9 Plasma Cutting Tips to Get the Best Metal Cuts
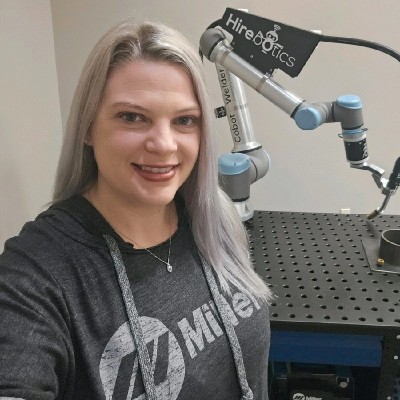
June 10, 2024
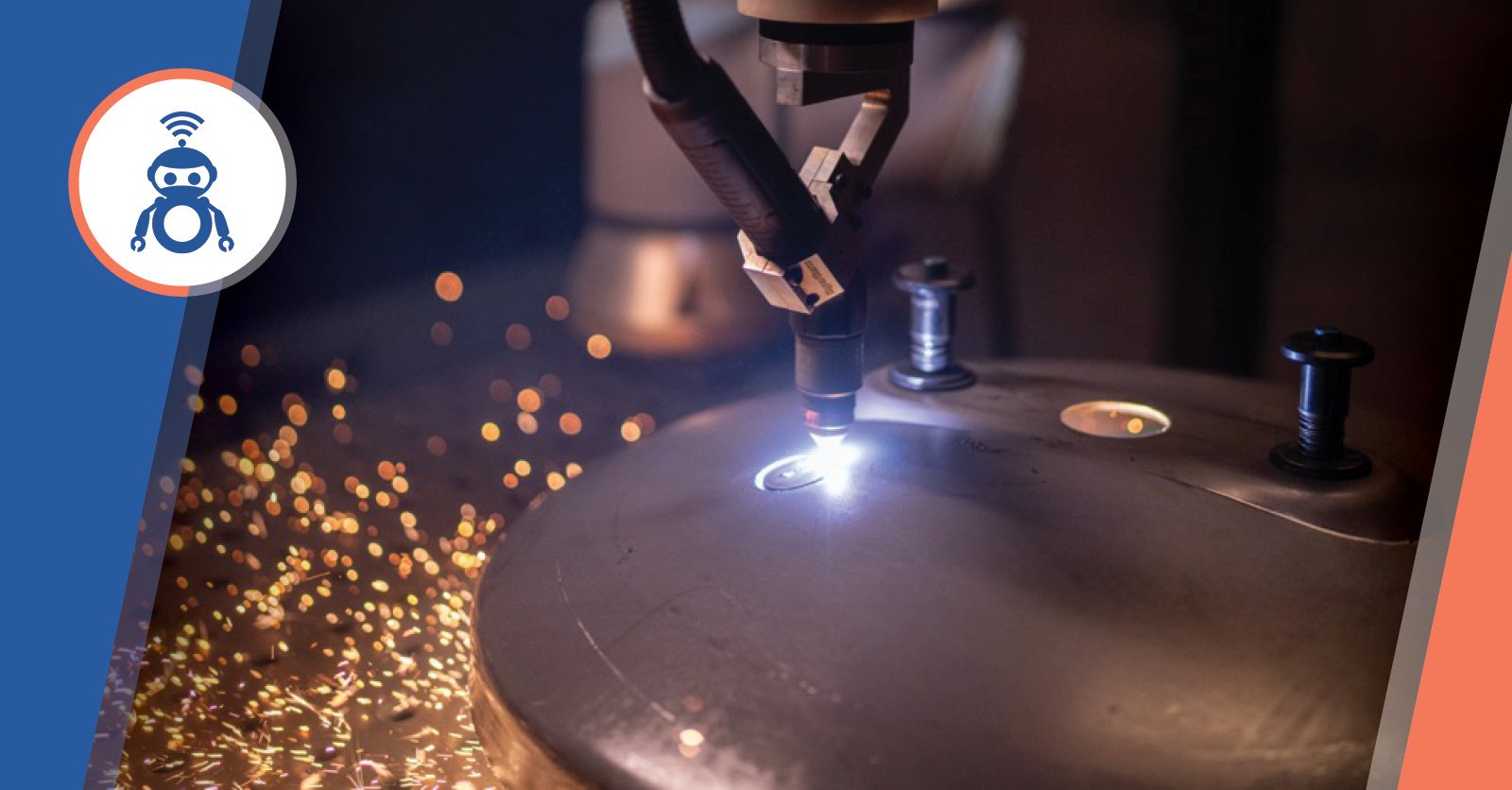
Follow the plasma cutting tips below to improve cut quality, consumable life, and productivity. Plasma cutting can be a bottleneck or the smoothest process in your shop. If you apply the best practices, you’ll improve not just quality but profits as well.
