Why Welding Robots Won’t Replace Welders Anytime Soon (Arguments for Welders)
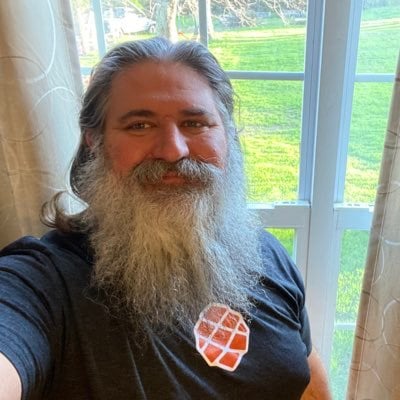
September 21, 2022
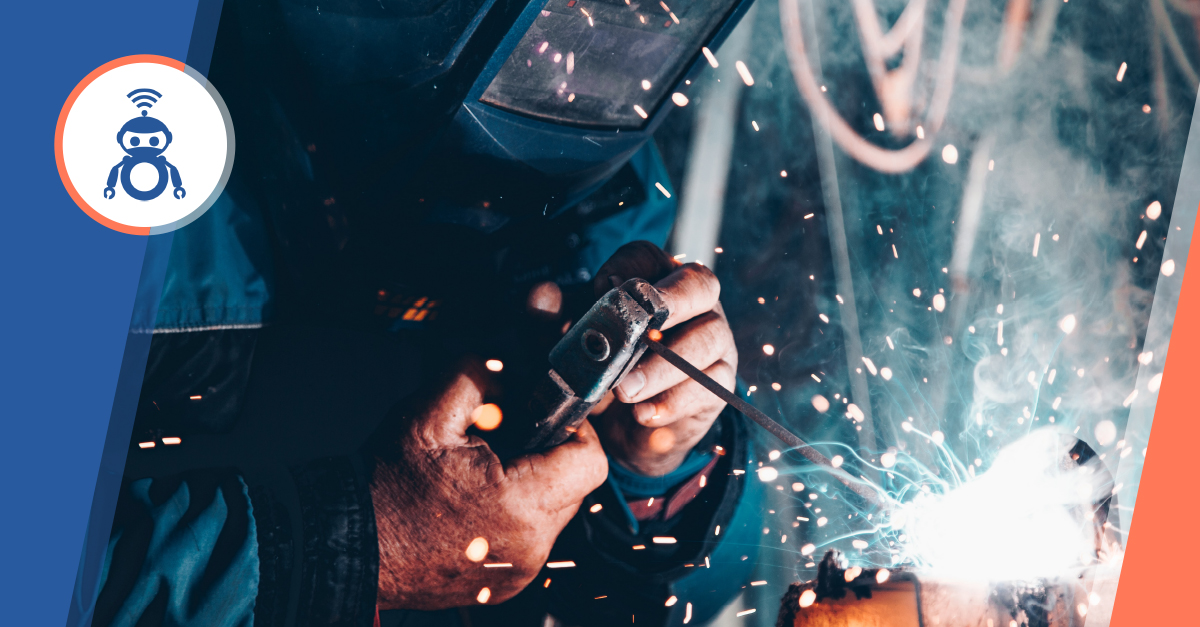
Just how much is welding becoming automated? Will welding be completely automated in the future? Will welding robots replace humans?
These are some of the many questions experienced, and younger welders are asking as they ponder the current state of automation in the welding industry. Due to the jarring shortage of welders and an abundance of news articles pointing to robots taking over welding jobs, many welders may be concerned that they will lose their jobs to automation.
However, the reality is more nuanced than that.
Let’s find out why.
What Is the Current State Of Automation in the Welding Industry?
Many experts predict that welding robots can replace up to 80% of welding jobs, with welding tasks becoming more and more automated over the next five to ten years. The reason? Manufacturers and fabrication shops are finding it extremely difficult to find welders. Here are some startling facts:
It stands to reason that companies are turning to industrial robots, and particularly collaborative welding robots (cobots) to keep up with demand, not lose sales and stay in business.
While robotic systems may replace several functional aspects of welding, there are many reasons why welding robots will not replace humans.
Let’s answer the main questions welders may ask!
Can Robots Replace Human Welders Completely?
There is great news for manual welders. There are many reasons why robots can’t take over welding spots. The idea that robots will replace humans is drastically exaggerated by fear-mongering and flashy headlines.
Robots need people (especially welders!) too
Automated manufacturing workflows with industrial robots and cobots nevertheless need experts to operate them. It is impossible to think that a company can simply set up a robot and let it run its course for each job. Qualified welders are still needed to help to operate the welding robotics systems, inspect parts, etc. Many businesses are providing comprehensive training to upskill welders in order to work with robots and elevate their work conditions.
Complex welding jobs
Industrial welding robots and cobots are often implemented to automate repetitive welding tasks and for high-volume production. Many welding jobs, however, are not suitable to be automated (more on that later). As product manufacturers develop more sophisticated designs in order to out-edge the competition, boost performance, or drive down costs, welding projects are increasingly becoming, in many instances, more complex. There are so many different types of welds for different industries and market needs, that expert human welders far outperform welding robots.
