How to Build Stability in an Unpredictable Market
May 15, 2025
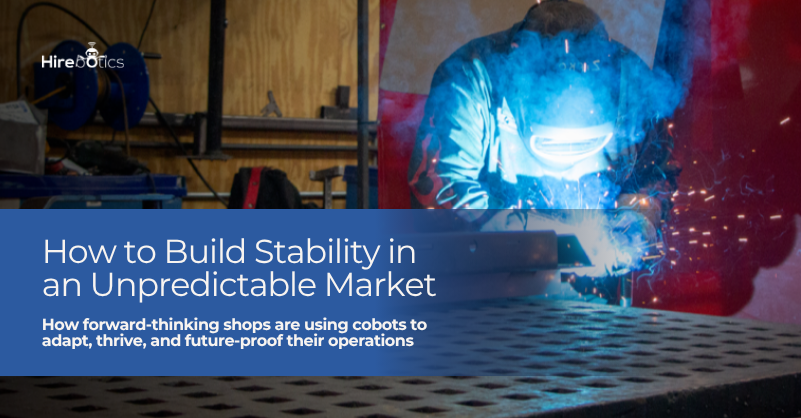
How forward-thinking shops are using cobots to adapt, thrive, and future-proof their operations
For many metal fabrication shops, staying competitive used to be a matter of hustle and precision. But in today’s volatile market, grit isn’t enough. Steel and aluminum prices are fluctuating, skilled welders are harder to find than ever, and tariff uncertainty continues to shake long-term planning. Amid rising costs and unpredictable demand, fabricators are left asking:
How do we protect our margins, meet deadlines, and keep growing – without burning out our workforce or risking too much capital?
The answer lies in a new kind of tool: not just faster or stronger, but smarter and more adaptable. Enter, welding and plasma cutting cobots.
The Cost of Uncertainty Is No Longer Bearable
Let’s be honest: fabrication has never been easy. But the pressure today is different. It’s not just about doing more with less, it’s about doing more with less predictability.
-
Material price hikes mean a misstep in planning can kill a job’s profitability
-
Labor shortages force shops to turn down work or miss deadlines
-
Tariff and global supply chain swings make long-term planning feel like guesswork
Even high-performing shops are playing defense. They’re absorbing rising input costs, retraining new welders who leave after six months, and fighting to keep experienced talent on repetitive jobs that cause fatigue and burnout.
In this climate, traditional thinking—“let’s hire another welder” or “we’ll figure it out next quarter,” no longer cuts it. What fabricators need isn’t just more hands on deck. They need resilience built into their process.
The Workforce Has Changed... Have You?
The shortage of skilled welders isn’t a temporary problem. It’s structural. As older welders retire, fewer young people are entering the trade, even with increased recruiting efforts. The U.S. welding industry is expected to be short over 300,000 welders by 2029, according to the American Welding Society.
At the same time, customer expectations are rising. Jobs that used to take two weeks now need to ship in five days. Quality standards are higher. And customers are less forgiving.
Fabricators are stuck in the middle; trying to meet modern demands with a shrinking labor pool and tools designed for a different era.
What if the solution isn’t replacing welders, but empowering them?
A New Tool for a New Era: The Welding Cobot
Welding and plasma cutting cobots (collaborative robots) are redefining how small and medium-sized fabrication shops stay competitive. Unlike traditional industrial robots, cobots are built to work alongside people. They’re easier to set up, safer to operate, and more flexible to redeploy from one job to the next.
Hirebotics’ cobots, for example, come with a no-code, app-based interface that welders can learn in a few hours – not weeks. This means your current team can become your automation team.
And that’s the shift: welding cobots don’t replace humans, they extend them. They take the most repetitive, fatiguing, and precision-heavy welds off your welders’ plates so your people can focus on what they do best: solving problems, managing complexity, and maintaining quality.
Why the Smartest Shops Are Investing Now
We hear it all the time: “It sounds great, but this isn’t the right time for us to make a big investment.”
That makes sense—on the surface. But here’s the reality:
Not investing in cobots means staying exposed to the very risks fabricators say they’re trying to avoid: unpredictability, rising labor costs, missed opportunities, and burned-out welders.
Welding cobots flip the equation. They create predictability in your cost per part. They add capacity without increasing your headcount. And they allow you to say yes to more jobs without overloading your team.
Cobots give you a new kind of control over your business—something that’s increasingly rare in today’s economy.
Your Edge in the Age of Uncertainty
When markets are in flux, the winners aren’t always the biggest shops with the biggest budgets. The winners are the most resilient – the ones who adapt early, learn fast, and make smart bets that create leverage.
That’s what welding cobots offer: real, measurable leverage.
1. Cost Control
Cobots reduce your cost per part by minimizing manual labor and rework. Once a weld path is programmed, the cobot repeats it exactly every time – no breaks, no burnout, no variability.
That means:
-
Fewer defects
-
Less wasted material
-
Lower per-job labor cost
2. Increased Throughput
Cobots are always ready. When the fixture is loaded, they weld. No lunch breaks, no shift changes, no sick days. This consistent uptime can dramatically boost your shop’s output, without needing to staff a second shift.
Some Hirebotics customers run lights-out production overnight with one cobot and a material handling system.
3. Reliable Scheduling
With cobots, your production plan becomes more than a wish list. You gain confidence that jobs will run as expected – helping you quote more accurately, hit delivery dates, and earn repeat business.
This reliability becomes a competitive edge when other shops are missing deadlines due to labor gaps or overcapacity.
Why Hirebotics?
We design welding automation for the real world. We understand that most shops don’t have an automation engineer on staff or weeks to train on a new system.
That’s why our cobots are:
-
App-based: Your welders can program them with just a few taps – no code required.
-
Flexible: Easily switch between jobs, parts, and processes with no downtime.
-
Compact: Fits into your existing weld cell without needing a full rework.
-
Empowering: Let your best welders focus on high-value work while the cobot handles the rest.
We’re not just giving you a machine. We’re giving you a path forward.
What Fabricators are Saying
“The impact on business productivity is pretty crazy. We went from having to cancel or not take orders to working ahead.”
— Industrial Production President
“We went from 100 minutes per order weld, to 10 minutes with the Cobot Welder. We recouped our costs in one order.”
— Marine Parts Fabricator
“Cobot welders run longer with hardly any downtimes, increasing our productivity and cycle times.”
— Manufacturing Engineer
How to Get Started
Making the leap to cobot welding and plasma cutting isn’t about changing everything overnight. It’s about taking the first step to recognizing one high-volume, repetitive job you could automate.
Here’s what we recommend:
-
Identify your most repetitive, fatiguing welds.
These are usually the best candidates for cobot automation. -
Talk to our team.
We’ll help you understand if a welding cobot is the right fit for your needs and walk you through the setup. -
Start small. Scale fast.
Most Hirebotics customers start with one cobot and quickly expand once they see the ROI.
Final Thoughts: Build Certainty into Your Shop
The challenges facing fabricators today are real. But so are the solutions.
Cobots give you more than just speed and efficiency, they give you confidence. Confidence that you can say yes to a big job. Confidence that your team won’t burn out. Confidence that your shop will still be standing – and growing – no matter what the market throws your way.
You don’t need to be a robotics expert. You just need to take the first step.
The future of fabrication isn’t about working harder. It’s about working smarter, with tools that make your business more resilient, more efficient, and more competitive.
Hirebotics is here to help you get there.