Transforming Manual TIG Welding with a Welding Cobot: A Success Story
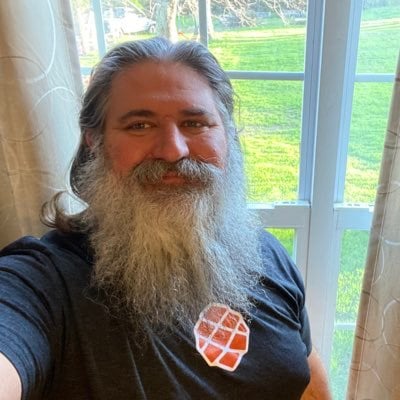
August 3, 2023
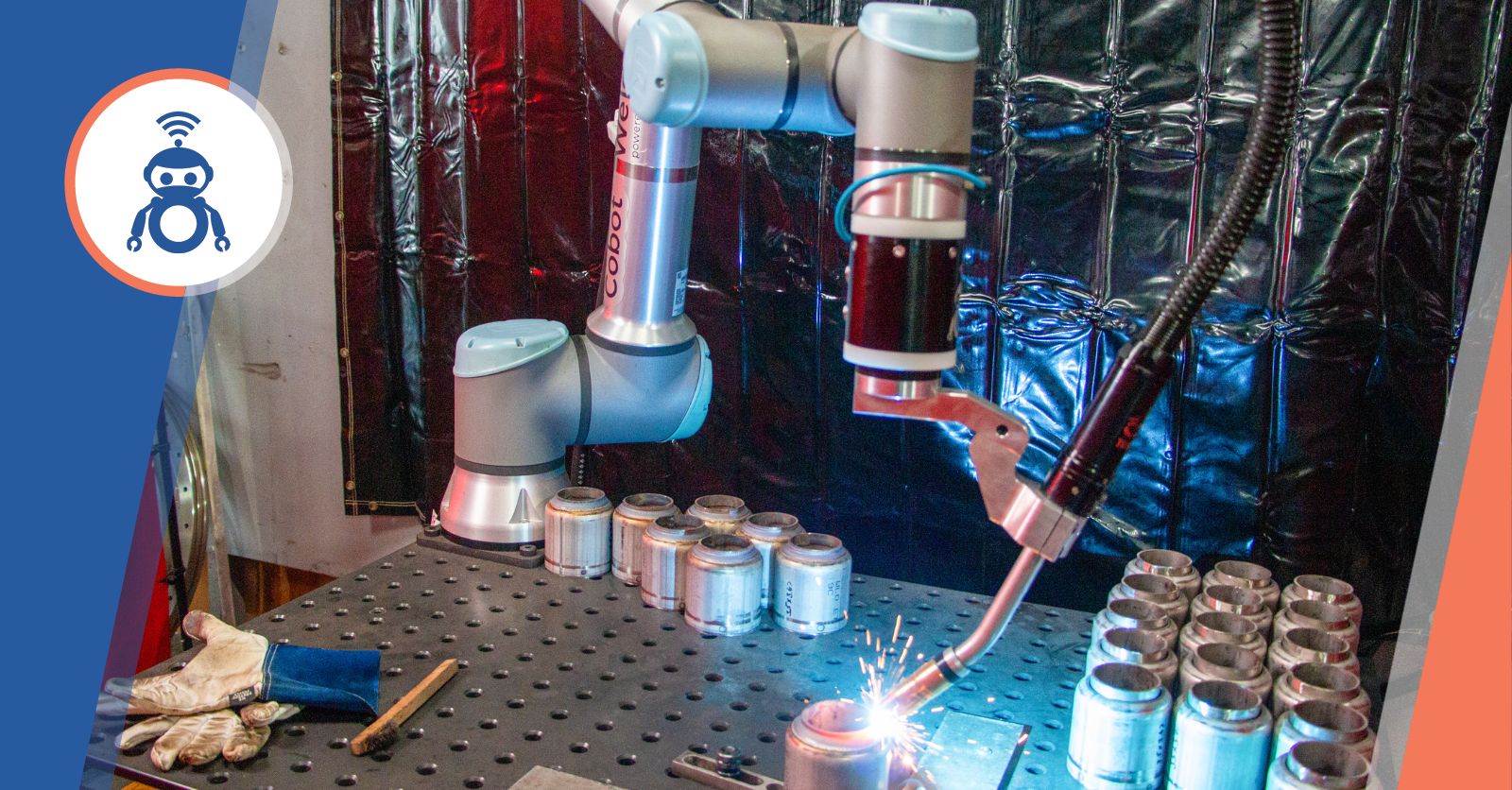
TIG welding is an incredibly versatile process, but it’s labor-intensive and demanding, and requires skilled and experienced welders. We understand that ongoing skills shortage and the pressure to enhance welding efficiency are daily challenges you face in the fabrication industry.
But what if we told you there's a game-changing solution for all of these problems?
Let's talk about transitioning from manual TIG to robotic MIG welding. Yes, you read that right!
