Welder can be a good fit for your operation or what the size of the investment is? Get in touch with our team and schedule a demo!