Robotic MIG Welding Unleashed: Exploring their Benefits and Impact of Cobots
July 5, 2023
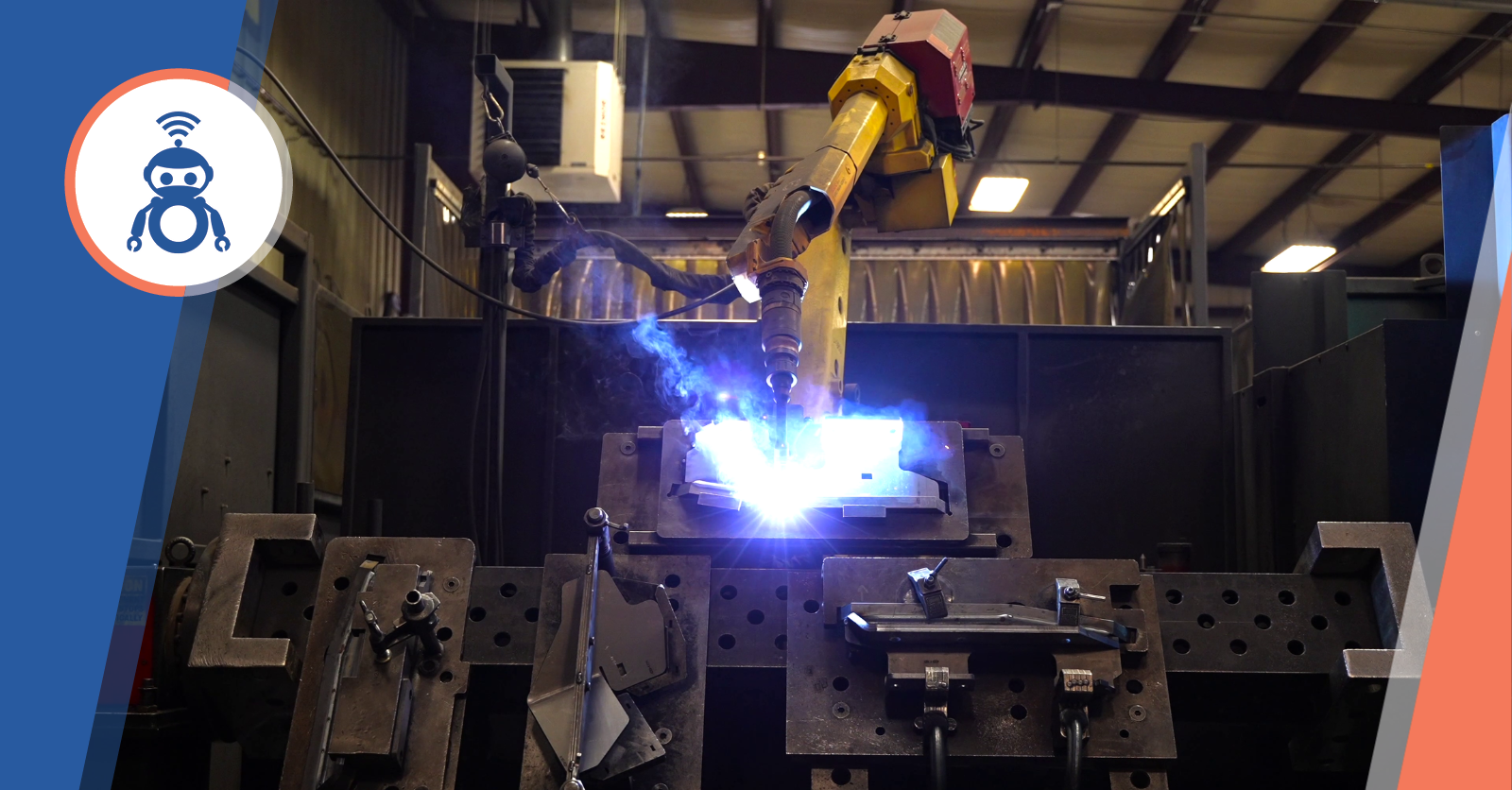
In every welding shop, there are common challenges that arise: Can the pace of production be increased without compromising quality? How can we mitigate the shortage of skilled welders? Is there a way to make operations safer and more cost-effective? If these questions resonate with you, you're not alone.
Many managers and CEOs grapple with these issues on a daily basis, but is there a solution that addresses these pain points head-on?
Welcome to the world of robotic MIG welding, a well-established technology that continues to evolve and improve, offering a range of benefits to help transform your operations.
