Industrial Automation: Your Solution to Labor Shortages
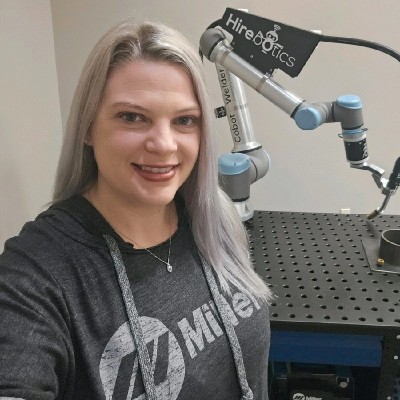
June 3, 2024
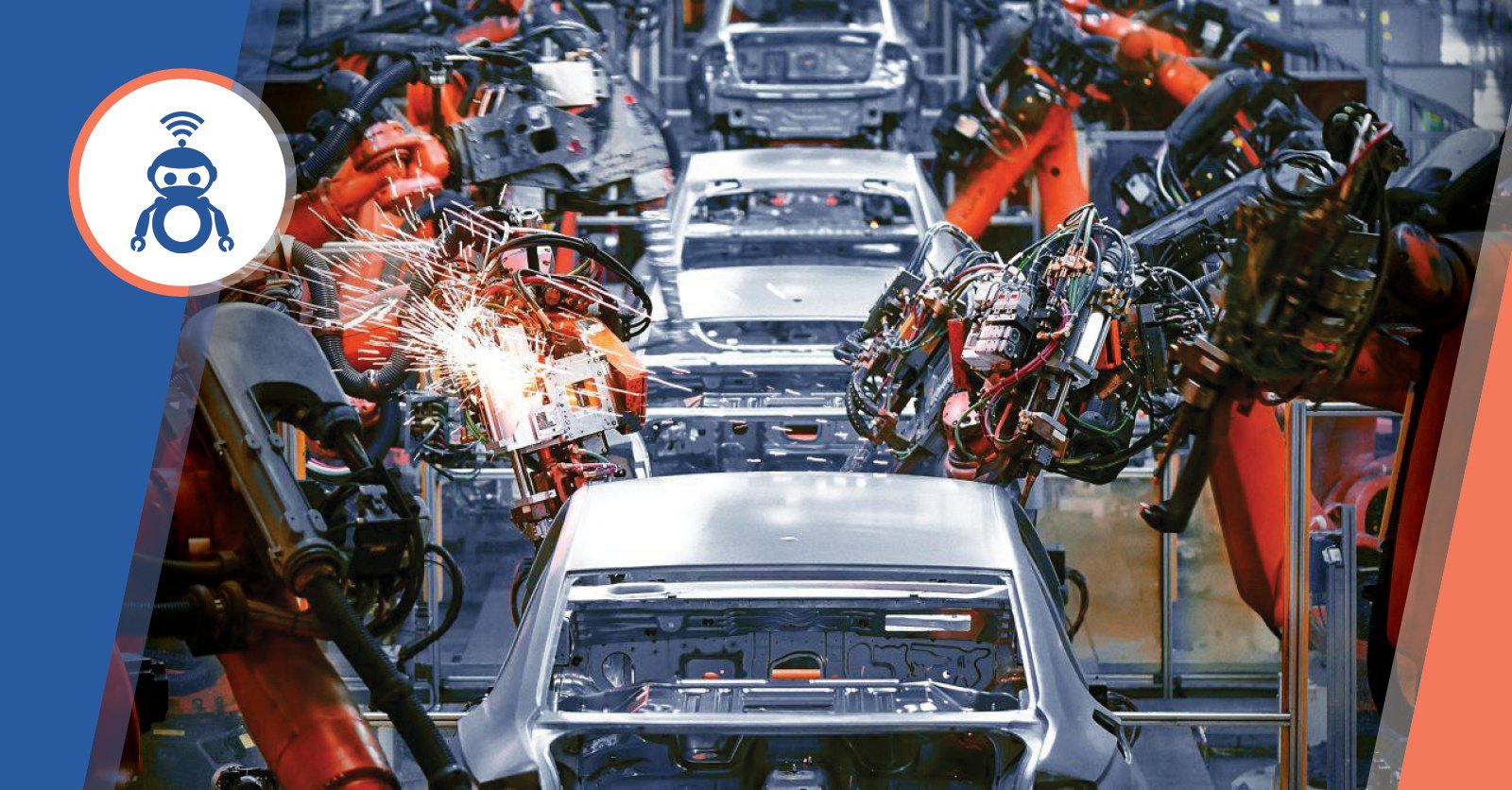
“By 2030, the manufacturing industry will need to fill 4 million jobs, 2.1 million of which could go unfilled if we do not inspire more people to pursue modern manufacturing careers… The cost of those missing jobs could potentially total $1 trillion in 2030 alone.” - The Manufacturing Institute and Deloitte
This prediction highlights the critical labor shortage many manufacturers are facing today. To stay competitive, they need to find innovative ways to meet production demands and maintain quality.
