15 Types of Welding Processes with Their Advantages and Limitations
May 3, 2024
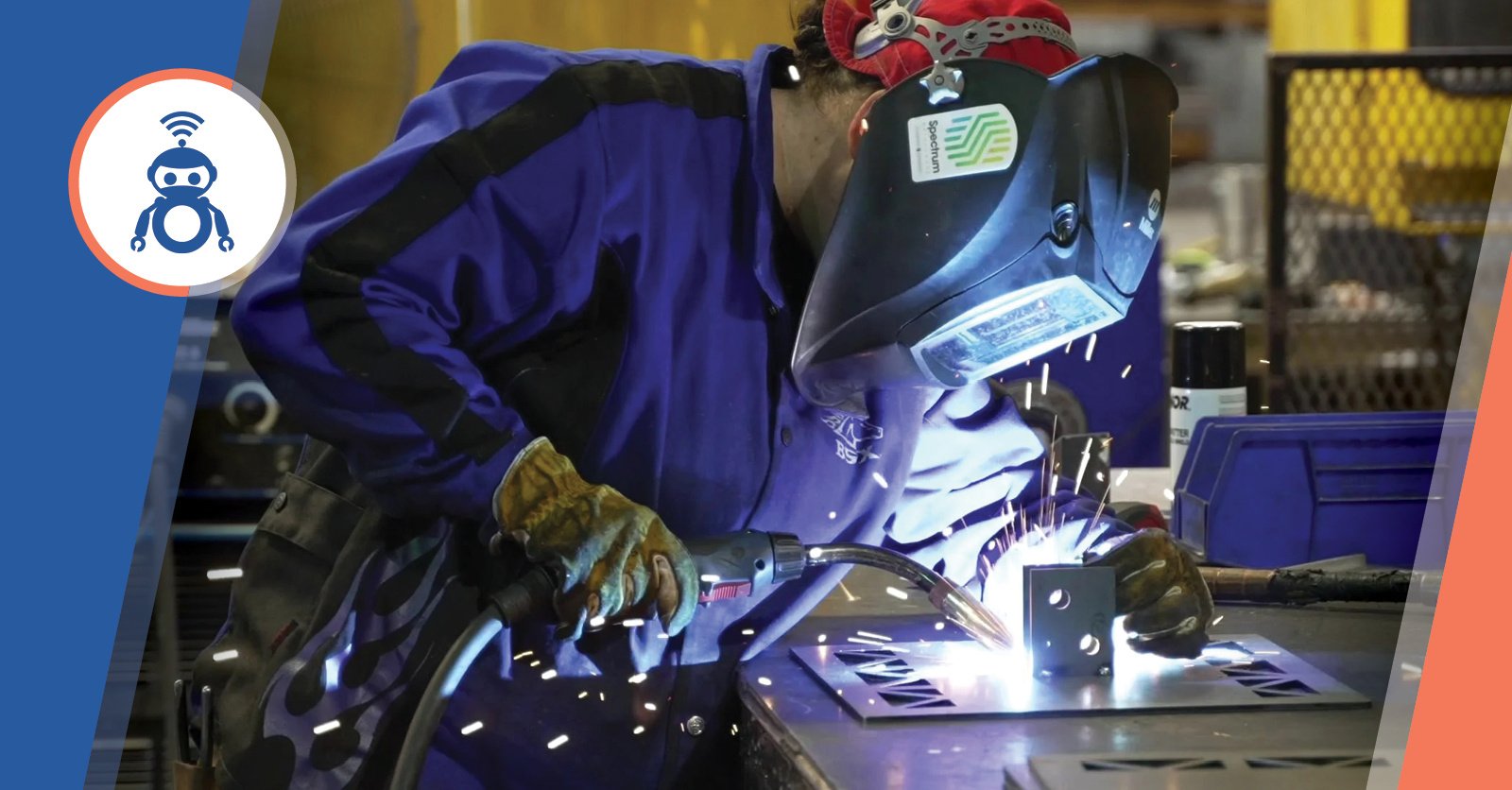
As a welder or welding manager, you probably already know about the common welding processes. 😅 However, we got curious and found out about many more welding types and techniques used in various industries.
We even compiled welding acronyms like GMAW, GTAW, and SMAW in an easy-to-refer table. Enjoy!
