Beacon + Cobot vs Other Solutions for Metal Fabrication
April 16, 2024
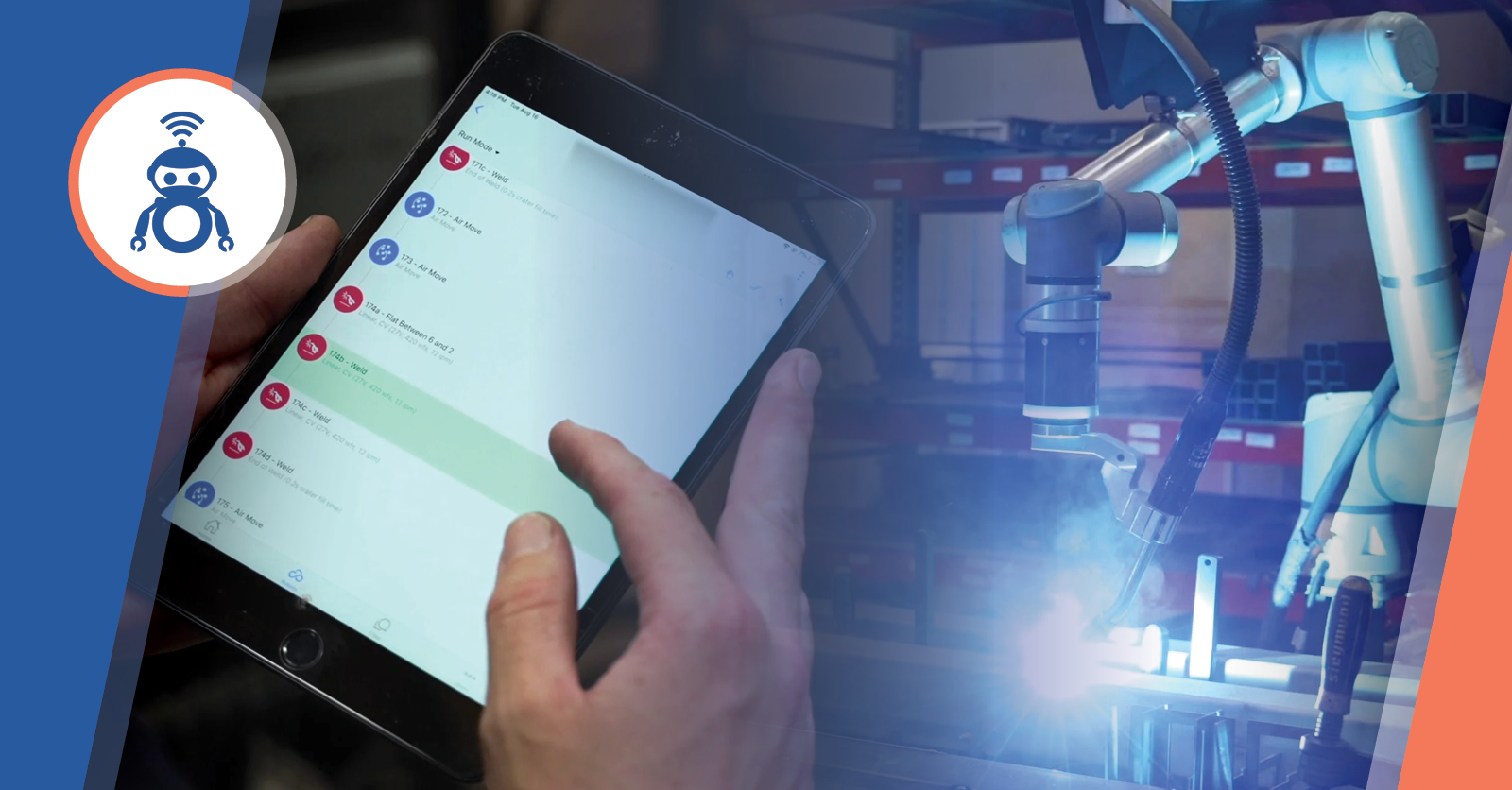
You hear it all the time: “cobots are easy to use.” While all cobot solutions are easier to program than traditional robots, they can still be quite complex to learn and use in the shop.
When you see “cobots are intuitive and easy to use,” a message almost every cobot brand uses, you envision a process where you only have to make a few clicks to weld/cut. However, that’s not always the case. Often, you must work with an interface with a bunch of windows, pop-out and drop-down menus, coordinate systems, and way too many options.
Do you really want to deal with TCP, variables, X/Y/Z axes, scaling factors, macros, math, planes, payload, cobot joint positions, the center of gravity, and other non-fabricating stuff?
No? We thought as much!
That’s why we believe, and our customer success case studies confirm, Beacon + Cobots is the way to go. Beacon redefines the “ease-of-use” that’s thrown around in the cobot industry, giving you a truly intuitive setup your fabricators can learn in minutes.
In this article, let’s discuss:
- What is Beacon?
