5 New Developments in Robotic Welding Technology
March 31, 2022
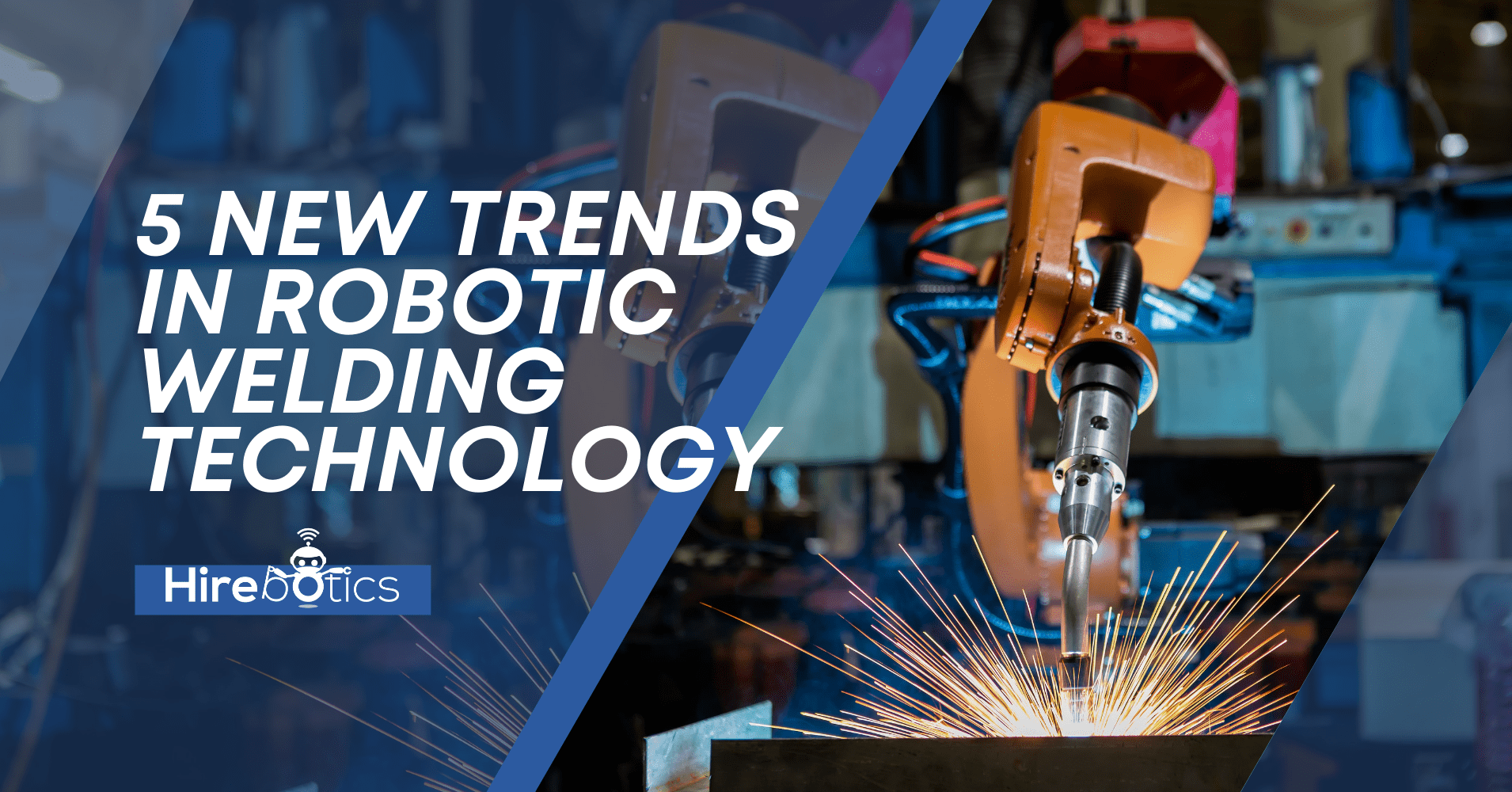
Manufacturers are under constant pressure to increase production capacity without compromising on quality. In the last decade, leading manufacturers have looked at robotic welding technology to assist their welders and increase productivity – but this approach came with its own set of challenges.
Welding automation and robot welders have been a rising trend in manufacturing for decades now. Robot welding is a key enabler for the manufacturers that want higher throughput during every shift. From the first UNIMATE spot welding robot used by General Motors in 19682 to today’s advanced robots with automated sensing and articulation systems, the industry has come a long way over the last 60 years.
Implementing robotic welding systems on the factory floor helps introduce a workflow that delivers quality welds repeatedly while saving on materials and improving safety.
