Exploring New Welding Technologies and Trends
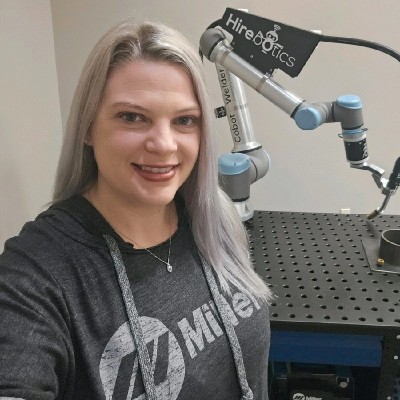
June 14, 2024
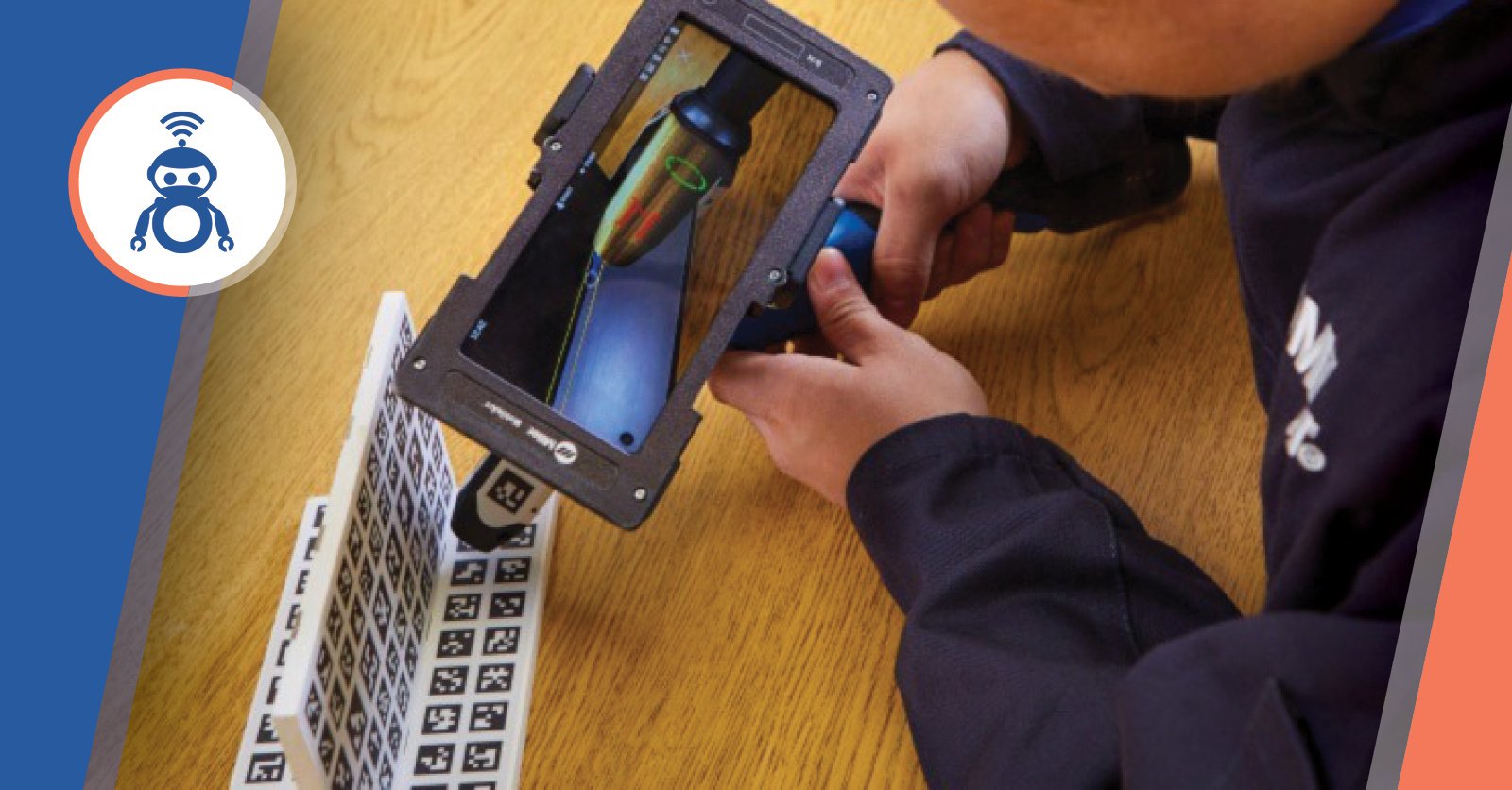
How can you stay competitive in an industry that's constantly evolving with new technologies? It feels like every time you turn around, there's a new tool or technique to make welding faster, safer, and more efficient.
