Robotic MIG Welding Tips: 7 Expert Suggestions
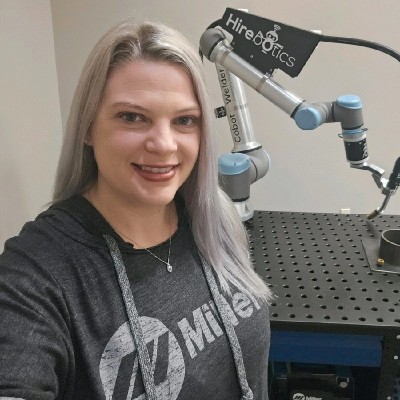
June 17, 2024
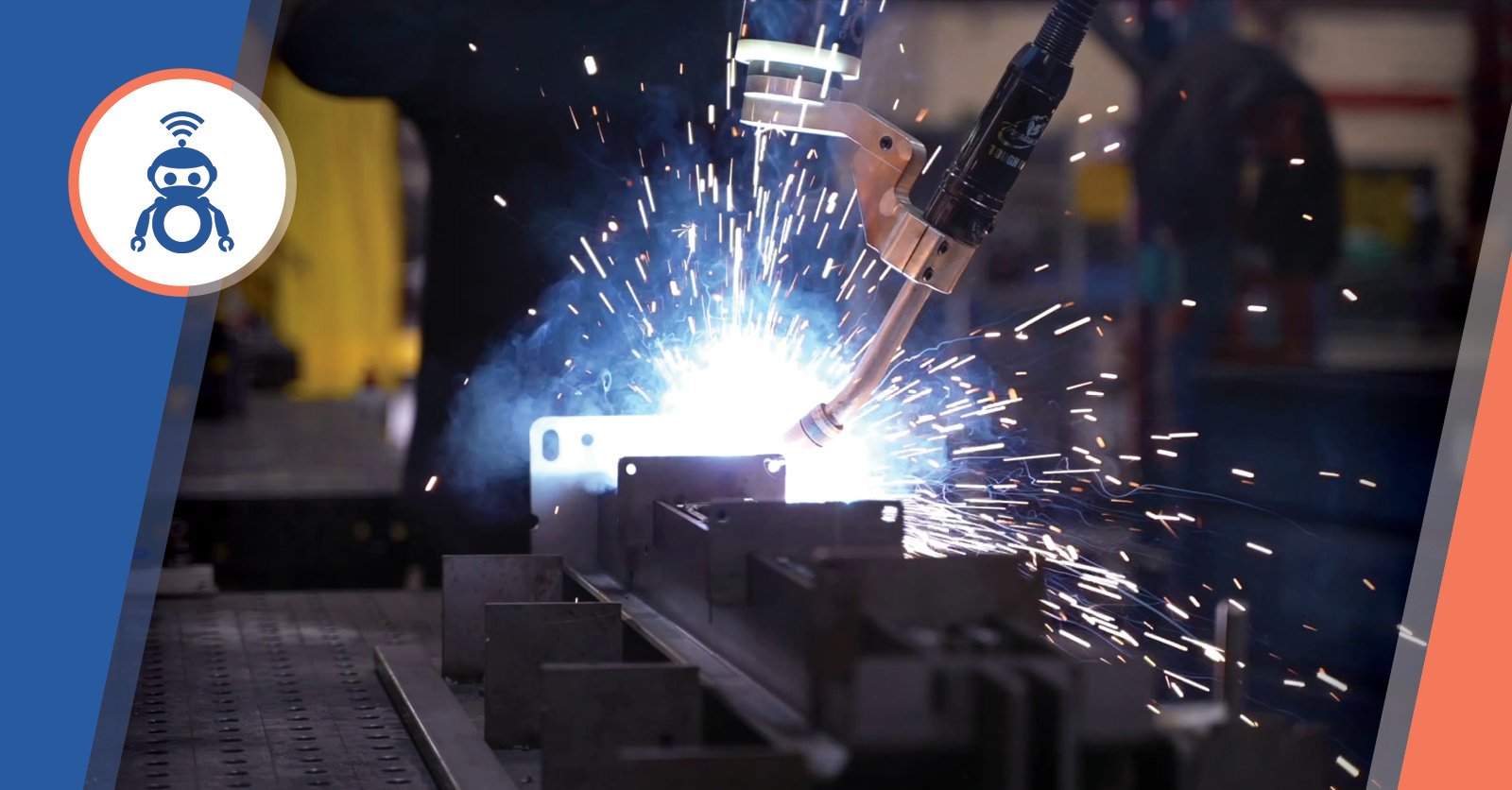
It takes just one or two unoptimized elements of the robotic welding process to make your production less efficient. Follow these robotic MIG welding tips and tricks to improve weld quality, productivity, and ultimately, profits.