While you might not have considered it before, the right cobot MIG welding solution has the potential to increase productivity, improve welding efficiency and eliminate the challenge of finding skilled welders.
Our client, DeAngelo Marine Exhaust inc, dealt with high demand and a shortage of skilled welders for their TIG welding operations by adopting cobot MIG welding. Their decision wasn't just successful, it transformed their marine exhaust fabrication process.
This article will explain how switching from traditional manual TIG welding to cobot MIG welding, can improve your production and solve your labor challenges.
Automating TIG Welding: Advantages and Challenges
As advancements in technology continue to revolutionize various sectors, the welding industry has not been left behind. The switch from manual TIG welding to automated welding is an exciting option that's gaining traction. It's essential to understand the pros and cons involved, and why cobot MIG welding stands out as a promising option for fabrication shops doing TIG welding.
Advantages of Automating TIG Welding
- Precision and Quality: Automated TIG welding boasts a high level of precision, producing exceptionally clean and visually pleasing welds. This leads to an overall improvement in the quality of the final product, vital for industries where aesthetics and precision are key.
- Consistency: Automation drastically reduces the risk of human error, bringing about remarkable consistency across all welding tasks. This makes it easier to meet quality control standards and increases efficiency in production.
- Speed: One of the notable advantages of automating TIG welding is its superior speed compared to the manual process. Robots provide a steady hand and, combined with finely tuned welding parameters, can achieve far higher speeds than a human welder.
Challenges of Automating TIG Welding
- Complexity: Automating TIG welding can be complex due to the high level of precision required and the accurate feeding of filler metal.
- Cost: The upfront cost of setting up an automated TIG welding system can be high. This substantial investment can be a barrier for smaller operations or those with tight budgets.
- Welding Environment Control: Automated TIG welding requires a controlled environment for optimal performance. Factors like temperature, gas purity, and cleanliness need to be closely monitored, which may be challenging in certain circumstances.
Key Takeaway |
|
The Compelling Case for Switching to Cobot MIG Welding
While switching from manual TIG welding to automated MIG welding may appear counter-intuitive, it offers many benefits—making it a smart strategic decision. However, to fully understand the benefits of this transition, it's vital to grasp how MIG welding compares to TIG.
Comparing MIG, TIG, and Cobot MIG Welding Approaches
MIG and TIG are both useful welding methods, but they have different characteristics that make them unique, especially when compared to the potential of cobot MIG welding.
MIG Welding |
TIG Welding |
Cobot MIG Welding |
|
Versatility |
Works with diverse materials like aluminum, stainless steel, and mild steel. |
Versatile but often used for thinner materials and more delicate welds. |
All the benefits of MIG welding and proven great for thinner material because of the control and consistency of the movement. |
Quality |
Produces high-quality welds but may require post-weld cleaning due to potential for spatter. |
Produces high-quality, clean welds with less spatter and post-weld cleaning. |
Matches TIG's quality while enhancing consistency. |
Speed |
Faster due to continuous wire feed. |
Slower, as it often requires manual filler feeding. |
Faster and more consistent than any manual welding process. |
Skill Required |
Easier to learn and master. |
Requires a higher level of skill and precision. 2-hand process. |
Skills are robot-specific. Collaborative robot solutions are simpler to learn and teach than traditional robotics. |
Automation Potential |
High, lots of options on the market, lots of options using cobots too. |
Lower, more complex to automate, fewer options on the market. |
High, lots of options on the market, and many cobotic solutions. The Cobot Welder, for example, offers the easiest solution on the market, as welders never have to touch a robot pendant. |
As you can see from this comparison, cobot MIG welding has significant advantages over manual MIG and TIG welding processes. With its high-quality results, speed, and ease of learning, especially with user-friendly cobot solutions like the Cobot Welder, it's a game-changer in the manufacturing world.
Why Choose Cobot MIG Welding
Cobot MIG welding, where cobots (collaborative robots) are used, stands as a compelling alternative to traditional robotic MIG welding.
- Simplicity and Efficiency: Cobots are designed to work alongside humans, simplifying the welding process and enhancing overall efficiency. They offer the benefits of automation while still retaining a level of human control and oversight.
- Cost-Effectiveness: Cobot MIG welding is often more cost-effective than traditional robotic welding systems. It has a lower setup and operational cost, making it a financially viable option for manufacturers.
- Ease of Implementation: Implementing cobots is easier compared to traditional automation because they can be integrated into existing workflows with ease. This ease of implementation makes cobot MIG welding an attractive alternative for businesses seeking to transition from manual TIG welding to an automated process.
Stop debating whether a welding cobot is right for your fabrication and see it live! Request a demo of the Cobot Welder and answer all of your questions!
Automating TIG Welding with a MIG Welding Cobot: The DeAngelo Marine Case Study
Real-world applications often speak volumes about the practical benefits of technological advancements. DeAngelo Marine's transition from manual TIG welding to MIG welding with the help of a cobot demonstrates how automation can greatly improve welding processes.