This article takes a closer look at the latest welding technologies and trends that are shaping the future of the industry. Let's look at what's new and what's next in the world of welding.
Table of Contents |
Robotic Welding Technology
Robotic welding is continuing to change the welding industry, offering precision and consistency that human welders can't always achieve.
Robotic welding involves using programmable robots or cobots to automate the welding process. These robots handle repetitive tasks, reducing human error and increasing productivity.
Latest Advancements
Advancements in automation and AI integration have significantly improved the capabilities of welding robots. Modern systems can now adapt to different welding conditions in real-time, and make adjustments to ensure optimal weld quality.
For instance, AI-powered vision systems allow robots to "see" and analyze the weld pool, adjusting parameters in real-time.
The impact of robot and cobot welding on productivity and quality is profound. According to industry forecasts, the global robotic welding market is expected to grow to $10 billion by 2026. This growth is driven by the need for higher efficiency and the ability to produce high-quality welds consistently.
Companies adopting robot and cobot welding technologies often see significant improvements in their production processes, with reduced downtime and lower defect rates.
Augmented Reality in Welding
AR overlays digital information onto the real world, creating a mixed reality experience that enhances the training and operational processes in welding.
Applications
AR is primarily used in two key areas:
- Training: AR systems, such as Miller Electric’s AugmentedArc® and MobileArc™, simulate real-world welding scenarios. These systems provide trainees with a hands-on experience without the need for consumables like metal, gas, or wire. Trainees can practice various welding techniques, such as MIG, TIG, flux-core, and stick welding, in a controlled, safe environment. This reduces training costs and improves skill acquisition.
Source: Miller - Link 1 | Link 2
- Operations: In the field, AR can provide real-time guidance to welders, helping them perform complex welds with greater precision. By overlaying welding instructions and real-time feedback onto the welder’s field of view, AR helps maintain consistency and quality in welding operations.
Benefits of AR
- Improved training efficiency: AR significantly reduces the time required to train new welders. Systems like the AugmentedArc give trainees immediate feedback on their techniques, allowing them to correct mistakes and refine their skills faster than traditional methods.
- Cost savings: By minimizing the need for physical materials during training, AR reduces the costs associated with welding education. This includes savings on metal, gas, and other consumables, as well as reducing wear and tear on equipment.
- Better learning experience: AR provides a safe and engaging way for trainees to learn. They can practice repeatedly without the risks associated with live welding, which builds confidence and competence.
According to industry professionals, the integration of AR into welding education can bridge the gap between theoretical knowledge and practical skills, making the transition from classroom to real-world applications smoother and more effective.
Personal Protective Equipment Innovations
Personal Protective Equipment (PPE) is vital for ensuring the safety of welders. Proper PPE helps prevent burns, eye injuries, and respiratory issues, ensuring welders can work safely and efficiently.
New Developments in Welding PPE
- Advanced helmets: Modern welding helmets feature auto-darkening filters that adjust the lens shade in response to the welding arc, providing continuous eye protection without needing to lift the helmet. Some helmets include integrated LED lights to improve visibility in low-light conditions and connectivity to mobile apps for real-time monitoring and diagnostics.
