Complete Guide to Universal Robots Welding
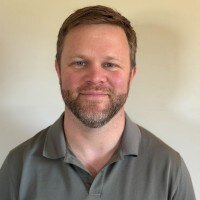
May 14, 2024
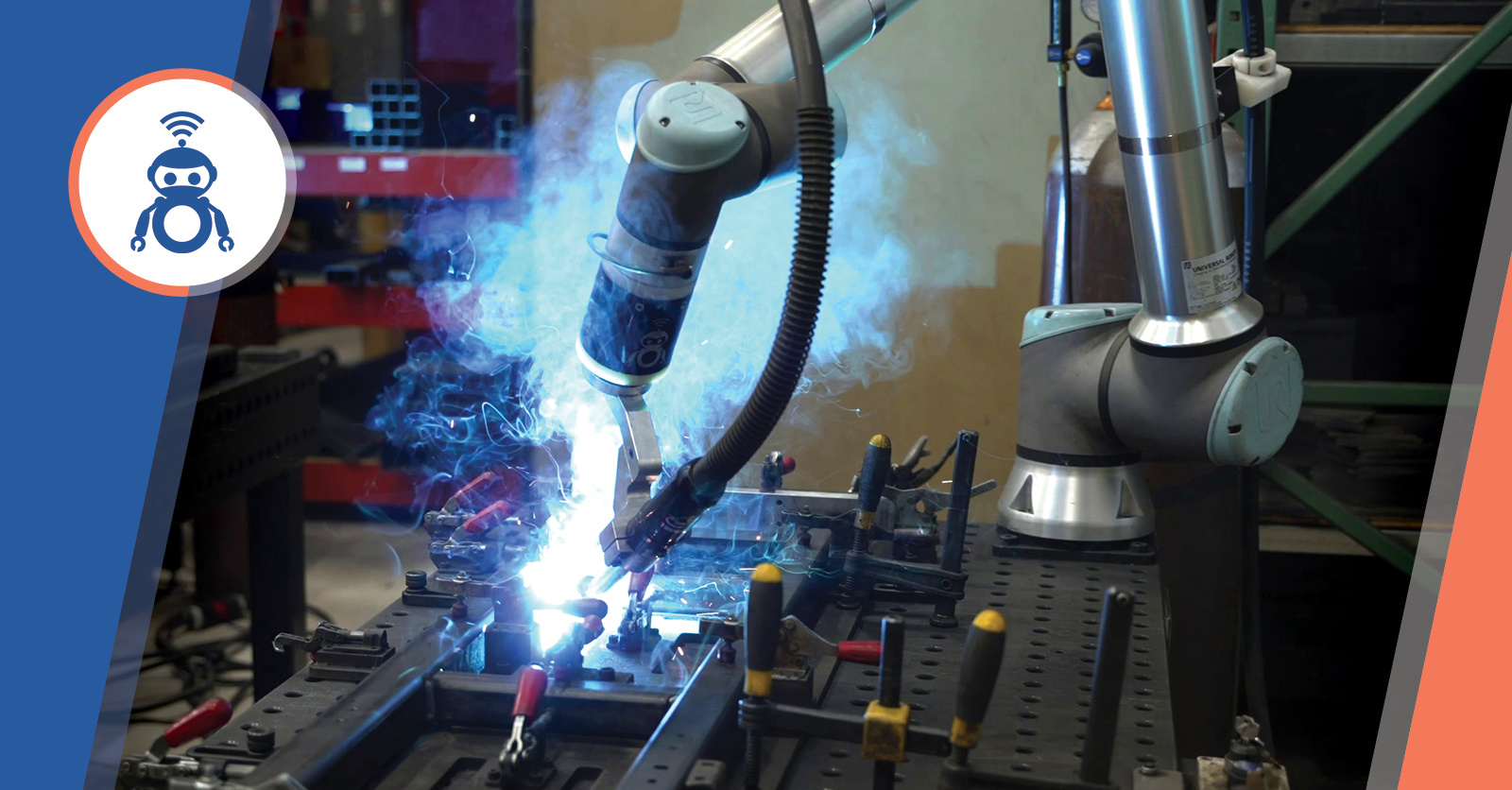
If you're in the metal fabrication, machining, or welding business, you've probably heard about Universal Robots (UR) and their versatile collaborative robots.
You might be wondering why fabricators are choosing Universal Robots' welding solutions over other brands or what sets them apart for welding.