1. Speed Is Your Friend, When Done Right
The faster you weld, the higher the productivity. However, you must also meet the required weld quality. Welding too fast or too slow can reduce the weld quality and your bottom line.
Material type, thickness, and position are the primary factors for selecting the right robotic MIG welding speed. Generally, it’s a good idea to run several weld tests before deciding on welding parameters like speed. As long as you meet the product quality, it's in everyone's best interest to increase the speed as much as the material and robot allow it.
Welding fast reduces heat input. However, using pulsed MIG (GMAW-P) can additionally limit heat input, distortion, and the risk of burn-through on thin gauge material by rapidly cycling the welding current. Pulsed MIG is especially useful for MIG welding aluminum, stainless steel, and nickel alloys.
Beyond heat control, Pulsed GMAW (MIG) enhances wire deposition efficiency and weld appearance. In fact, advanced pulsed MIG power sources and robotic systems can produce weld quality that rivals TIG welding.
3. Ensure Proper GMAW Wire Feeding And Wire Selection
Proper welding wire selection and implementation are critical for high-performance robotic welding. You can avoid issues like poor arc action, birdnesting, wire sticking, and excessive wire twisting by carefully considering wire type, diameter, and feed rate.
The wire cast (the diameter as the wire sits unwound from the spool/drum) causes the wire to rub against the MIG contact tip. This is essential for arc stability. With inadequate wire-to-tip friction, robotic welding can suffer much more than manual welding. A manual welder can adjust the torch for better arc action, while the robot always uses the same torch motion.
For proper wire feeding, use adequate roller selection (for wire size and material) and a wire straightener if necessary. It’s critical that the wire maintains a solid but not overly tight connection with the tip. A too-tight fit will cause the wire to widen the contact tip diameter and erode it quickly.
You must also select the appropriate filler metal for successful robotic welding. Choosing the right wire for the job can improve weld quality, post-weld processing, while reducing overall costs. For example, metal-cored wire can offer advantages like faster travel speeds, higher deposition rates, and reduced cleanup. When unsure, consult with experienced welding equipment and filler metal manufacturers to find the ideal wire for your specific welding process.
4. Use High-Quality Consumables, Liner, And MIG Gun
Robotic welding puts far more strain on consumables than manual welding due to significantly higher arc time. It’s best to use heavy-duty consumables to prevent downtime and weld defects from worn contact tips, liners, nozzles, and other consumables.
Besides quality, ensure proper consumable installation. Improper or loose connections between MIG gun components will cause more electrical resistance and heat. Of course, this means reduced consumable life and weld defects from an erratic arc.
MIG gun liner is the most often overlooked part. You should always use the right liner type for the wire and ensure the liner is cut to the right length with a proper fit with the gas diffuser/tip, depending on your MIG gun type.
5. Ensure The Robot Can Operate At All Times
The more your robot welds, the more revenue it generates. The more it collects dust, the longer it takes to pay itself off.
If your robot uses a complex software, you should ensure an experienced robotic welding programmer is available to work on it. This can be easier said than done, but it’s something to keep in mind. However, some solutions are easier to learn than others, removing the need to hire specialized robotic programmers. With the right system, your existing staff can quickly pick up how to automate MIG welding.
Easy to use and program systems, like the Cobot Welder, can save the day. For example, the smartphone app, Beacon, only uses shop language, not programming jargon for setting up the process. Teaching the Cobot Welder requires moving the cobot to the start and end of welds and setting up welding parameters (e.g., WFS, stickout, weave pattern). Since Beacon is so simple, anyone can learn to use it. Additionally, if a staff member is unavailable, another can easily take over, ensuring uninterrupted production.
Optimize the workflow so the robot finishes working with one material before switching to another. For example, weld all carbon steel parts before welding aluminum parts. Specific materials often require specialized liners, rollers, gases, and other system components. If your applications involve a variety of materials, investing in multiple robots can help you improve uptime.
6. Use Robot’s Consistency To Reduce Overwelding
Make several test welds until you create programming that produces a weld size that meets the customer's specs. Afterward, the robot will make the same weld over and over, preventing overwelding.
Overwelding wastes wire, gas, and time. For example, a 5/16” fillet weld has about 50% higher volume than a 1/4", requiring far more wire, gas, and work time. Standardizing your weld size before applying it on a batch with a robot can save significant resources.
