Robotic MIG Welding Speed: Why It Matters And How To Maximize It
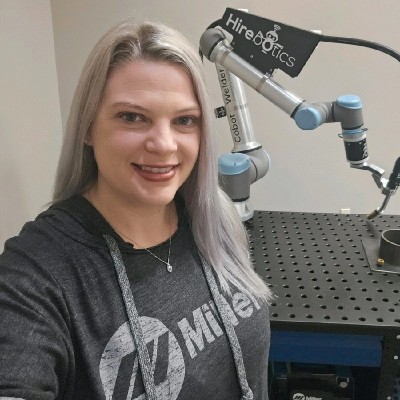
May 27, 2024
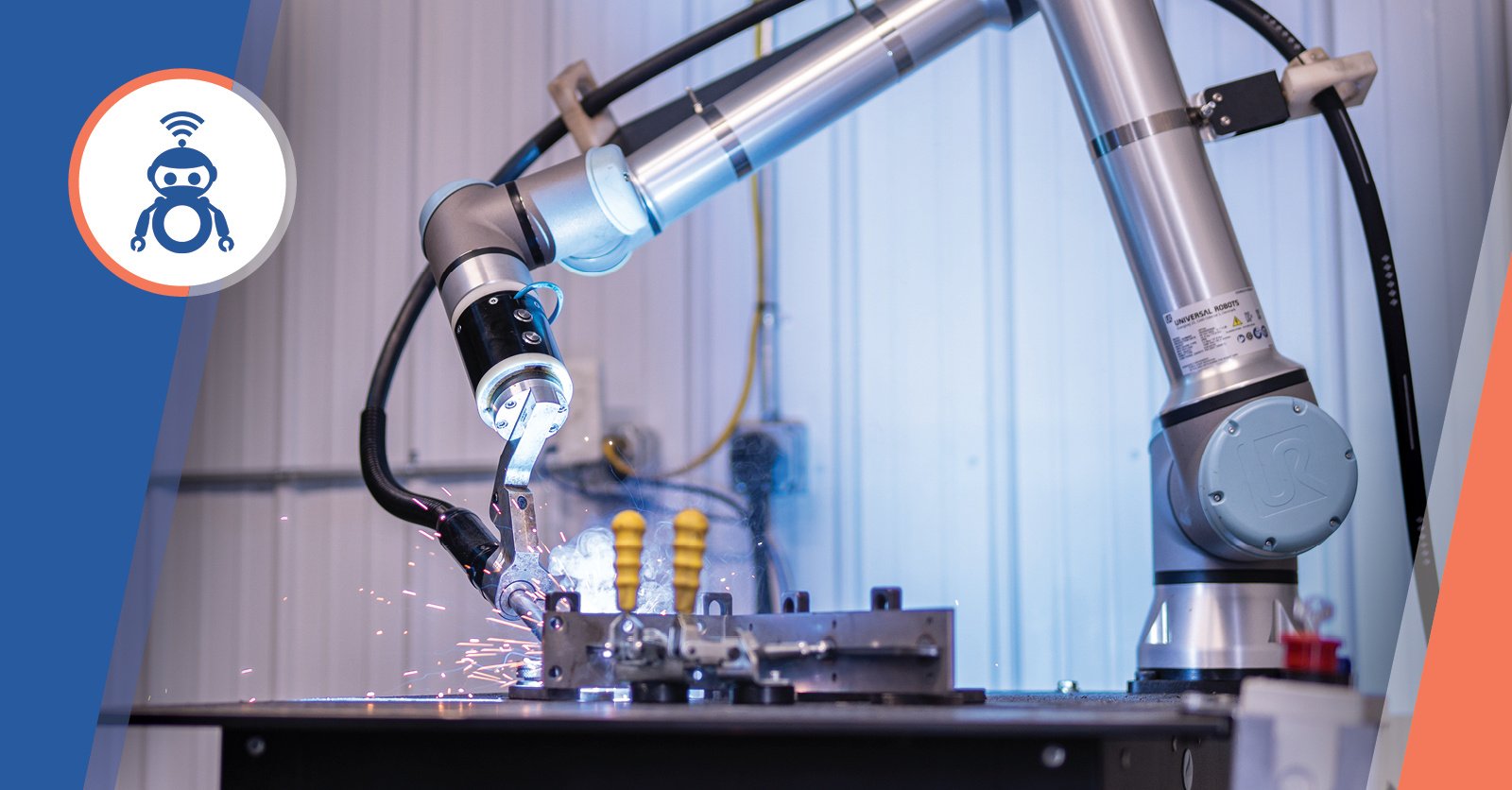
Welding speed is often the most critical component for production profitability and weld quality. Going too fast or too slow can impact your bottom line and position in the market. While robotic GMAW (MIG) speed may seem like just another parameter to set, its implications echo all the way to the end user.
If you properly leverage robotic welding speed, you can massively improve your welding capacity, quality, and ROI, giving you an edge in the market you never thought possible.