- Comparison Table - Beacon + Cobot Vs. Other Cobot Solutions
- How Beacon Compares To Standard Cobot Control Systems
- Program Creation
- Part Editing
- Accessibility
- Reporting
- Support - Beacon + Cobot Leads The Way
What Is Beacon?
If you can send a text message with your phone, you can program a cobot with Beacon. That’s the power of Beacon. It democratizes the cobot revolution, allowing everyone to scale their output with minimal training.
Beacon is a smartphone app with an interface so intuitive that even non-fabricators can run their first cobot weld/cut in minutes. It’s an alternative to complex teach pendants, but also a platform with real-time reporting, access to cobot details, and chat support.
We are so confident in Beacon that we recommend you demo other cobot solutions too! Once you see the difference between Beacon and what’s out there, you’ll know Beacon leads the way.
Comparison Table - Beacon + Cobot Vs. Other Cobot Solutions
Beacon + Cobot |
Standard Cobot Solutions | |
Program Creation |
Part creation takes less than a minute. Weld points automatically populate in the Beacon app. You can compound multiple weld types in the same interface. Automatically calculates approach and depart positions in the background. | Often going through multiple windows, settings, and more complex interfaces. Usually requires positioning the cobot, manually opening the window for each point, and verifying it on a teach pendant. Need to program approach and depart points. |
Part Editing |
Simply touch the weld/cut point in the part to edit it, or add the activity between two points. | Requires slightly more effort to get to all part editing options. You often must manually verify the newly edited point on a teach pendant. |
Weld/Cut Parameters |
Easier to access and more intuitive to manage in a smartphone view. | Accessible from the robot program screen on a teach pendant after switching to the process window. |
Accessibility | Beacon is available for smartphones and desktops, making it highly accessible worldwide. | Usually, you need to use a teach pendant to modify and view cobot tasks. |
Reporting | Comprehensive monitoring and alerts. | Limited monitoring and reporting abilities. |
Support | In-app chat support that responds in minutes. | Depends on the brand. |
How Beacon Compares To Standard Cobot Control Systems
Beacon eliminates clutter and helps you fabricate with a cobot faster. Fabrication makes you money, not getting stuck with complex interfaces. Smooth tools that integrate, not frustrate, keep your metal workers productive. Beacon is a simple welding robot programming software. It’s designed to make cobot fabrication as smooth and easy as sending an email!
Program Creation
At Hirebotics, we like to use the term “teach” instead of “programming” the weld/cut task. Beacon’s interface is so far from programming that it doesn’t make sense to use the industry-adopted term “program."
So, how do you teach a task with Beacon?
First, create a part. Click the “+” icon in the app, name the part, set the weld/cut parameters, or choose settings from the library, and that’s it.
Next, add the linear, radial, tack, stitch, rotary weld/cut path, or a combination of those. For example, you can use the Cobot Welder to do a linear weld that has a 90-degree radial before continuing with 3-stitch welds. You add these points by highlighting the item type in the app and moving the cobot arm manually. Once you touch the teach button on the cobot, the highlighted item is automatically added to the path in Beacon. The same goes for cutting with Beacon and our Cobot Cutter.
The whole process can be as short as less than one minute. But even highly complex weld/cut paths can be taught to cobot quickly.
Top Tip: Beacon can auto-program the welding speed for you! Based on the material type, thickness, process, wire diameter, and shielding gas, Beacon automatically calculates the welding speed most suitable to prevent distortion and cut consumable costs. Of course, you can also adjust it manually!
Now, doing all of the above on a teach pendant is not as straightforward. First, your Tool Center Point (TCP) must be set for your application. This is a typical prerequisite for cobot work that Beacon eliminates from your workflow. Setting up the TCP can be quite demanding, depending on the cobot interface. Definitely not something that’s “easy to do,” as most claim. Even if you’ve got the aptitude for robotics, doing this in a fast-moving production environment is frustrating at best and time-consuming at worst. You can lose up to an hour on TCP alone.
https://www.instagram.com/hirebotics/p/CANarUGpZD9/
After the operating environment is set, you’ll need to set the weld/cut path and parameters.
For most pendant-type software, you must choose the item type to include in the robot program. That’s not challenging on its own. But, dealing with the approach and depart points, several windows, and too many bells and whistles simultaneously can be intimidating.
Unlike Beacon, many standard teach pendant software don’t automatically populate the path. Instead, you position the torch to the path point, select the start/end or other point parameter on the teach pendant, click adjust the waypoint, and verify the XYZ axis on the pendant - a more time-consuming process compared to Beacon. The difficulty can grow substantially with highly complex parts.
Part Editing
Alright, we made the part. But, what happens if we need to modify the weld/cut path or parameters of the process? Or what if we want to copy or shift the path to another part?
Excellent questions! These scenarios will happen all the time in the shop, which is why we designed Beacon to make these processes as smooth as possible.
Maybe your customer decided to change the material for the upcoming part batches, or one member of the part needs to be replaced with a different thickness. For example, going from mild steel to stainless steel requires reducing the heat input, using the pulsed MIG, or increasing the welding speed.
