Welder Help Wanted: Expand Your Workforce with a Robotic Welder
August 5, 2021
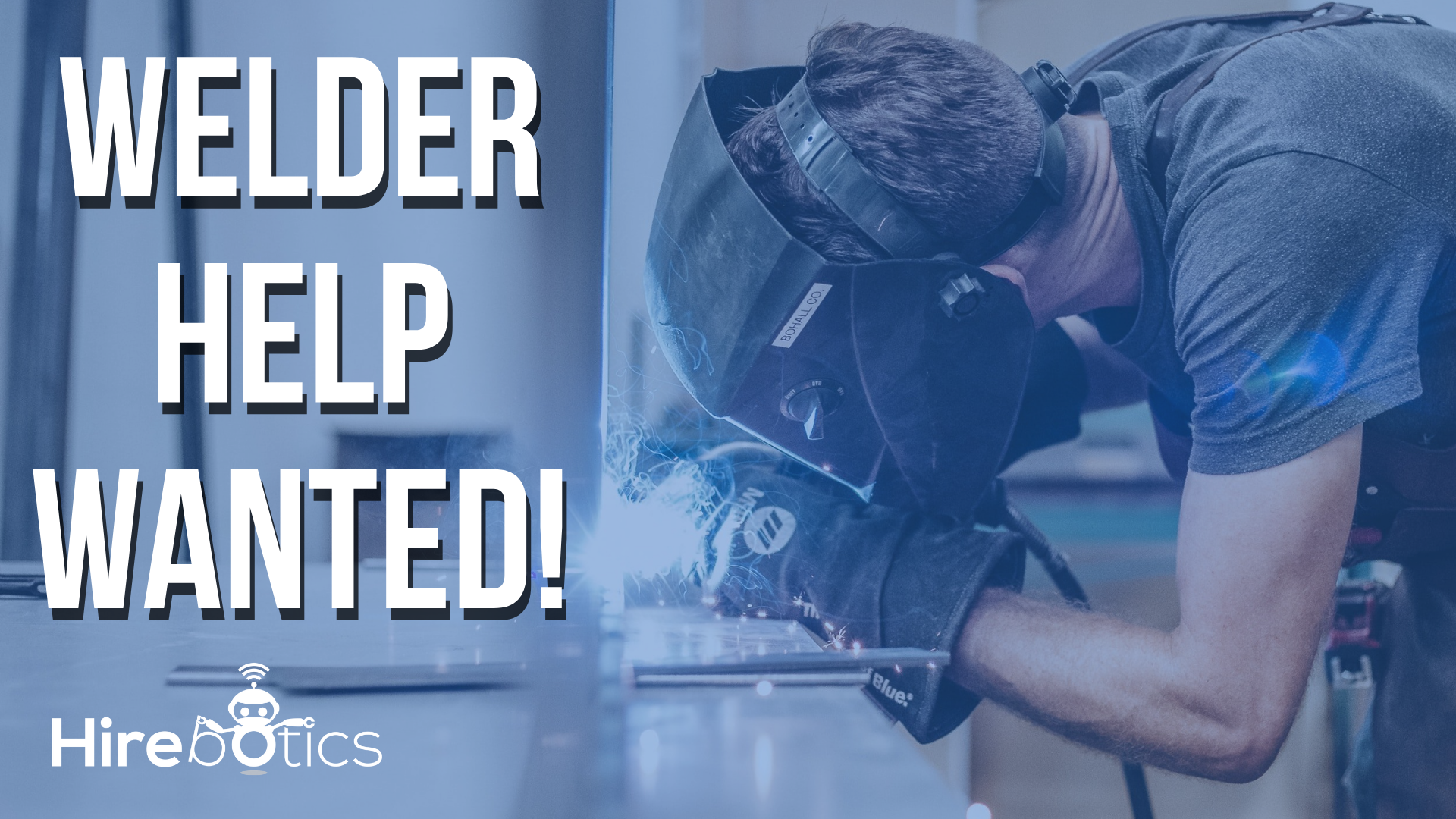
Welder Shortage: The Situation
The world is experiencing a welder shortage. In the US, statistics predict that there will be 375,000 welder jobs unfilled by 2023.
Chances are if you’re running a small to medium welding business, you’ve already experienced the headache of trying to hire experienced welders from a limited pool. You don’t need numbers to tell you this. You’ve felt firsthand the statistics and the dire predictions. The more important question now is how do you solve YOUR welder shortage problem?
Do the Obvious: Increase wages and be more aggressive in recruiting
In tight market economy situations and a dwindling talent pool, there are two things that you can do. The most obvious thing is to increase wages to make your offer more attractive to potential welders. You can pair this with an aggressive recruiting strategy. Together, you can get first dibs on budding welders.
It looks like a great solution from the surface, and these strategies can even get you a welder or two. But this kind of tactic has some not-so-pleasant consequences.
Your company is not the only one who is doing this strategy. Other businesses need welders too. And are also increasing their salary offers. This competition can cause you to unwillingly engage in a hiring tug of war with another welding company. In a bid to win welders, you might raise wages to a point where it’s too high for you to maintain.
High wages are fantastic for welders. But not so much for your company. Remember that the economy does not go up in a straight line. When the economy dips, the cost of running your business can go higher because of the wages you offered. Depending on the financial state of your company, this might not be sustainable. And you can end up having to let go of the welders you worked so hard to get.
Automation is the Key to Augmenting Welder Shortage
Welding automation with robotic welders is the key to augmenting the gap of finding experienced welders. With robotic welders, you can do more work with the welders that you already have. Robotic welders take over mundane, repetitive tasks. And your human welders can do more significant and complicated welding tasks.
The high-tech robotic welders can also help in attracting more young people to work for you. Although they are not interested in welding, the tech of robotic welding may be an attraction for them. And they can come on board as robot programmers and operators.
There are many benefits to welding automation. With robotic welding, your company can increase productivity since robots don’t tire. Welds are also more consistent since robot welders can do the same weld repeatedly without compromising quality. Robotic welders also improve your employee safety and well-being.
The Catch: Not all Automation Solutions are a Fit for your Business
It all looks so great, but there is a catch: industrial welding robots may not be the answer to your welder shortage problem. Yes, you heard right. For one thing, engineers built industrial robots with the automobile industry in mind. They are big and bulky and are made for high-volume production. They also require complex programming. And are set up to do only a single task.
Industrial robots can’t work with humans alongside because they are dangerous. Because of this, they are permanently housed in cages and can’t be moved. They also require a high capital investment to start with.
These reasons make the industrial robot less than ideal for your low volume, high mix environments of small to medium companies like yours.
Automate With A Collaborative Robot
If automation is the answer to the welder shortage, but industrial robots are not the right fit, what is? Welding with a collaborative robot is a viable option for businesses, especially those looking to automate their welding workflow. They work great with low volume, high mix environments like welding businesses.
Welding cobots are robotic arms with welding tools at the end. They have safety systems built in to be able to work alongside humans. Cobots are fast and repeatable. They are relatively light enough for your welders to move around the production floor.
In contrast to industrial robots, they are easily programmable. You don’t need a robotics degree to program them. Robotic welders like the Cobot Welder from Hirebotics can be taught by your welders using only an app. They can teach the Cobot Welder to weld anything by moving the cobot by hand to the different positions, using the Smart Puck. This process involves taking the robotic arm and going through the welding process without touching the screen.
Are you thinking of adding a cobot to your team and automating your welding workflow? Talk to our welding cobot experts!