How Fast Can You Weld With a MIG Robot?
The maximum speed you can use depends on the robot type and make, material type, thickness, and some weld factors, like width-to-depth ratio. Generally, you’ll want to weld as fast as possible most of the time.
For some applications, getting 40 inches per minute (IPM) can be considered fast, while for others, you can push way faster than that. The best example of speed variability would be thick (>5/8") vs thin steel (<1/4”) welding. Thickness can limit the speed quite a bit, but a robot will almost always weld much faster than a manual welder.
As long as you achieve adequate penetration, a weld profile, and other customer-specified specs, you can keep pushing the speed. The faster you weld, the higher the productivity.
Are All MIG Welding Robots The Same?
There are two types of welding robots you can use: traditional robots and collaborative robots. Welding and operational speeds, as well as programming environments, vary between these two types of robots.
- Traditional robots move so fast that they must be in a safety cage, or they can harm the operator. Their welding speed varies depending on the model and make. However, they aren’t designed for flexible automation. Traditional robotics works great for high-volume, serial production, like car manufacturing. They typically require a skilled robotic technician and are time-intensive to program. You can spend anywhere from a day to several weeks programming a welding batch. So, they usually aren’t helpful for small to medium-sized shops with high part volatility.
- Collaborative robots, or Cobots, move slower than traditional robots for safety reasons but still weld far faster than humans. They can’t harm the operator, so they don’t need specialized enclosures. Likewise, cobots are far easier to program. Some cobots, like our Cobot Welder, can be programmed for a part batch in just a few minutes!
Collaborative robots make robotics far more accessible. With cobots in the picture, almost any shop can benefit from robotic welding speeds and productivity. Cobots often make more operational and economic sense for small-to-medium-sized shops and manufacturers.
Cobots weld fast. Our Cobot Welder goes up to 90 IPM! Contrast that with typical manual welding speeds of 10-20 IPM, and it's easy to see how some of our customers quadrupled their welding output.
How MIG Welding Speed Affects The Welded Part
The “right” welding speed is the one that completely maxes out the travel speed while meeting all the weld quality and penetration goals. This achieves maximum productivity and weld quality.
Welding slower or faster than optimal could reduce your ROI and cause weld issues.
The travel speed should be set correctly with consideration of these variables:
- Wire feeding speed and deposition rate
- Desired weld size and profile
- Joint preparation and type
- Penetration
- Material type
- Base metal thickness
- Shielding gas
- Wire diameter
Here’s an example: You are welding 3/8" steel plates with a 45-degree bevel in a V butt joint configuration. If you move excessively fast, you’ll get a narrow convex bead, undercutting at the toe since the filler metal deposition is insufficient for the rate at which the path melts, and you might not get proper penetration. But, if you move too slowly, you’ll lose productivity, distort the metal, and possibly even burn through the root since the part is beveled and it’s thinner at the root.
There can be hundreds of examples combining the factors from the bullet list above.
Finding the maximum speed can involve some trial and error on weld coupons. Experienced welders can get this right quickly, usually with several tries on scrap metal manually or with a cobot.
Robot Consistency Can Be More Important Than Speed
Cobots can almost always weld far faster than humans, but the speed is only half of the picture. The other half? Consistency.
Even if you, as a manual welder, pushed yourself to weld way faster than sustainable, you couldn’t do it as precisely and consistently as a cobot.
The thing is… with elevated speed comes a greater need for robotic-level precision. A simple hand tremor or a traverse angle inconsistency can affect the weld. Imagine driving 200 mph on a race track; a single error in steering and things could turn ugly real fast. It’s similar for high-speed welding. Not to mention that changes in the weld geometry, switching from linear to radial, and other joint variations would throw off a human if they tried welding fast with the same consistency from part to part.
Some welding variables, like the contact-tip-to-work distance (CTWD), can have profound effects on the weld quality. It’s simply impossible for a welder to match the cobot’s welding speed while keeping critical variables consistent. Even just a 1/4-inch variance in CTWD can drop the amps and significantly affect the joint’s integrity.
With a robot, stop-starts are dramatically reduced. So you’ll have fewer pauses between different weld types (linear/radial or changing from horizontal to vertical). A robot can weld these consistently, while a human must stop and realign their body/torch to the new position, causing a possible defect and a weakness in the weld with every stop and start. This problem is only exacerbated with high welding speed.
A cobot follows programming to a tee every time with every part, no matter how fast you set it to weld. Our Cobot Welder is adjusted via a smartphone app, Beacon. Once you input the parameters like travel speed, WFS, weave pattern, and voltage, the Cobot Welder will apply them precisely the same, always.
Benefits Of Maximizing Welding Speed With a MIG Cobot
On the surface level, a higher welding speed means faster production and more profits. That’s true, but leveraging the cobot’s welding speed can net so much more!
