Plasma Cutting Guide: What Fabricators Need to Know
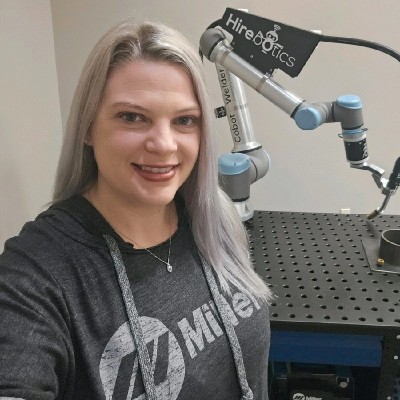
April 22, 2024
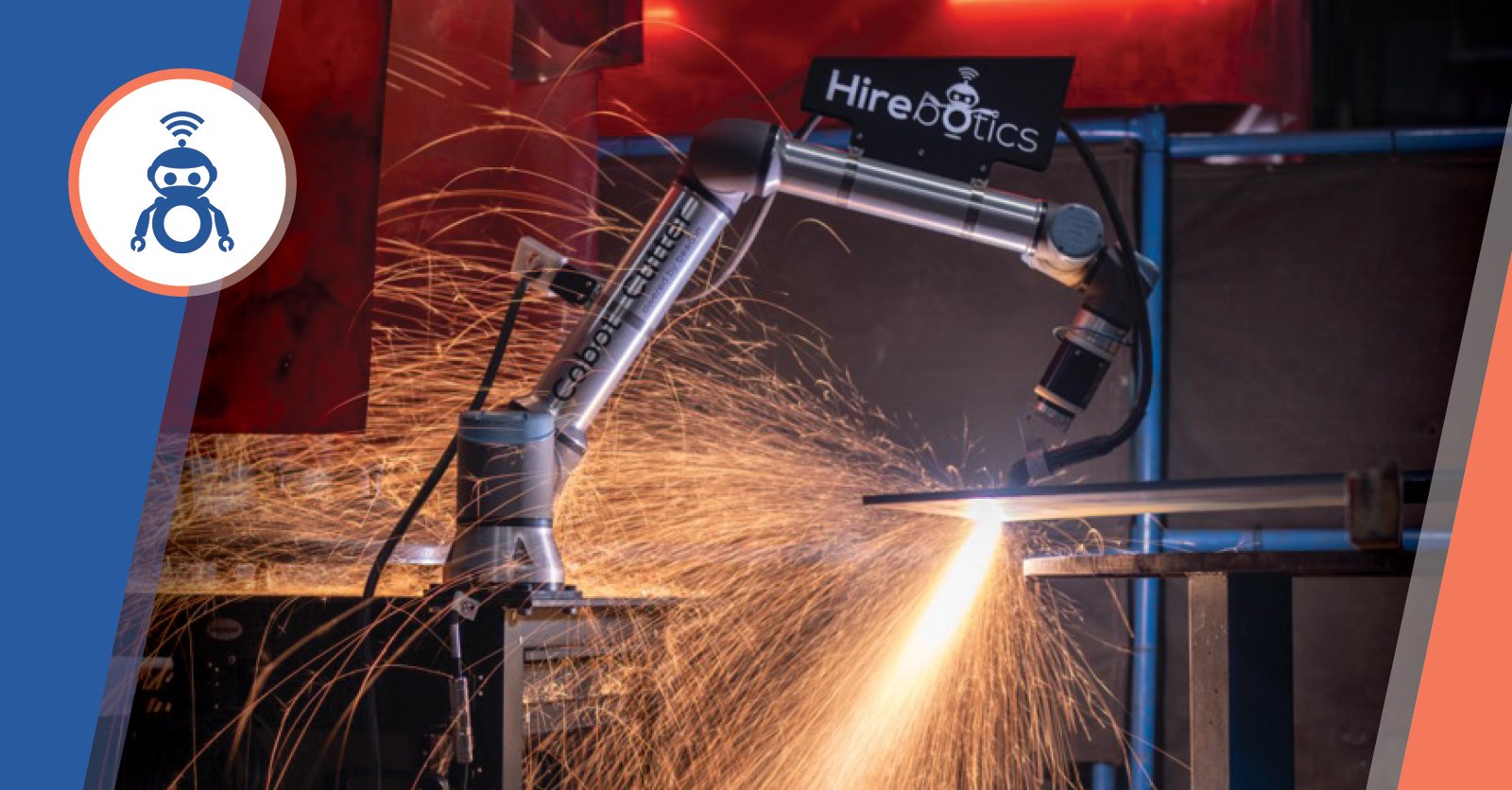
Plasma cutting produces rapid, clean cuts and has highly versatile applications. It’s the most efficient method for precise metal cutting.
