Robotic Welding Programming: Best Practices & Challenges
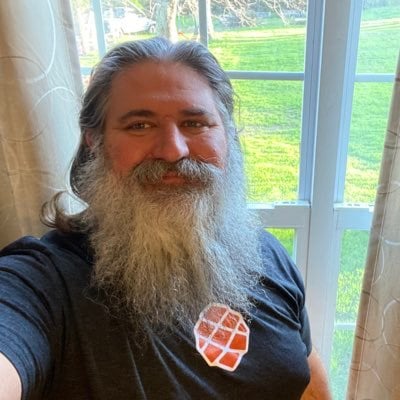
January 29, 2024
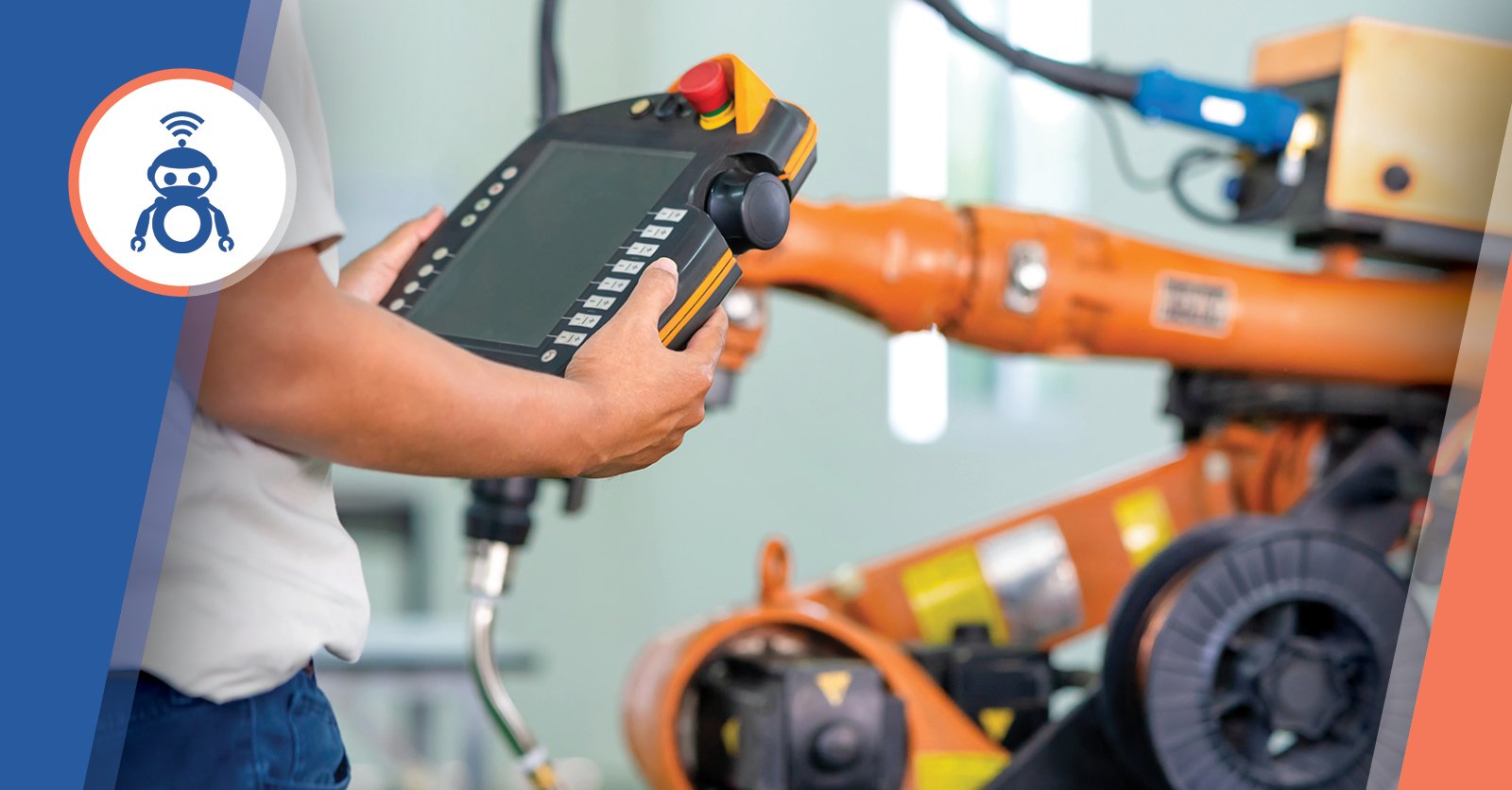
Understanding the do’s and don'ts of robotic welding machine programming might be the most crucial factor in protecting your investment and ensuring the production of high-quality products.