Higher Productivity Helps With Welder Shortage
The welder shortage isn’t going away anytime soon, while the demand for quality welding is rampant. You’ve probably already had to turn down work because it’s simply impossible to meet all the demand with manual welding operations. That’s something we often see with our customers—struggling to keep the backlogs at bay.
Welding at 2 to 3 times faster with a Cobot Welder can significantly alleviate this issue. For example, Industrial Manufacturing Services (IMS), was struggling with the labor shortage in South Carolina and had difficulty to meet the growing demand for parts.
Read the case study on how Cobot Welder helped IMS maintain production despite labor shortage..
“We had welders learn how to use Cobot Welder in about half an hour,” said Matt Blowers, an IMS Manufacturing Engineer. “Hirebotics’ Cobot Welder has allowed us to let non-welders operate the machine. They don’t need to learn the programming language, and they don’t need to go to a school.”
Higher ROI Per Paid Labor Hour
Massively improved productivity with the Cobot Welder means higher ROI on your labor. Since your welding team’s output is higher with a cobot, the paid hours generate more revenue.
Advanta Southeast LLC, our South Carolina customer, increased their welding by 400% with our Cobot Welder. “We went from 25 parts to 100 parts a day within a matter of just a few hours after we set up the first unit. So, it increased our output to 400% compared to manual welding.” - Mark Moye, Plant Manager.
Ability To Take On Jobs Previously Unavailable
In the same example of Advanta Southeast LLC, our Cobot Welder helped them open up to a broader market.
“One of the biggest benefits that we've seen from buying Cobot Welder is our ability to go after contracts that we weren't able to get before. Now, we're doing a lot more tower projects. Actually, we’ve just been awarded a big project to build towers for an electric vehicle manufacturer.”
High welding speed paired with exceptional consistency is non-negotiable for many high-value jobs. Some customers simply won’t accept manually welded parts due to welding inconsistencies from part to part or because of high lead times. Integrating our Cobot Welder with your processes can help you capture a larger segment of the market.
Reduced Operating Costs
Besides massive labor savings (in the sense that your existing labor will produce more), you can cut wire and gas costs. Optimized robotic welding speed eliminates overwelding (a common occurrence), helping you reduce shielding gas and wire use.
Overwelding is often overlooked, but it can be a significant cost factor. A WPS asks for a 1/8” fillet weld, but the welder deposits a 3/16” bead. This can happen due to low welding speed because the operator is melting more wire than necessary. While it may seem insignificant, the additional wire and gas costs compounded over thousands of welds you do annually can make up a good chunk of your accounting.
There’s also the labor cost of overwelding. A 5/16” fillet weld requires nearly 3X more arc time to complete than a 3/16” fillet. Compound such differences over the entire year, and you’ll pay far more in labor, overtime, power, wire, and gas due to welding slowly and inefficiently.
Have a look at this table for volume and deposited metal of fillet welds. The difference between a 3/16” fillet and just one size higher 1/4" is 20% more wire!
Fillet Weld Size | Volume (in.3/ft) | Weight (lb/ft) |
3/16 | 0.34 | 0.10 |
1/4 | 0.43 | 0.12 |
5/16 | 0.68 | 0.19 |
3/8 | 0.96 | 0.27 |
7/16 | 1.3 | 0.36 |
The Cobot Welder can help you reduce overwelding by making consistent welds.
Reduced Welding Defects And Distortion
Using an optimal welding speed for the welded thickness and material with a cobot can reduce distortion on sheet metal. You can MIG weld sheet metal manually, but you might not always be able to maximize the speed potential and do it as consistently as a cobot. When adequately programmed, Cobot’s heat input and distortion are minimal, and it achieves consistent results.
Low heat input also helps prevent defects like the loss of corrosion resistance for stainless steel and embrittlement of the HAZ in materials prone to it. In addition, it helps reduce weld oxidation and resulting discoloration in stainless steel.
Consistent Quality At High Welding Speeds
Not only do cobots weld fast, but they do so consistently. This is critical for taking your production to the next level. A human can never match the consistency at robotic welding speeds.
How To Set The Welding Speed On a MIG Robot
Collaborative robots are typically easier to program than traditional industrial robots. However, the ease of use among various cobot brands can vary.
Here at Hirebotics, we put the user first. Beacon, our smartphone software for robot welding, is designed for welders. Beacon has no complex interfaces, coordinate systems, excessive popups, matrix arrays, programming languages, and other non-fabricating stuff.
Inside Beacon, you can set the welding speed in just a few clicks.
You can also edit the travel speed for the whole part if you wish the speed to remain consistent over the entire weld length. Beacon also has a built-in AI that can assist you with the travel speed. It calculates the speed for the material and thickness, giving you a starting point to optimize. |
![]() |
Ready To Maximize Your Welding Speeds With Beacon?
Maximize your speed while minimizing rework with Beacon and our Cobot Welder. Book a Free Demo with our team to see if your shop can benefit from a cobot. Let’s hop on a call, and we’ll show you just how easy it is to program with Beacon!