You’ll learn everything about plasma cutting in the guide below. But, we’ll also show you how to leverage plasma like never before using extremely simple automation. With the right setup, plasma cutting can produce jaw-dropping results with minimal effort. So, stay tuned!
Table of Content
- What is Plasma Cutting
- How Plasma Cutting Works
- What are the Use Cases of Plasma Cutting
- Why Fabricators Choose Plasma Arc Cutting
- How Much Does a Plasma Cutter Machine Cost
- Plasma Cutting Pros & Cons
- Manual/Traditional Plasma Cutting vs. Cobot Plasma Cutters
- CNC Plasma Cutting Machines vs. Cobot Plasma Cutters
- How Hirebotics’ Plasma Cutters Change The Game
What is Plasma Cutting
The plasma cutting process cuts through metal by using a constricted electric arc under a high-velocity jet of ionized gas. This gas bursts out of a constricted orifice at the tip of the plasma torch. The ionized gas is plasma, the fourth state of matter.
In plain English, plasma is air/gas that has been so heated by an arc that it starts conducting electricity, allowing it to get extremely hot and transfer the arc to the cut piece.
How Plasma Cutting Works
Plasma cutting works on a simple principle: initiate the arc and guide it along the cut line. It’s much like welding, only far easier.
The bulk of plasma cutting comes down to:
- Attaching the ground clamp to the work to complete the circuit
- Using suitable plasma cutting settings for the material and thickness
- Touching the workpiece with the plasma torch, depending on the torch type
- Pressing the trigger to initiate the plasma arc
- Slicing the metal in any direction as you wish
Pro safety tip: Don’t hook the ground clamp to the part of the work to be cut off. That can lead to you becoming the path of least resistance and injury. Likewise, always read all instruction manuals and warning labels.
Plasma Cutting Settings
The most critical plasma cutter settings are amperage, voltage, and torch-to-work distance.
- Amperage defines the arc’s heat and the thickness you can cut. But most importantly, it determines the cutting speed and the cut quality. You can absolutely max out the amps to cut sheet metal, but you’ll have to move extremely fast to avoid distortion and excessive edge loss.
- Voltage defines the “pressure” of the current. Advanced plasma cutters let you modify this setting. It should always be set according to the manufacturer’s specs for the material and thickness.
- Torch-to-work distance (standoff) is adjusted by controlling the voltage and vice-versa. Voltage rises with a higher standoff and reduces with a lower one. Voltage and torch-to-work distance determine the bevel angle of the cut part, an important aspect of part quality.
Arc Starting Methods
There are three types of plasma arc-starting methods:
- High-Frequency (HF) non-pilot arc start is often used by low-cost systems. It works well for manual plasma cutting but can cause problems with CNC and other sensitive equipment. HF current causes the electricity to spark between the electrode and the nozzle, initiating the arc.
- HF pilot arc works similarly to HF start. However, it provides a pilot arc that lets you run through any surface impurities as you transfer the arc from the torch to the workpiece.
- Mechanical blowback arc also offers the pilot arc but without the HF current. It’s used by advanced plasma cutting equipment for CNC and similar applications. Here, the air/gas forces the shorted electrode (-) to separate from the nozzle (+), causing the electricity to jump between the two, initiating the pilot arc.
Plasma Torch
Plasma cutting torch consists of the body and consumables (swirl ring, electrode, nozzle, shield/deflector, and o-rings). Torches can be air or water-cooled (above 100A).
You should use consumables and the torch rated for the used amperage. Otherwise, you’ll experience poor cut quality and significant consumable wear. Some torches are designed for dragging over the work surface, but most require setting the standoff and voltage for mechanized cutting. For manual plasma cutting, you can maintain the standoff with a mechanical guide.
Compressed Air or Gas
Plasma cutting requires an air compressor or a compressed gas cylinder to sustain the plasma arc. You can’t run a plasma cutter without gas.
It’s the most cost-effective to use your shop air compressor. Air produces good cut quality on mild steel, stainless, and aluminum. However, you must filter the shop air to remove oils, moisture, fine dust, and other contaminants that can affect consumables and cut quality. Air can cause oxidizing and nitriding of the cut surface, which can lead to porosity when welding such plasma cut joints. However, a welding wire with deoxidizers, like the AWS ER70S-4 or ER70S-6 for mild steel, can solve this issue for the most part.
Specialized gasses like oxygen, hydrogen, nitrogen, argon, and their mixtures are used to achieve higher cut quality and consumable life.