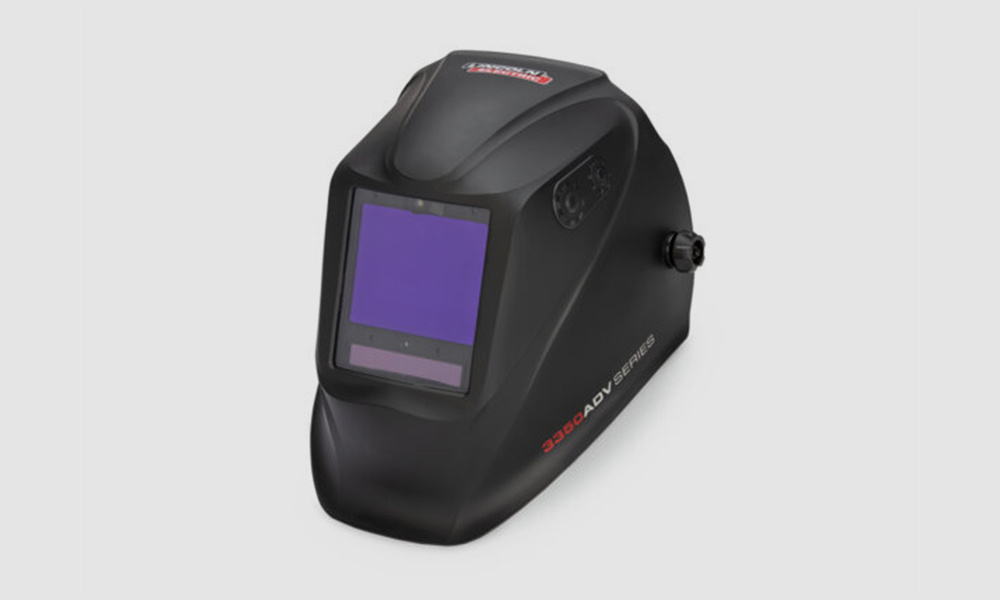
Source: Lincoln Electric
- 3D glove design: Innovations in glove design have led to the creation of gloves that offer a better fit and greater dexterity. With pre-curved fingers these gloves conform to the natural shape of the hand, reducing fatigue and improving precision during welding tasks. Made from advanced materials, they provide better heat resistance and durability.
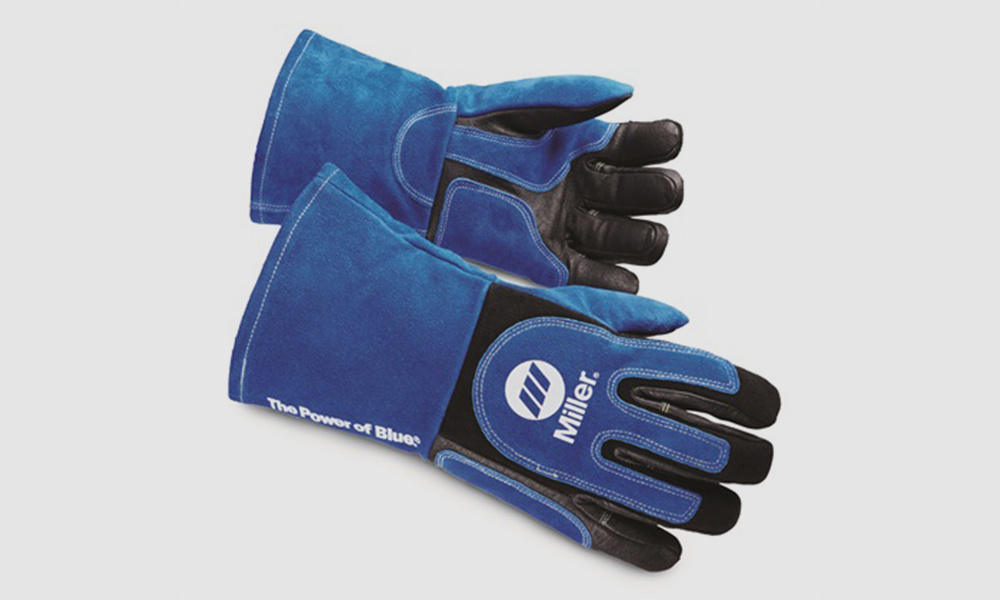
Source: Miller
- Protective clothing: New materials and designs offer improved heat and flame resistance while remaining lightweight and breathable. These garments provide better protection without compromising comfort, allowing welders to move freely and stay cool.
