Cloud Connecting Cobots makes Robotic Workers Better
April 6, 2020
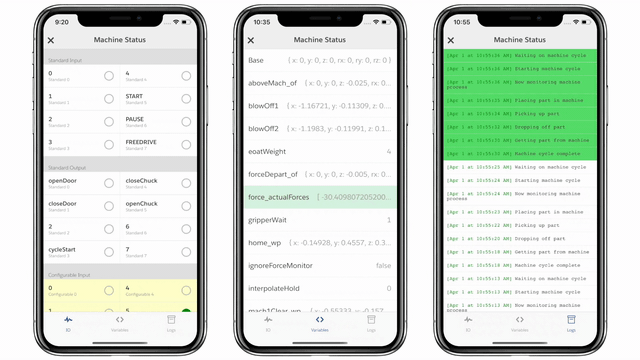
Even before our current situation relegated us to working in new environments, Hirebotics employees have been working remotely since our inception in 2015. Each one of our robotic employees carries out their job, by not only telling us when they clock in and out, but how they are feeling, and what might prevent them from doing a better job. Here in Nashville, it is our job to make sure we are aware of what they tell us, and respond appropriately.
We answer the same core questions frequently: What do you monitor on Universal Robots remotely? How is that used to make informed decisions and help customers? How can that reduce cost? How can that help me maintain production? Here, we will answer those questions as we share how we work remotely with our robotic employees - and our partners - to keep everyone running smoothly.
What does the robot tell you?
Industry 4.0 is a popular term taking on increasing complexity, but one of the main tenants of the concept leveraging the Internet of Things to be better connected with the world around us. In our line of work, that means the robot tells us information that can be broken down into 3 main categories: digital IO, robot variables, and log messages. From within the Hirebotics app on our phones, we are able to see the IO signals that users would see on the Universal Robots touch pendant if they are standing next to the robot onsite. In real time, we are able see inputs that are triggered and outputs as they are turned on and off, in the format shown below:
In the same way, we can see the variables that the robot is putting on the variables screen. These are especially helpful in determining the state of the robot during troubleshooting. Using these variables together with the digital IO, we can know what the robot is looking for, and what it is seeing. We can also see what is going on in the cell, giving us more information into how the system is running and the processes being used by the humans working with the robot.
The final part of the trifecta is log messages. We access these in real time as they are streamed to us, as if we were next to the robot watching it onsite. This helps us keep automation acting as intended, and shortens our response time since it is only a few taps away on our phones.
However, sometimes we just need the full story. In the same way, we occasionally compile and collect a larger log file where we can see the full story by looking much farther back in history. In addition to the information directly related to robot logic, we can monitor all sensors in the cell. Is the door not closing on a lathe? Is a part not being sensed in a fixture? Is the robot ready for more parts? By using digital IO, variables, and log messages together we can understand how our robot worker is performing, and better support partners as needed.
The Beauty of Log Messages
While we rely on streaming IO, variables, and logs, we place an emphasis on useful log messages. The best way to convey the usefulness of proper logging is to contrast it with an example of some logs that are more haphazard. In the first example below, the log messages are not very informative - they are few and far between. In contrast, the second example of logging shows the what steps the robot has gone through, and what information it is using to make decisions. With this, it is much simpler to pinpoint any problems that exist in a small amount of time.
What are the benefits?
There are a number of distinct benefits to having these inputs so accessible in cloud connected real time. During normal running we can provide info to partners on the parts they produce, sort, or inspect. These are sent to the app in easy-to-read charts that show production, good and bad parts, and even reason for rejection across time. This is one of the key ways in which Hirebotics enables our users to stay informed of their processes in real time.
Having all these streams in one place and easily accessible means that when Hirebotics does need to support an application, we can look at the pertinent information quickly and draw a conclusion as to what action we must take. This streamlines the support process for our robots, allowing us to spend less time looking back, and more time looking ahead. For our partners, the result is less down time and more productive output, in addition to the peace of mind that comes with being in control of complex situations.
The final benefit is one of the key pillars of Hirebotics itself - our partners do not need to be experts in automation to keep their robot and automation process running smoothly. By taking varied outputs, log files, and machine variables and creating an unambiguous flow, our partners can expend fewer resources trying to understand their robotic employees and get straight into resolving known quirks that may be hampering production.
The Verdict
Those are some of the most common tools Hirebotics uses to keep advancing ourselves and our partners. Observing variables, digital IO, and log messages helps us navigate trends and implement resolutions rapidly. They help us support our customers, as well as maintain our own assets more intelligently. All within the convenience of our phone - in the office, home, or on the road.
We recently release some of our Cloud Tools for anyone to use, for free, without any additional hardware required! Give them a try and be sure to let us know if there's more capabilities you'd like to use with your Universal Robots.
When writing on a topic, we enjoy feedback just like we get from our robotic workers. Use the comment section below to pose questions and generate new ideas. Recommend a new blog topic. We are always eager to discuss the passion underlying our daily activities. Thanks for reading!