As welding robots become increasingly sophisticated and user-friendly, navigating the world of robotic welding still comes with its share of challenges.
This guide is designed to walk you through the crucial dos and don'ts of robotic welding programming. It will equip you with the insights needed to avoid common pitfalls and elevate your programming.
In this article, let’s discuss:
- Robotics General Best Practices - The Do’s
- Robotics General Best Practices - The Don’ts
- Welding Robot Best Practices - The Do’s
- Welding Robot Best Practices - The Dont’s
- Welding Robot Programming - The Do’s
- Welding Robot Programming - The Don'ts
- Welding Robot Programming: Some Common Challenges
- A New Era for Welding Robot Programming: App-Based Programming
- Frequently Asked Questions
Key Takeaway:
Robotic welding programming is in high demand. It is a blend of two disciplines: welding and programming. The ongoing advancements in robotic welding enhance production and open up avenues for both experienced programmers and new welders to significantly contribute to production efficiency.
Robotics General Best Practices - The Do’s
While robot applications vary by industry, you can apply their general best practices broadly across most robot types. These best practices ensure that you’re prepared, safe, and deploy your welding robot intelligently.
1. Take Advantage of OEM Training
The best advice for end users is to take advantage of the robot manufacturer's training.
Proper training ensures your technicians are prepared to operate and program the welding robot. Even experienced welding programmers can benefit from training.
Every manufacturer has nuances in their software and UI. There can even be differences and updates between models of the same brand.
Exposure to training on your welding robot gives your programmers the confidence to write programs for your robot.
2. Start Slow
Starting new programs slowly is essential for ensuring both safety and performance. Welders should start small and build the program up section-by-section.
Welding robots have step functions that allow you to “step through” the program one function at a time.
This feature, combined with reduced speeds, limits the chance of crashing the robot and damaging peripherals.
3. Design Your Program in Real Conditions
Failure to develop weld robot programs under realistic working conditions can undermine the efficiency and reliability of your welding robot, posing significant challenges.
For example, present the parts as they would in actual production. Factors such as jigs, positioners, clamps, and other equipment should be present.
Programming in these conditions allows welder programmers to catch potential issues before they lead to scrapped parts or damaged components.
Robotics General Best Practices - The Don’ts
Neglected tasks and improper usage are common mistakes made with welding robots. Unfortunately, these mistakes lead to issues that affect worker safety and your bottom line. Let’s look at some common mistakes.
Don’t Forget About Maintenance
Maintenance is often highly-regarded in theory but not nearly practiced enough. Improper attention to welding robot maintenance leads to increased downtime and shortens the lifespan of your equipment. It’s a common refrain to hear manufacturers think about maintenance only after components begin to fail.
Unfortunately, this means that production time and money are already lost on issues that could have been resolved by adhering to a proper maintenance schedule. Every OEM provides a maintenance guide with their welding robot documentation for reference.
Don’t Assume the Cell is Safe
Welding robots are hazardous when operating around people. Even welding cobots–inherently safer alternatives–still threaten people in the vicinity of the work cell. It’s tempting to see the welding robot as predictable and, therefore, less hazardous.