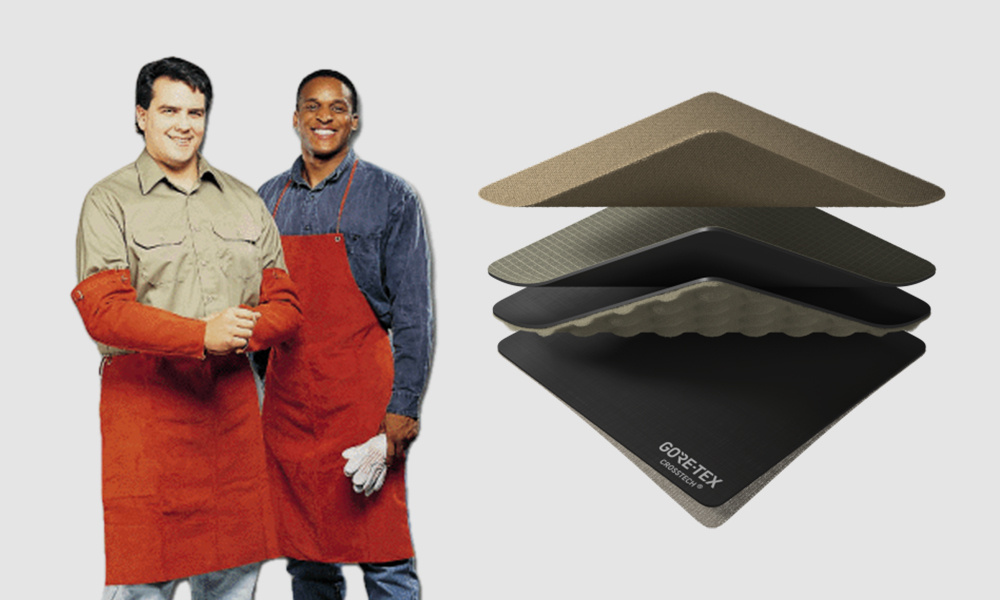
Sources: Conney & Gore-Tex
Welding PPE has come a long way. It is more effective and comfortable, allowing welders to perform their tasks with greater confidence and precision.
Sustainable Welding Practices
As environmental concerns become increasingly pressing, the welding industry is embracing sustainable practices to minimize its environmental footprint.
Sustainable welding is not just about compliance with regulations but also about contributing to global efforts to conserve resources and reduce emissions.
Implementing green initiatives in welding can lead to significant environmental and economic benefits.
Sustainable Techniques and Materials
- Fume extraction systems: These systems capture and filter harmful welding fumes, which contain particulates and gases that can be detrimental to both human health and the environment. Modern fume extraction systems, such as those from Lincoln Electric and Miller Electric, use high-efficiency filters to remove contaminants from the air, significantly improving air quality in welding environments.
- Recycling metals: Using recycled or reclaimed metals reduces the demand for new raw materials, conserving energy and resources. More people in the industry are using reclaimed steel and aluminum, supporting a more sustainable supply chain.
- Eco-friendly supplies: The use of eco-friendly welding supplies, such as water-based flux and electrode coatings, minimizes the environmental impact. These materials break down naturally, reducing the accumulation of hazardous waste.
New Welding Equipment and Tools
Advancements in equipment and tools have improved efficiency and quality in welding processes. Here are some of the latest innovations:
- 3D printing and additive manufacturing: Combining 3D printing with traditional welding techniques opens up new possibilities for custom fabrication and rapid prototyping. This combination is particularly beneficial in the automotive and aerospace industries, where intricate designs and high precision are required.