Table of Content |
What is Welding?
Welding in its very basic form, is the joining of two metals through heat or pressure. It’s an ancient process that dates back as far as the Iron Age. During that time, our ancestors hammered two metals together using heat.
All the welding equipment and techniques we see today started during the Industrial Revolution. Since then, the welding process has progressed significantly. Now, different types of welding processes are used depending on factors such as:
- Type of metal welded - aluminum, copper, steel etc.
- The thickness of the metal
- The welding environment (inside, outside, underwater, etc.)
- Where the final product is going to be used - hospital, automotive, aerospace, etc.
The welding industry is made even more exciting with its shift to automation, but that is for another article.
The 4 Main Types of Welding Processes
There are many different types of welding methods. The welding type you choose depends on the application. Four common welding techniques are widely used in the welding industry. These are:
- Gas Metal Arc Welding (GMAW or MIG)
- Gas Tungsten Arc Welding (GTAW or TIG)
- Shielded Metal Arc Welding
- Flux Cored Arc Welding
These types of arc welding join two pieces of metal with the assistance of an electric arc. This electric arc is formed between the metal part and an electrode on the gun.
Gas Metal Arc Welding (GMAW or MIG Welding)Gas Metal Arc Welding (GMAW) is also popularly called Metal Inert Gas Welding (MIG) among welders.
In this welding process, the wire electrode also acts as the filler metal to create the weld. It is constantly fed through the welding gun as it melts. MIG also uses shielding gas that comes in the form of carbon dioxide, oxygen, helium, or argon. This gas traveling through the welding gun is essential. It helps protect the molten pool of metal (weld pool) from environmental contaminants that can affect the quality of the weld.
GMAW is the most accessible type of welding to master. It is often used for welding stainless steel, copper, nickel, carbon steel, and aluminum. This type of welding is also best for lower-volume work, usually found in medium welding businesses.
Advantages of Gas Metal Arc Welding (MIG Welding)
GMAW is popular and can join metals of different thicknesses. It’s easy to learn and master, and the components needed to start welding are readily available. It has one of the best deposition rates, making it suitable for low, medium, and high-volume environments.
Gas Metal Arc Welding can be easily automated with Cobots like the Cobot Welder from Hirebotics. The Cobot welder is a robotic arm with a welding torch at the end of the arm built to work alongside welders, producing high-quality welds. It can be deployed on the factory floor to help automate the monotonous parts of welding. Using our Beacon software, it’s also the easiest cobot in the market to program - you can teach it through a phone or tablet application!
Find Out More about Why Collaborative Robots Are Changing the Welding Industry Here!
Limitations of Gas Metal Arc Welding (MIG Welding)
With GMAW, you always need a bottle of gas for shielding. And depending on what gas you use, it can be expensive. The positions you can weld with standard GMAW are also limited. However, the different types of transfer, short-arc, spray, globular, and buried arc, allow it to be more versatile. In addition, you can’t use the GMAW process outdoors because elements like wind can adversely affect it.
Gas Tungsten Arc Welding (GTAW or TIG Welding)Of all the welding techniques, Gas Tungsten Arc Welding (GTAW) is the most versatile. People in the welding industry also call this type of welding Tungsten Inert Gas Welding (TIG Welding).
As its name indicates, this type of welding uses a tungsten electrode. This electrode is what gives current to the welding arc. Like GMAW, Gas Tungsten Arc Welding uses gas shielding. It’s commonly used for welding aluminum and magnesium. TIG welding can also be used to weld metals such as copper, copper alloys, nickel alloys, and stainless steel.
Gas Tungsten Arc Welding (TIG Welding) produces precise and neat welds. This welding process found uses in industries like electronics, aerospace, automotive, repair, and even art.
Advantages of Gas Tungsten Arc Welding (TIG Welding)
Welds made from Gas Tungsten Arc Welding are very precise and have a neat appearance. The welds have a superior cosmetic appearance compared to other welds. GTAW is often chosen for visible welds because it creates an aesthetically pleasing appearance. These welds are also durable and of high quality. Gas tungsten arc welding can be used to weld a wide variety of metals, making this a versatile process.
Limitations of Gas Tungsten Arc Welding (TIG Welding)
Gas Tungsten Arc Welding is complex and requires a great deal of expertise. Welders using this welding process use both hands. They use one hand to hold the torch and the other hand to hold the filler metal.