We’ll also show you how to drastically reduce the cut time, all while maximizing the cut quality!
1. Enter Dross-Free Zone With The Right Cutting Speed
Cutting too slow or too fast for the material, thickness, amps, and used gas will cause dross along the cut edge. However, there’s always the sweet spot that maximizes your productivity and sits in the dross-free speed window.
Low-Speed Dross | High-Speed Dross | Dross-Free Window |
The arc grows and widens the kerf, preventing complete metal expulsion. The dross solidifies along the edge. | The arc lags in the kerf and leaves uncut material or rollover dross at the bottom. | Not too fast or slow. Ideally, the arc should lag about 15-30 degrees behind the torch. |
For plasma cutting, you should almost always cut faster, not slower. Of course, not overly fast to negatively affect the cut. As long as you meet the desired cut quality, cutting faster means higher productivity and profits.
It’s tough to maximize your cutting speed if you do it manually compared to robotic plasma cutting. For example, the Cobot Cutter can cut 100+ inches per minute, depending on the thickness. A human can’t reliably apply the same speed, especially not consistently.
With the right speed adjustment, you can use a higher speed than manual cutting and still achieve minimal or no dross for many jobs. This may require some trial and error on test pieces until you find the maximum speed that’s in the dross-free window.
2. Use Adequate Torch Height And Maintain ItTorch height determines the arc voltage. The higher the torch standoff, the higher the voltage. And voltage determines the angularity of the bevel on the cut edge. So, set your torch height according to the plasma cutter cut charts.
But setting the arc voltage/torch height is only half the battle. The torch height must stay consistent along the cut. Otherwise, you’ll get a varying bevel angle.
Material inconsistencies like bumps and warps from transport, distortion from heat, or curvature from corrugated metals can throw off your torch height, causing inconsistencies.
Our smartphone app, Beacon, lets you set the arc voltage for our Cobot Cutter. The cobot senses the arc voltage as it cuts. As soon as it notices any voltage change (height between the metal and the torch), it will auto-adjust to compensate and help achieve a uniform cut bevel.
There are three critical things to consider about plasma cutting kerf:
- Kerf width is a gap where the material is expelled. This material is wasted.
- Kerf compensation must be set accurately for the amperage, material, and thickness. This setting ensures the torch is offset for the kerf gap. Otherwise, your part size will be reduced by the kerf width.
- Plasma torches that use a clockwise swirl air/gas flow (most standard torches) produce a straighter cut on the right side of the kerf relative to forward torch motion. So, adequate torch positioning will help get a cleaner cut on the side that matters—the part side.
Always attach the work clamp to the clean surface of the cut material or working table. Rust, paint, metal oils, and other surface contaminants can impede the electrical flow. This can delay the current transfer by more than 0.5s, worsening consumable wear and causing those frustrating arc starts.
Poor work connectivity can also reduce arc stability and cause intermittent defects along the cut line. If the arc stutters during the cut, you might get an uneven cut. The work clamp connection is the first thing to check if you are having arc issues with a plasma cutter.
5. Use The Right Gas Or Shop AirStandard shop air filtered for moisture is the most economical gas source for plasma cutting. All you need is an air compressor and a filter. Shop air is free, while bottled gasses can be costly, especially when accounting for transportation and safe storage and handling.
Sometimes, you might benefit from specialized gases. For example, oxygen can slightly boost edge quality and speed on mild steel. However, it additionally oxidizes the edge, which can affect weld quality if you must weld the edge. Nitrogen can be beneficial for stainless steel and aluminum for less oxidation and better edge quality. However, using the free shop air provides excellent results for most cutting jobs.
