Guide to Weaving in Welding: Weave Patterns and Pitch Calculation
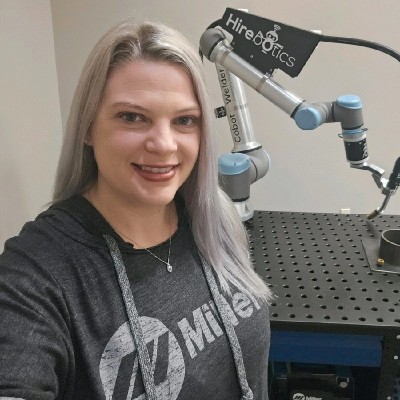
May 20, 2024
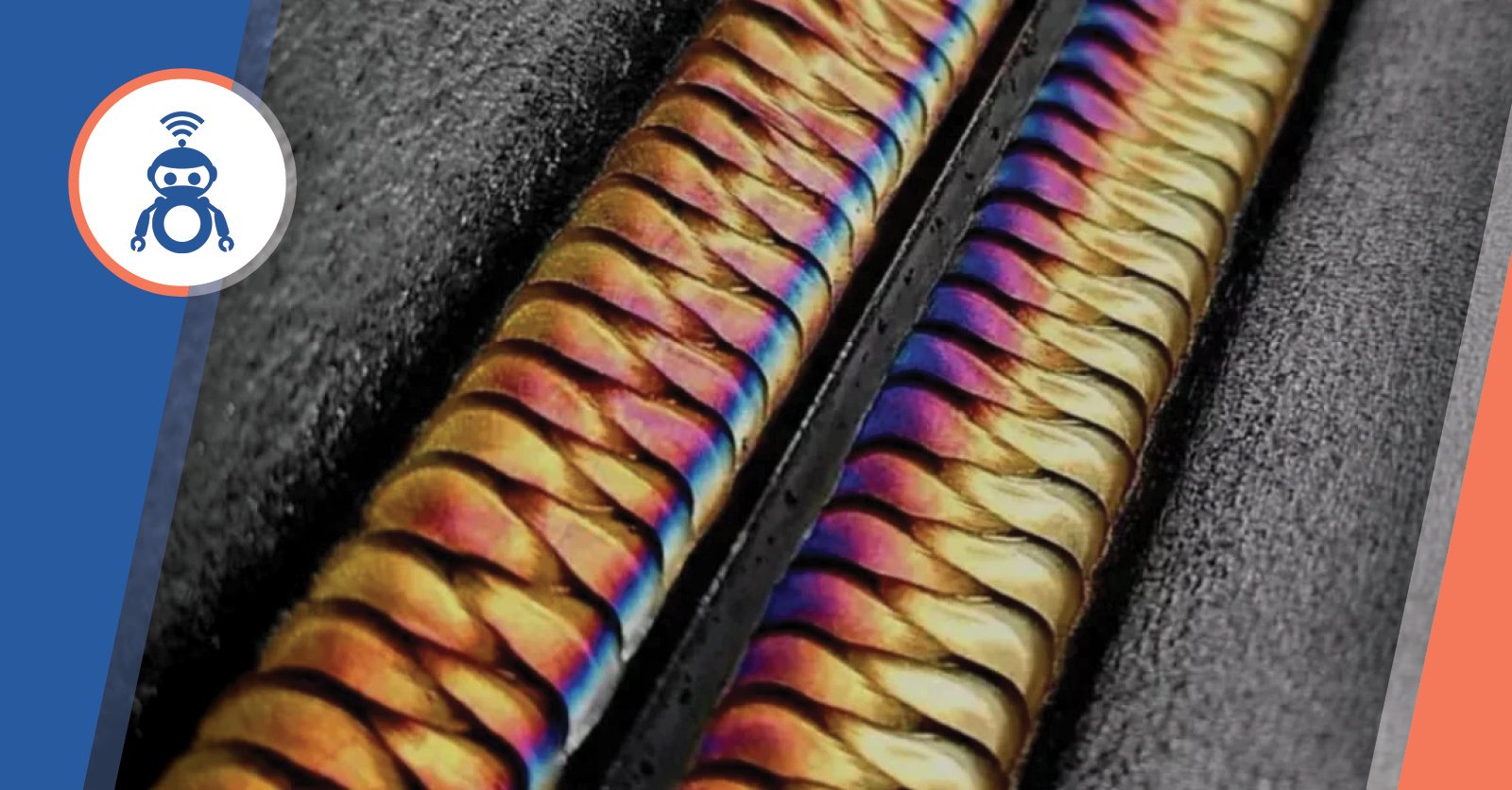
Weave welding is achieved by offsetting the motion of the weld arc as it moves along the weld path, making it ideal for filling wide, flat joints or welding thick metals.