Industrial automation has become an effective strategy for manufacturers facing this challenge. By implementing advanced technologies, manufacturers can streamline their processes, cut costs, and improve product quality.
In today's competitive manufacturing landscape, automation isn't just an option—it's a necessity.
Table of Contents |
What is Industrial Automation?
Industrial automation refers to the use of control systems, such as computers and robots, and information technologies for handling different processes and machinery in an industry to replace human intervention.
It encompasses a wide range of applications, from manufacturing and production to quality control and material handling.
Benefits of Industrial Automation
- Improved productivity: Automation optimizes processes and reduces downtime. Automated systems can operate 24/7 without breaks, ensuring consistent production rates and improving overall productivity. For example, automated assembly lines can produce goods faster and with fewer errors than manual lines.
- Cost reduction: One of the most compelling benefits of automation is cost savings. By reducing the need for manual labor, companies save on wages, benefits, and other labor-related expenses. Automation also minimizes waste and reduces operational costs through more efficient use of resources.
- Improved quality: Automated systems provide consistency and precision in manufacturing processes. They perform tasks with high accuracy, reducing the variability and errors associated with human workers. This results in higher quality products and fewer defects.
- Safety: Robots and automated systems can handle dangerous materials and work in environments that are unsafe for human workers, improving overall workplace safety.
- Flexibility: Automated systems quickly adapt to new tasks and products. They can be reprogrammed and reconfigured to handle different processes, making it easier for manufacturers to adjust to market changes and new production requirements.
Types of Industrial Automation
To be able to select the right system for your manufacturing needs, you need to understand the different types of automation available.
Let's look at the four main types: fixed automation, programmable automation, flexible automation and integrated automation.
Fixed Automation
Also known as hard automation, it refers to systems where the sequence of processing operations is fixed by the equipment configuration. This type of automation is designed for high-volume production with dedicated equipment. It's ideal for repetitive tasks and mass production.
Examples and Use Cases
- Automotive assembly lines: Car manufacturers use fixed automation for tasks like welding, painting, and assembly. These processes require precise, repetitive operations at high speeds.
- Bottling plants: Fixed automation is used in the beverage industry to fill, cap, label, and package bottles.
Programmable Automation
Used for batch production where the sequence of operations can be changed to accommodate different product configurations. The equipment can be reprogrammed to handle various tasks, making it more flexible than fixed automation.
Examples and Use Cases:
- CNC machines: Computer Numerical Control machines can be programmed to create different parts with various specifications.
- Robotic welding: Robots can be programmed for different welding tasks, making them suitable for medium-volume production runs.
- Programmable Logic Controllers (PLC): PLCs are digital industrial computer control systems that carry out automatic operations in industrial processes. They continuously monitor and receive information from input devices or sensors, process the information, and trigger connected output devices to complete tasks.
Flexible Automation
Also known as soft automation, it is the most adaptable form of automation. It allows for quick changes in product design and production processes without significant downtime. This type of automation is ideal for industries with low to medium-volume production who produce a variety of products.
Examples and Use Cases
- Automated Guided Vehicles: AGVs are used in warehouses to transport materials. They can be easily reprogrammed to handle different routes and tasks.
- Flexible manufacturing systems: These systems are suitable for manufacturing environments that frequently change product designs as they can produce a variety of items without significant reconfiguration.
