Top 5 Costly Mistakes to Avoid When First Buying a Welding Robot
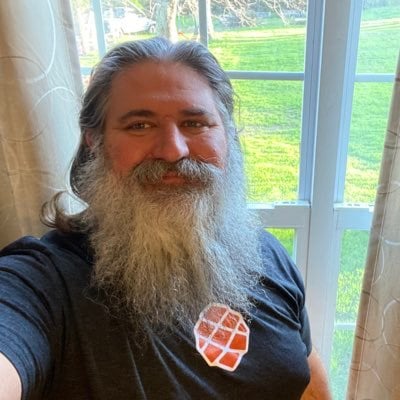
August 31, 2022
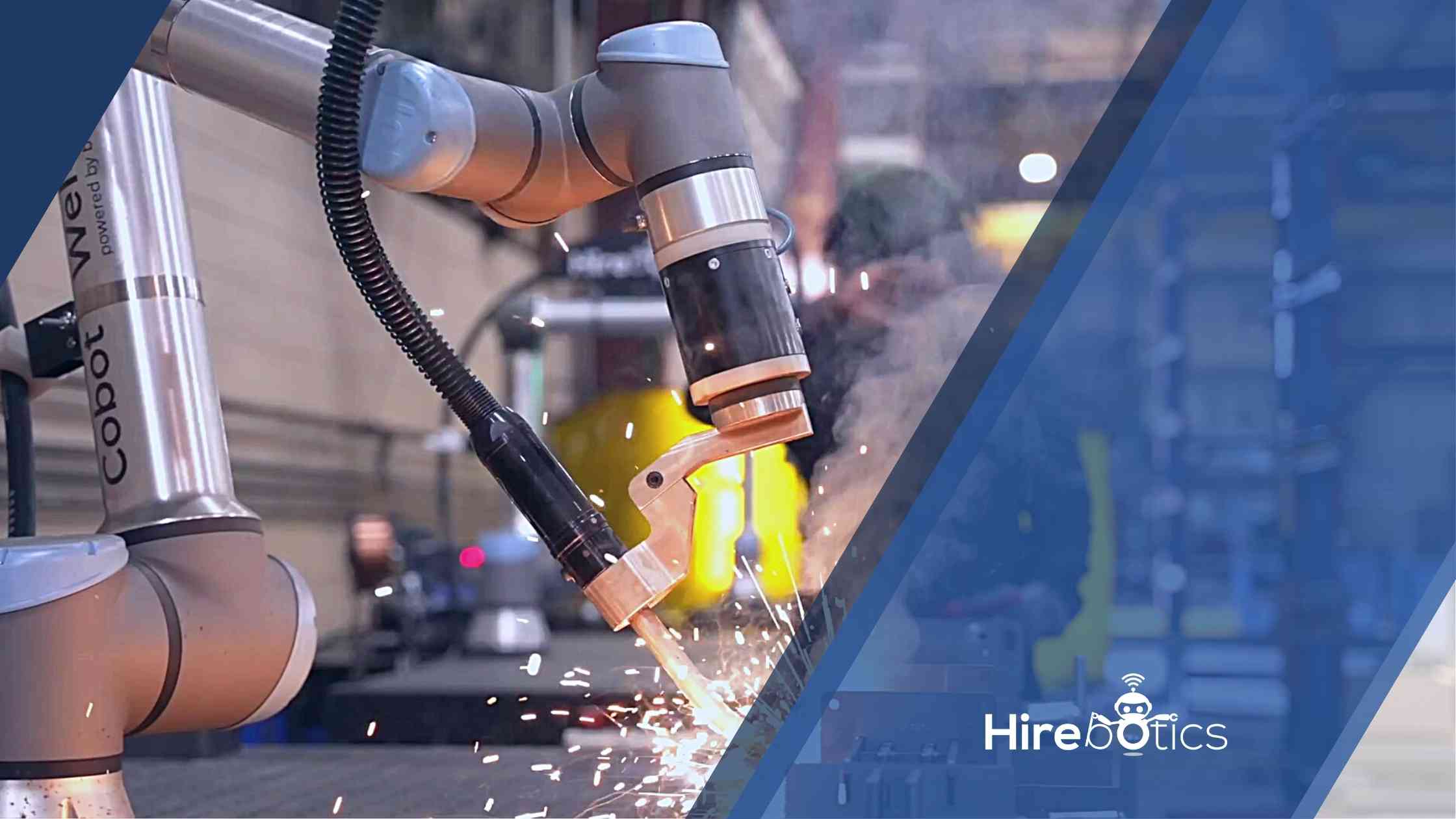
Thinking of making the transition to a robotic welder?
Have you ever thought about what could go wrong when investing in welding automation?
Robotic welders are increasingly popular in manufacturing environments and fabrication shops alike as businesses continue to struggle with an unprecedented welder labor shortage. Robot welding systems, particularly cobots, are becoming more affordable and easier to use than before.
However, the path towards welding automation using robotic welding systems should start with careful planning. Investing in robot welding can generate huge returns—or substantial, unexpected costs.
As we tackle some of the most common mistakes companies make, we will also share some points to consider when buying a welding robot.
