Is Welding Automation A Good Fit For Your Business?
August 11, 2021
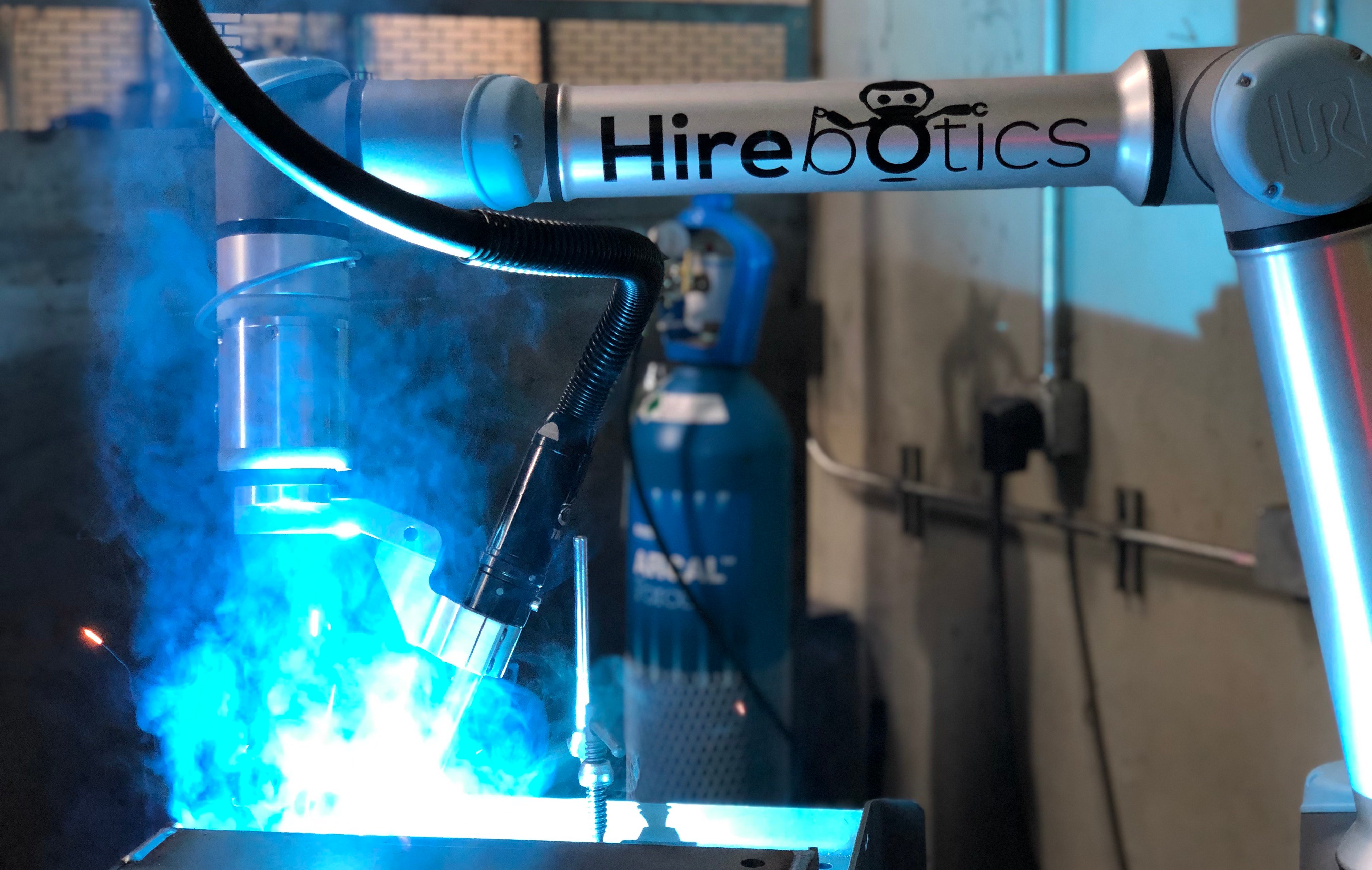
Automation is a buzzword in all industries for various tasks. Welding is not exempt from this trend. But before you join the bandwagon, it’s best to ask yourself a question: Is automation the best route to take for your welding operations? Or is it better to stick to manual welding? Let’s assess the situation.
Are Your Welding Operations Ready for Automation?
Deciding to automate your welding process is not as easy as putting a robotic welder in and calling it a day. Some things should already be present in your welding workflow for the robotic welder to work. Let’s take a look at these factors.