- Human Machine Interface (HMI): An HMI is a software application that allows interaction and communication between a human operator and the machine, translating complex data into accessible information for better control of the production process.
Integrated Automation Systems
These systems employ advanced technologies such as CAD software, robotics, and computer-controlled machinery to streamline tasks typically performed by humans.
They improve production by combining independent equipment, processes, and data into a unified, synchronized operation.
By automating complex processes, IAS improves efficiency, accuracy, and overall productivity. Additionally, IAS can provide real-time monitoring and predictive maintenance, reducing downtime and extending equipment life.
Examples and Use Cases:
- Smart factories: In smart factories, various automated processes and equipment work together in a cohesive environment. This integration boosts efficiency, reduces downtime, and minimizes human error.
- Industry 4.0 implementations: IAS are central to Industry 4.0, utilizing IoT devices and advanced software to create a fully connected production system. This allows for real-time data exchange and flexible manufacturing processes.
- Supervisory control and data acquisition: These systems control and monitor industrial processes by acquiring and processing real-time data from devices like sensors and PLCs.
- Distributed control systems: A central monitoring network that interconnects devices to control different elements within an automated system.
Current Trends in Industrial Automation
The field of industrial automation is evolving rapidly, driven by advancements in technology and changing market demands. Here are some of the most significant trends shaping the future of automation.
Industry 4.0 and the Internet of Things (IoT)
Industry 4.0 represents the fourth industrial revolution, characterized by the integration of digital technologies into manufacturing processes.
IoT plays a crucial role in this transformation by connecting machines, devices, and systems to collect and exchange data. This connectivity allows real-time monitoring and predictive maintenance, ultimately improving efficiency and productivity.
Industry 5.0 (Human-Tech Collaboration)
While Industry 4.0 focuses on automation and data exchange, Industry 5.0 emphasizes the collaboration between humans and technology.
This trend aims to combine the precision of machines with the creativity and problem-solving abilities of humans.
In Industry 5.0, robots and cobots work alongside human workers to improve productivity and create a more flexible manufacturing environment.
Artificial Intelligence and Machine Learning in Automation
AI and machine learning are transforming industrial automation by allowing machines to learn from data, adapt to changes, and perform complex tasks.
These technologies improve the efficiency and accuracy of automated systems, allowing for advanced applications such as predictive maintenance, quality control, and autonomous decision-making.
Human-Robot Collaboration (Cobots)
Cobots are designed to work safely alongside human workers. Unlike traditional industrial robots, cobots are equipped with sensors and advanced programming that allow them to operate close to humans without extensive safety measures.
This trend is particularly beneficial for small and medium-sized enterprises that need adaptable and cost-effective automation solutions.
Sustainability and Green Manufacturing
Sustainability is becoming a key focus in industrial automation as manufacturers strive to reduce their environmental impact.
Green manufacturing practices involve using energy-efficient technologies, reducing waste, and implementing sustainable supply chain practices.
Automation plays a significant role in achieving these goals by optimizing resource use and minimizing emissions, resulting in more sustainable production processes.
Specific Applications and Use Cases
Industrial automation has resulted in streamlined processes and improved product quality across many industries. Here are some specific applications and use cases.
Manufacturing Automation
- Robotic Welding: Robotic welding integrates automated welding systems into manufacturing processes to improve precision, speed, and consistency. These robots can perform various welding techniques, including MIG, TIG, and spot welding, which are ideal for automotive, aerospace, and metal fabrication industries.
- Assembly Lines and Production Systems: Automated assembly lines use robotics and conveyor systems to perform repetitive tasks with precision and speed. This reduces human error and increases production rates. For example, automotive manufacturers use automated systems for tasks such as welding, painting, and assembling components.
- Quality Control and Inspection Automation: Automated quality control systems use cameras, sensors, and AI to inspect products in real time. These systems can detect defects that might be missed by human inspectors, ensuring higher quality standards. For instance, electronics manufacturers use automated inspection to ensure circuit boards are free from defects.
Material Handling and Logistics
- Automated Guided Vehicles: AGVs are used to transport materials within factories and warehouses. They navigate using sensors, lasers, and cameras, reducing the need for manual labor. They are commonly used in automotive plants and large distribution centers, where they move parts and products.