Most of the time, only experienced and educated welders can manage this type of welding in a production environment. And, although it produces strong welds, you have to be sure to work with clean metals as impurities can produce weaker welds. In GTAW, you have to be careful that the tungsten material doesn’t go to the molten weld, or it can contaminate the welding pool.
Shielded Metal Arc Welding (SMAW or Stick Welding)Shielded Metal Arc Building (SMAW) is also called stick welding. It’s one of the earliest and most common welding techniques. In this type of welding, you’ll use a protected and consumable electrode (stick). This stick melts in the arc and becomes the filler metal to join the two metal parts. As the stick melts, it also emits a gas that protects the area to be welded.
Construction, underwater pipelines, and industrial fabrication use this type of welding. You can use this type of welding to join steel, cast, ductile iron, nickel, or copper. However, it’s rarely used on aluminum.
Advantages of Shielded Metal Arc Welding (Stick Welding)
This type of welding is portable and does not require external shielding gas, making it possible to weld anywhere. SMAW doesn’t need the metal to be free of impurities. So you can even use this type of welding process on rusty materials. You can also easily change the welding rods to adapt to different metals.
Limitations of Shielded Metal Arc Welding (Stick Welding)
This type of welding is advanced and needs skilled welders. It also produces a lot of waste from the materials used -mostly coming from the slag. The slag is the leftover material formed at the top of the welded metal. It’s also slower because you need to chip away the slag every time the rod is finished.
Flux Cored Arc Welding (FCAW)Flux-Cored Arc Welding (FCAW) is similar to Gas Metal Arc Welding but can be performed without shielding gas. The difference lies in the electrode material. FCAW uses a flux-cored electrode as a filler material for the weld.
Flux is a mix of silicate and carbonate material. Since its density is lighter than the welded material, it floats to the surface. The flux protects the metal being welded from contaminants from the atmosphere. FCAW is usually the welding technique used in bridge construction, shipbuilding, and heavy equipment repair.
Advantages of Flux Cored Arc Welding
Flux Cored Arc Welding has a heavy deposition rate. Depending on the electrode used, a welder can deposit anywhere from 3 pounds up to 20 pounds (9kg) of metal. It also has a more stable arc compared to other types of welding processes.
Unlike GMAW, Flux Cored Arc Welding can be used outdoors without gas shielding. Moreover, the metal doesn’t have to undergo precleaning. You can also weld in any position with this type of welding process.
Limitations of Flux Cored Arc Welding
FCAW produces more smoke than other welding methods. Sometimes, the smoke is even carcinogenic. So, if you want to do FCAW indoors, make sure that the area is well-ventilated.
The electrode is more expensive, and the metals it can weld are limited to carbon and stainless steel, cast iron, and hard surfacing alloys.
What Are The Other Types of Welding?
The four we’ve discussed above are the most common types of welding processes. But there are other welding processes that are also worth being familiar with.
- Electron Beam and Laser Welding
- Thermit Welding
- Submerged Arc Welding (SAW)
- Plasma Arc Welding (PAW)
- Gas Welding/Oxyacetylene Welding
- Electroslag Welding (ESW)
- Resistance Welding (RSW)
- Stud Welding (SW)
- Friction Welding (FW)
- Cold Welding (CW)
- Atomic Hydrogen Welding (AHW)
Electronic Beam welding and Laser Welding is a welding process where two metals are fused using a beam of high-velocity electrons or a laser. The welds made by this process are precise and very high quality.
The welding process only takes place inside a special vacuum atmosphere. This vacuum environment ensures everything is stable for the electrons to do their job. Industries like aerospace and car manufacturing use this type of welding.
Thermite WeldingThermite Welding, or exothermic welding, is a welding process that uses molten metal to permanently join the metals to be welded. The process needs thermite - a mixture of metal oxide and aluminum powder.
The process is an exothermic reaction of the thermite composition that heats the metals and fuses them together. An external heat source ignites the thermite and starts the chemical reaction. This type of welding is commonly used to weld cracks in railways and make heavy, strong joints for large pieces of machinery.
Submerged Arc Welding (SAW)The Submerged Arc Welding process is a type of arc welding. The formation of the arc is made from an electrode, acting as the filler material. The weld zone is entirely covered with a layer of granulated flux, hence the term "submerged" in the name.
