What started as a solution to a labor shortage became a powerful tool for growth and innovation in their production process.The welding industry is no stranger to labor shortages. In recent years, it's become increasingly difficult to find skilled welders to keep up with demand.
So what is the solution? More and more manufacturers are using cobots and robotic systems to fill the gap, but not in the way you might think.
Far from replacing welders, these automated tools are designed to work alongside them. It’s not about taking away jobs – it’s about improving the skill set of the welder and making their work more efficient and enjoyable.
This topic was explored on a recent episode of the Manufacturing Happy Hour podcast, featuring Rob Goldiez, CEO of Hirebotics, and Justin Montes, CEO of D'Angelo Marine Exhaust. From overcoming challenges with automation to empowering welders with new skills, they discuss the real-world impacts of adopting cobots in manufacturing. You can listen to the full discussion here.
Welding Automation – Overcoming Challenges with Cobots
The labor shortage has hit the welding industry hard. Companies that once relied on a consistent stream of skilled welders are now struggling to meet demand.
Justin Montes, CEO of D'Angelo Marine Exhaust, experienced this firsthand.
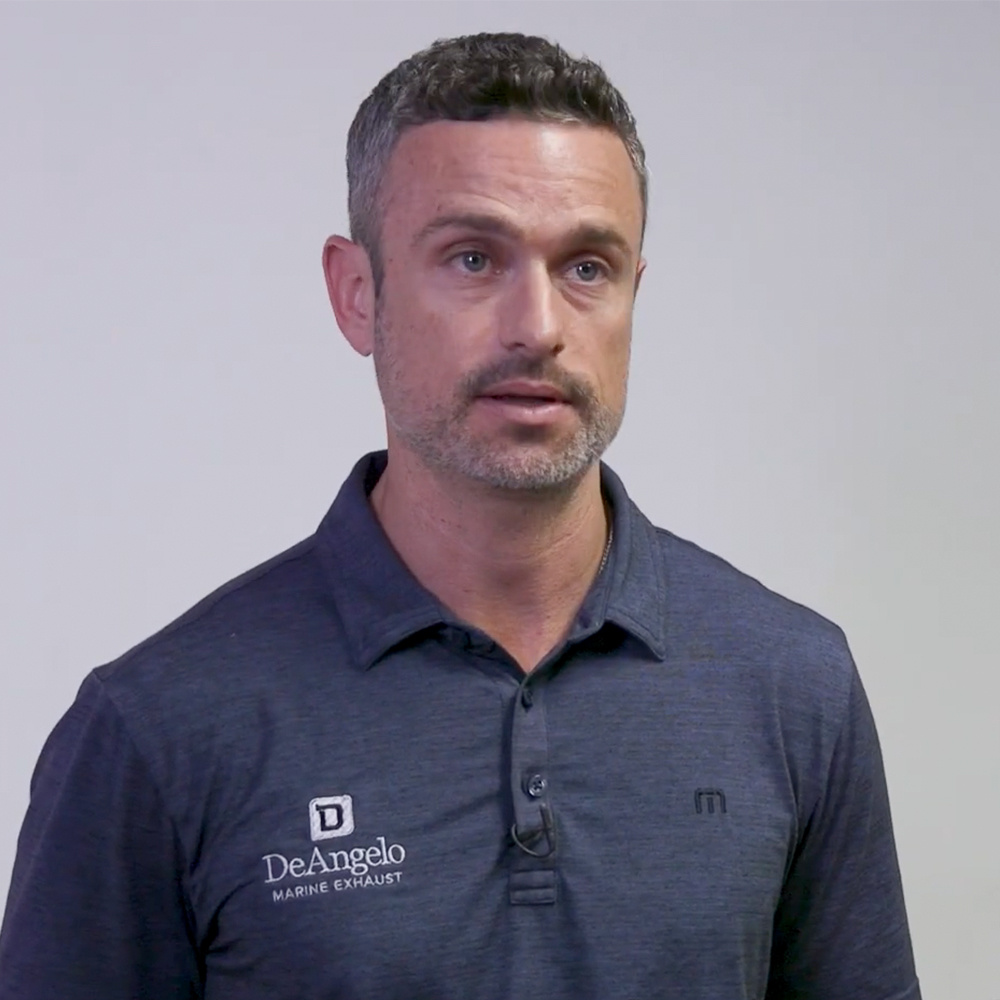 |
"We were way over capacity, behind on everything, delivering late. Our workforce was aging, specifically our fabricators, which are the heart and soul of the company. Marine exhaust fabricators do not grow on trees." |
This workforce challenge isn’t unique to them; it's an industry-wide issue. Finding skilled welders has become increasingly difficult, especially as older generations retire and fewer young workers enter the field.