Table of content:
- 1- Don’t Choose a Robotic Welder that Requires a Ph.D. to Program
- 2- Resist the Temptation to Build an Automation Team Right Off the Bat
- 3- Don’t Exclude Welders and Employees From your Welding Automation Project
- 4- Avoid Overdesigning your Robotic Welding Cell
- 5- Stay Away from Robotic Solutions that Call for Special Fixtures When Starting
- How to Choose a Welding Robot?
- Key Takeaways
1- Don’t Choose a Robotic Welder that Requires a Ph.D. to Program
Not all automated welding systems are created equally. Many industrial welding robots require sophisticated programming skills and robotics experts to set up and operate.
Moreover, complex automated welders lack flexibility. Manufacturers that specialize in high-mix, low-volume productions will undoubtedly experience lags in throughput due to endless programming and reprogramming.
Traditional robots also require weeks of training off-site for the employees, which is costly and forces them to be removed from daily production lines where they are desperately needed.
In order to eliminate the need for robotics specialists and programming, opt for a welding robot that requires little programming, which will definitively help onboard your current welding teams that may be concerned that their jobs are at risk.
2- Resist the Temptation to Build an Automation Team Right Off the Bat
An offshoot problem of acquiring an overly sophisticated automated welding system is needing skilled robotics professionals to integrate, program, operate, and carry out maintenance on the equipment. Robotics experts are even harder to find and retain than your standard welders.
When starting out in welding automation, avoid hiring a programming team. Don’t run off hiring multiple people right at the start; you may not know who you need and onboarding the wrong staff or too many employees can be a costly endeavor no business needs. Heck, that is why you are investing in robots in the first place!
Instead, invest in your top welders to upskill them so that they can work with the robotic welder. This will ensure that the robot can be up and running in no time, accelerate production, and boost welders’ job satisfaction.
An initial cobot welding project is a learning experience. Start slowly and have a robot “champion” internally help you spearhead your successful transition to robot welding!
3- Don’t Exclude Welders and Employees From your Welding Automation Project
Not including your welders and other team members in your welding automation plans is a surefire disaster. Remember, robots may be scary for your employees. As mentioned before, they are likely concerned that their jobs are on the line. They might even eye new technologies with suspicion, and flat-out refuse to work with them.
Robots need people to run them! That is why including staff in your project from the start and addressing the objections your welders have are musts. Employees will learn to like the productivity they can have when working with automated welders, particularly if the robotic welding solution you select allows them to work alongside the machine
Your welding team will also appreciate relegating mundane and repetitive tasks to the welding robot so that they can take on more complex and creative work.
4- Avoid Overdesigning your Robotic Welding Cell
As manufacturers and fabrication shops evolve towards automation, one of the major pitfalls is scope creep—or the continuous, uncontrolled growth of a project’s scope. Scope creep not only complicates the implementation of a robot welder but also ramps up costs, which in turn will prolong your return on investment.
Start your welding automation journey by properly defining a simple project aligned with your specific requirements. This will reduce the need for expensive machine integrations, automated tables, arch seam tracking technologies, etc.
5- Stay Away from Robotic Solutions that Call for Special Fixtures When Starting
When starting with welding robots, you might find yourself needing to design new and more complex welding fixtures. These are additional costs to consider when automating your welding workflows. Moreover, replacing jigs can be technically challenging, especially when a manufacturer or fabrication shop produces a high number of different welded parts.
Some collaborative welding robots can be integrated using a business’ existing assets; welding teams can therefore maintain or even increase productivity by reusing the manual jigs they currently have with a welding cobot.
How to Choose a Welding Robot?
These are just some of the points to consider when buying a welding robot. However, other factors come into play when you select a robot welding system.
Steps | How to Choose a Welding Robot |
1 | The number-one question you need to ask yourself is what do you want your automated welder to do? What types of welding applications do you envision your welding robot carrying out? Would you prefer an industrial robot or cobot welder to operate with your welders? |
2 | Then, take a look at the specs for payloads, reliability and durability in harsh production environments, as all of these features can affect welding performance. |
3 | Inquire about how the robotic welding systems have functionalities in place to mitigate the risks associated with welding. |
4 | Naturally, you will want to explore how much a robotic welder costs, including training and support fees. Be sure to discuss all associated costs so that the total cost of ownership of your welding robot is kept in check. |
5 | Above all, think about the partner you choose when buying a welding cobot. Are they consistently innovative? Do they truly understand the intricacies of welding? Do they work with other best-in-class partners to complement their technologies? Investing in an automated welding system necessitates the right partner to make your robot integration project as successful as possible in the short and long run. |
Key Takeaways on Points to Consider When Buying a Welding Robot
Manufacturers and fabrication shops are likely to fail in their integration of welding robots if they ignore these points to consider when buying a welding robot.
In a nutshell, with robotics for welding, simplicity trumps complexity. Involving your team at the start of the project is critical. Finally, partnering with the right vendor of robotic welding machines that puts your business and production priorities first will enable you to achieve high paybacks in as little as a year.
Want a stress-free way to implement your first robotic welder? Talk with one of our experts today.