Empowering Partners to be One with their Automation
by Josh Crane, on Apr 24, 2020 8:52:53 AM
One of the most prevalent principles at Hirebotics is providing team members the resources and autonomy to get the job done without input from others. We make certain that we have hardware and software tools in place to inspect the robot performance and make necessary changes. Even before recent times, this mentality has grown to involve our partners. Using Hirebotics software tools including our new URcap that continues to evolve, they understand how the robots are functioning and have the information pertinent to getting more good parts manufactured, inspected, and processed out the door.
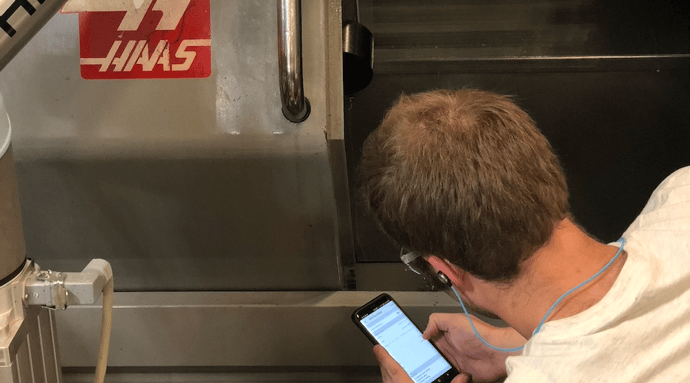
The Motivation
When we take on a new project, we are enabling a robot to operate a lathe, a mill, a stamping press, or other piece of complex machinery. From the time the project kicks off, we are learning about the equipment we are operating - its quirks, its constraints, and how we can maximize efficiency by providing the right inputs and reading the right information from it. During this process we ask a lot of questions.
The questions are answered by the same group each time - our partners. They have lived with these machines, often for years, and have adjusted to the quirks. When Hirebotics completes the installation, our partners are the eyes and ears - as well as the hands - that keep the integrated cells chugging happily along. It is in the best interest of Hirebotics and our partners to enable all users to support their automation. It reduces downtime and allows Hirebotics to move forward with new capabilities.
The Action Plan
There are a few different angles from which we can enable our customers to be hands on, we will focus on 3 right now:
- Onsite training during deployment;
- Communication and recommendations in the Hirebotics app; and
- Autonomous adjustments to the robot cell.
Once the robot is installed and running production, we will carry out a variety of training with our partner. This includes preventive maintenance like air filter changes, cleaning the end of arm tooling, and inspecting the part presentation system if needed. It also involves communicating and documenting what we learned during our time with them. Did we have to add an unexpected input? Did we have to make a change to our program? Did we find that the machine takes a certain amount of time to be ready between parts processed? These are all factors we learn and communicate before we exit the site. We train our partners on the robot and the equipment around it. By the time we leave, we and our partners know each component in the cell and how they interact - then we can communicate effectively when we are not face to face.
In the Hirebotics app, users can reach out by sending us a message or picture when they have questions about their automation. By responding quickly, often within minutes, and providing remote support, Hirebotics empowers our partners to prevent slowdowns and resume running quickly - faster than we could be onsite. Our partners are experts in their automation and can see the cell and monitor the machine in real time. In the app, they also have access to data from their cell, including good parts, runtime, and reasons for rejected parts. They receive push notifications when action is required, whether the robot is asking for new parts or it needs a human to reset a machine in the cell. Messaging and controlled robot actions will soon be within the Hirebotics URcap as well. These messages are automated, and our partners do not need to wait for input from Hirebotics to take action.
Messaging and controlled robot actions will soon be within the Hirebotics URcap as well.
In fact, sometimes customers improve their cells without our input at all. They may add a piece of equipment or change a machine program that reduces run time. They might make easier the way in which humans interact with the cell or robot. They are able to do this because they are experts in the cell, especially the tools and processes they have had in place even before they reached out to Hirebotics for automation. They know their projected needs, and demands, and can adjust accordingly using the tools mentioned here: training to become familiar with the robot and its abilities as well as the Hirebotics app to understand where the cell is providing success, and where improvements are possible.
Together, all these tools are key to driving productivity and giving our partners a chance to move faster and reduce cost. Time is money. Being able to understand the robot cell in real time and have the autonomy to make changes as needed, and even receive input from Hirebotics allows them to process better parts in less time.