Here are the popular types of weaving patterns:
Table of Contents |
4 Popular Types of Weave Weld
Depending on what you're working with or the challenges you're facing on the job, each weave pattern has its own set of benefits. Below, we break down a few key styles and how you can use them for specific welding tasks.
1. Triangle Weave
The triangle weave is perfect in situations where you need precise control over the weld pool, such as in overhead welding. This pattern allows for a steady build-up and efficient management of heat, which are key when working against gravity.
The side-to-side motion of the triangle weave helps distribute the weld metal evenly, preventing the sagging that can occur with less controlled techniques. It’s ideal for ensuring deep penetration and even filler distribution in challenging welding positions.
Best for:
- Overhead welding
- Thick plate welding
- Controlled heat distribution
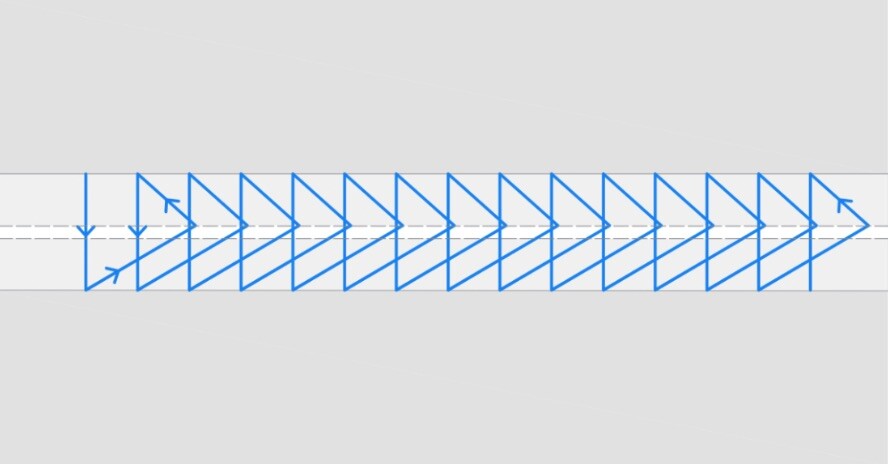
2. In-Line Weave
This technique involves a straightforward back-and-forth motion across the joint. It works well for creating consistent welds over long lengths.
Using the in-line weave ensures a consistent bead appearance. It’s especially useful in scenarios where the length of the weld could lead to inconsistencies without careful technique management.
Best for:
- Aesthetics (similar to TIGS ‘stack of dimes’)
- Long, straight welds
- Flat and horizontal surfaces
- Structural steel projects
3. Circular Weave
The circular weave is a versatile welding pattern suited for a range of applications. It features a circular or looping motion that expertly manages the weld pool, ensuring uniform heat distribution and consistent penetration.
The radius of the weave plays a key role in dictating the heat input. A tight radius leads to deeper penetration while a wider circular motion achieves shallower penetration, which is suitable for surfacing and hardfacing welds. This makes the circular weave a general-purpose technique useful for tasks like horizontal plate butt welding as well.
Best for:
- Pipe welding
- Horizontal plate butt welding
- Even heat distribution
![]() A wide circular radius makes shallow penetration |
|
4. Zigzag Weave
When faced with large gaps or wide joints, the zigzag weave is particularly effective. The back-and-forth motion allows for a large amount of filler to be deposited, which is crucial for maintaining a stable heat throughout the weld and successfully bridging gaps. This technique is invaluable in construction welding, where variable joint sizes and gap widths are common challenges.
Best for:
- Bridging large gaps
- Welding wide joints
- High filler deposition
Importance of Torch Progression
Along with the weave style, the method of torch progression is also important. It significantly influences weld penetration and the overall contour of the bead. Each direction of torch travel brings its own characteristics to the weld, affecting its strength and appearance.
- Forehand direction of travel: When the torch is moved in a forehand direction, the penetration tends to be shallower, resulting in a wider and lower bead contour. This method is often used for applications requiring less depth but greater surface coverage.
- Perpendicular travel: Moving the torch perpendicular to the workpiece achieves deeper penetration. This method produces a bead that is narrower and higher, suitable for joints needing strong, deep welds.