This complacency can lead to mistakes that result in injury. You should undertake proper safeguards to ensure a safe working environment for your employees and equipment.
Don’t Deploy Untrained Technicians to the Weld Cell
Trained technicians should be the only employees to operate welding robots. Additionally, only those qualified should engage in writing its programs. While modern welding robots are user-friendly, they should only be handled by those properly trained.
Welding Robot Best Practices - The Do’s
Neglected tasks and improper usage are common mistakes made with welding robots. Unfortunately, these mistakes lead to issues that affect worker safety and your bottom line.
1. Don’t Forget About Maintenance
Implementing a preventive maintenance program is crucial to protecting your investment. The program should cover the:
- Robot
- Robotic MIG gun
- Consumables
- Cables
- Peripherals
Checking connections, cleaning fixturing, and confirming tool center points can prevent performance issues and keep the system running smoothly.
Maintenance can be scheduled to align with routine production pauses to ensure the system operates within proper parameters.
Improper attention to welding robot maintenance leads to increased downtime and shortens the lifespan of your equipment. It’s a common refrain to hear manufacturers think about maintenance only after components begin to fail.
Unfortunately, this means that production time and money are already lost on issues that could have been resolved by adhering to a proper maintenance schedule.
Every OEM provides a maintenance guide with their welding robot documentation for reference.
2. Don’t Assume the Cell is Safe
Welding robots are hazardous when operated around people. Even welding cobots–inherently safer alternatives–still threaten people in the vicinity of the work cell.
It’s tempting to see the welding robot as predictable and, therefore, less hazardous. Being complacent about safety can lead to mistakes that result in injury.
Proper precautions should be made to ensure a safe working environment for your employees and equipment.
Effective management of the power source, grounding, and wire feeder is necessary, as well as ensuring welders can work safely and consistently with proper ergonomics.
A well-planned layout can support productivity, quality, and cost savings.
3. Don’t Deploy Untrained Technicians to the Weld Cell
Trained technicians should be the only employees to operate welding robots. Additionally, only those qualified should engage in writing its programs.
While modern welding robots are user-friendly, they should only be handled by properly trained individuals.
Welding Robot Best Practices - The Do’s
Welding robots present unique challenges compared to general-purpose robots. Operators and programmers experienced with other robot types should be aware of the new challenges and concepts that welding robots present.
1. Familiarize Yourself with the Teach Pendant
Welding robots come with a device called a teach pendant that OEMs recommend for programming.
While traditional methods of programming still exist, the teach pendant tends to be the easiest and most efficient way to write a basic welding robot program.
The keypad contains many useful functions and shortcuts, such as speed adjustment, torch control, and jog commands.
Components like the live/dead man switch and e-stop are important to practice using to familiarize yourself with their positioning and operation.
2. Create an Arc File Library
Arc start files define the welding parameters for the arc. They should be named thoughtfully so that future robot programmers can identify these files and incorporate them appropriately.
For example, naming a file ‘arc_file_001’ can confuse you and others regarding its contents.
3. Be Mindful of TCP
Proper TCP calibration ensures that your robot moves precisely about the workpiece. The TCP helps create the offset required for the robot program to adjust the tooltip's geometry.
Typically, you define the TCP by jogging the robot to a reference point at several orientations. Once the calibration is complete, you should perform a test to ensure the tool moves smoothly.
Many manufacturers provide a pin that you use as a TCP reference. You will need to redefine the TCP after crashes and tool changes.
Welding Robot Best Practices - The Dont’s
Welding robots present unique challenges to operators and programmers. There are a few common mistakes that lead to damage, production errors, and inefficient operation. Being aware of these mistakes can protect you from making them in your facility.
1. Don’t Assume the Issue is the Program
It’s a predictable reaction to blame production issues on the welding robot program. But, while the programmer can be an easy scapegoat, the underlying problem is rarely the code.
