How to Elevate the Career of a Welder Using Cobots
August 3, 2022
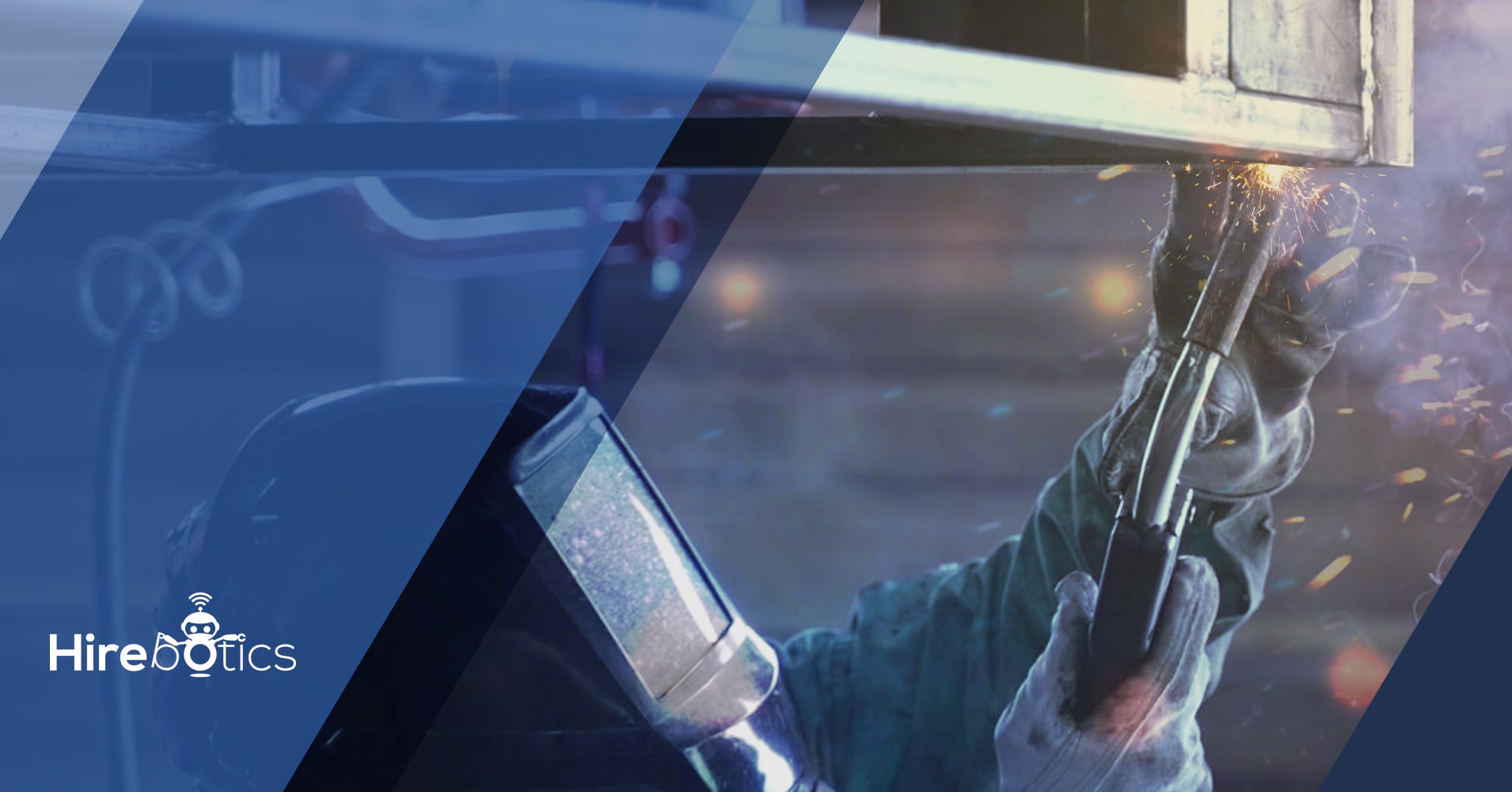
Retirement.
Job changes.
A negative perception of welding as a career.