This flux is made from carbon and silicate material. The flux generates a gas shield and facilitates electrical conduction when molten. During the welding process, the flux is continuously delivered by a tube attached to a flux hopper.
The entire welding process is mechanized and is buried under the granular flux, so it can’t be seen from the outside.
This type of arc welding process can have a high metal deposition rate of up to 20 kg/hour. It also has a capacity for welding metals with thicknesses up to 100mm. This type of welding is often used in heavy fabrication industries. The aviation industry, shipbuilding, railroads, and bridge-building also use this type of welding.
Plasma Arc Welding (PAW)Plasma Arc Welding or PAW is a type of arc welding similar to Gas Tungsten Arc Welding. The similarities lie in the arc created between a tungsten electrode and the object being welded. However, in PAW, the plasma arc is isolated from the shielding gas. Isolation is done by putting the electrode inside the torch’s body.
The arc is also constrained by plasma pushed through a fine-bore copper nozzle. The electronics industry often uses this type of welding. It’s also found application in the aerospace industry.
Gas Welding/Oxyacetylene WeldingGas Welding is also known as oxy acetylene-fuel welding or oxy welding for short. This type of welding process is a form of solvent-based fusion welding.
This process involves a handheld torch that pumps out acetylene and oxygen—combining these two burns to form a flame that connects the surface of the two metals using oxygen as the fuel.
The flame produced from combustion is scorching - more than 4500 degrees Fahrenheit. This intense heat is more than enough to weld two metals together.
Welders usually use this welding technique to join thinner metals. These types of metals can be ferrous, non-ferrous metals, alloy steel, carbon steel, etc. Moreover, it has been used in the aircraft and automotive industries.
Electroslag Welding (ESW)
This advanced technique is specifically designed to vertically join thin metal plates edge-to-edge. Unique to ESW, the welding action occurs directly between the edges of the plates rather than being applied externally to a joint.
The process begins by positioning consumable metal guides between the two plates, setting them up for the welding operation. A copper electrode, which doubles as the filler material for the joint, is then introduced through these guides.
The welding arc is initiated by applying an electrical current, and the weld begins at the start of the seam, progressively moving across the designated weld area. This movement is meticulously controlled by a machine, rendering the process fully automated once the plates and guides are set up.
Electroslag Welding is predominantly used for joining low-carbon steel plates that are exceptionally thick. It can also be aptly applied to structural steel, provided certain precautions are considered.
A distinctive feature of ESW is its reliance on slag conduction, which is pivotal in carrying the welding current through the process.
Electroslag Welding (ESW) finds its application in industries such as shipbuilding, power generation, and petrochemical sectors, where it serves as a crucial welding process.
Resistance Welding
Resistance spot and seam welding (RSW) join two or more welded metal sheets by melting them between the two electrodes as a result of electrical resistance flow. The electrodes introduce electricity into the metal sheets. However, welded metal sheets have a higher resistance to electricity than electrodes, causing them to melt and fuse. The electrodes also apply pressure before, during, and after the welding process.
Resistance welding is used in the automotive industry, appliance production, aerospace, and general fabrication, where sheet metal must be welded quickly.
Stud Welding
Stud welding is most commonly applied as an arc welding process where the electric arc is drawn between the stud and the metal surface, causing them to fuse. The stud gun also applies pressure, plunging the stud into the molten pool. It doesn’t use filler metal, but can require a shielding gas or a ceramic shielding ferrule.
Stud welding is extremely fast. It’s the most productive way to weld a large number of studs to the metal surface. It’s most commonly used for through-deck welding in construction, where shear studs are welded to the steel deck before pouring the concrete. They are also heavily used in shipbuilding (decks), equipment manufacturing, insulation fastening, cable management, piping supports, and other applications where studs are irreplaceable.
Friction Welding
Friction welding is an advanced welding process typically used in high-volume production. It involves rapidly moving one part over the surface of another or rotating it, causing friction that melts and fuses the two.
Friction welding and its subgroup friction stir welding are used in industries where weld quality must pass stringent standards. Some applications are aerospace, defense, chemical, nuclear, and similar industries. Equipment for friction welding can be very expensive and the working process may not be possible for all parts. For example, one part must be symmetrical, and the process must support rotating the part around its symmetry axis.