Like many manufacturers, Justin initially had his hesitations about automation. His company explored various robotic solutions, sending parts to different providers, only to be met with disappointment. It wasn’t until Justin discovered Hirebotics that things started to change.
For Justin, the shift from skepticism to confidence came quickly after meeting with Hirebotics. "Within 20 minutes, I'm running the parts."
No complicated programming was needed—just a straightforward, app-based solution tailored to welders, not robotics experts.
Key benefits of Hirebotics' cobot solution:
- User-friendly interface: Welders can quickly learn to operate the cobot using a simple app.
- Custom-fit solutions: Cobots are designed specifically for welding, not for general robotics.
- Immediate results: After initial setup, D'Angelo Marine Exhaust saw rapid improvement in production efficiency.
When evaluating and selecting the right cobot solution, Justin was impressed with Hirebotics' support. Unlike other providers, Hirebotics understood his unique challenges. As he put it,
"There were no long ROI studies, no hesitation. We knew what we needed, and Hirebotics delivered. It was that simple."
What started as a solution to a labor shortage became a powerful tool for growth and innovation in their production process.
Impacts of Cobots in the Workplace
One of the most immediate benefits of cobots in the workplace is their ability to take over the repetitive, dull, and often dangerous tasks that welders are typically burdened with.
At D'Angelo Marine Exhaust, this meant that welders could shift their focus to more skilled and creative aspects of their work.
As Justin noted:
"We didn’t have enough labor. So, we were working all kinds of overtime... Now, they got the cobot, and we got caught up right away."
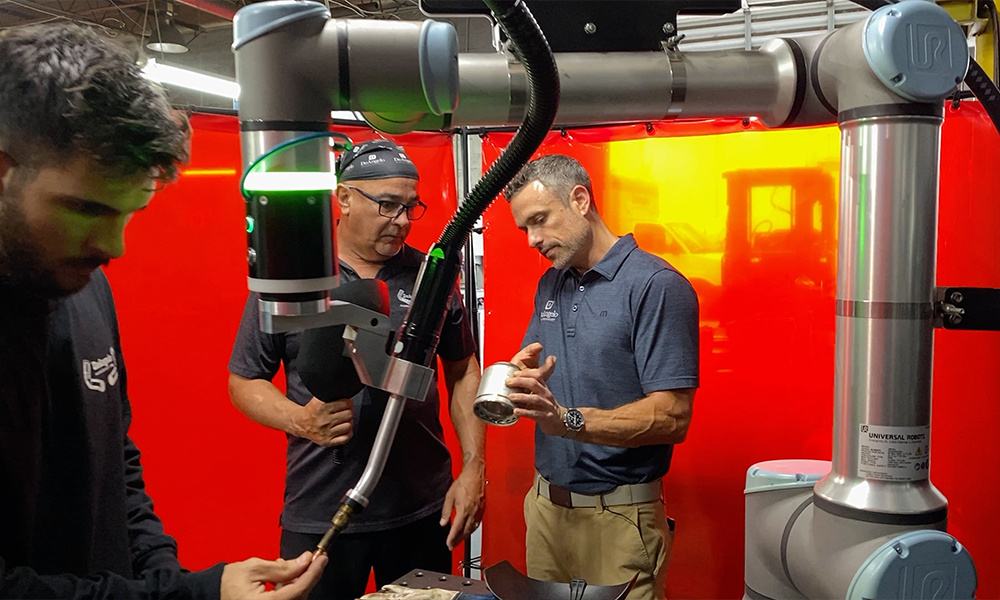
The introduction of cobots didn’t just boost productivity—it significantly improved employee morale.
