How Welding Cobots Can Drive Cost Savings for Metal Fabricators
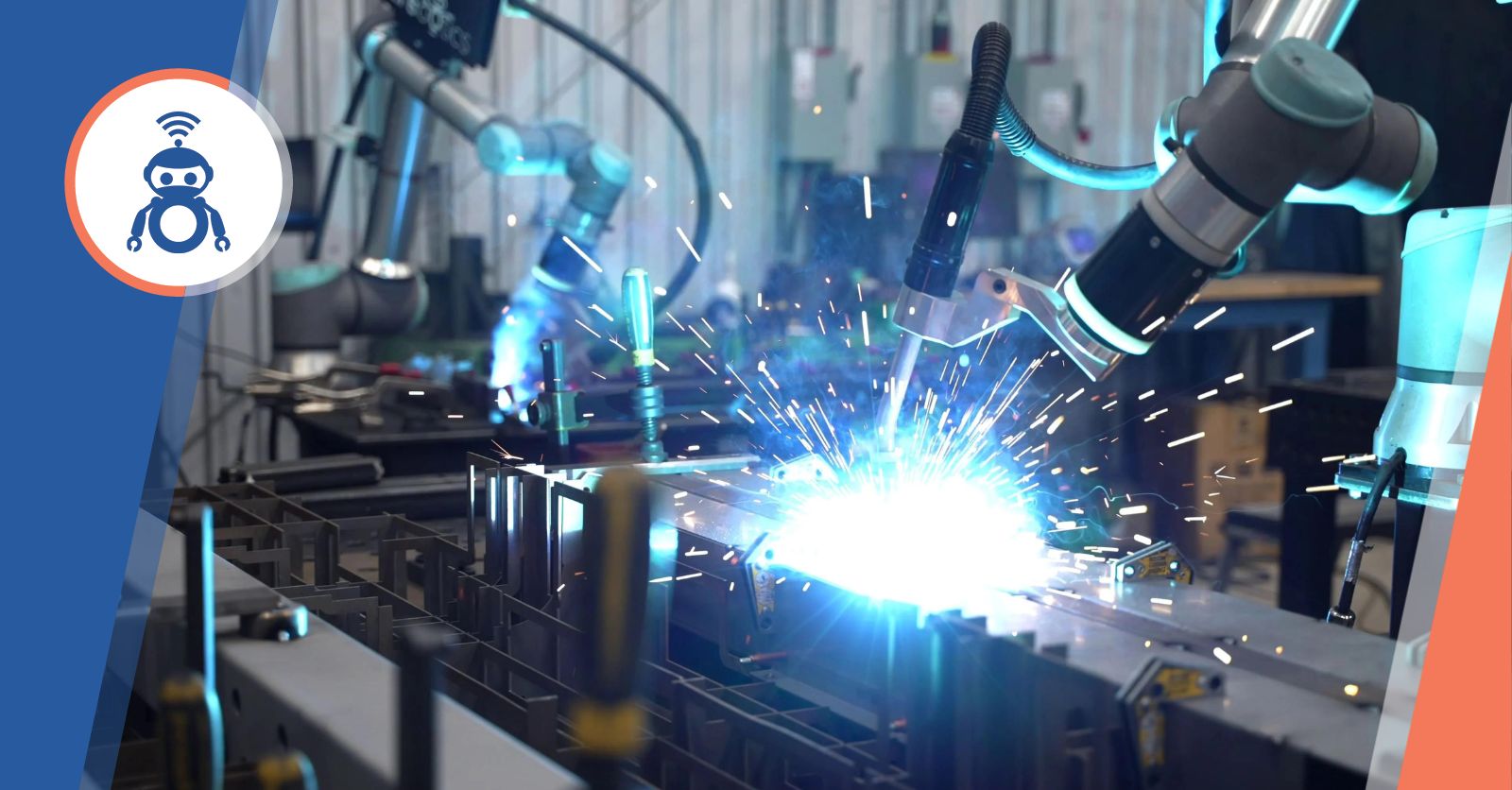
Increased Production Capacity and Speed
Welding robots offer a tremendous amount of productivity improvements for manufacturers. These improvements come in the form of:
- Reliable production scheduling
- Greater uptime
- Increased production capacity
- More output
Most manufacturers have heard of these benefits before. So how does it look in reality?
- Robots enable manufacturers to run more reliable production, empowering them to be more confident about their scheduling and ability to meet orders on time.
- Welding robots can run continuous production if the weld cell remains fed—some manufacturers even achieve lights-out production—which isn’t the case for manual processes.
- Manufacturers leveraging robots are less prone to the cost of not producing—or the opportunity cost of foregone production opportunities lost to a lack of capacity.