A lack of a pipeline of new welders.
The global pandemic.
Companies can never seem to cut a break regarding ongoing welder shortages. According to the National Association of Manufacturers (NAM), nearly 81% of manufacturers cannot hire enough qualified welders to meet their needs.
However, did you know that upskilling current welders using technology and state-of-the-art equipment, like welding cobots, can help?
Upskilling, or providing training to help workers learn new skills and take on new responsibilities, can indeed mitigate three of the most challenging issues companies face:
- finding experienced welders or enthusiastic entrants into the workforce,
- overcoming the skills gap,
- and boosting retention.
Welding Cobots Alleviate the Burdens of a Lack of Welders
An increasing number of manufacturers across many industries are using welding cobots to stave off the problems surrounding a reduced number of welders. Cobot welders are implemented to carry out welding jobs of all sizes and complexity.
Automating welding processes means manufacturers can ensure, if not speed up throughput, 24/7.
Contrary to human welders, welding cobots can lock in weld consistency and quality as they never have bad days, suffer from fatigue from long hours or have their work impacted by other distractions. Better quality and a higher production capacity justify the investment in welding cobots, mainly if they are easy to set up and learn and require little programming.
In addition, welding cobots can improve job satisfaction among welders. Some older welders may initially be skeptical about working side by side or with a cobot welder. However, it is important to remember that humans are more efficient and effective when they have jobs that require cognitive ability, problem-solving skills, etc.
When a manufacturer has to produce 1000 parts, that is a mind-numbing, repetitive task better suited for automation. If a welding team can let cobots do those types of mundane tasks, they can be assigned to more challenging and rewarding jobs that put their minds to work.
More compelling tasks cause a positive ripple effect for welders. The days pass by more quickly. They learn how to handle complex welding tasks, which can increase their self-confidence and perception of their jobs.
Welding is no longer considered a dirty, dead-end job with no possibilities for advancement: the more welders fine-tune their craft, the more they can earn—and the more likely they will stay with their current employers.
Cobot Welders: More Than a Solution to the Welder Shortage
Companies that embrace cobots as solutions to be integrated with their welding teams, rather than simply a one-off answer to manpower issues, will likely be highly successful in attracting and keeping top welder talent.
Here’s why.
When a manufacturer invests in welding cobots and automated production workflows, they will need staff that is comfortable with them. That is why choosing intuitive, programming-free, and simple welding cobots is so important: even the most resistant employee will experience immediate, positive results.
They realize they don’t have to do the dull jobs anymore. They can handle the fun stuff.
More comfort in working alongside or with cobot welders inevitably leads to curiosity and a willingness to make the most use of them.
These welders become a part of the automation team—not the welding team. They can take on the responsibility for not just making parts on the system but creating new parts, developing library sets, and training other users to run the cell or make new parts.
Galvanized by the ability to transpose their ingenuity and flair for resolving problems from welding to the cobots, welders can be encouraged to look for ways to optimize the utilization of the robotic cells, run more complex parts with the equipment, and improve fixturing or operational steps.
In a nutshell, they can genuinely embrace how to make the welding cobots as productive and effective as possible.
A Case Study in Elevating the Welding Team’s Position in the Company
As an example, when Scott Fetzer Electrical Group acquired cobots, the company opened two positions.
- One was a line position responsible for keeping the cobots running daily on the line, clearing faults as they occurred, conducting minor preventative maintenance, etc.
- The other was a technical position with responsibilities for implementing new cobot applications and working with the engineers to design tooling, etc.
These two positions were created to enable the manufacturer to make the most of the systems it had purchased and installed. The management team was exploring not only ways to keep existing cells running and productive but also how to increase efficiency and more strategically determine where upcoming cobots should be integrated within the production line.
By having two welding cobot champions, the manufacturer also:
- Ensured the early adoption of the new technology among the other welders
- Sped up the onboarding process for the welding team
- Benefited from creative solutions that solved welding and production challenges
- Increased job satisfaction
Interested in learning how Hirebotics’ Cobot Welder can elevate your welding team’s skills?
Discuss your specific parts with our robotic welding experts today.