6. Cutting Perfect HolesArguably, holes are the most challenging application of plasma cutting. However, following the best practices outlined below can significantly improve your results:
- Avoid cutting holes with a diameter smaller than the plate thickness. (e.g., a 1/4" plate should have a larger than 1/4" hole diameter). This will help you prevent excessive taper of the cut edge.
- Use the recommended cut height and pierce delay for the plate thickness (check the instructions manual or our plasma cutting settings guide). Since hole cutting typically requires piercing instead of starting on the edge, pierce delay and height are critical to saving consumables from molten metal shooting up the torch tip.
- Sometimes, it can be helpful to start the cut from the center of the hole. This gives the arc enough time to stabilize before getting to the radius and ensures the pierce occurs on the discarded piece.
- It can be beneficial to use lower amp consumables at their maximum amp rating. This will reduce the kerf size (smaller orifice) and produce a finer cut at the expense of speed. Still, with adequate equipment (like robotic cutters), you can maximize the speed, considering that manual cutting typically can’t replicate automated plasma cutting.
Plasma cutting holes is a challenge, but it can be done successfully. For example, Tank Technologies Inc (TTI), a Wisconisn-based water tank producer, uses our Cobot Cutter to plasma cut high-quality holes on curved tank heads, a task not possible with CNC.
Manually Plasma Cut Holes | Holes Cut by Cobot Cutter |
![]() |
![]() |
Cutting holes on a curved surface is significantly more difficult than on a flat plate. Still, our Cobot Cutter easily handles this task. With the right equipment, plasma cutting can be used for nearly any application.
If you always bevel metal with acetylene, you might be wasting resources. Simple bevels on medium-thick plates can be effectively done with adequate plasma cutting equipment. Plasma is faster and less costly than the oxy-fuel process.
8. Use Cutting-Edge TechImplementing the latest tech in your workflow can significantly improve your results and give you the competitive edge other shops may not have.
As two examples, let’s look at advanced consumable technologies and collaborative robots.
Hypertherm’s SmartSYNC technology has changed everything about plasma cutting consumables. Instead of dealing with individual consumable parts, all you need is a single-piece cartridge. This saves time and ensures you aren’t using parts with mixed wear. They are color-coded for easy installation and contain an RFID chip that provides data to the plasma cutter to auto-set the amperage. Likewise, the chip detects end-of-life and gives you data like the number of arc starts and the total arc time over its lifecycle. | ![]() |
Collaborative robots (cobots) are transforming the way many industries work today. Cobots are easier to program than traditional robots, and you can manually guide them by hand. For example, our Cobot Cutter is programmed using a simple smartphone app, Beacon. You can program a cut in less than a minute and learn to use the system in less than an hour. | ![]() |
Skilled fabricators are in short supply, but the demand for production keeps rising. Using the latest technologies helps your existing staff do more with better quality. This improves job satisfaction and might help with employee retention, not to mention higher profits and reduced costs.
If you run a small to medium-sized fab shop, automating repetitive plasma cutting could drastically improve your results.
Manual plasma cutting works well for one-off jobs, cutting on-site, or for jobs where cut quality isn’t critical. However, fab shops producing small to large part batches can drastically improve cut quality and productivity with automation.
CNC is one way to automate, but it requires skilled operators to use CAD/CAM software for programming. Likewise, CNC is limited to cutting 2D shapes, and you can’t quickly (or at all) switch from horizontal to vertical cutting or work in tandem with equipment like positioners.
Cobots optimized for plasma cutting are much more flexible and can cut most geometries. However, not all cobots are equally easy to use. Your team can use our Cobot Cutter, powered by Beacon, from day 1 and they won’t need specialized training.
Your fabricators can quickly program a part batch, have the cobot cut it, and reprogram it for another batch. They can easily repeat this process all day long, producing better parts much faster than manually.
Tank Technology Inc. reduced their plasma cutting time by 94% using our Cobot Cutter! And they nearly eliminated rework compared to manual plasma cutting. Read more in the case study to see the dramatic impact Cobot Cutter had on their business. |
|
Schedule a demo with our team to learn more about Cobot Cutter and Beacon. We’ll help you determine if cobot cutting is suitable for your parts and business and show you just how effective and easy automated cutting can be.