In this discussion, we will explore how UR is different from its competitors, the various types of UR welding cobots, and their pros and cons, and help you determine the best option for your specific application.
Who Is Universal Robots?
In 2005, Universal Robots introduced to the industry the concept of a collaborative robot. Breaking from the paradigm of traditional industrial robots, Universal Robots and their cobot sought to make robots human-safe, simple to program, and more flexible than traditional industrial robots. The goal of Universal Robots was to find people working alongside robots rather than working like robots. Despite the rapid expansion of the cobot sector in the ensuing years, Universal Robots has maintained its market share and innovated over 5 generations from the original UR robot.
Universal Robots mission is clear: “Automation for anyone, anywhere”. Innovating with this principle in mind, Universal Robots makes their technology accessible to companies across various industries and sector types, including welding.
Welding and fabrication shops find their products especially attractive for their reliability, adaptability, and seamless integration into existing operations. With over 75,000 units sold, UR cobots are known for their consistent performance, improving productivity while upholding high safety and quality standards.
Why UR Cobots are Well Suited for Welding Applications
Universal Robots cobots are a great fit for welding, with a strong track record and reliable performance in harsh conditions. Here’s why they stand out:
- Reliability in dirty, hot production environments: Designed to endure the harsh conditions of welding areas, UR cobots maintain high performance in environments that are typically challenging for machinery. Their proven track record and ability to consistently perform in these environments minimize downtime and improve production reliability.
- Ease of Use: One of the pillars of Universal Robots value proposition is ease of programming. Much of the Research and Development efforts by Universal Robots has involved creating an interface that is intuitive and simple to learn. While scripting in the UR robot is made possible, new entrants to robotics can use the Graphical User Interface (GUI) to program the UR robot for simple or even more complex applications.
- Safety: Universal Robots are collaborative robots that fall inside the category of “power and force limiting robots.” This means UR robots are human-safe. If a person impedes the path of a UR robot and is impacted by the robot, the robot will stop its path of motion. For welding, this means in most applications the UR robot can operate without the need for fencing and guarding. The benefit is a reduction in deployment cost and the saving of floor space.. Further, it permits human-machine collaboration, allowing operators to load parts while the robot is working.
- UR+ Platform: Universal Robots boasts one of the more open platforms of any robot company. The UR+ platform allows developers of peripheral components, application types, or software packages to build on top of the UR platform. This means that original equipment manufacturers (OEMs) can offer custom software specifically for welding. This also allows developers to integrate other types of equipment to the UR robot in a simple and straightforward fashion.
Best Universal Robot Models for Welding
Universal Robots offers a diverse range of collaborative robots tailored to meet various needs for any application. The 3 mentioned below are recommended for welding primarily because of their long reach.
Here’s a closer look at each UR model most recommended for welding applications.
- UR10e: As the most popular model, the UR10e is known for its flexibility and ability to integrate into a wide range of welding applications. It has great reach for small to medium size workstations, parts, assemblies and a good payload for the torch and end-of-arm welding systems.
- Reach: 1300 mm / 51.2 in
- Payload: 12.5 kg / 27.55 lbs - UR20: The UR20 is designed with 18 inches more reach than the UR10e. This extended reach and a new coordinated motion feature allow you to work on larger parts and perform longer welds without having to move or reposition the part or set it up again—this saves valuable cycle time compared to manual welding.
- Reach: 1750 mm / 68.9 in
- Payload: 20 kg / 44.1 lbs - UR30 (New): The newest addition, the UR30, offers a heavy payload capacity in a compact design. Because of the welder's added weight, it is an excellent choice for spot welding applications.
- Reach: 1300 mm / 51.2 in
- Payload: 30 kg / 66.13 lbs
Components of a Welding Cobot Cell
It's important to note that Universal Robots only provides the robotic arm. You'll need additional components beyond the arm itself for a fully integrated welding cell.
Here’s an overview of the common elements of a UR welding cobot cell:
Welding Power Source and Feeder
The welding power source and wire feeder are critical components of a cobot welding system. Depending on the process, brands like Miller, ESAB, or else might be integrated with the UR robot to offer a turnkey welding solution.