7. Carefully Consider The Robot Programming Software
Robot programming software is one of the most important factors when considering an MIG welding robot. Here at Hirebotics, many customers choose us precisely for the software above everything else.
Welding robot programming software are typically used with a teach pendant to program a weld. Software can be more or less demanding. Programming typically requires experienced and specialized staff, but there are software solutions that anyone can master quickly. For example, Beacon, a smartphone app, allows your welders themselves to program a robot from day 1, eliminating the need for robotic specialists.
The software difficulty primarily varies between robot types. Which brings us to…
Collaborative Robots vs. Traditional Robots
You can automate MIG welding with a collaborative or a traditional robot. Their differences are outlined in the table below. You can learn more in the guide to welding robots.
Robot Type/Feature | Traditional Arc Welding Robots | Collaborative Welding Robots |
Designed For | Autonomous work | Working with the operator |
Flexibility | Lower | Higher |
Ease Of Programming | Difficult | Easier |
Safety Measures | Higher | Lower |
Best For | High-volume, low-mix | High-mix, low-volume |
All collaborative robots (Cobots) are easier to use than traditional robotics. However, not all cobots can be mastered quickly or programmed smoothly. While easier to use, they still have a learning curve you should consider.
Some cobot systems, like the Cobot Welder + Beacon software, are exceptionally easy to integrate into the welding workflow. Even a non-welder or someone who has never worked with a robot can run their first cobot weld in less than an hour with the Cobot Welder. Typically, welders and fabricators learn to use the system the same day it enters the shop.
Advanced Tips For Cobot MIG Welding
All the points discussed earlier apply to cobot MIG welding. Cobots are robots too, only designed to work alongside humans.
Let’s now see some advanced tips for cobot MIG welding:
1. Use Simplified Systems To Eliminate Excess Work
Cobots, like traditional robots, must have their tool center point (TCP) set for application. This is challenging and can be frustrating for welders or other non-robot technicians.
The Cobot Welder has its TCP preconfigured, eliminating this time-consuming hurdle. Likewise, you don’t need to set approach and exit points, reducing your operators' time and effort.
Other cobot software may also require you to set and adjust XYZ axes and go through multiple windows to get to the needed settings. Beacon is polished and simplified for welders, not programmers. You won’t find any programming jargon in Beacon; you’ll only need to adjust weld settings like travel speed, arc length, WFS, wire stickout, and other parameters your welders are familiar with.
2. Use Weld Patterning To Save Time
Want to set up several parts on the welding table for simultaneous welding? You can do this easily with the right programming software.
Watch this 2-minute video on how to apply the same programming to a part next to it. This can save you a tremendous amount of time when setting up a cobot to weld a large batch at once.
3. Air Moves Optimize The Welding Process
With a complex jigs and fixtures setup, your cobot can collide with the part or the setup. This is particularly true for multi-part setups on the table, especially the complex ones.
Here, air moves solve this issue. In Beacon, you can set an air move in less than 30 seconds to circumnavigate potential obstructions.
4. Collect Data And Optimize Your Production
You don’t need to be a data analyst to improve your robotic MIG welding efficiency. The data alone will tell you a lot.
- Am I using too much gas here? The graph shows a similar job in the past didn’t require this much gas.
- Why is there too little arc-on time? A similar part I welded earlier had more arc-on time. Is my weld programming too complex? Too many air moves?
- Can I meet the customer’s deadline? Let’s check the parts per hour graph on similar parts done earlier.
- Are my welds using too much wire? What does wire data look like between various part batches?
These are just some examples of how clear data charts can help you optimize your workflow and understand your production better.
Beacon automatically collects this data and shows it on your app home screen. You can modify and chart your data graphs to track and optimize various welding processes.
5. Ensuring Cobot MIG Welding Uptime
Whether your operator gets sick or the cobot goes down, your production schedule could get pushed out.
This is where software and strong support can significantly make things better.
For example, Beacon is so easy to use that all your staff can learn to use it relatively quickly. If your main welder is unavailable, someone else may jump in to keep the cobot running.
BeaconCare is a Hirebotics service you can leverage to avoid downtime if the Cobot Welder needs repairs. It includes total coverage of your cobot system and discounted non-warranty repairs. But most importantly, you get a loaner cobot replacement until your cobot is back in shape. So, no matter what, your team keeps producing.
Learn More About Cobot MIG Welding
Download the free ebook on welding cobots, or schedule a free demo with our team. We would love to discuss whether your production could benefit from cobot welding and show you how Beacon significantly makes robotic welding easier.