In this article, we will discuss the many benefits and potential drawbacks of robotic MIG welding, as well as explore some of the emerging technologies designed to support and enhance this automation solution and how it can enhance your production capabilities.
Table of Content |
Introduction to Robotic MIG Welding
The welding industry has always been marked by innovation, resilience, and a consistent drive to improve efficiency. One particular area where these principles manifest is in the field of MIG welding.
The Evolution of MIG Welding
Metal Inert Gas (MIG) welding, also known as Gas Metal Arc Welding (GMAW), was first developed during the 1940s as a fast, portable process to create strong, durable joints. This method, which uses a continuous solid wire electrode fed through a welding gun, quickly gained popularity due to its ease of use and versatility.
GM Factory source: Automate.org
Over time, as technology evolved, so too did MIG welding. The advent of computer technology and robotics led to a shift towards automation. Robotic MIG welding systems emerged, marking a significant evolution in the welding process. These automated systems, capable of delivering precise, consistent welds, marked a leap in productivity and efficiency, further strengthening the appeal of MIG welding.
Need for Automation in MIG Welding
Manual MIG welding, while versatile and widely used, has several challenges. Inconsistencies in weld quality can occur due to human error, resulting in rework and wastage. Additionally, the process can be labor-intensive, leading to worker fatigue.
The demand for skilled welders has also seen a steady rise over the years. However, the industry is grappling with a growing gap between this demand and the availability of trained professionals. This challenge is exacerbated by an aging workforce and a lower influx of younger individuals into the profession.
In response to this shortage, the industry has turned to automated solutions like MIG welding robots. These systems offer a way to maintain productivity levels even when skilled labor is hard to find. Moreover, robotic welding systems deliver consistent, high-quality welds, minimizing the potential for human error and reducing waste.
Automation in MIG welding also enhances workplace safety. Robotic systems can perform tasks in environments that may be hazardous for human workers, reducing the risk of workplace injuries. These factors make robotic MIG welding an effective solution to labor shortages and contribute to a safer, more efficient workplace.
Key Takeaways |
The evolution of MIG welding, driven by advancements in technology and the rise of robotics, has allowed the industry to address the growing welder shortage and improve productivity. |
Robotic MIG Welding Systems
Robotic MIG welding systems are intricate assemblies of components, each playing a crucial role in ensuring efficient and high-quality welding. The functioning of these systems follows a specific workflow, and the quality of welds produced relies heavily on several factors.
Key Components of Robotic MIG Welding
At the heart of a robotic MIG welding system is the industrial robot arm. The robot arm, equipped with multiple axes of movement, provides the agility and precision required for welding operations.
Attached to the robot arm is the welding torch, which performs the actual welding process. The torch receives its welding power from a dedicated power supply, which regulates voltage and current to ensure a stable arc.
The robot controller is the 'brain' of the system, governing the actions of the robot arm and often interfacing with other components to coordinate the welding process. Additionally, the system includes a wire feeder that provides a continuous supply of filler metal, an essential aspect of MIG welding. Other components include a shielding gas supply to protect the weld pool from contamination and safety equipment like shields or curtains to protect surrounding areas and personnel from the welding arc.
The Process of Robotic MIG Welding
The process begins with programming the controller with the necessary specifications, such as the path, speed, and other parameters for the welding operation. Programming can be done offline using CAD models or directly on the production line through a teach pendant.
Once programmed, the robot arm, guided by the controller, positions the welding torch at the start of the weld joint. As the welding process initiates, the wire feeder supplies the filler metal, and the power source generates the arc. The robot arm moves along the predetermined path, creating a consistent weld.
Both upstream and downstream processes are also part of the robotic MIG welding workflow.
This includes activities like:
- Workpiece preparation
- Positioning
- Post-weld inspections
- Any required post-weld treatments
Quality Considerations in Robotic MIG Welding
Several factors influence the quality of a weld in a robotic MIG welding process. Among these are torch alignment, travel speed, arc length, and part fixturing.
- Torch alignment is crucial to ensuring a consistent weld, as misalignment can lead to a range of weld defects.
- The travel speed of the robot arm must be precisely controlled, as moving too quickly or slowly can impact weld quality.
- Arc length, influenced by the voltage settings on the power supply, is another essential factor. If the arc is too long or too short, it could lead to spatter, undercut, or other defects, compromising the integrity of the weld.
- The use of precise and stable fixtures is essential for maintaining part position and alignment during the welding process. Without proper fixturing, even the most finely tuned robotic MIG welding system could produce flawed results. Therefore, investing in accurate, reliable fixtures and positioners can significantly enhance the consistency and overall quality of your welds.