How Cobots Have Streamlined Tasks at D'Angelo Marine Exhaust:
Welding of standard components: The cobot now handles the repetitive welding of exhaust system flanges and other parts, ensuring consistency and precision.
Increased production speed: Welders reported that the cobot could weld at ten times the speed of traditional manual welding while still achieving full penetration, a crucial requirement in high-quality welding.
Reduced overtime: With cobots handling the bulk of the repetitive work, welders were no longer forced to work excessive overtime, leading to a better work-life balance.
Justin reflected on the transformation, saying:
"It went from a little bit of hesitancy to now they're coming up with more things to do on the cobot... Our fabricators are constantly going into engineering, saying, ‘Hey, how about this?’”
How Cobots Improve Production
Cobots are changing the way welding shops run, and the fear that automation will replace jobs is quickly fading. In reality, cobots aren’t taking jobs away—they’re making existing ones better and even creating new opportunities.
D'Angelo Marine Exhaust is a great example of this. After bringing in cobots, instead of cutting jobs, Justin actually hired more welders.
"The robot did not replace anybody. The robot made us hire more welders and more fabricators. It increased our capacity so much," he says.
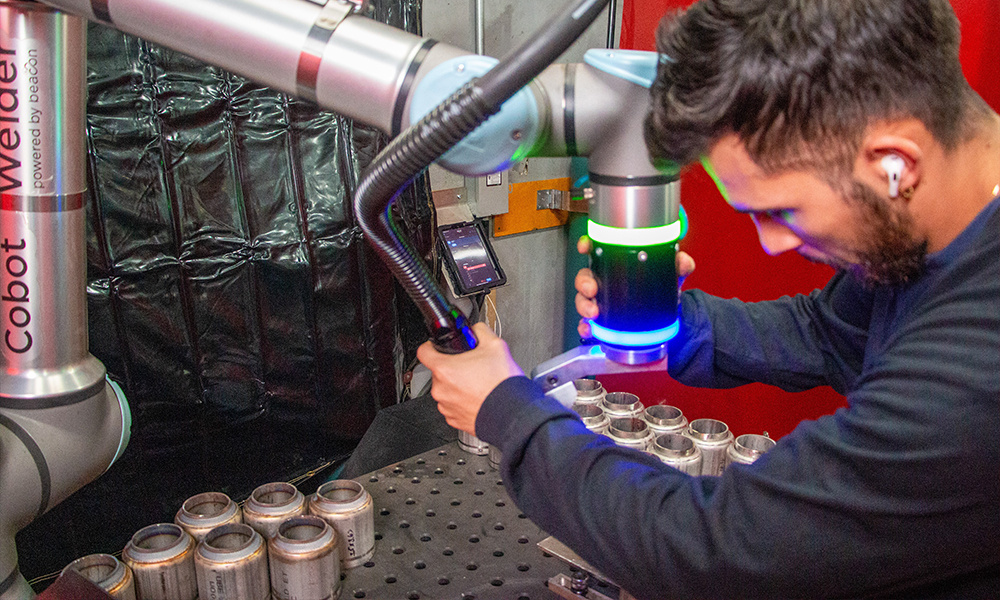
Rob Goldiez, CEO of Hirebotics, backs up this experience. He believes cobots are all about helping welders do their jobs better.
"Cobots take over the dull, dirty, and dangerous tasks, allowing welders to focus on more creative and complex work," Rob explains.
The result? Satisfied workers and more productive teams.
Cobots also make it easy for shops to handle high mix, low volume (HMLV) production. Unlike traditional robots that are stuck doing the same task over and over, cobots are flexible and can switch between different jobs easily.
Another huge advantage is how quickly companies are seeing a return on investment (ROI).
“We paid off the cobot in one order. Now the rest is just icing.”
- Justin Montes
For businesses, cobots aren't just about automating tasks—they're about creating a more innovative and efficient workplace where both the company and its employees can thrive.
The Impact on Efficiency and Innovation
Cobots have a clear impact when it comes to improving efficiency and driving innovation in welding. One of the biggest advantages is the consistent quality and repeatability that cobots bring to the table.