Unless the programmer has made recent changes, there is typically an electrical or hardware issue leading to the malfunction.
Common problems include:
- Improper part presentation
- Broken peripherals
- Faulty grounding
- TCP offset error
- Contact tip wear from burnback
- Inconsistent wire feed
2. Don’t Ignore the Tool Path
A poorly thought-out tool path can affect weld quality and damage the weld tip. Therefore, it’s often advised to pull up and out away from a finished weld before moving to the next position.
This motion helps avoid collisions with curing seams and other surfaces. Additionally, this gives you a proper approach angle for the next weld.
3. Don’t Operate the Robot with Broken Peripherals
Broken or malfunctioning mounts, nozzle cleaners, cable management, and other devices can further damage these components and the welding robot.
Proper maintenance routines should identify broken peripherals and stop or limit production until the component(s) are replaced.
These measures will protect your robot from short-term damage and enhance its longevity thanks to properly functioning peripherals.
Welding Robot Programming - The Do’s
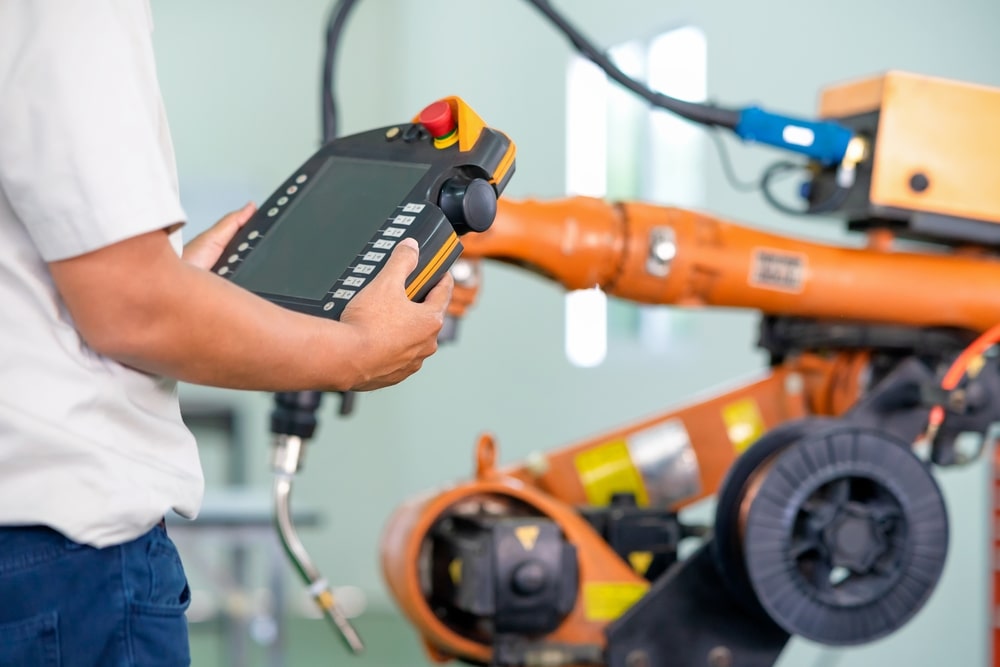
While there may not be a "perfect" way to write a welding program, there are countless improper ways to do so. A few key concepts go a long way in keeping your programs simple, effective, and robust.
1. Keep it Short
The simple programs are often the most elegant. Programming complexity typically leads to future issues that are difficult to debug.
For example, a basic welding program should be no longer than 100-200 lines. Longer programs are likely over-complicated and could benefit from simplification.
Subroutines aid in simplifying complex programs, and comments help you and others understand sections of code. Use both generously.
2. Use Joint, Linear, and Circular Moves Properly
It may seem evident that curved paths require circular moves, and straight lines call for linear moves. However, cleverly applying the proper move type is vital for creating an efficient welding program.