Low-volume/High-mix welding
Keep in mind that conventional industrial robots need to be reprogrammed for each welding job. This can be very inefficient and expensive for a business to use a welding machine for low-volume/high-mix work. It is much faster and more cost-effective for human welders to tackle low-volume/high-mix jobs. For example, some welding projects, such as in the pipeline and construction sectors, entail field work for on-site repairs or hard-to-reach places. An industrial robot just can’t cut it in these applications.
Agile and better decision-making
Artificial intelligence, also known as AI, is often described as going hand-in-hand with robotics systems and the panacea of the future of decision-making processes. Indeed, AI, which basically collects data from machines in order to improve manufacturing performance, will play a part in companies’ digital transformation towards automated welding.
Smart robots will provide the data businesses need to increase productivity and quality. However, just because robots generate data doesn’t mean they will be making all the decisions automatically. Humans, including welders and welding teams, will still be called upon to interpret the information and make the right decisions for welding projects and workflows.
How Welding Automation Is Impacting Jobs in the Welding Industry
Will robots take over welding? Will jobs in the welding industry drastically decrease because of industrial robots or cobots? The answer is no. There will always be a place for human welders. The jobs will shift and evolve, however.
The future of human welding is actually very bright! There are many job opportunities that will be available for a long time to come for welders. And, as mentioned before, as businesses acquire robots or cobots for welding, they are also planning to invest in training for welders to be able to use automated welding systems.
That is great news for welders who are looking to elevate their careers, job positions and salaries. Finally, as robots take on the dull, dangerous and dirty welding tasks, welders can enjoy using their expertise and ingenuity on more fun projects. Job satisfaction is likely to rise!
Will Automated Welding Take Jobs Away?
No, automated welding will not take jobs away from human welders.
As an article in Tech.co explains: robots don’t understand context and robots lack creative problem-solving. Industrial robots and cobots “just” do what they are programmed to do. In addition, they lack the dexterity for finer welding tasks. As one journalist quipped: would you trust a robot to cut your hair? Probably not.
While welding and hairdressing are two vastly different professions, you can appreciate the allusion to the fact that humans trump robots when it comes to complex jobs.
What Welding Jobs Can’t Be Done by Robots?
Welding robots replacing welders is pretty much science fiction. Welding jobs are multi-faceted, which means humans will be needed to carry out many aspects of a project.
Furthermore, many welding jobs cannot be done by robots. Here are a few:
Gas Tungsten Arc Welding
Gast tungsten arc welding (GTAW), which is also known as tungsten inert gas (TIG) welding, is an arc welding process often used to weld stainless steel and non-ferrous metals, like magnesium, copper, and aluminum alloys.
Since the filler metal needs to be brought in separately from the arc, the TIG process is a challenge to automate. Because it is a complex and difficult process, human welders are ideal for carrying out this welding process, as of now.
Prepping welds
As all welders know, proper weld preparation is key for producing high-quality components, maintaining productivity, and minimizing the costs associated with rework and downtimes.
From developing comprehensive welding plans, choosing the right products and equipment, cutting, fitting, and beveling the base material, to prepping and cleaning surfaces, readying a welding project takes time and know-how. Even if a welding robot or cobot will automate a job, a skilled welder has to nevertheless prep it.
Complex weld projects
Complex weld geometries and field welding can be too challenging for industrial robots. Robots are better suited for simple welds that do not involve 3D welding.
As an example, bringing a robot to a construction or pipeline site is cumbersome and not very cost-effective. Moreover, rugged or harsh field conditions can affect the performance of the robot. Human welders are likely to be assigned to these types of projects.
Small batches
As previously stated, it does not make sense from a cost and productivity perspective to assign small-batch welding production tasks to a robot or cobot. In order to automate small batches, the programming and setup times for the batches need to be less than the time it takes to actually weld the batches. If not, there are no productivity gains. Human welders or more modern cobot welders, which are faster and simpler to program, are often preferred.
New Welding Technologies Will Create New Jobs for Welders
As new technologies emerge in the market, such as welding cobots and Hirebotics’ Cobot Welder, they will definitely impact the job landscape for welders. Welding cobots will become tools for welders, just like their welding torch, to help them weld more as well as ditch the monotonous welding of high-volume parts.
Welding jobs will change. Here are some of the different types of welding jobs that will appear in the not-so-distant future.
Welding Robot Operator
A robotic welding operator is responsible for the set-up, maintenance, and operation of industrial welding robots and welding cobots.
Welding Robot Programmer
Welding robot programmers develop, test, and modify robot programs that instruct robots what to do for any given subject. They are responsible for using robotic software.
Robotic Welding Fixture Designer
Robotic welding fixture designers are tasked with creating welding fixture designs as these can be quite challenging and drastically affect the output (think repeatability and consistency) of welding jobs.
Robotic Welding Manager
As the job title implies, robotic welding managers manage robotic welding teams. They also optimize a company’s welding operations and find new parts to produce with the robot (those actually being produced or new quotes).
Conclusion
As manufacturers transform their production lines to take full advantage of robots or cobots, the key takeaway is that welders should not fear welding robots replacing welding jobs. Welding robots will not replace welders. The job of a welder will evolve and actually enhance many welders’ careers, thanks to training, better work conditions, contentment at work, and an overall improved appreciation of the profession.
Want a stress-free way to implement your first robotic welder? Talk with one of our experts today.