Cold Welding
Cold welding uses pressure to form a weld between two metals pressed together. It’s most commonly used for welding wires and applications where electric arc or flame could be hazardous. It’s limited to welding ductile and face-centered cubic lattice structure metals like aluminum and copper.
Atomic Hydrogen Welding
Atomic Hydrogen Welding (AHW) is a type of arc welding. It uses an arc between two electrodes made of tungsten with hydrogen gas. The electric arc between the two electrodes breaks down the hydrogen molecules. The molecules later recombine and produce a very high amount of heat. This heat facilitates the welding process by fusing the two metals. Nowadays, the GMAW welding process replaced AHW.
Welding Abbreviation Table
Abbreviation | Full Name | Description | Best Use Cases | Critical Things to Consider |
GMAW / MIG | Gas Metal Arc Welding | Uses a wire electrode and shielding gas. It’s used for welding stainless steel, copper, nickel, carbon steel, and aluminum. | Welding sheet metal and thick sections, large groove filling, general fabrication. Most welding applications in most industries. Also, to replace TIG where possible. With the right system, MIG can produce TIG-like welds. |
Transfer mode affects characteristics and application. Must use shielding gas. Multiple gas options for varying results and costs. Easy to learn. The easiest process to automate. Exceptionally versatile. |
GTAW / TIG | Gas Tungsten Arc Welding | Uses a non-consumable tungsten electrode and a shielding gas. It’s used for welding aluminum, magnesium, copper, copper alloys, nickel alloys, and stainless steel. | High-quality, critical welds requiring high precision and purity. (high-value industries like semiconductors, aerospace, marine, petrochemicals, etc.) | Slow travel speed. The most difficult arc welding process to master. Must use shielding gas. Can induce too much heat and have a wide HAZ. Tungsten selection and shape affect characteristics. |
PAW | Plasma Arc Welding | Similar to TIG, but the torch has two nozzles: one constricts the arc and isolates the electrode in an orifice gas, the other provides the shielding gas separate from the electrode. By constricting the arc with a tight orifice, PAW has many advantages over TIG. | Same as TIG, but with better weld quality. | Lift/touch start is not possible, only HF start. Many PAW variables must be set right. It’s a complex process to use. Arc can’t be easily deflected due to high stiffness, leading to better stability. |
SMAW | Shielded Metal Arc Welding or Stick Welding | Commonly known as stick welding, it uses a consumable electrode coated in flux. This type of welding is used to join steel, cast, ductile iron, nickel, or copper. | Outdoor welding in adverse conditions. Pipeline welding and structural steel. Indoor/outdoor welding where joints are difficult to access with other processes. Stick rod is long and can even be bent to access the joint. | Slower than FCAW/MIG. Produces slag. Produces material waste due to discarding the unused part of the electrode. There are hundreds of AWS-classified stick rods you can use. It’s exceptionally versatile. |
FCAW | Flux Cored Arc Welding | Similar to MIG, but uses flux-cored electrodes as a filler material for the weld. They can be self-shielded (no need for a shielding gas) or gas-shielded (require gas). | To replace the stick welding process (self-shielded FCAW) in outdoor welding, and for gaining additional deposition with gas-shielded FCAW. Used in shipbuilding, structural steel, bridge building, and pipe welding. | Produces slag (even gas-shielded FCAW). Runs hotter than MIG and can burn through sheet metal. You can use some wires with 100% CO2 gas to cut gas costs. Can’t weld aluminum. Some wires can’t be used for all-position welding. |
SAW | Submerged Arc Welding | Type of arc welding that uses an electrode that acts as the filler material. The weld zone is entirely covered with a layer of granulated flux, hence the term "submerged" in the name. | Heavy-duty welding of very thick structural steel or pressure vessels. | Granular flux can significantly impact the weld and should be selected for the used wire. Multi-wire Sub-arc can drastically boost deposition rate. |
ESW | Electroslag Welding | Produces metal coalescence through molten slag melting the filler metal and the base material. The arc only exists at the beginning of the process. It’s soon extinguished, letting the molten slag conduct electricity and fuse the metal. | Single-pass welding of thick plates in vertical or above 45-degree positions. | Extremely high metal deposition and speed. Preheating isn’t typically required. No spatter. 100% deposition efficiency. Can only be used for carbon steel and some stainless steels. Can’t be used on materials thinner than 1/2-inch. |
