Improve Your Plasma Cutting Settings (with Cut Charts)
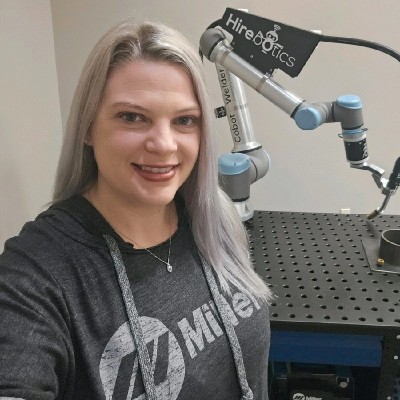
April 29, 2024
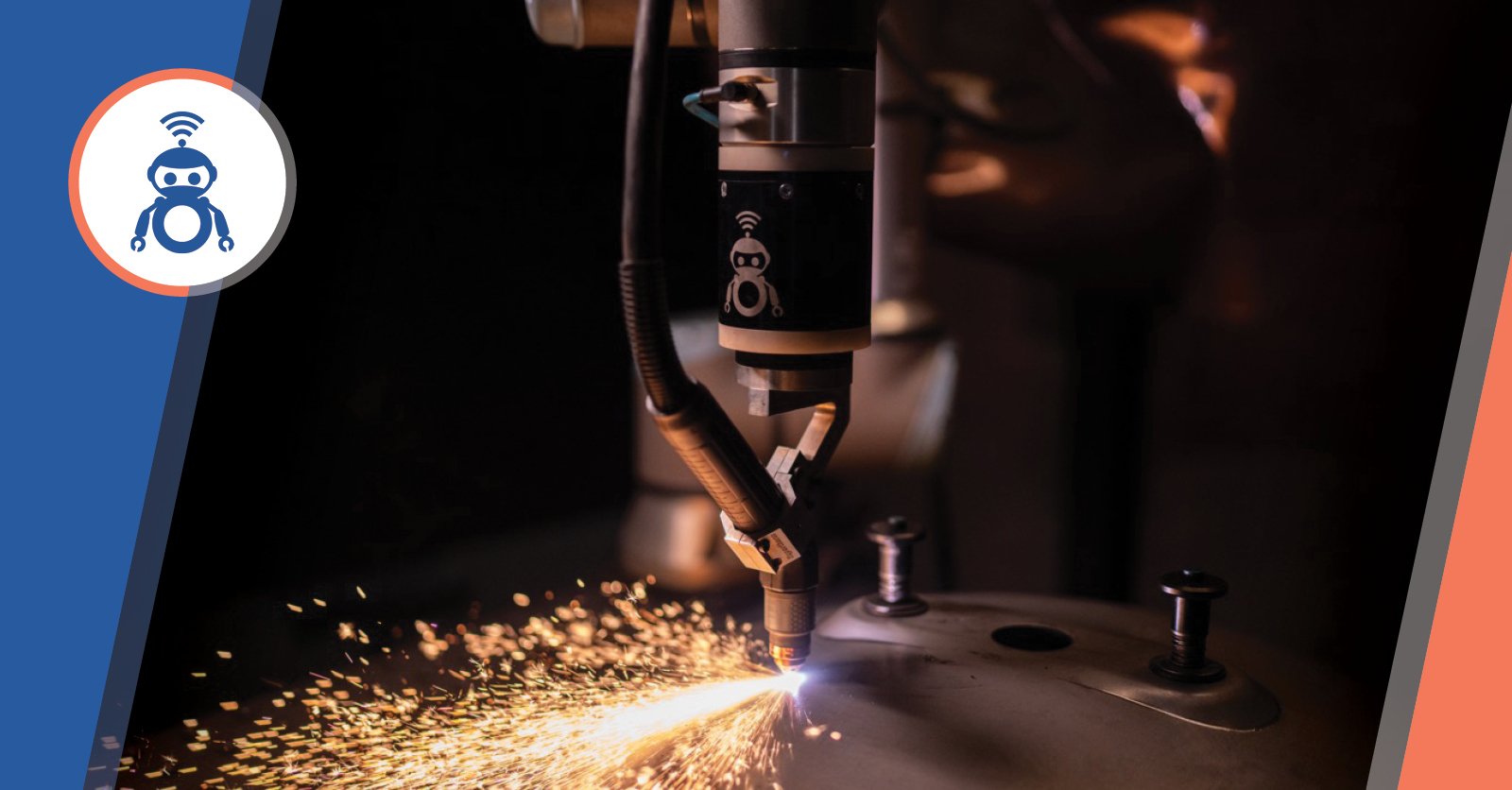
Need help with the plasma cutter settings? You’ve come to the right place!
Bad plasma cutting setup ruins productivity and cut quality. Getting the settings right makes a world of difference.
You are about to learn how to set up your plasma cutter for maximum results. We’ll also include handy charts to help you adjust settings based on material type and thickness.
In this article, lets discuss:
- Plasma Cutting Speed Makes All The Difference
- Plasma Cutting Amperage Provides Power
- Plasma Cutting Voltage Shapes The Cut
- Pierce Height Saves Your Consumables
- Kerf Width Compensation Puts Waste to Waste
- Plasma Cutting Settings Charts
- Setting Up a Plasma Cutting Process On a Beacon-Powered Cobot vs Other Systems
Plasma Cutting Speed Makes All The Difference
Cutting speed is the most critical aspect of plasma metal cutting. Cutting too slow or too fast reduces cut quality. But getting the speed right requires some trial and error.
The faster you cut, the higher the productivity. So, you should almost always max out the speed for your material type, thickness, and the desired cut quality.
Plus, the higher the speed, the lower the heat input, distortion, and HAZ width. So, it’s in your best interest to cut as fast as the material and cut tolerances allow.