- Backhand direction of travel: Similar to perpendicular travel, the backhand direction also facilitates deep penetration. The bead, however, remains narrow and high, providing robust joint integrity especially in thicker materials.
Understanding these torch progression methods allows welders to tailor their approach based on the specific requirements of the job, improving the performance and appearance of the weld.
What is Weave Weld Pitch & How to Calculate It
Weave weld pitch is the measure of the distance from one point in the weave pattern to the next identical point along the weld seam. This metric is important because it helps control the consistency and quality of the weld, particularly in terms of deposition rate and heat input.
How to Calculate Weave Weld Pitch
Calculating weave weld pitch is pretty straightforward. Here’s a simple way to express it:
Weave Weld Pitch = (Weave Width x Travel Speed) / Number of Weaves per unit |
This calculation will help you determine how spaced out each repetition of your weave pattern should be to maintain a consistent weld. By adjusting the pitch, you can better control the weld pool and achieve the desired characteristics in your weld bead.
Manual Weave Welding vs. Cobot Weave Welding
When performing a weave weld manually, it can be a challenge to maintain a consistent speed. Uneven speeds can lead to poor fusion along the joint edges and at the root, potentially weakening the weld.
On the other hand, cobots don’t have this issue. They are programmed to keep a constant speed and movement.
Robotic systems provide a level of precision and consistency that manual welding often struggles to match, improving the efficiency, quality, and cost-effectiveness of your projects.
Aspect | Manual Weave Welding | Cobot Weave Welding |
Speed | Generally slower due to manual operation, speed is determined by the skill of the welder | Faster, as the robot can maintain the optimal welding parameters to maximize the speed |
Cost | Lower initial cost, higher labor costs over time | Higher initial investment, but lower labor costs, saving rework cost and improving quality |
Setup | Minimal setup required, adaptable on-the-fly | Initial setup and programming needed |
Consistency | Varies depending on the welder’s fatigue and skill level | Extremely consistent, with precise control over weld parameters and weld patterns |
Scalability | Limited scalability for large-scale production | Highly scalable, ideal for large-volume production or HMLV |
Weaving with Beacon
The Cobot Welder with the Beacon app excels at performing both triangle and in-line weave patterns.
With Beacon, the Cobot Welder simplifies what would typically be complex manual setups. It can weld both triangle and in-line weaves, adapting quickly to different project requirements. This flexibility speeds up the welding process and produces high-quality consistent welds.
Create Efficient Weave Welds with Hirebotics’ Cobot Welder
Weave welds play a crucial role in welding, providing better penetration, filler distribution, and overall weld integrity, especially in challenging positions or when dealing with thick materials.
If you are looking for an automated solution that can perform intricate weave welds while maintaining high precision and consistency, then Hirebotics’ Cobot Welder (powered by the Beacon app) is an excellent choice.
Designed to handle both high-volume repetitive tasks and detailed applications, this tool helps improve the efficiency and quality of your welding operations. Any welder can use Beacon and its simple welding language to weld consistent, repeatable parts.
Curious to see the Cobot Welder in action? Book a demo!
Weave Welding Techniques: FAQs
What is the strongest weave welding method?
The strength of a weave weld depends on the application. The triangular weave is considered one of the strongest because it provides consistent heat distribution and penetration. This method is ideal for high-pressure, high-strength requirements.
How wide can you weave a weld?
The width of a weave should generally not exceed three times the diameter of the electrode being used. This guideline helps maintain control over the weld pool and ensures proper heat distribution and penetration. Going wider can lead to defects and inconsistency.
What is the difference between stringer and weave beads?
Stringer beads are run straight along the joint with minimal or no side-to-side motion, primarily used for thinner materials or when heat input needs to be minimized.
Weave beads, on the other hand, involve moving the electrode side to side in a pattern (such as zigzag or circular), which increases the weld's width. A weave bead is beneficial for filling larger gaps and ensuring better fusion on thicker materials.
Why should a weaving motion be used when making horizontal welds?
A weaving motion is recommended for horizontal welds to help control the weld pool, manage heat input, and ensure good fusion and penetration. Weaving helps distribute the heat evenly and prevents sagging, ensuring a more stable and consistent weld bead.
Are there any differences between TIG and MIG welding weave patterns?
Yes, there are.
TIG welding involves tighter, more controlled weaves that are essential for precision and aesthetics, especially on thinner materials or in visible areas. MIG welding can accommodate larger, more aggressive weaves, suitable for thicker materials and where higher deposition rates are needed.