How Cobot Welding Is Solving Your Welder Shortage
May 24, 2022
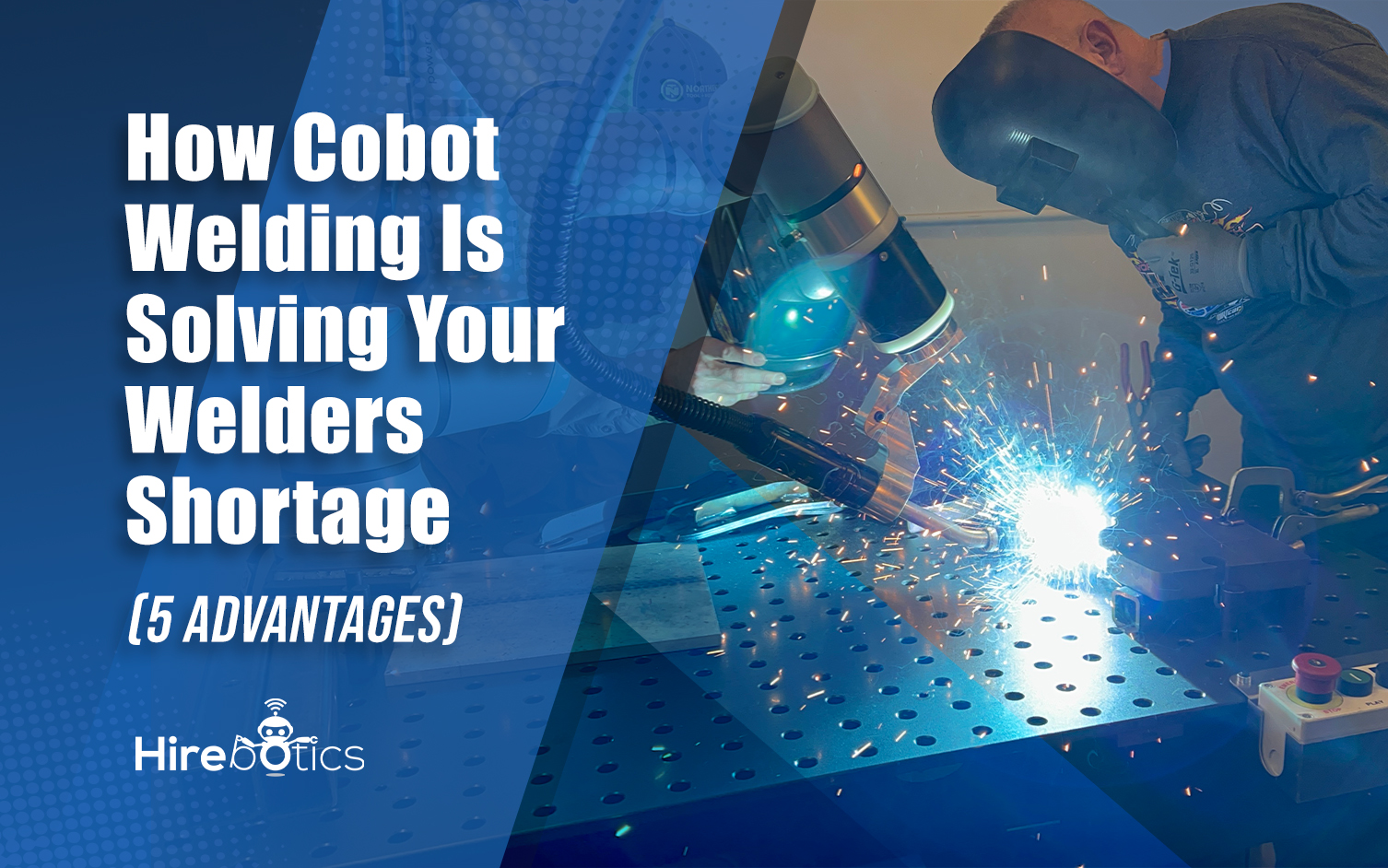
The welding industry is currently facing a shortage of welders. While there are several ways to fill this gap, cobot welding offers some unique advantages. Here we'll look at 5 reasons why the right welding cobots might be the best way to overcome the welding shortage.
What is a Cobot?
A cobot is a collaborative robot designed to work alongside humans in close physical proximity. They are also known as 'human-safe' or 'tabletop' robots because of their smaller stature (usually 20 to 40 inches in reach) and lower payload capacity (11 to 22 pounds).Cobots are designed to interact directly with humans in shared workspaces. This capability results from several important cobot design features:
- Reduced size and weight: Cobots are physically smaller and lighter than traditional industrial robots, making them less imposing and more accessible for humans to work around.
- Safety sensors: Most cobots include built-in safety sensors that detect when a human enters the robot's workspace. This allows the cobot to stop or slow its motion to avoid collisions.