All these factors underline the importance of proper setup, programming, and maintenance of a robotic MIG welding system in producing high-quality welds.
Advantages and Limitations of Robotic MIG Welding
Robotic MIG welding systems offer several significant advantages that can boost efficiency and precision in a welding operation. However, they also bring along their own set of limitations and challenges that must be acknowledged.
Efficiency and Repeatability of Robotic MIG Welding
One of the most prominent benefits of robotic MIG welding is its high efficiency. With the ability to operate continuously without fatigue, these systems can significantly increase productivity levels. They also speed up the welding process due to their ability to work at a consistent pace without breaks, leading to quicker project completion.
Robotic MIG welding systems also deliver exceptional repeatability, ensuring consistent weld quality across components. They follow programmed paths with extreme accuracy, leading to fewer errors and less waste compared to manual welding.
An often overlooked benefit of robotic welding is the ability to free up skilled welders for more complex, added-value tasks. Instead of being occupied with repetitive welding operations, these professionals can focus on tasks that require critical thinking, problem-solving, and expertise, effectively improving the overall productivity and quality of the operations.
Limitations and Challenges of Robotic MIG Welding
Despite the substantial benefits, it's also essential to understand the limitations and challenges of robotic MIG welding. One challenge is the need for skilled programmers. While the robot performs the welding, it requires a skilled technician to program its operations accurately, which requires specialized training.
The initial investment for a robotic MIG welding system can also be significant. This high upfront cost can be a barrier, especially for small to medium-sized businesses. However, it's worth noting that the increase in productivity and efficiency will lead to a return on investment over time.
Finally, robotic systems can have limitations when dealing with complex or variable parts. These systems excel in repetitive, high-volume production but may struggle with tasks requiring adaptability or handling unique pieces. While advancements in robotic technology address these issues, they remain a consideration when adopting robotic MIG welding.
Pros of Robotic MIG Welding |
Cons of Robotic MIG Welding |
Increased Efficiency: Robotic MIG welding systems can operate continuously without breaks, significantly increasing productivity. |
Need for Skilled Programmers: These systems require technically skilled operators to accurately program the robot's movements and operations. |
High Repeatability: Robots can follow programmed paths with extreme accuracy, leading to fewer errors and waste compared to manual welding. |
High Initial Investment: The upfront cost of robotic MIG welding systems can be significant, potentially posing a financial barrier for smaller businesses. |
Consistent Weld Quality: Robotic welding systems canprovide consistent welding parameters, ensuring the quality of welds remains uniform across components. |
Limited Adaptability: While great for high-volume, repetitive tasks, robots may struggle with variable or complex parts requiring adaptability. |
Reallocating Skilled Welders: By handling repetitive welding tasks, robots free up skilled welders to focus on more complex and added-value tasks. |
Maintenance Needs: Regular maintenance and possible system repairs can add to the overall cost and downtime. |
Cobots vs. Robots
While traditional robotic systems have been in use for many years, particularly in the automotive industry, a newer type of robot has entered the scene over the past decade or so. These are collaborative robots, or 'cobots,' designed to work hand-in-hand with human workers.
What are Cobots?
Cobots are a type of industrial robot designed to work alongside humans in a shared workspace. Unlike traditional robots, which operate autonomously or under strict control, cobots are equipped with advanced sensors and safety mechanisms that allow them to interact safely with human operators.
Unlike their traditional counterparts, cobots aren't caged off or isolated from human workers. They're designed to assist, rather than replace, human workers in tasks that require precision or are repetitive or ergonomically challenging.
Common Challenges in MIG Welding
Manual MIG welding, while versatile and widely used, has several challenges. Inconsistencies in weld quality can occur due to human error, resulting in rework and wastage. Safety is also a concern, as manual welding exposes workers to potential hazards such as harmful fumes and burns. Additionally, the process can be labor-intensive, leading to worker fatigue and decreased productivity over time.
Safety Considerations with Cobots
One of the key features of cobots is their built-in safety mechanisms. They are designed to stop immediately when they come into contact with an object or person, significantly reducing the risk of injury. Moreover, most cobots are equipped with force-limiting technology, which ensures that if a collision does occur, it's at a safe force level which protects the robot and prevents damage to the torch and other equipment, preventing costly repairs.
Despite these safety measures, it's crucial to conduct risk assessments and follow best practices in cobot operation, such as proper training, to ensure a safe working environment.
