Increase Welding Robot ROI: Boost Production and Profits
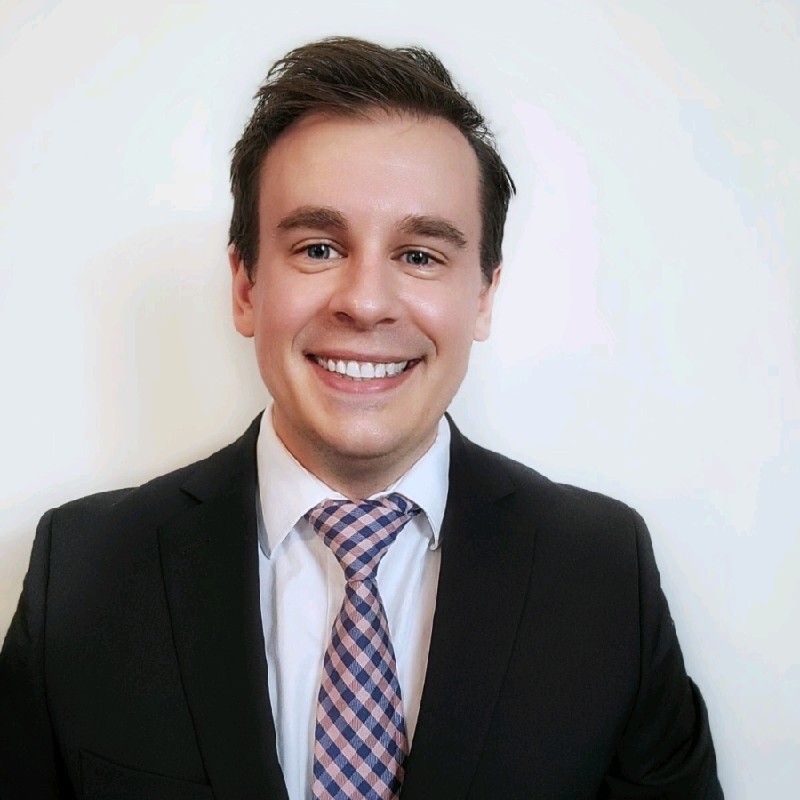
March 21, 2024
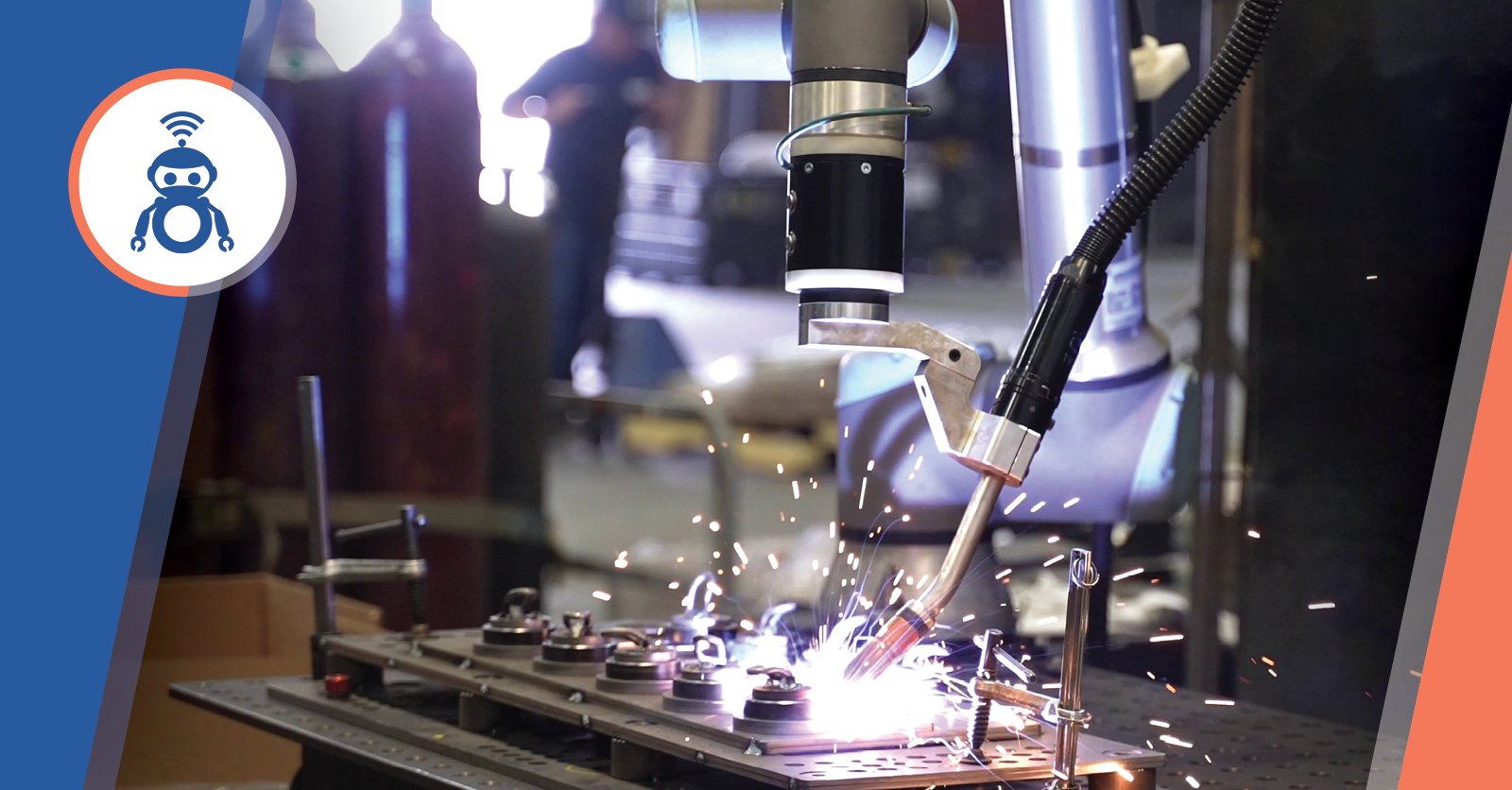
Have you been thinking about adding automation to your welding processes but have a few concerns? For a lot of shop owners, especially those who work with high-mix low-volume, this can seem like a big step. Why? Because implementing and learning how to program a welding robot can be complicated and time-consuming.
That's where Hirebotics' Beacon teaching App can help, turning what might seem like an uphill battle into a simple, straightforward process.
The Beacon teaching app eases the transition into automation, and ensures your production is efficient, and your workflow is seamless. Let’s take a closer look at how cobot welding powered by Beacon can make it easier for you to add automation to your metal fabrication processes.
In this article, let’s discuss:
- Automation Myths
- High-Mix, Low-Volume Production Challenges
- Welding with Beacon: 5 Ways to Increase ROI
- Simplifying Cobot ROI
- Hirebotics' Cobot Solutions for Metal Fabrication
- FAQ
Automation Myths
First, let's tackle some myths that might be holding you back from considering automation:
- Too pricey: Yes, automation involves upfront costs, but it's not as out of reach as you might think. The efficiencies gained often lead to savings on labor and materials and a boost in product quality, which can quickly offset the initial investment.
- Slow return on investment: Taking on a new welding system can seem like a big undertaking, with worries about the time and effort it will take to get everything up and running, not to mention getting the team up to speed. However, many shops find that automation leads to significant and quick returns thanks to higher throughput, reduced waste, and the cobots ability to easily adapt to new tasks.
Clearing up these automation myths opens the door to more possibilities. Now, let's pivot to explore how high-mix, low-volume production brings its own unique challenges, and why understanding these is key to making automation work for you.
High-Mix, Low-Volume Production Challenges
High-mix, low-volume production also presents a unique set of challenges.
- The demand for variety: The diversity of projects in a HMLV shop requires constant adjustments in production schedules, setups, and inventory management. This can make it difficult to maintain efficiency while meeting the needs of a wide range of customers.
- Complexity in quality control: Each product may come with its own set of specifications and quality standards, requiring meticulous attention to detail and a high level of adaptability in quality control processes.
- Flexibility: Traditional automation is often designed with large-scale, repetitive tasks in mind, which makes them ill-suited for the ever-changing demands of HMLV production. This lack of flexibility can be a major hurdle, as the ability to swiftly adapt to new and changing metal fabrication tasks is crucial for staying competitive and meeting customer expectations.
Let's explore how Beacon can streamline high-mix, low-volume production, increase ROI, and make it simpler for your business to adapt and thrive.
Welding with Beacon: 5 Ways to Increase ROI
Beacon is a thoughtfully designed teaching App aimed at mid-size shop owners who aren’t sold on the initial investment and operational complexity of traditional robotic welding.