For example, linear movements are precise and useful for most welding paths. The tradeoff for this precision is speed. The robot caps the motor speed to maintain path precision throughout the move.
Using linear moves for much of the non-process motion might unnecessarily increase cycle speed.
Joint moves use less-predictable non-linear motion paths to reach their destination.
These moves are much quicker because the robot finds the fastest path from point a to point b–which, ironically, usually isn’t a straight line.
If a linear move isn’t required for a non-process move, you should probably use a joint move to reduce cycle time.
Welding robot programmers use circular moves to achieve curved motion. A circular move doesn’t need to be a full circle; it can be a small curve or a circle fragment.
Like linear moves, precision is the priority here. So, for non-process moves, a few joint moves will likely be more efficient than a circular move.
3. Be Smart About Your Angles
Think like a welder when writing your welding program. Welders consider factors like weld settings and torch angles to ensure a consistent and quality weld.
As the programmer, you should also think about these concepts during the programming phase. You must combine basic welding concepts with robot programming knowledge to produce high-quality parts.
Lately, forward-thinking companies like Hirebotics have reimagined robotic welding programming by getting away from the robotics aspect of it and focusing on the welding trade.
They offer app-based, process-focused programming interfaces that eliminate the need for an operator or programmer to understand complex robotic programming.
The Beacon provides a step by step process, using easy-to-understand welding terms that any welder can grasp.
Read more in the “A New Era for Welding Robot Programming: App-Based Programming" section below.
Writing a Welding Program - The Dont’s
With the number of factors to consider when writing a robot welding program, there are plenty of opportunities for mistakes and errors. To save yourself from future issues, here are a few concepts to keep in mind.
1. Don’t Ignore Cable Management
Ignoring cable management can be devastating to the robot’s hardware. For example, welding robots require cable harnesses to provide power and consumables to the robot. Depending on your setup, cables can be exposed outside the robot frame.
Writing programs without considering these components opens up possibilities for these cables to be caught by environmental obstacles. This can badly damage your robot and its peripherals, leading to high replacement costs and downtime.
2. Don’t Disregard Speed Settings
Like angle and power adjustments, you should consider speed settings like a welder. Heat input is a function of input power and travel speed.
Because travel speed is a key factor in controlling heat and weld size, it’s an essential consideration during programming.
3. Don’t Create Singularities
Singularities are impossible motion paths created by the mechanical constraints of the robot’s geometry.
Due to the flexibility of welding robot programming, it’s possible to get the robot stuck in a singularity, unable to complete its motion path.
Some singularities can have surprising effects, such as accelerating joint motion temporarily. Be aware of ways your robot can enter a singularity condition to avoid this problematic issue.
Welding Robot Programming: Some Common Challenges
Regardless of industry, robot programming is a highly sought-after skill due to the high demand for talent and the level of expertise required to develop programs for robots.
Welding robots offer unique challenges that must be met to be a successful welding robot programmer.
Combining Welding Knowledge with Programming Skills
The combination of two different areas of expertise is the greatest challenge for welding robot programmers.
Welding robot programming and manual welding are different disciplines that are entirely unrelated. However, the application of robotic welding requires knowledge in both domains.
Working with Multiple Robot Brands
To make matters more complicated, a welding operation rarely maintains only a single brand of welding robots.
As companies expand, demands grow, and business relationships change. Brand A might be phased out for brand B or brand B might be introduced to the plant while brand A is still operational.
These situations place a lot of demand on robot programmers to be flexible in working with multiple robots.
Staying Current with Technological Developments
Developments in robot technology are proliferating at a rapid pace. New hardware components and software tools offer increased performance or new features over their previous counterparts.
New generations of robots have more features and ways to interact with them, and it’s the programmers need to stay up to date with these developments.
Ultimately, it will be the programmer that will be responsible for implementing these new features.