- Warehouse Automation Systems: Warehouse automation includes robotic picking systems, automated storage and retrieval systems (AS/RS), and conveyor belts. These technologies reduce picking errors and improve order fulfillment speed.
Process Automation
- Chemical and Pharmaceutical Industries: In these industries, automation ensures precision in mixing, temperature control, and packaging. Automated systems maintain consistency and compliance with stringent regulations. For example, pharmaceutical companies use automated filling and packaging lines to produce medicines at high speed while maintaining quality.
- Food and Beverage Production: Automation in food and beverage production helps maintain hygiene and reduce waste. Automated systems are used for tasks like sorting, packaging, and quality control. Beverage companies use automated bottling lines to fill, cap, label, and package drinks.
Packaging and Palletizing
- Automated Packaging Systems: These systems include machines for wrapping, sealing, and labeling products. They improve packaging speed and accuracy, ensuring products are safely prepared for shipping. Industries ranging from consumer goods to pharmaceuticals rely on automated packaging to meet high-volume demands.
- Robotic Palletizing Solutions: Robotic palletizers stack products onto pallets with speed and precision, optimizing space and reducing labor costs. These systems are widely used in warehouses and distribution centers to prepare goods for transport.
Welding Automation In Manufacturing
Welding automation is addressing many of the challenges the welding industry is facing.
As experienced welders retire and fewer young people enter the trade, manufacturers are finding it harder to find qualified workers to meet production demands.
Traditional welding relies heavily on the skill and precision of individual welders, leading to variability in weld quality. Human factors such as fatigue, inconsistency in technique, and varying skill levels can result in defects and rework, which affects overall product quality and production costs.
Automating specific welding tasks is addressing these challenges. Cobots are being used for repetitive, time-consuming tasks, freeing up skilled welders for other tasks.
Why Welding Automation?
These systems are programmed to follow specific instructions and can perform precise and consistent welds.
Automated welding systems include robotic arms, welding torches, sensors, and control software, which work together to execute welding operations.
Benefits:
- Precision: Automated welding systems perform accurate welds, ensuring consistent quality across all products. This precision reduces the need for rework and minimizes defects.
- Repeatability: Once programmed, robotic welders can perform the same weld repeatedly with the same level of accuracy. This consistency is particularly valuable in high-volume manufacturing environments.
- Safety: Automation significantly reduces the exposure of human workers to hazardous conditions. Robots can handle dangerous tasks, reducing the risk of injuries and improving overall workplace safety.
By adopting welding automation, manufacturers can address the challenges of skilled labor shortages and improve weld quality, ultimately leading to more efficient and reliable production processes.
Automate Your Processes with Hirebotics’ Cobot Welder
Hirebotics offers an innovative Cobot Welder solution designed to streamline welding processes and address the challenges faced in traditional welding.
Overview of the Cobot Welder Solution
The Cobot Welder is a collaborative robotic welding system that combines ease of use with advanced welding capabilities.
It is designed to improve precision, consistency, and safety in welding operations, making it an ideal solution for manufacturers facing skilled labor shortages and quality control issues.
Easy Integration with the Beacon App
The Beacon app allows you to program and control your welding cobot from your phone or tablet. Users can program welds, track performance, receive alerts, and make adjustments, all from the Beacon app!
Real World Success
Hirebotics’ Cobot Welder proves its value through real-world use. For example, Iron Supports implemented the Cobot Welder to improve their welding processes. They achieved significant productivity gains and improvements in product quality. Read the full story here.
When you choose Hirebotics, you’re choosing a reliable partner in welding automation, one that provides robust solutions, exceptional support, and tangible results.
Automation for Success
Industrial automation is successfully addressing the problems we are facing in the manufacturing industry. Welding automation, in particular, offers precision, repeatability, and safer working conditions, making it a valuable addition to many manufacturing processes.
Explore how Hirebotics' Cobot Welder can improve your welding operations. With easy integration, comprehensive support, and a strong ROI, Hirebotics provides the solutions you need to succeed in today's manufacturing landscape.
Contact us to learn more about our innovative automation solutions or to schedule a demo.