When you're running precision welding jobs, knowing that each weld will meet the same high standards, every time, is invaluable.
Cobots also help cut down on errors, which means fewer mistakes and rework. This doesn’t just save time—it ensures the overall quality of the production stays high, even as the workload increases.
As Rob points out,
"Cobots are all about helping manufacturers achieve consistency. You get the same precise weld every time, which is something that’s hard to match with manual labor alone."
Hirebotics’ cobots are designed specifically to boost productivity without compromising on quality.
The result?
Shops can handle larger workloads, take on more complex projects, and still maintain the high standards their clients expect.
Reactions to Cobots
When cobots first arrived on the floor at D'Angelo Marine Exhaust, there was some hesitation. Welders were used to doing things a certain way, and the idea of introducing a machine into the mix sparked concerns.
"There was some pushback," Justin admits. "The old dogs here knew one thing: TIG welding good, MIG welding bad. So, bringing in a cobot, which is a MIG welder, had them on edge."
But those initial doubts quickly faded once the welders saw what the cobot could do.
"Once they started using it and tweaking the settings, they loved it. Now you can’t tell the difference between my best TIG welder and what the cobot puts out," Justin says.
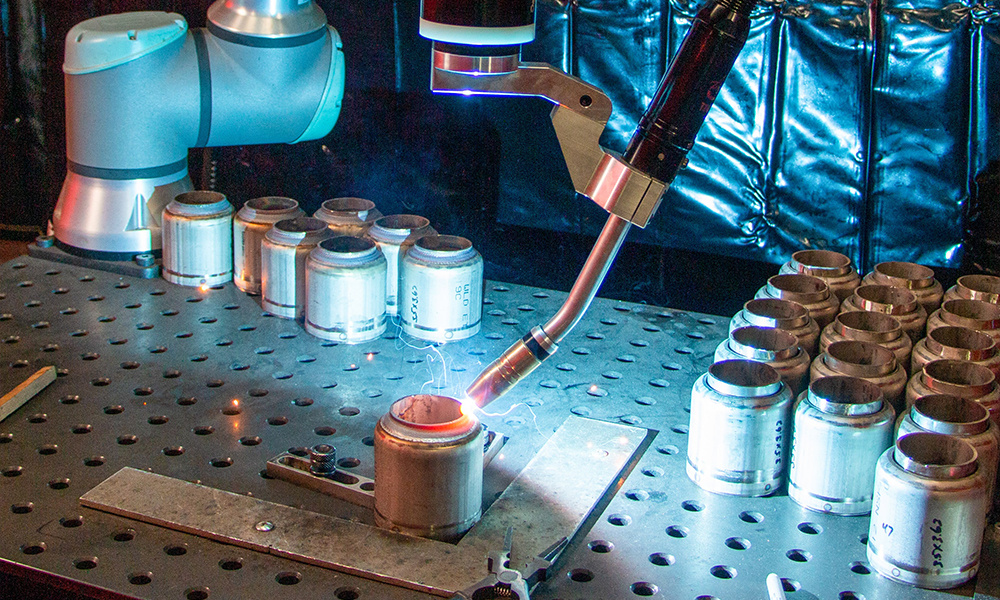
The cobot wasn’t replacing them—it was making their jobs easier and the results more consistent.
As more companies adopt cobots, the fear of automation is steadily being replaced with excitement about the potential they bring to the table.
How Cobots Empower Welders
Cobots are more than just automated tools—they’re empowering welders to expand their skillsets and take their careers to the next level. Instead of viewing automation as a threat, many welders are realizing that learning to operate cobots opens up new opportunities for them.
Justin encouraged this shift by offering incentives.
"We told our welders, ‘Hey, if you can learn to operate the cobot, we'll give you a raise.’ It was a way to keep them motivated and show them that these new skills are valuable," he explains.
By learning to program and operate cobots, welders are gaining a competitive edge in their careers. These new skills create opportunities for career advancement, as welders transition from hands-on labor to overseeing and optimizing the cobot’s performance.
Explore Hirebotics’ Robotic Solutions
At Hirebotics, the mission is clear: to empower welders, not replace them. By providing cobot welders that are specifically designed to enhance the skills and capabilities of welders, Hirebotics is changing the way automation is integrated into the welding industry.