Welding Torch
The welding torch is designed to meet the specific demands of different welding processes and materials being welded. The choice of torch—whether air-cooled, water-cooled, or featuring a push-pull system—varies based on many factors. Its important to also consider the weight of the torch as this will impact the payload calculation of the UR robot
Welding Cart or Table
Most cobot welding solutions feature the robot mounted on a cart or a table. This allows the robot to be fix mounted to the table in close proximity to the parts it will be welding. The table also serves as a place for fixturing parts using clamps or other placement mechanisms. Like with any robotic application, consistency of part placement is paramount. This setup can also conveniently house all the necessary welding equipment in a compact, organized package.
Programming Software
Universal Robots welding solutions often involve custom programming interfaces designed by third parties. Custom interfaces, which are enabled by the UR+ platform, are beneficial when programming the UR robot for specific types of applications like welding.
The Hirebotics Beacon Difference
While Universal Robots makes an interface that is relatively simple for general-purpose applications, Hirebotics took the ease-of-use concept a step further and created custom software specifically for welding. In fact, the majority of Hirebotics’ customer base finds that welders, not robot programmers, program the Hirebotics Cobot Welder.
Hirebotics software, Beacon, lives on a device that everyone is familiar with: an iPhone, an iPad, an Android, or a Windows device. The software interacts with a smart puck which is attached to the flange of the UR robot. The puck has two buttons, one to freedrive the robot (i.e. move with your own hand) and one to record points along a linear, radial, or rotary path. The end result of this elegant design is unmatched accessibility, where anyone, regardless of experience, can create a welding program.
How Much Do Welding Cobots Cost?
The cost of a welding cobot system can vary significantly based on several factors. These systems typically range from $80,000 USD to over $150,000 USD. The final cost depends on the equipment selected, the complexity of the tasks to be automated, and the time required for installation.Factors Influencing Cost
- Equipment selection: The choice of the cobot model and the associated welding equipment (such as welding guns, tables, and software) significantly impacts the price. Different models and setups are tailored to various applications, and higher-specification equipment generally comes with a higher price tag.
- Task complexity: The complexity of the tasks the cobot is expected to perform also affects the cost. More complex applications may require advanced set-up, seam tracking, additional programming, and superior precision components, all of which add to the overall expense.
- Installation time: The time it takes to install and fully integrate a cobot into your existing systems can vary. Longer installation times involve more labor and can increase the overall cost, especially if extensive customization or integration with existing machinery is required.
How Universal Robots and Hirebotics Work Together
Hirebotics and Universal Robots collaborate, with Hirebotics leveraging UR's advanced robotic technology on different levels. Here’s how their collaboration works.
Hirebotics as a Universal Robots OEM
Hirebotics is an original equipment manufacturer (OEM) that integrates Universal Robots’ robotic arms into its own product offerings. The standard version of the Cobot Welder uses the UR10e robot arm from Universal Robots.
It's also worth noting that the new UR20 version is particularly appealing to fabricators due to its additional reach, improving its capability to handle larger or more complex welding tasks.
UR+ Partnership
Hirebotics is also a UR+ approved partner. The UR+ program involves a network of companies, referred to as creators, who develop specialized products that complement and enhance the functionality of UR cobots.
These products range from complete solution packages and application kits to individual components like grippers, cameras, and software.
Integration and Compatibility
All products developed under the UR+ partnership, including those by Hirebotics, undergo rigorous testing to ensure they are fully compatible with Universal Robots cobots.
This testing process guarantees that the integrated products uphold UR’s standards for fast setup, flexible deployment, easy programming, collaborative safety, and reliability.
This guarantees that when customers select a UR+ certified product such as the Hirebotics Cobot Welder, they are getting a solution that seamlessly integrates with UR technology.
Why Consider Hirebotics’ Cobot Welder
Hirebotics' Cobot Welder stands out with its easy-to-use Beacon app and easy-to-understand welding language. With a few simple steps and no programming jargon, any welder can manually guide the cobot to weld points with the teach button.
It is perfect for small- to medium-sized manufacturers dealing with skilled labor shortages or a high mix, low volume ratio of parts, and looking to boost their production capacity.
The Cobot Welder from Hirebotics simplifies the transition to automation. It offers consistent, repeatable welding results and empowers your current team to accomplish more with less.
Change the Way You Weld with Hirebotics Cobot Welder
The Hirebotics Cobot Welder offers a straightforward and effective way to improve your welding operations without the complexity often associated with automation. Its user-friendly design ensures that your team can easily adapt and thrive without specialized training.
If you're interested in seeing the Hirebotics Cobot Welder in action or if you want to learn more about how it can benefit your operations, please contact us for a free demo. We're excited to show you what this tool can do for your business.