EGW | Electrogas Welding | Uses a solid or a flux-cored wire, with or without a shielding gas, with backing shoes (dams) to retain the molten metal. | Vertical welding of 1/2 to 1-1/2-inch thick plates. | Requires backing. Challenging process to learn. High heat input can negatively affect the weld zone. |
EBW | Electron Beam Welding | Uses a beam of high-velocity electrons in a vacuum to weld materials. Can also be used in a nonvacuum environment with a shielding gas. | Applications where maximum weld quality is needed. Aerospace, nuclear, and similar industries. | Can make shallow or extremely deep autogenous welds. Nonvacuum welding can require a shielding gas. |
LBW | Laser Beam Welding | Works by sending a highly focused beam of light (laser beam) to the metal, causing it to melt and fuse with or without the filler metal. | High-quality welds on thinner materials. | Non-contact process. High welding speed. Requires very accurate joint fit-up. Mostly limited to sheet metal and low thicknesses. Aluminum, copper, and similar reflective metals are challenging to weld. Equipment and fixturing costs are high. |
FW | Friction Welding | A solid-state process that fuses the two metals by rotating or moving them relative to one another with surface contact, causing friction between the two to melt and weld them together. | High-volume production and dissimilar metal welding in critical industries like aerospace. | No filler metal. Typically no need for shielding gas of fluxes. High weld quality. High equipment cost. Part alignment for FW can be difficult. |
RSW | Resistance Spot or Seam Welding | Two electrodes clamp sheet metal, causing the spot or seam weld to form as a result of electrical flow resistance. Electrodes apply force prompting the materials to fuse together. | Sheet metal work, cans, containers, various automobile parts. | There are many electrode shapes, including wheels, cylinders, clamps, and others. Electrodes wear with use. Complex equipment maintenance. Costly equipment. |
SW | Stud Welding | This process uses a stud gun to weld studs onto metal surfaces. Can be used with or without a shielding gas. | For efficient stud welding. Typically used for shear studs in construction, ship’s decking, insulation pins, and similar applications. | Portable equipment. Extremely fast. Can weld almost all stud shapes. Sometimes requires using a ceramic shielding ferrule. |
Oxyacetylene | Gas Welding / Oxyacetylene Welding | Uses a flame produced by oxygen and acetylene to weld metals. | Repair welding when other processes aren’t suitable. | High explosion and fire hazard. Requires high operator skills. Relatively low travel speed. It’s not limited by electrical power availability. Ideal for fieldwork. |
TW | Thermite Welding | Thermite welding uses a thermic reaction between aluminum and a metal oxide (typically iron oxide). Once these two are mixed, an extreme amount of energy is released, and so is the filler metal. | For field welding. Railtrack welding, and ship, mill, and mold repairs. | Very dangerous process. Operators must be well-trained to deal with thermal chemical reactions. No need for additional power sources. |
CW | Cold Welding | Solid-state welding, where pressure fuses the two metal pieces. | Wire welding, sealing containers with flammable/explosive substances, and welding in environments where arc or flame are hazardous. | Fast and produces high weld quality. No liquid metal phase. Limited to specialized applications. |
AHW | Atomic Hydrogen Welding | Type of arc welding. It uses an arc between two electrodes made of tungsten with hydrogen gas. | Largely obsolete. An early arc welding process. Can be used to weld tungsten as it’s hot enough. | Not widely used. Equipment may be difficult to source. Extremely hot, requiring more operator care. |
Want To Know More About Welding?
Considering a career in welding is a great idea as it offers both interesting work and excellent job prospects. Due to a shortage of skilled welders, there is a high demand for welders, making it an ideal time to get started in this field.
In response to the welder shortage, welding companies have implemented automated solutions. Incorporating modern technology has made the welding industry more dynamic, utilizing welding machines and robotic welding. With welding technology advancing rapidly, more efficient and precise welding processes are available than ever before.
Whether you're looking to automate a portion of your production or seeking a collaborative robotic welding solution, Hirebotics has the expertise and resources to meet your needs. Discover how we are helping fabricators & manufacturers just like you to automate their processes.
Contact us today and let us help you take the first step towards transforming your welding process with accessible automation technology!