Some of the latest robotic welding developments make it even easier to adopt this technology to assist with your daily operations. Here are five trends driving the industrial use of robots in welding applications.
Key Trends Driving Robotic Welding Technology Today
Robotic welding systems aren’t new, but the technology deployed with today’s solutions has advanced considerably. For example, Robotized gas metal arc welding (GMAW) provides high-volume productivity and can now overcome the challenges that professional welders face.
Some of the challenges that require adjustments during weld operations include:
- Subtle variations in workpiece dimensions
- Thermal distortions and imperfect edge preparation
- Workpiece inaccuracies and weld penetration control
Welding robots commonly use semi-autonomous system designs to ensure that each weld is perfect before leaving the production line. Let’s look at five of the latest innovations driving the robotic welding industry.
1. Elimination of Fixtures for Increased Efficiency
Fabricators maximize efficiency on the production floor by incorporating material handling robots into the weld cell. This eliminates the need for operators to load and unload fixtures during the weld workflow and maximizes throughput by reducing cycle times.
By automating these mundane tasks, fabricators can reduce costs and increase safety in the factory. Operators don’t have to attend to every weld operation, and you can reduce the exposure to toxic gasses or other hazards that are common in fabrication shops.
2. Automated Sensing for Improved Weld Quality
Automated sensing technologies enable robotic welders to adapt operations according to individual workpiece dimensions. This improves the quality of each weld while increasing the speed of operations and, as a result, provides for higher throughput.
Including these technologies into each weld, cell helps to:
- Automatically adjust the weld robot’s parameters according to the workpiece
- Monitor the weld operation and record the details for continuous process optimization
- Stop any operation that falls outside of the benchmark parameters for improved quality and safety
Laser sensing technologies facilitate greater autonomy during welding operations. Advances in this field continue to drive up productivity while ensuring the quality of each seam during the manufacturing process. If any workpiece falls outside of the pre-defined tolerances, the robotic welding system can send an alert to an operator to address the issue.
3. Real-Time Data Acquisition and Analysis
Along with automated sensing, the operational data acquisition and analysis of robotic welding systems are improving at a rapid speed. As each weld needs a proper inspection to pass the quality control process, these tools make it possible to validate the joint strength, weld penetration, and seal of every seam during the weld operation.
Arc tracking control systems can automatically detect faults and correct the weld operation to reduce rework that usually only emerges during a secondary inspection. Additionally, these systems provide for:
- Joint edge detection and tracking seam penetration during welds
- Controlling weld penetration according to the specifications
- Joint width and profile measurement during weld operation
- Contour management with image acquisition for complex weld operations
4. Integration with Upstream and Downstream Processes
Welding robots often operate directly on a production line where the process depends on upstream quality checks and downstream inspections. Modern robotic welding systems need to integrate with other information management systems to keep the production line flowing at the required rate for greater productivity.
By integrating the part transfer systems with the weld cells, operators can maximize efficiency and reduce defective welds to downstream operations. Merging operational control systems with robotic weld systems allows you to:
- Increase throughput with precise quality control for each workpiece
- Save on time, materials, and floor space in the facility
- Achieve a streamlined production process with automated transfers between work cells
5. Improvements in Ease-of-Use with Cobots
One of the most significant advances in robot welding technology is improved operational control and cost-efficiency using cobots. Historically, manufacturers needed to employ programmers to set up industrial robots and manage any change to the production parameters or new software code. Apart from needing skilled coders to work on the robots, any shift in the operational parameters also increased downtime and reduced productivity.
Modern cobot welding tools like the Cobot Welder from Hirebotics empower operators to manage each welding cobot using an app for improved ease of use. Instead of depending on programmers, manufacturers can let welders set up the parameters and remain in control of each weld.
By improving the ease of use, manufacturers can:
- Overcome the skills gap for experienced welders currently facing the industry
- Easily define the weld parameters, including torch angles, speed, and weaving
- Let welders set up the system and deploy welding robots quickly throughout the factory
- Set up alerts for any issue that the robot may face or require human intervention
With Hirebotics and easy-to-use cobot welders, manufacturers have the freedom and flexibility often lacking from these solutions.
Increase Efficiency and Productivity with Welding Robots from Hirebotics
A significant challenge for manufacturers is deploying a robot welder quickly and with minimal programming expertise. Hirebotics makes it possible to configure the welding parameters for a robotic welding system by people who have years of expertise in the industry. In addition, welders can use the app to set up each weld’s specifications and teach the cobot without resorting to programming.
To see how our welding robots can help you increase efficiency and speed at your facility, schedule a demo from Hirebotics today.