First, your welding operations will benefit more from automated welding if they have one of these characteristics:
- The quality and/or function of the weld is critical
- The welds are repetitive; on identical parts
- The parts have accumulated significant value before welding
- For best success, parts to be welded should have simple, repeatable welds with minimum gaps. Non-complicated details will make it easy for the robot to weld.
See Our Case Studies and
Learn how Advanta industries Increased their productivity 400%!
In addition to the actual welding itself, your welding workflow should accommodate the robotic welder. For instance, do you have enough space to store the welded parts? Can your painting and assembly lines handle the increased productivity?
You should also already have a good understanding of your current production workflow. This understanding enables you to measure the improvements of the automated system in place.
The best candidates for automation are parts that are high volume and low-variety welds. Low variety welds need less programming and tooling changes.
If your welding projects have low volume but high variety, automated welding might not be easy to implement. The same is true if you’re accepting complicated welding jobs. For example, welding parts that have a tight access point. This would not be suitable for automated welding because it requires a lot of operator input, translating to a lot of programming.
Benefits that Welding Automation Can Bring
We know that you may be facing many challenges in your business and many are related to your welding processes alone. Automating your weld process can have a positive effect on your company in general. There are many benefits that your company can reap from automation. We can list them, but generally, these fall into four categories.
- The first is improved weld quality because the robotic welder doesn’t tire and delivers the same quality every time.
- You’ll expect increased productivity because robots don’t need rest and can keep on going.
- You’ll also find less scrap because the robot is more efficient in using the materials.
- And, of course, robotic welders can lower labor costs over time.
Not Any Welding Automation is Right For Your Company
Although, at first glance, it looks like industrial automation is the answer to all your prayers. It may not be a good fit for your actual welding needs. Industrial welding robots work best in industries that have high volume, low mix environments. The automotive industry is an example of this.
Also, the welding robots are bulky and dangerous. They need to be housed away in a robotic welding cell. And intensive safety protocols have to be put in place to make sure that accidents don’t happen. Their size means they can’t be moved and need to be placed in a fixed position.
These robotic welders also require intensive programming. Some even need a dedicated team for programming and maintenance. All of these translate to more investment on your part.
Small to medium companies with welding operations might not be a good fit for automated industrial welding. This is because you need a cost-effective robot that can handle the low volume but high variety projects you are welding. Unfortunately, industrial robots don’t fall into this kind of category.
Automate with a Collaborative Robot
So if you’re a small to medium business with welding needs, and you’ve ticked off all the boxes and determined that you are ready for automation. What now? Can you find robotic solutions that fit your reality?
The good news is you can! You can automate your welding process with a collaborative welding robot. Also called a cobot, they are robotic arms that are built to work alongside humans. You can think of them as an assistant to help with every weld. Unlike industrial robots, they are flexible. They can also do several tasks depending on what project you’re working on.
Cobots are also easy to program and don’t need a robotics specialist. The Cobot Welder from Hirebotics, as an example, only requires an app on a phone or tablet for your welders to start using it. They can weld anything using the Smart puck technology to teach the robot. So if you’ve doubted if automated welding is a good fit for your small business, look no further. Welding cobots may be what you need to solve your many welding challenges.
Need more help in figuring out if your company is ready for automation? Contact us and our friendly staff is ready to answer all your questions.
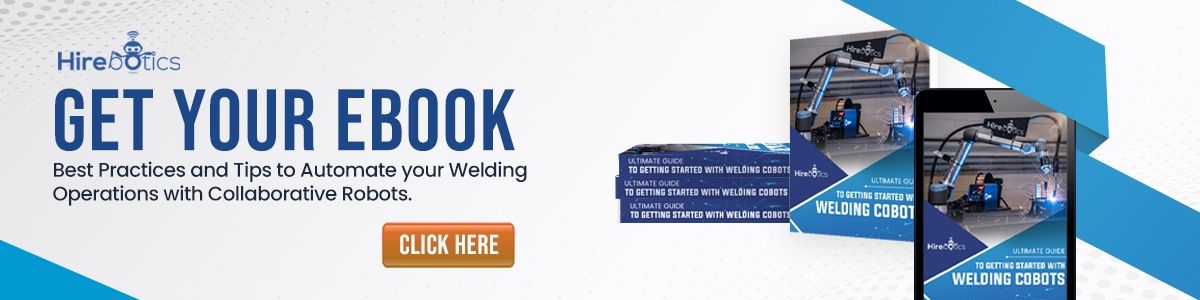