The table below shows the effects of too fast/slow cutting and how to achieve the most optimal speed for your application.
Cutting Too Fast | Cutting Too Slow | Optimal Cutting Speed |
The arc shoots upwards into the nozzle, the arc becomes perpendicular to the cut line, or you are getting surface dross. | The sparks are shooting vertically right beneath the nozzle tip or ahead of the tip, cut is too wide, cut line is melted, there is too much dross, and you experience distortion. | The sparks beneath the plate are spraying at 15-30 degrees behind the torch. Try multiple cutting speeds to get the highest speed you can. |
With plasma, speed is king. However, a human can only cut at about 10-15 inches per minute (IPM). That’s why cobots or CNC can drastically boost your productivity. Our Cobot Cutter can easily cut faster than 100 IPM (depending on thickness). So you can almost eliminate distortion from excessive heat and skyrocket productivity.
For example, Tank Technology Inc., an employee-owned tank production shop, went from 3 minutes of manual plasma cutting per tank head to 11 seconds using our Cobot Cutter.
Plasma Cutting Amperage Provides Power
Plasma cutting amperage gives the arc power to slice metal. Generally, you’ll want to use the maximum amperage you can to get the most out of the speed benefit. The higher the amps, the faster you can cut. But, to achieve maximum cut quality, you’ll need to match the thickness with the suitable amp settings for plasma cutting.
However, if you are cutting manually, you’ll have to lower the amperage to avoid distortion and excessive cut line melting. If you max out the amperage but can’t cut extremely fast, you’ll get the negatives of cutting too slow.
Plasma Cutting Voltage Shapes The Cut
Voltage and torch-to-work distance (standoff distance) are essentially the same. Voltage rises with a higher standoff and lowers with a reduced standoff. The arc voltage determines the bevel angle of the cut. The higher the voltage (standoff), the more angular the cut.
It’s extremely important to maintain the set standoff distance as you cut. You don’t want to get inconsistent or excessive bevel of the cut.
This sounds easy in theory, but it becomes increasingly challenging with:
Slight sheet metal warpage from the supplier.
- Heat-induced distortion
- Bumps in the material
- The curvature of corrugated metals
- Other issues causing varying material elevation
So, it’s not the torch that has inconsistent height; it’s the material beneath it that causes varying standoff distances.
In our smartphone app Beacon, you can set the arc voltage for our Cobot Cutter. As a result, the cobot will automatically sense the change in voltage and adjust the torch distance to keep it consistent and ensure a uniform bevel of the cut regardless of the material bumps and distortions.
Pierce Height Saves Your Consumables
If you don’t start your cut from the edge, you’ll first have to pierce a hole to initiate a cut.
But, what happens when you apply a plasma torch to a metal plate? The jet forms a molten pit with a spherical surface, causing the material to gush out upwards into the torch. To save your consumables, your pierce height setting should generally be 1.5-2X the cutting height.
Kerf Width Compensation Puts Waste to Waste
Kerf compensation protects your cut piece from becoming a part of the kerf width that’s wasted in the process. When plasma cutting, the arc creates a cut gap (kerf) where the material is expelled. This material is wasted, so you need to follow the plasma kerf chart for the cut metal and thickness. The compensation will offset the cut path for the kerf, leaving your part unaffected.
Plasma Cutting Settings Charts
The plasma cutting settings charts below are a good starting point, but you should always make test cuts before working on production material. Your elevation, humidity, part shape, desired cut quality, slight alloy differences among material vendors, and other factors may require fine-tuning your settings.
The charts are based on the Hypertherm’s recommended settings for the Hypertherm Powermax plasma cutting power sources and SYNC consumables. All of our Cobot Cutters include these machines, giving you the best all-around plasma cutting equipment.
Beacon makes it easier than ever to setup automatic plasma cutting on our Cobot Cutter. All settings are available in a single, uncluttered smartphone interface. With Beacon, you can input the cut chart settings in less than a minute.
Mild Steel Plasma Cutting Settings Chart
Stainless Steel Plasma Cutting Settings Chart
Plasma Cutting Aluminum Settings Chart
Setting Up a Plasma Cutting Process On a Beacon-Powered Cobot vs Other Systems
Manual plasma cutting, CNC, and cobot systems have different ways of adjusting and maintaining the settings. However, the same principles apply.
Ease of use | Cut Quality | Uniformity | Productivity | |
Manual Plasma Cutting | Extremely simple | Low | Low | Low |
CNC Plasma Cutting | Difficult. Requires specialized skills | Maximum | Maximum | High |
Standard Cobot Plasma Cutting | Moderate, depending on software | Maximum | Maximum |
Medium to high, depending on software |
Cobot Plasma Cutting With Beacon | Extremely simple | Maximum | Maximum | High |
Not all cobot solutions are as easy to use as Beacon + Cobot Cutter. Beacon eliminates the teach pendant and its complexities as it runs on your smartphone/tablet. Beacon lets you get to cutting with a cobot in just a few minutes—often in less than a minute. See our detailed Beacon + Cobot vs other cobot solutions comparison.
Set your plasma cutting with Beacon in just a few steps:
- Name the part in Beacon.
- Adjust settings like arc voltage, cut speed, pierce height, and others, or use pre-defined settings from the library.
- Highlight the cut path type (linear, radial, or rotary).
Manually guide the cobot arm and click the teach button on its smart puck. - Beacon will automatically populate the cut path for you; click save once ready.
- Hit the start button.
- Enjoy as our Cobot Cutter effortlessly repeats the cut procedure part after part.
Learn more about our Cobot Cutter and Beacon, and book a demo with our team. We’ll help you determine if cobot cutting is a good fit for your parts and show you how simple Beacon is.