A New Era for Welding Robot Programming: App-Based Programming
Hirebotics thinks outside the box to offer a new way of programming. This approach eliminates the need to be a world-class robot programmer with 20 years of experience.
Instead, we leverage the knowledge that welders already have by providing app-based programming using only welding parameters and standard terminology they are used to.
These features allow welders with little to no programming knowledge to control and program a welding robot.
Traditionally, fabricators had to send their programmer candidates to the OEM training school for weeks in order to get them at a comfortable level of programming.
That meant traveling and lodging expenses on top of the absence of the worker at their facility. These expenses are not necessary nowadays with simpler program systems.
Are you interested in an easier way to program?
Wondering if the Cobot Welder from Hirebotics can weld your part efficiently?
We can help. Let us show you how our robotic welding systems can simplify your programming process and efficiently weld your parts, saving you time and money.
Frequently Asked Questions
How do you program a robotic welder?
Robotic welders are typically programmed in one of three ways:
- Hand-teaching or app-based tools
- Pendant
- Offline programming
The method you use will depend on your experience and how comfortable you are with the equipment.
More straightforward programs and newer programmers might prefer app-based or pendant-based programming tools. These methods are more approachable and are sufficient for most applications.
Offline programming is the most challenging method but offers the most capability for writing complex programs and incorporating CAD models during development.
Which type of path programming is suitable for arc welding?
Weld paths are typically circular or linear depending on the shape of the required weld. Linear and circular paths allow for precise motion along the weld path.
How to adjust a robotic welder?
Robotic welders are adjusted by changing programming parameters. This is typically accomplished with one of these methods:
- Hand teaching or app-based tools
- Pendant
- Offline programming
Weld settings, motion paths, TCP adjustments, and more can be adjusted to achieve the desired performance characteristics.
How to test a program in a welding robot?
Programs are best tested slowly. Most robots have options to step through the program one line at a time. You should reduce the operating speed to safeguard further against crashes. This gives you an opportunity to observe the program for issues.
As you become more comfortable with the results of the test, you can run the full program at reduced speeds until you’re confident that it will perform as expected.
Can anyone program a robotic welder?
Anyone can learn to program a robotic welder! Entry-level options include hand teaching tools, apps like Hirebotics’ Beacon, and teaching pendants. Training programs exist to teach programmers at any level to program a welding robot.
How hard is it to program a robotic welder?
Most traditional robotic welding systems will require a couple of days to weeks of intensive training for someone without experience to master the programming language and functions.
Usually, a new robot programmer or programmer learning a new brand of robots will have to go to the manufacturer’s facility for intensive training.
Modern welding robots feature user-friendly options. New welding cobots are investing in the accessibility and ease of programming of their solution.
Even individuals with no experience can learn to create simple programs within a matter of hours with accessible programming tools and guided instruction.
There has never been a better time than now to learn to program welding robots.
How can I improve my welding robot programming skills?
You can typically find the best resources for robot training from the OEM. Leading brands offer courses year-round and often provide application-specific training.
What’s better: app-based programming, pendant programming, or offline programming?
It all depends on your skill and comfort level with the equipment. More straightforward programs and newer programmers might call for app-based or pendant-based programming tools.
These methods are more approachable and are sufficient for most applications.
Offline programming is the most challenging method but offers the most capability for writing complex programs and incorporating CAD models during development.
What are some more recent developments in robotic welding?
Cobot welders are becoming more prevalent in the industry today for SME’s. They provide a lower cost and more approachable alternative for manufacturers that might not have experienced welding programmers on staff.
What’s your best advice for welding robot programmers?
Back up your files. Programs can be lost for a number of reasons. The best way to protect yourself and the production line is to keep backups (and maybe backups of your backups)! Losing a welding program and having to start over is a very bad day.
By the way, Hirebotics’ Cobot Welder offers handy automatic backups. ;)
Interested in learning how Hirebotics’ Cobot Welder can elevate your welding team’s skills?