- Welding robots can move directly from completing a part to beginning the next part, which means they’re always maximizing for metrics like arc-on time.
- Welding cobots will outperform welders over time thanks to the aforementioned capabilities and superior cycle time, enabling manufacturers to deliver more orders faster and more reliably than their competitors.
Lower Defect Rates and Rework Costs
Defective welds negatively impact manufacturing processes in several ways:
- Wasted material
- Backing up production
- Increased labor costs
- Field failures
Some defects can be so severe that the welder must scrap the material. Scrapping parts wastes both material and labor costs. When welders can salvage the material, the production process must be backed up to make time to rework the part. This decision hurts throughput and efficiency but also increases the cost to produce that part due to the increased labor and consumables applied to the rework.
Weld defects aren’t always caught during the QA process. In these cases, field failures can occur. These failures can be detrimental to manufacturers in a few ways:
- Cost to replace or repair the part
- Liability costs
- Impact on customers’ opinion of the manufacturer’s quality
The precision and consistency of welding cobots can reduce defect rates and the associated rework costs. As a result, manufacturers can save time and money on quality control, product repair or replacement, liability costs, and maintain high customer opinion by minimizing errors and ensuring high-quality welds.
Improved Worker Safety
Welding is a hazardous occupation. Among other risks, OSHA lists the hazards of welding to include:
- Chromium exposure
- Eye damage
- Fire hazards
- Noise exposure
- Electrocution
- Toxic fume inhalation
Companies are responsible for providing a safe working environment for their employees. Manufacturers can enhance workplace safety by delegating hazardous welding tasks to cobots and reduce the risk of accidents, injuries, and associated costs. This improves worker well-being and contributes to a more productive and cost-effective work environment.
How Hirebotics Has Helped Manufacturers Address Welding Challenges
Understanding the potential cost savings of welding cobots, we have observed real business impacts on manufacturers like you. They chose to invest in collaborative welding robots, such as Hirebotics' Cobot Welder and witnessed firsthand the benefits in profitability and cost reduction.
Let’s explore how Hirebotics' welding cobots have helped businesses tackle their welding challenges head-on.
Increased Profits at Vortex Companies
Vortex Companies, a Kansas-based firm specializing in the design and steel-manufactured components for dry bulk solids' transportation and flow control, faced the challenge of a lack of experienced welders. In response, they adopted Hirebotics' Cobot Welder, an automated welding solution known for its ease of setup and use by operators with varying skill levels, requiring little to no programming.
Since implementing the Cobot Welder, Vortex Companies has experienced significant benefits.
“Since implementing the cobot, we have been able to take hundreds more parts in a much quicker timeframe than our previous robots. We have had fewer overtime hours with hand welding as we have been able to assign more jobs to Cobot Welder. We’ve increased our profits just by cutting out on overtime.”
Additionally, monotonous tasks can now be delegated to the cobot, allowing manual welders to focus on more complex projects and reducing their work weeks from 55 hours to a more balanced 40-hour week without any job losses. Vortex created three new positions since the Cobot Welder's implementation.
The cobot has also drastically reduced errors, particularly in repetitive tasks, thanks to fixturing. Vortex Companies has seen improved efficiency, boosted production capacity, reduced errors, and happier manual welders due to adopting the Cobot Welder.
You can read the full Vortex Companies success story here.
Advanta Southeast Finds a 400% Increase in Throughput
Advanta Southeast LLC, a South Carolina-based industrial metal fabrication company, faced challenges in its welding operations due to:
- A challenging labor market
- The global pandemic
- Increased competition for skilled welders
Seeking a solution to mitigate these issues, they implemented Hirebotics' Cobot Welder, which was new to the company but offered ease of setup and use.
Within two weeks, Advanta Southeast received their Cobot Welder unit and was up and running on the same day. The team found it easy to set up and required less than a day of training for the welding team. Initially hesitant, the welders quickly adapted to the Cobot Welder and appreciated its ease of use and ability to improve their efficiency.
The welding team could work on manual jobs while the cobot handled other tasks, resulting in higher quality and more consistent output.
One key advantage of the Cobot Welder for Advanta Southeast was the lack of programming required and the ability to track various metrics through the accompanying app. These features allowed Advanta Southeast to make better operational decisions. The company experienced such success with the initial unit that they acquired more Cobot Welders for their South Carolina plant and the Advanta Industries facility in Michigan.
As a result, they have increased output by 400%, enabling them to secure contracts they previously could not pursue.
You can read the full Advanta Industries success story here.