Decision Process: Why DeAngelo Decided To Switch From TIG to a MIG Welding Cobot
For DeAngelo Marine, the decision to switch was not made lightly. They found themselves grappling with labor shortages and the mounting pressure of pending orders from some of the finest boat builders, naval architects, and engine companies in the world.
"The last thing I want to do is promise them the world and be two weeks too late," says Justin Montes, the CEO of DeAngelo, highlighting the urgency to innovate and improve their workflow.
While exploring automated solutions, DeAngelo's attempts to find a reliable automated system proved disappointing.
"I had sent out parts to about seven of the big welding companies to see if they can do a demo weld," says Justin, "and a lot of those companies struggled to send me back parts that match our quality."
Implementation: Ease of Introducing and Integrating the MIG Welding Cobot
The turning point arrived when Hirebotics stepped onto the scene with their cobot welding solution. Not only did they promptly return a part demonstrating their welding proficiency, but they also had the team welding parts in a matter of minutes. "Twenty minutes later, I'm running parts like I've been running robots my whole life," he shared, highlighting the ease and simplicity of cobot MIG welding.
Results: How the MIG Welding Cobot Has Impacted DeAngelo’s Operations
The impact of the MIG welding cobot on DeAngelo's operations was immediate and transformative.
The cobot's ability to perform at a speed of "20 inches a minute" was a significant jump from the "2 to 5 inches a minute if you're good" that manual TIG welding allowed.
This marked increase in speed enabled DeAngelo to clear their daunting backlog in just a few weeks.
As for cost savings, Justin shares a compelling example:
"The day that we were installing the cobot we received a large order from the Coast Guard, now that part roughly requires 200 inches of welding altogether. It's five welds that need to be done in a sequence. If I'm using TIG welding by hand that's a hundred minutes to do one, but if I'm doing 20 inches a minute with the cobot that's 10 minutes to do one. That one order paid for my first cobot”
Looking ahead, Justin envisions a future where "our seven lead fabricators have a cobot with a UR arm on all their fabrication tables." Their experience serves as an instructive blueprint for companies considering a transition from manual TIG welding to automated MIG welding using a cobot.
Lessons Learned: What Other Manufacturers Can Learn From DeAngelo Marine Experience
DeAngelo Marine's journey from manual TIG welding to automated MIG welding offers valuable insights for other manufacturers considering a similar transition. Here are some key takeaways from their experience:
- Don't fear change, embrace it: DeAngelo Marine successfully increased their welding speed from a range of 2 to 5 inches per minute to a staggering 20 inches per minute. This dramatic improvement showcases the efficiency that embracing automation can deliver.
- Invest in proven, quality tech: DeAngelo Marine tried multiple welding companies before finding a solution that met their high-quality standards. It is crucial to do your due diligence when choosing an automation partner to ensure you're investing in technology that can deliver the desired results.
- Fast implementation isn't just a dream: DeAngelo Marine's experience shows that integrating a MIG welding cobot can be quick and seamless. The right technology and support from Hirebotics can streamline the implementation process, saving you time and effort.
- Expect fast ROI: The case of DeAngelo Marine shows how automation can quickly pay for itself. With a single large order, the investment in their cobot was justified, revealing the potential for considerable cost savings and productivity gains.
- Look ahead and plan for expansion: DeAngelo Marine's future plans to incorporate Hirebotics cobots into all their fabrication tables reveal the scalable nature of automation. Look beyond the immediate benefits and consider how automation can support your long-term growth strategy.
The impressive transformation of DeAngelo Marine from manual TIG to automated MIG cobot welding shines a bright light on the significant benefits that come with embracing automation in the welding industry.
With the right approach and technology, automation can significantly enhance efficiency, quality, and productivity in welding processes, delivering tangible business benefits.
Want similar results to Deangelo Marine? It’s possible!
Are you tired of facing the challenges posed by the ongoing welder shortage?
Do long delays in your fabrication process put a strain on your client relations? We feel your pain!
Fabricators like you are constantly seeking ways to boost productivity and streamline operations to stay ahead in the game.
Welding cobots are a great avenue, but they are not all created equal. Many are difficult to use and require a robot programmer, which will only add to your staffing issues.
But don’t worry, we have the perfect solution.
Say goodbye to complicated robotic jargon and lengthy training sessions. The Cobot Welder is the first industrial welding cobot that runs on an app that you can easily operate using your phone or tablet.
With the Cobot Welder, you'll have the simplest welding cobot on the market and be in production in a matter of hours.
Picture this – no more delays, no more labor shortages, and no more headaches.
Your welders, or even untrained personnel, can quickly master this user-friendly cobot in a matter of hours.
It's time to take charge of your fabrication process and elevate your client relations to new heights.
Embrace the power of automation with the Cobot Welder and watch your productivity soar! Don't miss out on this game-changing solution – jump on a virtual demo with our team!