Production Welding & Automation: Why Robotic Welding Is The Future
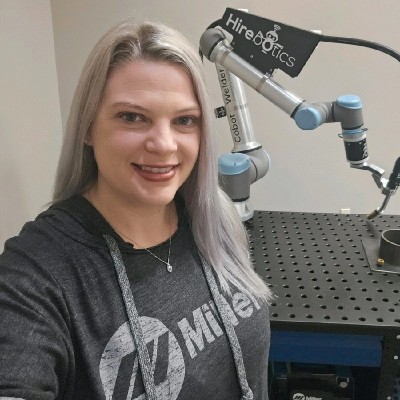
June 7, 2024
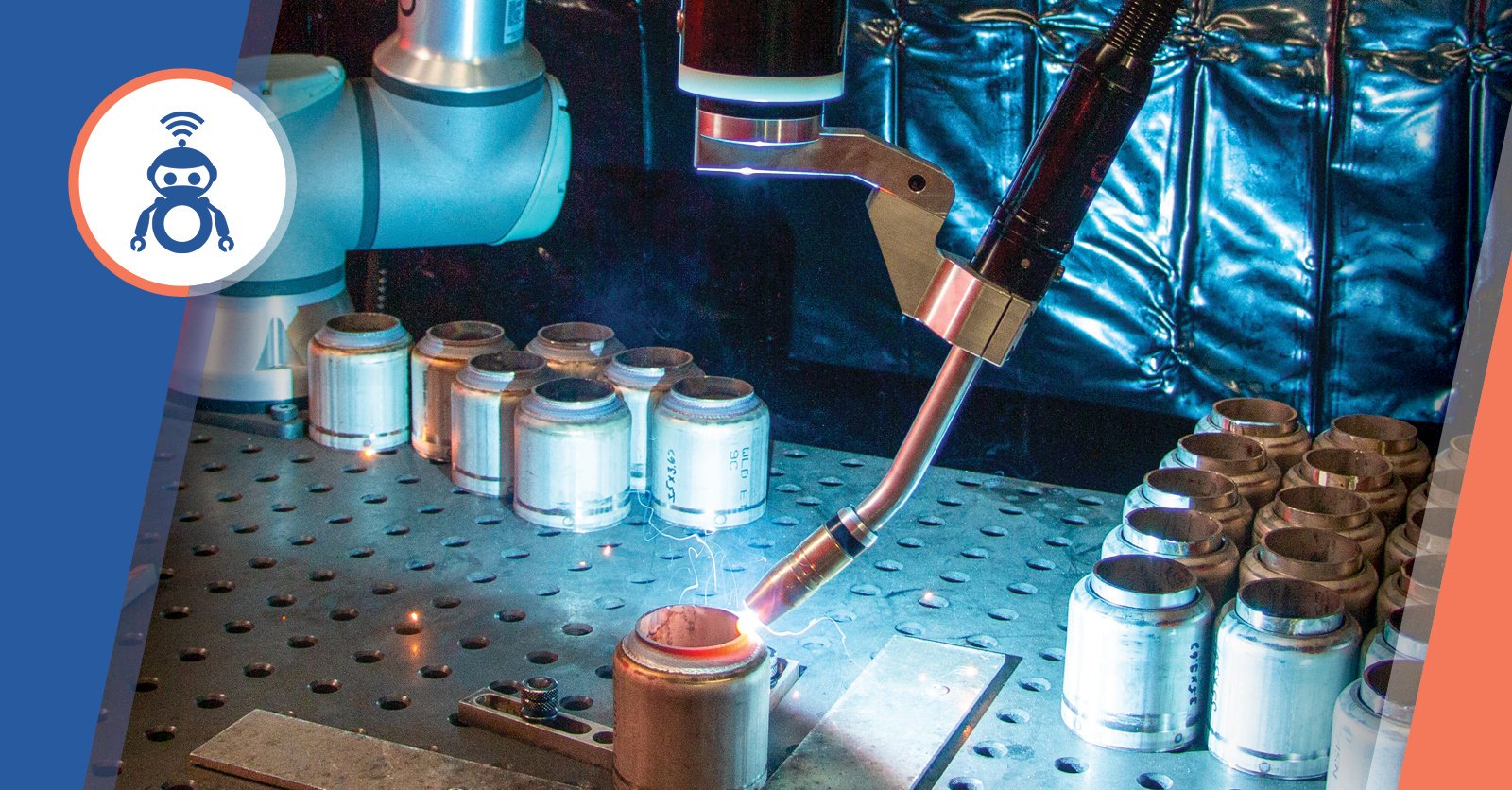
Production welding is mostly about repetition and volume, tasks ideally suited for robotics, not always for humans.
Many production welding operations advance from manual to automated welding once they reach their capacity. At some point, you simply can’t manually meet the demand with exceptional welding quality.
Read on to discover how robotics solves traditional production welding challenges and which system can give you immediate results.
Table of Contents |
What Makes Production Welding Different?
Whether in a manufacturing plant or fab shop, production welding creates new parts out of fresh materials. Production welders weld small to large volume batches with low to high part volatility.
It typically maximizes productivity and welding throughput without sacrificing quality. This is critical for achieving satisfactory profits and providing good quotes to the customers.
Fabrication vs. Manufacturing: Where Does Production Welding Fit?
The line between fabrication and manufacturing can be quite blurry. Generally, higher repeatability and volume are standard for manufacturing, while lower volumes with part volatility and one-off jobs are typical for fab shops.