Here's how Beacon addresses your concerns and delivers on its promise to increase ROI:
1. Simplicity in Operation
The days of needing specialized knowledge to program welding robots are gone. Beacon’s user-friendly interface, accessible via a smartphone or tablet, drastically reduces the learning curve. This ease of use means your team can get up to speed quickly, ensuring the transition to automation is quick and easy.
“The training was extremely simple, and the cobot operation was easy to learn. It was fun, actually,” says Power Glover, a Robotic Weld Tech at Vortex Companies.
2. Operational Flexibility
Thanks to Beacon's remote programming capabilities, making adjustments or troubleshooting doesn't require an on-site specialist. You can manage operations right in the app, reducing downtime and keeping the production line moving.
3. Adaptable for High-Mix, Low-Volume
Beacon enables rapid reprogramming and redeployment of cobot welders to accommodate changing production needs or new tasks. This agility allows businesses to quickly respond to market demands and optimize production efficiency.
4. Direct Cost Savings
The investment in Beacon exceeds traditional cost-saving. Beacon reduces both upfront and ongoing costs because it eliminates the need for expensive teach pendants and program training. The quicker setup and integration times further cut labor costs, contributing to a faster ROI.
5. Speed, Quality, and Throughput
Beacon produces high-quality welding at a pace that manual processes can't match. This means you can deliver better products faster, increasing your throughput and, ultimately, your bottom line.
“If a hand weld took us 25 minutes in the past, it now takes us 5 minutes. If it’s a 5-minute part, it takes us 37 seconds”, says Ryan Lockhard from Spectrum Metalcraft
Simplifying Cobot ROI
“How quickly can a cobot pay for itself ?” you might wonder. Well, let’s break it down with an example. Let’s say you're you're paying a skilled welder $30 per hour, which includes regular overtime.
- Welder's Weekly Earnings: With 5 hours of overtime each week, paid at time-and-a-half, your welder's total earnings would be approximately $1,425 every week.
- Annual Cost: Over the course of a year, accounting for 52 weeks of work, this amounts to an annual expenditure of $74,100 on wages alone for this welder.
Now, let's compare this to investing in a cobot with a price tag of $150,000 or less.
Given the annual cost of employing the welder, the $150,000 investment in the cobot would effectively 'pay for itself' in just over 2 years. This calculation is based on the savings from automating tasks that the welder would otherwise handle, including those overtime hours.
It’s interesting to note that while a skilled welder or welding technician is needed to oversee the weld quality of multiple cobots, one cobot can match the efficiency and output of 2-3 welders for simpler tasks.
For more info on Cobot ROI check out our “Tips To Calculate The ROI of Your First Welding Cobot” article.
Hirebotics' Cobot Solutions for Metal Fabrication
High-mix, low-volume production is a challenge for many mid-size shops. Balancing the diverse demands of small orders without sacrificing efficiency or profitability can feel like an uphill battle.
It's a challenge that requires a smart, adaptable solution.
Hirebotics’ Beacon app offers a simple automated welding solution tailored to the HMLV environment. It lowers operational costs, improves weld quality, and allows you to quickly adapt when new orders come in.
Ready to take your welding shop to the next level with Beacon? Schedule a demo and see how we can help you integrate automation into your operations efficiently, effectively, and securely.
FAQ
What is the most common problem with robotic welding applications?
The most common issue is lack of flexibility. Many robotic welding systems are designed for high-volume, repetitive tasks and struggle to adapt to the variety and customization required in high-mix, low-volume production settings. This is where Beacon by Hirebotics shines, offering a solution that's as adaptable as it is efficient, perfectly suited for a wide range of welding tasks.
Are robotic welders worth it?
Absolutely. Robotic welders can significantly increase efficiency, improve weld quality, and reduce waste, leading to a quick return on investment (ROI). With user-friendly and flexible solutions like Cobot welder powered by Beacon, even smaller shops can benefit from the cost savings and productivity boosts that robotic welders provide.
Will robots replace welders?
While automation is transforming how welding tasks are approached, they're not here to replace welders but to augment their skills. Tools like Beacon offer numerous benefits by optimizing welding tasks and allowing welders to focus on more complex, high-value aspects of their work. This relationship between welder and machine maximizes the skills of the welding team, rather than rendering them obsolete.
Can Beacon integrate with my existing welding setups?
Cobot solutions powered by Beacon are designed for easy integration with a variety of welding setups. Its user-friendly interface and flexible programming make it a seamless addition to most shops, enhancing your current operations without requiring extensive overhauls.