What are the Use Cases of Plasma Cutting
Some of the most suitable tasks for plasma cutting are:
- Gouging and material removal
- Demolition and decommission jobs
- Cutting wire mesh and extruded metals
- Cutting all electrically conductive metals
- Flush cutting and removing nuts and bolts
- Manual, mechanized, and automated cutting
- Cutting and beveling plates, sheet metal, and pipes
- Marking bend lines, inventory numbers, or reference points for robotic processes
Industries that rely on plasma cutting:
- HVAC
- Mining
- Energy
- Shipbuilding
- Construction
- Bridge building
- Transportation
- Petrochemical
- Auto-body repairs
- General fabrication
Why Fabricators Choose Plasma Arc Cutting
Fabricators choose plasma cutting for its extreme versatility and low cost of use. Compared to oxy-fuel, plasma is leaps ahead. Even compared to waterjet and laser, plasma has cost and efficiency advantages.
1. Excellent Cut Quality And Versatility
Plasma cutters are incredibly versatile. They cut thick, thin, and anything in between. As long as it’s conductive, they’ll cut it. And with the right setup, you can achieve phenomenal cut quality and productivity.
Manual plasma cutting produces good results. But automated solutions, like cobot plasma cutting, make exceptional cuts with minimal heat-affected zone (HAZ), distortion, edge oxidation, and other negatives.
For example, Tank Technology Inc. is an employee-owned ASME code shop that produces pressure vessels, heat exchangers, and water heaters. They have drastically improved their productivity and cost-effectiveness by switching from manual plasma to our Cobot Cutter. Of course, producing ASME vessels is among the most challenging things a shop can do, further proving just how useful an automated plasma cutting process is for fabricators.
Remember those jaw-dropping results we promised? Our Plasma Cutting Cobot has helped Tank Technology Inc. achieve remarkable improvements, including:
- Reducing production cycle time per tank head from 3 minutes to just 11 seconds
- Going from 1 set of consumables per day to 2-3 sets during 3-4 months
- Removing bottlenecks in the plasma cutting process
- Reducing the rework rate from 25% to almost zero
- Enabling accurate cuts on curved tank geometry
- Drastically reducing heat input
- Beveling plates with a cutter
- Increasing repeatability
2. Low Cost And High Production Speed
Plasma cutting systems are less costly than laser or waterjet. Plasma running costs are also lower, and it usually cuts faster. For most fabrication jobs, plasma cutters are a no-brainer cost-effective solution, especially when automated.
3. Safe Cutting Process
Plasma cutting is relatively safe. However, arc, electricity, fire, fume, and burn hazard prevention must be followed. Still, plasma cutting safety is straightforward and can mostly be handled by a single person.
Oxy-fuel, for example, is far more dangerous and has a higher potential for a disaster. A failed flashback arrestor can easily lead to a fuel tank explosion, while plasma cutters can’t cause such severe hazards.
How Much Does a Plasma Cutter Machine Cost
High-quality, portable plasma cutting machines cost several thousands of dollars, depending on their power. However, powerful, industrial plasma cutters can cost upwards of $30,000. You can do most fab shop jobs with a $3000-$8000 plasma cutter.
Plasma Cutting Pros & Cons
Pros |
Cons |
|
|
Manual/Traditional Plasma Cutting vs. Cobot Plasma Cutters
Manual plasma cutting is excellent for non-repeatable tasks where cut precision isn’t vital. Likewise, hand plasma cutting is more portable and requires less space.
Cobot cutting is significantly better for repeatable, low-volume/high-mix precision parts. Jumping from manual to cobot plasma cutting is like switching from a worn-down car from the 90s to a brand-new Ferrari. It’s incomparable. You get drastically better edge quality, far lower heat input, reduced consumable use, higher cut speed, and ultimately, a dramatic boost in productivity.
Remember the case study we mentioned earlier? From 3 minutes to 11 seconds per cut.
CNC Plasma Cutting Machines vs. Cobot Plasma Cutters
CNC plasma cutting can be an invaluable tool for shops that produce high-volume parts. It’s precise and offers excellent productivity. However, CNC requires programming the cut path using complex CAD software and isn’t as flexible as a cobot mounted on a table.
Cobot plasma cutters are much easier to operate and make more sense for high-mix/low-volume cutting. Cobots also offer cut geometry that’s usually impossible with CNC. For example, Tank Technology Inc. considered CNC, but due to the curvature of the water tank, our cobot plasma cutter was a much better option.
How Hirebotics’ Plasma Cutters Change The Game
Today, cobots are more popular than ever before. But they aren’t all exactly “easy-to-use.” Hirebotics Cobot Cutter and our Beacon robot programming software actually make cobot cutting as simple as manual cutting, only far more precise and productive.
With manual plasma, you just take the torch and start cutting. Beacon makes it as easy but with a cobot. No coordinate systems. No math. No confusing non-fabricating stuff. Learn more about our Cobot Cutter and schedule a no-obligation call with our team to see how our cobot solutions can help your shop get to the next level.