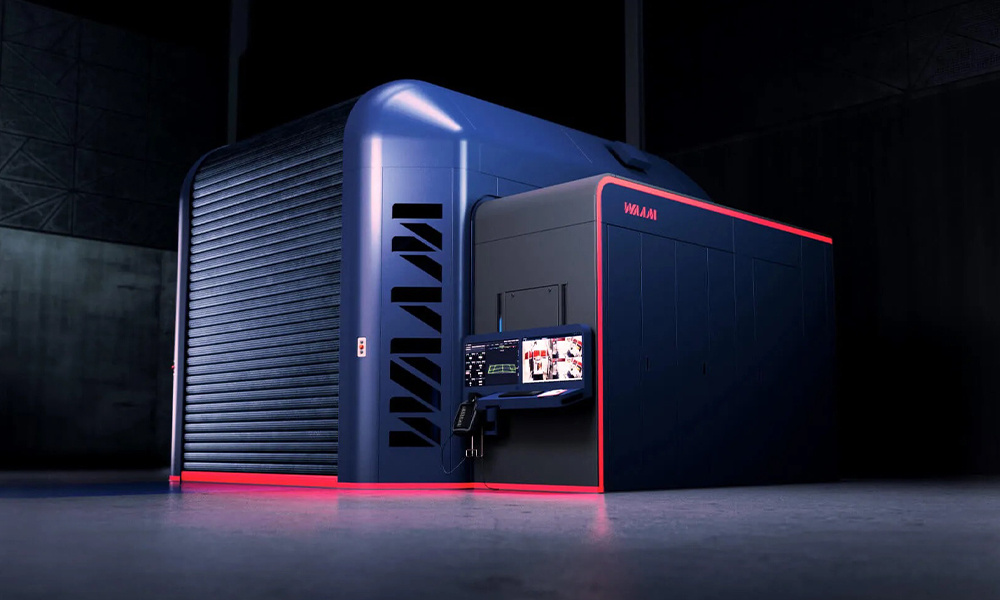
Source: WAAM
- IoT and data analytics: The use of IoT devices and data analytics in welding equipment allows for better monitoring and quality control. These technologies provide real-time data, allowing welders to make immediate adjustments and perform predictive maintenance to reduce downtime and extend equipment lifespan.
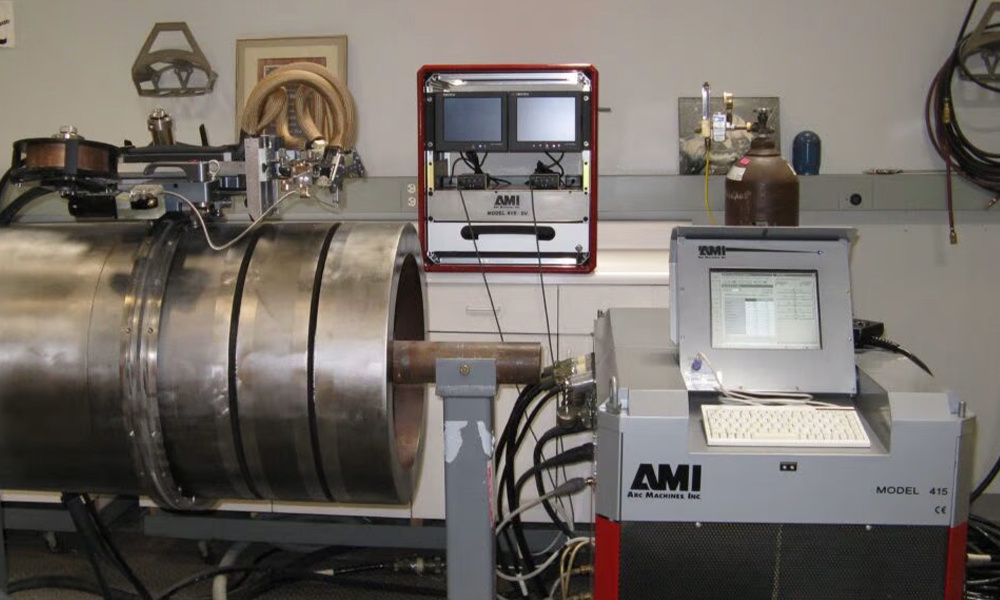
Source: AMI
Embracing the Future of Welding
It is an exciting time to be in the welding industry! The advancements in welding technology are driving the industry toward better efficiency, improved safety, and greater sustainability.
Although these new innovations are becoming more accessible, some welding cobot, like the Cobot Welder, can solve your production problems. No new technology needed. At Hirebotics we believe in making automation simple. The Beacon App makes automation accessible to everyone. It eliminates the need for complex programming and simplifies the adoption of this exciting technology. |
Would you like to see how cobots can transform your welding operations? Download our free EBook, "Ultimate Guide To Getting Started With Welding Cobots".
This guide will walk you through the benefits of welding with a cobot and how to seamlessly integrate them into your processes. Download your EBook and start your journey toward innovative welding solutions with Hirebotics.