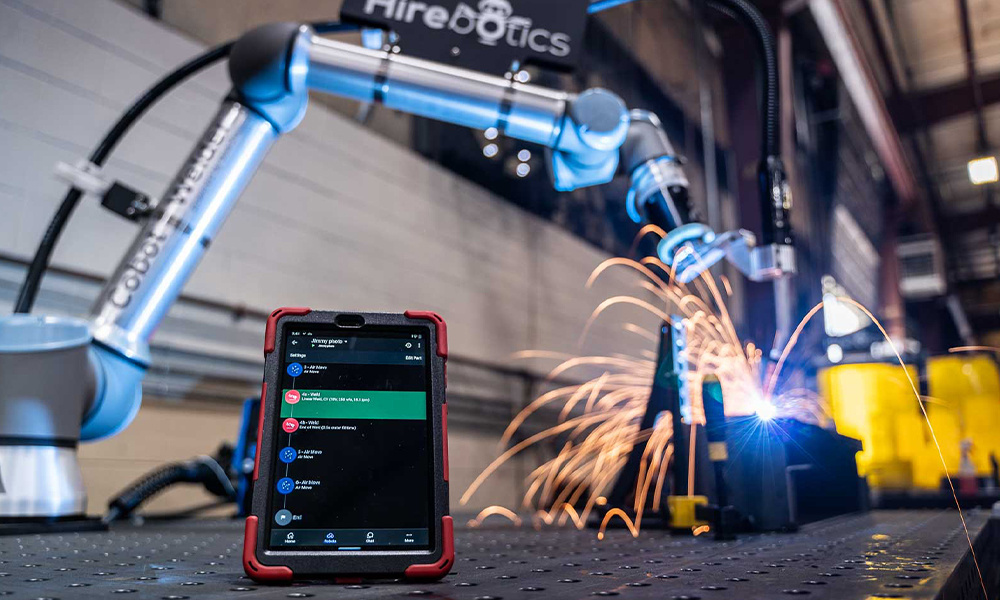
One of the standout features of Hirebotics’ solutions is their Beacon App. This app allows welders to teach the cobots with ease, providing real-time software updates, tutorials, and troubleshooting support—all from a smartphone or tablet.
It’s designed with the welder in mind, meaning there’s no need to learn complicated robot programming or deal with confusing interfaces.
And the support doesn’t end once the cobot is installed. Hirebotics is committed to providing ongoing assistance to ensure their cobots are always running smoothly. Through their live chat feature, welders and manufacturers can get a response in an average of 2 minutes, whenever it’s needed.
Ready to see how Hirebotics can transform your welding operations? Schedule a demo and explore their Beacon App and experience a new era of welding automation that puts welders first. With fast support, easy-to-use tools, and a system built for the welding industry, Hirebotics is here to help your team thrive.
FAQ
Will robots take welding jobs?
Robots are not expected to take welding jobs but rather complement and assist welders in their work. While robots can handle repetitive or hazardous tasks, welders are still needed for complex, creative, and precise work. Automation helps fill the gap left by the ongoing labor shortage in the welding industry, allowing welders to focus on more skilled tasks.
Are robots replacing welders?
No, robots are not replacing welders. In fact, many companies are finding that incorporating robots leads to an increase in hiring, as robots take over the less desirable, repetitive tasks, allowing welders to focus on higher-value work. Robots and welders work together to improve efficiency and productivity, creating a collaborative environment rather than one of replacement.
Are robotic welders worth it?
Yes, robotic welders are worth the investment for many businesses. They can significantly improve productivity, consistency, and quality while reducing the risks associated with manual welding tasks. The quick return on investment (ROI) often seen with robotic welders makes them a smart choice for manufacturers looking to scale operations or meet high-demand production needs.
Will welders be needed in the future?
Absolutely. Welders will continue to be in high demand, especially as automation expands. Robots can handle certain tasks, but skilled welders will always be essential for more complex, custom jobs and for overseeing automated processes. The future of welding is a partnership between welders and technology, with welders leveraging automation to enhance their work.