Maximizing the Value of Your Investment in Welding Cobots
Successful manufacturers recognize the importance of cost savings when investing in welding cobots, as it is a key financial aspect that contributes to maximizing their investment. Talking about maximizing the investment, businesses can also improve financial outcomes by implementing effective strategies to optimize cobot implementation.
These strategies enable businesses to fully harness the potential of this cutting-edge technology, driving operational efficiency and maintaining a competitive edge in the market.
Understanding ROI
Return on investment (ROI) is a critical metric that measures the profitability of a manufacturer’s investment. Manufacturers must understand the nuances of ROI calculations to go beyond equipment cost and revenue.
Calculating Total Cost
The cost of a welding robot typically ranges from $80,000 to $150,000. However, there are many more equipment costs to consider.
- Robot fixturing
- Jigs
- Installation fees
- Programming fees
- Peripherals
- Safety equipment
Manufacturers can protect themselves from some of these costs by opting for a welding cobot where possible. Cobots require less safety equipment than standard robots. Additionally, some cobots come with no-code, app-based interfaces, which enable manufacturers to save on expensive programming costs.
Labor Considerations
Manufacturers’ greatest cost tends to be their labor. It’s critical to calculate the labor cost to run the same production schedule and output capacity as the robot to understand the potential savings.
The cobot welder’s ability to produce consistently and efficiently has a massive impact on ROI.
Maintenance and Operations
While cobots require minimal maintenance, you might need to develop an automation team to manage tasks such as:
- Programming
- System/process design
- Maintenance
- Repair tasks
These are additional costs to factor into your ROI calculation. Manufacturers leveraging no-code systems can save significantly on programming costs. Additionally, many operators and welders transition into automation team members thanks to their valuable experience and welding domain knowledge.
Intangible Benefits
There are several benefits from automating welding processes that don't have a hard monetary value but greatly impact ROI. These include:
- Increased production quality
- Improved employee safety and health
- Increased efficiency
- Freeing experienced welders from monotonous tasks,
- More return customers due to faster delivery times and improved quality
- Increased competitiveness
While some of these benefits are hard to measure, they’re real advantages that should be considered as part of the overall package when exploring a welding automation system.
By truly understanding all aspects of the ROI of a welding cobot, manufacturers can set clear expectations and make the most informed decision to begin automating their welding processes.
Strategies for Optimizing Your Welding Cobot System for Maximum ROI
First, identify the right welding jobs for your cobot within your production process. Focus on welding processes that are:
- High-volume
- Labor intensive
- Hazardous for human workers
Second, invest in proper training for your employees. Ensuring that your workforce is well-versed in operating, programming, and maintaining welding cobots will result in smoother implementation and more efficient utilization of the technology.
App-based cobots, like Hirebotics’ Cobot Welder, allow manufacturers to save time and training costs by offering a setup interface amenable to operators with little to no programming experience. No extensive training is required for these systems!
Next, continuously evaluate and refine your welding processes. Being able to get data from welding production can provide valuable insights into production efficiency and quality. Analyzing this data can help identify areas for improvement, enabling you to make informed decisions and optimize your processes further.
Lastly, consider integrating your welding cobots with other automation solutions in your facility, such as material handling systems or inspection equipment. A seamless integration of automation technologies can increase efficiency and cost savings throughout your production process, ultimately boosting your ROI further.
By adopting these strategies, manufacturers can ensure that their investment in welding cobots delivers maximum value and contributes to long-term operational success.
Final Thoughts on Cost Savings with Welding Cobots
Welding cobots offer numerous cost-saving benefits to manufacturers, making them an attractive solution for businesses seeking to improve operational efficiency, increase productivity, and reduce expenses. These benefits include:
- Lower labor costs
- Increased production capacity
- Increased production speed
- Lower defect rates and rework costs
- Improved worker safety.
By leveraging welding cobots, manufacturers can successfully navigate the challenges of labor shortages, economic uncertainties, and the increasingly competitive global market.
The case studies presented in this article highlight the tangible advantages that welding cobots have provided to various manufacturing companies across different industries. By addressing the implementation challenges and maximizing the value of their investment, these businesses have reaped the rewards of increased productivity, reduced costs, and enhanced competitiveness thanks to Hirebotics’ Cobot Welder.
Manufacturers looking to secure long-term success and maintain a competitive edge should seriously consider investing in welding cobots. As technology evolves and reshapes the manufacturing landscape, early adoption of these advanced automation solutions will position businesses for future growth, flexibility, and competitiveness.
Hirebotics is experienced in aiding manufacturers reach their business goals through automation. Are you wondering if our Cobot Welder is a good fit for your welding operation? Contact us today to schedule a demo and learn more.