Cost-effectiveness of Automation
While the upfront cost of automation, including cobots, can be high, the long-term benefits lead to significant cost savings.
- By increasing efficiency and reducing wastage and rework, automation can improve the overall productivity of an operation, leading to lower costs per part.
- By assuming repetitive tasks, cobots can free up skilled welders to focus on higher-value tasks, effectively utilizing their skills where they're most needed.
- By integrating cobots into the manufacturing process, reliance on skilled workers is diminished, leading to less labor costs to manufacture parts.
This blend of human expertise and automated efficiency creates a potent mix that can significantly boost the cost-effectiveness of a welding operation.
Hirebotics - Revolutionizing MIG Welding with Cobots
At Hirebotics, we're pushing the boundaries in the realm of MIG welding. Our unique approach hinges on the integration of cobots, offering a solution that emphasizes user-friendly programming, swift support, and seamless integration into your existing infrastructure—the Cobot Welder.
Our Approach to Automated MIG Welding
Our unique approach to MIG welding involves deploying cobots from Universal Robots and augmenting them with our custom software (Beacon) that runs on your tablet or phone! Beacon is a free app that operates directly on the robot controller and negates the need for any additional hardware, thus eradicating startup costs and network complications.
This setup creates a user-friendly and adaptable MIG welding solution that stands out in the market.
A common industry challenge is delayed response to support calls. We see that challenge, and we’ve done something about it. We prioritize customer support in our business model. With our in-app support system, you can expect responses within just two minutes, meaning your concerns are addressed promptly, and operational disruptions are minimized.
Quick and Easy Implementation
At Hirebotics, we understand that any operational change needs to cause minimal disruption. That's why our systems are designed for swift implementation. They reduce the downtime associated with incorporating new machinery, ensuring your operations get back to full capacity as soon as possible.
The quicker a system can be implemented and begin delivering results, the better it is for your business. And we strive to make this a reality for you.
Seamless Integration with Existing Infrastructure
One of our core strengths at Hirebotics is the adaptability of the cobots we use. They are designed to integrate smoothly with existing production lines or welding workstations. The flexibility and compact design of cobots make it possible to slot them into your current layouts without requiring extensive overhauls or space adjustments.
This seamless integration means you can start reaping the benefits of automation without fuss and lower integration costs. It's a testament to our commitment to providing user-friendly, efficient solutions that deliver real, tangible results to our clients.
Empowering Welders with Cobots
Cobots are not just about automation—they're about empowerment. They are a tool designed to enhance and upgrade the skills of your existing workforce and to open up new avenues of productivity and efficiency in the welding industry.
The Role of the Existing Workforce in Cobot Operation
The introduction of cobots into the welding process doesn't diminish the importance of skilled welders; it enhances it. Cobots are tools that can be operated and monitored by existing welding professionals. By learning to work with cobots, welders can enhance their skill set, becoming proficient in the latest technologies that are shaping the future of the industry.
The integration of cobots means welders can be reassigned to tasks that require human insight and problem-solving skills. Rather than being replaced, welders become an even more vital component of the industry, operating and overseeing automated systems that increase productivity and reduce error.
Building a Future with Cobots
Cobots are here to aid and empower the existing workforce, not to replace it. They provide an opportunity to upgrade skills, improve work conditions, and increase output in a way that benefits everyone involved.
In essence, cobots represent a more productive future for the welding industry—one where human skill and robotic efficiency combine to produce the best results. By embracing cobots, we're not just investing in technology; we're investing in the welders who make our industry possible. With cobots, we can look forward to a future of welding that is safer, more efficient, and more rewarding for everyone involved.
Last Thoughts about Robotic MIG Welding
As we've explored in this article, the advent of cobots represents a significant turning point for the welding industry. These innovative machines are more than just automation tools—they're catalysts for enhancing productivity, improving job quality, and empowering the welding workforce.
With their user-friendly programming, rapid support, and seamless integration, cobots like those offered by Hirebotics, are driving change in the MIG welding process. They're tackling the common challenges of manual MIG welding and providing an efficient, reliable solution that complements rather than replaces the invaluable human skill.
Embracing cobots is not just a decision about technology—it's a strategic move towards a more productive, skilled, and efficient future in welding. We at Hirebotics are at the forefront of this revolution, committed to providing robust, user-friendly, and efficient cobot solutions.
If you're ready to harness the power of cobots and propel your MIG welding operations into the future, we're here to help. Get in touch with us at Hirebotics, and let's build a more efficient, more empowered future in welding together.