Production welding fits both categories. But, as the volumes and part variability rise, the welding approach varies. One-off jobs, 10 variable 20-part batches, or one 5000-part batch, can all require more or less flexible automation and operator training.
Welding Processes Used In Production Welding
Production welding primarily relies on GMAW (MIG), while some specialized jobs require GTAW (TIG), SMAW, SAW, and laser welding processes.
GMAW or MIG is the most widely used welding process. It’s fast, easy to learn, equipment is inexpensive and produces excellent welds. And most importantly, MIG is the easiest process to automate.
GTAW or TIG is used for excellent weld aesthetics and accuracy. However, due to its low speed, some shops replace it with MIG to benefit from monumental productivity gains. For example, DeAngelo Marine Exhaust Inc. gained a 10X productivity boost after switching from TIG to MIG with our Cobot Welder.
Challenges Of Production Welding
Production welding is a fast-paced job riddled with challenges. Profit per part is typically low, so everything must go relatively smoothly to make it worthwhile.
Labor Constraints
The biggest challenge of production welding is labor constraints. Humans can only weld so much repetitively before their performance and weld quality drops. It’s repetitive and monotonous for the most part.
Young welders often join production shops to gain as much time under the hood as possible before switching jobs to something less monotonous. Retaining talented welders with repetitive jobs is difficult, especially now with the welder shortage affecting the whole industry.
Just take a look at how welders are talking about production welding on the r/Welding subreddit.
Of course, experiences vary from shop to shop. But many welders agree that production welding is good for gaining experience, not staying there for your entire career. So, shops struggle with onboarding experienced talent and have a high turnover rate.
Long Backlogs And Lead Times
Labor constraints mean long lead times and backlogs, causing bottlenecks in production. Customers want their parts ASAP and at a low cost per part since they are buying in bulk.
Excessive Production Costs And Lost Profits
Profits are getting squeezed out by excessive overtime and part defects. Parts often accumulate value along the production chain before welding. So, once fatigue kicks in, inconsistency and defects can rise, causing customer rejects or rework.
Overwelding is common in the industry, especially when the welder is rushing to clear that backlog. This results in more wire, gas, and labor costs.
Imagine a scenario…
Your shop must finish a 500-part batch soon, as the deadline approaches. Your welders are working overtime, they are tired, and their weld defect rate somewhat increases. Likewise, they are doing their best to clear the job, but they can’t focus on every weld to make it precisely as required (say 1/8" fillet), so they do 3/16" fillets, requiring more gas, wire, and time. So, you spend more (+ overtime), and you might get more rework or rejections. That’s far from ideal.
Unpredictable Production Schedule
Take the example above and imagine if your welder gets sick or simply feels burned out and can’t do overtime anymore. All of a sudden, you can forget about hitting the deadline.
Staying on schedule can be difficult if your welders call in sick or there are part quality issues. If a part with a defect slips by the inspection and gets to further post-processing before someone sees the issue, you get production bottlenecks. Even if you spot all defects in time, rework prolongs lead times and makes it difficult to meet deadlines.
Production Welding Automation Is The Future, And The Future Is Now
Robotic welding automation solves the vast majority of the problems outlined above. It multiplies your workforce, drastically boosts productivity, kills the monotony, makes everything more reliable, and drastically improves weld quality.
But robotic welding is difficult to implement, right? Not necessarily.
With robots, you can take two roads:
- Traditional Welding Robots - Best suited for very high volumes with low part variability. They can be challenging to program and require specialized staff. Likewise, they need more safety measures.
- Cobots or Collaborative Robots - A modern alternative to traditional robots best suited for low to medium volumes with high part variability. With the right cobot system, you can program parts in a few minutes without robotic welding experience.
Our Cobot Welder is programmed using our smartphone app, Beacon. You quite literally guide the robot’s hand manually to the weld and set up the weld in the app. Nothing except standard welding parameters — no programming language, no math, no XYZ coordinates, no complex teach pendants.
Any welder can learn to use our Cobot Welder in a day. Most people can run their first weld in minutes, even if they aren’t welders. We cut out the middleman (robotic tech), letting your welding staff use the robot, making it their most productive tool in the shop.
Advantages Of Welding Automation For Production Work
Some of the most significant benefits of our Cobot Welder are:
- Higher capacity
- Production reliability
- Massive productivity gain
- Safer than manual welding
- Higher profits, reduced costs
- Reduced or eliminated rework
- Dramatically less taxing on the operator
- Scaling the application of knowledge of your best welders
- Ability to take on higher-value jobs requiring robotic welding precision and quality
Take a look at our case studies. We quadrupled production for some, alleviated backlogs for others, reduced overtime, improved profits, cut costs, and helped everyone with the capacity and ability to take on more jobs.
Another added benefit is eliminating the soul-crushing monotonous tasks that cause welders to job-hop after gaining experience. When you give a cobot to the operator, their job becomes much more fulfilling. Now, they are responsible for robotic welding, not just churning out batches day in and day out.
And ease of implementation? Well… that’s kind of our motto here. If you are new to Hirebotics, just know that our entire approach is making automation accessible to everyone. That means every welder in your shop can use our Cobot Welder from day one!
Book a free demo with our team, and we’ll show you just how easy it is to work with Beacon. We’ll also discuss your parts and production to help you decide if the Cobot Welder is the right choice for your business.