Beacon lets you alter the individual part points and their weld/cut settings by simply touching the point. For example, touching the start point in the linear weld lets you immediately adjust weld settings or the torch position in a smooth, uncluttered interface.
Doing the same on various teach pendant software requires a bit more work using a less optimized interface. The process is similar. You touch the weld/cut path point, but instead of the settings all being presented in a single, non-intrusive pop-up, you must click the “process” tab or the “update waypoint” to start modifying. Finally, positioning your torch (if the point needs to be updated) doesn’t typically automatically log the update like Beacon. Instead, you must verify the XYZ position on a teach pendant, an extra step that makes it more time-consuming. This process can vary from the cobot brand, but this is the industry norm for the most part.
Shifting And Patterning
Let’s say you wanted to program your cobot to do 10 parts at once on the table, each with a linear fillet weld. With Beacon, all you have to do is set the weld path on the first part and use the pattern function in Beacon on the remaining 9 parts you’ve placed in fixtures.
First, select all weld points of the first part. Then, click the shift button in Beacon. Finally, position the torch manually to the origin point of the new part and click apply in Beacon. You’ll be asked if you want to shift or pattern the part. Click pattern, and you are done. Now, the next part will have the same weld path applied.
If you wish to shift the path instead of patterning, select the shifting option when prompted. This lets you move the weld/cut path if you’ve physically moved the fixtures on the table.
Many other cobot solutions offer patterning and copying of the weld/cut process. But, the process is more challenging as you can deal with planes, re-verifying of the points, and multiple windows and steps, depending on the cobot solution.
Beacon does it faster and more straightforward. With Beacon, the bulk of it comes down to moving the starting point (origin) from one part to another while the process is copied automatically. It’s like saying to Cobot, “I showed you how to do the first part. Now do the other 9 exactly the same, and here are their origin points.”
Accessibility
Beacon is always with you; teach pendants are fixed to the cobot. Beacon is incredibly intuitive; teach pendants have too many windows and menus.
When you are on the shop floor, and someone’s using an angle grinder nearby, your workmate is welding or plasma cutting manually, mechanized positioners and manipulators are used, or other equipment is working near you, you don’t want to be bothered with a bunch of windows and settings on your teach pendant. It can get messy. Shop conditions aren’t always idyllic where you have the time or the focus to work with complex digital equipment. Of course, this depends on the person and the shop’s activities. But, generally, you want the cobot use to be as simple as possible.
Beacon provides not only cloud-based, smartphone accessibility to use anywhere, but also an accessible interface. Beacon is a highly polished app for improving the welding robot ROI. Nothing is hidden behind too many options and menus. The elements don’t clutter the interface. Accessibility means intuitiveness and total control wherever you are. This also includes desktop access, which is a Beacon supported platform.
So, you can monitor, copy, share, update, change, or revert cobot settings even being hundreds of miles away, or just by moving a little to the side in the shop to get away from the noise. Whatever you presently need.
Reporting
Most cobot solutions provide limited data that is not as easy to access. Beacon offers an in-app, real-time overview of your cobot fleet.
Just hit the home screen in the Beacon app, and you’ll see automatically populated graphs of your cobot arc time, parts per minute, gas and wire consumption, and other critical information. It’s easy to customize the reporting to your needs, giving you total productivity monitoring software as part of your cobot experience. This data alone is worth using the Beacon, let alone all the other goodies.
Support
Depending on the cobot brand, you can have phone, chat, or email support. We’ve built the support right into the Beacon interface. We are there with you at all times. Just tap on the chat icon in the app, and we’ll get back to you in several minutes.
Beacon's comprehensive instructional videos and how-to articles are extremely easy to grasp. We cut the clutter and get right to the point. For example, our how-to video on combining different weld types is just 2:33 minutes long. Compare that with other solutions on the market where you have to watch videos for hours.
Beacon support videos are simple because the software is actually easy to use. There is no “Oh, but you first need to set your TCP and the plane and this and that.” In fact, our complete Beacon how-to video, which combines all of our how-tos, is just 17 minutes long. On the other hand, some cobot solutions require you to watch several 10-15 minute videos to solve an issue you encountered in the shop. That’s counterproductive and not what cobots are about.
Beacon + Cobot Leads The Way
Besides Hirebotics, some of the most prominent cobot brands on the market are Vectis Automation, Lincoln Electric, Miller Electric, THG Automation, ESAB (Hirebotics partner) and Smooth Robotics. There are several other popular welding robot manufacturers, too. We invite you to try all of them! That’s right. Demo our competition when choosing a welding cobot solution, and you’ll see why we are so confident in our products.
We believe Beacon, paired with our Cobot Solutions, offers the most productive cobot setup that requires the least effort from the operator. Our focus is on maximizing your arc time, not banging your head against the wall time. We believe in effortless automation and democratization of the game-changing cobot technology. That’s our mission. That’s why we developed Beacon.
Ready to join the cobot revolution with an app as simple as your social media? Book a Demo with Hirebotics today.