- Force-sensing: Some cobots are equipped with force-sensing technology that allows them to 'feel' how much pressure they are exerting. This makes it possible for a cobot and human worker to share tasks like loading and unloading parts from a welding fixture without guarding.
- Simpler programming interface: The new cobots offers another advantage over traditional robots with their more straightforward programming interface. The first mainstream cobot, Universal Robots, changed the industry by providing a graphical, more intuitive interface allowing non-programmers to learn and program robots. This new approach makes automation more accessible than ever to SMBs without robotic teams or expertise.
Combining these design features enables humans and cobots to work collaboratively in close proximity, opening new possibilities for how robots can be used in manufacturing.
Cobot Welding: A New Approach to Automation
Traditional approaches to automation focus on using robots in cells away from human workers. This 'lights-out' automation is typically used in high-volume manufacturing, where the goal is to produce large quantities of parts with minimal human labor.
While this approach can be successful in some cases, it doesn't work for all manufacturing applications, especially for smaller manufacturing companies with high-mix and low-volume productions. In addition, traditional welding robots do not offer the required flexibility or can be costly to do modifications.
In addition, traditional approaches to automation are often cost-prohibitive for small and medium-sized businesses (SMBs). The initial investment in hardware and software can be significant, and the time and effort required to program and maintain the system can be daunting for companies with limited resources.
Considering the present shortage in the welding workforce, SMBs struggle to hire and retain welders. When looking into welding automation to solve this issue, some companies may create another problem by needing to hire robot experts or programmers, which are even harder to hire and retain in this economy.
Welding cobots offer a new approach to automation that overcomes these challenges. Cobot welding systems are designed to complement the human welders you already have. This collaborative approach enables SMBs to take advantage of the benefits of automation without the high cost and complexity of traditional systems or needing to exchange welders for robot programmers.
The Advantages of Cobot Welding During the Labor Shortage
There are several key advantages of using cobots for welding, including:
1. Cobot Welding Helps Empowering the Welders You Already Have
Manufacturing companies are leveraging welding cobots as tools for the welders they already have. Using a welding cobot solution that is simple to learn and set up, they see their welders being able to work with them without any robotic or programming background. This allows them to empower their skilled welders to work on more value-added tasks while having the cobot do repetitive and dull welding tasks.
Welding cobot tools like the Cobot Welder from Hirebotics as proven time and time that anyone without a programming or robotic background can use their proprietary app. This app, called Beacon, only requires the welder to enter welding parameters and position by hand the welding torch at the start and end of the welds - No robot jargon needed!
2. Cobot Welding Can Help You Increase Production Throughput
Businesses that adopt cobot welding technologies can expect to see increased production throughput. By automating specific tasks, companies can free up employees to work on other value-added tasks or projects.
This results in more production with fewer welders allowing the company to focus on growth instead of hiring!
In addition, cobot welding can help to improve accuracy and consistency, resulting in higher-quality products. Moreover, by helping the welder, cobot welding can reduce the time needed to complete a weld by up to 50%.
3. Cobot Welding Requires Less Training Than Traditional Robotic Welding
Due to the simplicity of the cobot welding tools, you can assign their operation to welders or workers who understand welding but could be less experimented with or skilled. Therefore, there is no extensive training needed to fly the worker to a training facility for weeks. Welders are already scarce, and you need them to produce, not spending long weeks in training!
4. Cobot Welding Offers Your Businesses a More Consistent Quality of Welds
Traditional welding methods require a high degree of skill and experience, making it challenging to maintain consistency across a workforce. Cobot welding offers a solution to this problem by providing a more consistent quality of welds. The operator simply teaches the robot what to do, and the robot does the rest, repeatably.
This means that your production can get the same quality welds with less-experienced workers.
5. Cobot Welding Can Attract the New Generation of Welders to Your Business
The welder shortage exists due to more welders retiring than new welders coming out from trade schools. The new generation of workers isn't as interested in trade jobs despite their importance in the economy. The repetitive, dull, and dangerous tasks are not as attractive to them.
Adding welding cobots to your production process can be a way to make your company more appealing to the younger workforce. In addition, they are used to working with their smartphone or computer, so operating a robot could be very attractive to them.
Needless to say, cobot welding systems like the Cobot Welder fit perfectly in the skillset of this new generation with its smartphone app, Beacon.
The Bottom Line
If you're considering adding a welding cobot to your factory floor, one key element is to choose a solution that your welders can learn and operate easily. The business can then use their welders for higher-value tasks harder to automate.
Remember, your welders are the keystone of your automated welding operation - if they're not happy with the new system, it's likely to fail. To ensure a successful installation, take the time to consult with your team and get their feedback on which solution would work best for them. With their input, you can make the best possible decision for your business - and set your welders up for success.
Can your welders REALLY learn our Cobot Welder App and be in production in 1 day? Let us show you how your business can benefit from cobot welding, schedule a live demo of our Cobot Welder today.